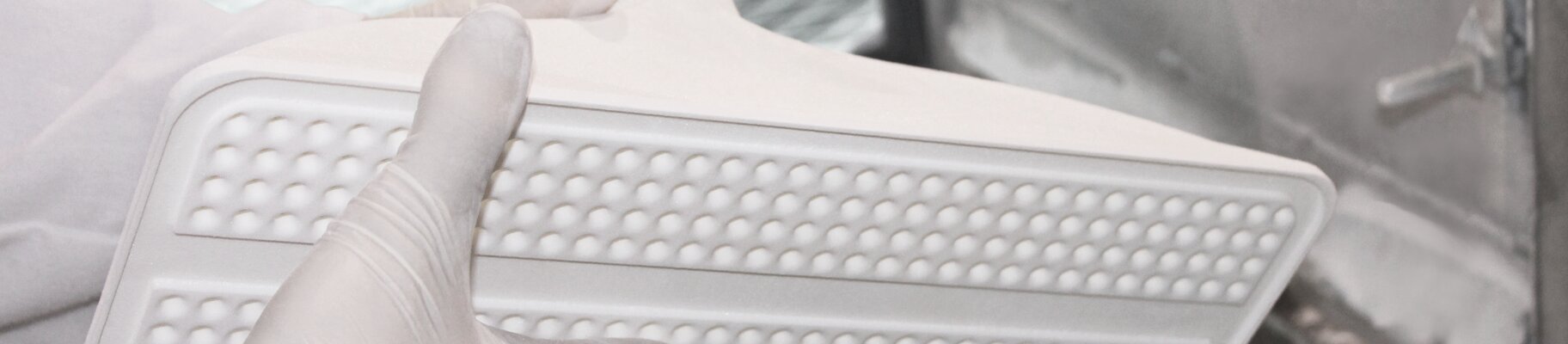
Fabrication additive pour les pinces
Extrémité de bras pour un emballage plus intelligent fabriqué avec FORMIGA P 100
Anubis 3D - Étude de cas
-
Le nombre réduit de pièces facilite l'assemblage
-
Le nouvel outil a été prêt à l'emploi en une semaine seulement
-
Une pince légère de 500 g quatre fois plus puissante
"Je dis aux gens que, contrairement à la fabrication traditionnelle, la complexité est libre avec la fabrication additive. Un concepteur peut avoir toutes sortes d'idées folles et personne ne s'en plaindra. Il est possible de réduire le poids des pièces, de maintenir leur résistance et de fournir des produits esthétiques dotés d'une plus grande fonctionnalité, en moins de temps et à un coût plus bas que jamais. Il s'agit d'un véritable changement dans la fabrication.
Tharwat Fouad | Président | Anubis
Une extrémité de bras innovante, industrielle et imprimée en 3D permet au groupe Langen d'alléger la charge de la ligne d'emballage robotisée de son client.
Pour atteindre une vitesse maximale sans perturber le centre de gravité des robots, l'outil - plus le poids du produit lui-même - ne pouvait pas peser plus de deux kilogrammes. Or, la plus grande charge de crackers sur la ligne était de 1,5 kilo pour un paquet de dix. Il ne restait donc que 500 grammes pour concevoir l'outil parfait. Une fois la décision de recourir à la fabrication additive prise, Fouad a analysé en détail les différents types d'équipements disponibles avant d'opter pour un système FORMIGA P 100 d'EOS.
Dans le cas de l'important fabricant américain de produits alimentaires qui travaille pour le groupe Langen, Anubis a conçu un ensemble de composants plus légers et rationalisés qui offrent une force de préhension quatre fois supérieure à celle des pinces à vide traditionnelles, au lieu d'une plaque à vide et d'un carénage métalliques plus traditionnels (qui auraient pris des mois à concevoir et à fabriquer). Il n'a fallu qu'une semaine pour fabriquer, assembler et tester le nouvel outil de manière additive.
Le matériau utilisé pour la partie principale du vide est le nylon 12 (PA 2200 d'EOS), choisi pour sa flexibilité, sa capacité à supporter des charges d'impact et parce qu'il est certifié USP Class VI pour le contact alimentaire.

"Concevoir et produire un outillage capable de prélever ce que nous voulions, tout en respectant les contraintes de charge utile du robot,
tout en respectant les contraintes de charge utile du robot,
aurait été impossible auparavant".
Robert Husnik | Directeur de l'ingénierie | Groupe Langen
Les résultats en un coup d'œil
- Une puissance quatre fois supérieure
- Amélioration des performances
Études de cas EOS
Découvrez trois décennies d'excellence en matière d'impression 3D avec EOS