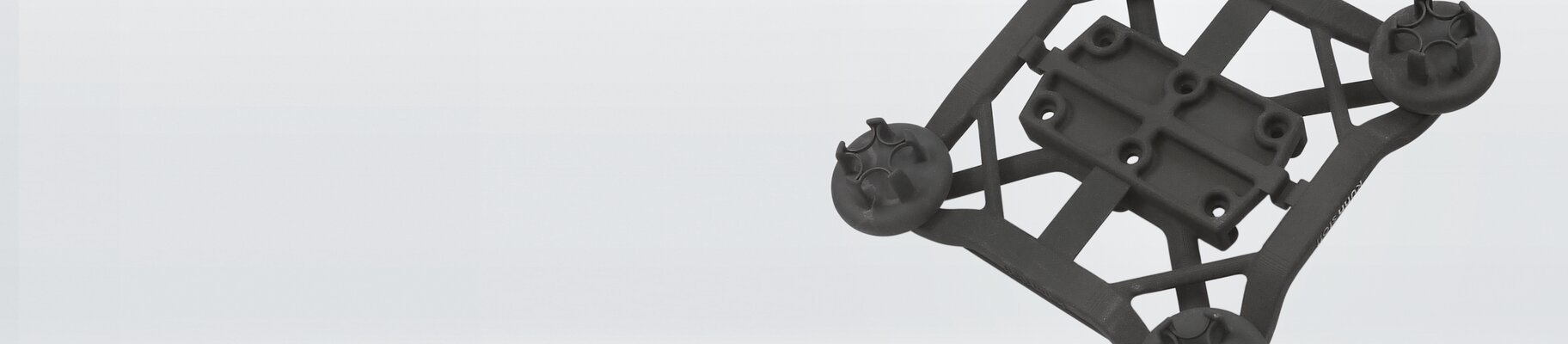
Système de préhension fabriqué par additif, léger et durable grâce à la technologie EOS
Wittmann Group & KuhnStoff | Etude de cas
Grippeur bronchique avec plaque de base fonctionnelle Léger et durable grâce à la technologie EOS
La main est l'une des pierres angulaires de l'évolution humaine : avec son pouce qui s'oppose aux autres doigts, la main humaine est un outil idéal pour saisir, explorer et travailler. Elle est donc la clé de l'activité culturelle et du progrès technique. L'industrie exploite souvent ce principe ingénieux : l'un des processus pour lesquels des machines sont utilisées est la préhension automatisée de presque n'importe quelle pièce souhaitée pour la transporter à l'étape opérationnelle suivante.
Ces machines de préhension sont des chefs-d'œuvre d'ingénierie. Kuhn-Stoff GmbH & Co KG s'est consacré à l'ingénierie spécialisée en appliquant la technologie de fabrication additive EOS. Ce procédé consiste à fabriquer des pièces de machine, couche par couche, à partir de poudre de plastique fondue à l'aide d'un faisceau laser. Kuhn-Stoff a ainsi développé et produit une pince bronchique extrêmement légère, solide et durable pour Wittmann Robot Systeme GmbH, à Nuremberg, en Allemagne. Quatre de ces préhenseurs reposent sur un cadre de support avec des conduits pneumatiques intégrés.

"Nous déployons depuis des années des pièces fabriquées à l'aide de la fabrication additive dans divers secteurs de l'automatisation. Le préhenseur bronchique répond à toutes nos exigences, et les dépasse même. La pièce est très fiable en termes de performances quotidiennes."
Michael Tolz | Responsable de la technologie, Allemagne et directeur de succursale | Wittmann Robot Systeme GmbH à Nuremberg
Défi
Le client est un fabricant de robots et de systèmes d'automatisation. Kuhn-Stoff a été chargé de redessiner un préhenseur mécanique qui soulève, transporte et dépose les pièces d'une machine de production par l'intermédiaire d'un mécanisme pneumatique. Les exigences suivantes ont été établies : le préhenseur doit être plus léger que son prédécesseur, tout en étant capable de déplacer les charges requises. La complexité de la conception doit être simplifiée et la pièce doit répondre à des critères d'efficacité.
L'importance du poids relève de la physique : les systèmes de préhension de ce type doivent fonctionner rapidement afin de déplacer le plus grand nombre possible de pièces de machines dans une unité de temps donnée.
Le fait que la masse soit inerte signifie qu'une force doit être appliquée pour la mettre en mouvement. Plus une charge est lourde et plus elle se déplace rapidement, plus les forces nécessaires à l'accélération et à la décélération sont importantes.
Outre le point de vue de l'efficacité énergétique, ce fait a également des conséquences particulièrement négatives sur la durabilité du système : plus les forces en jeu sont importantes, plus l'usure de la machine est élevée.
La version précédente de la pince était composée d'aluminium, de tubes en caoutchouc et de plusieurs éléments de connexion, et sa production était coûteuse. Les experts en fabrication par couches de Kuhn-Stoff se sont fixé pour objectif de simplifier considérablement la conception. La nouvelle structure de la pièce de la machine devrait contribuer à une partie de la réduction du poids. Une autre partie devrait être obtenue grâce à l'optimisation structurelle des pièces restantes - l'un des principaux avantages de la fabrication additive. Dès le début des travaux, il est apparu clairement que la nouvelle pince pouvait être produite en une seule pièce, sans qu'il soit nécessaire de procéder à une finition post-production ou à un assemblage ultérieur.

Solution
L'équipe de Kuhn-Stoff a commencé par examiner la fonctionnalité et les exigences de fonctionnement de la pince : lorsque de l'air comprimé circule dans une membrane flexible, les griffes de la pince s'ouvrent ; de même, le système se referme lorsque l'air comprimé est coupé. En plus de la flexibilité du plastique, la pièce doit pouvoir pivoter à 90° pour effectuer la séquence de mouvements nécessaire. En tenant compte de ces exigences, il a été possible de réduire le nombre de pièces nécessaires à seulement deux composants.
Une fois le processus de conception achevé, Kuhn-Stoff a commencé à produire le nouveau système de préhension à l'aide d'une FORMIGA P 100. En quelques heures seulement, les deux composants du système de préhension ont été fabriqués en polyamide. Grâce à la technologie EOS, les conduits pneumatiques et les connecteurs ont été entièrement intégrés dans la plaque de base.
"Comme d'habitude, la production à l'aide du système EOS s'est déroulée sans problème. Le résultat final a, une fois de plus, impressionné toutes les personnes impliquées. En une seule étape, nous avons pu créer une pièce fonctionnellement intégrée qui a dépassé toutes les exigences du client. En résumé : la fabrication additive est désormais une réalité quotidienne, mais les résultats restent extraordinaires", déclare Hannes Kuhn, PDG de Kuhn-Stoff GmbH.

"Nous utilisons la technologie EOS depuis plus de huit ans et nous n'avons obtenu que des résultats positifs. Lorsqu'elle est appliquée correctement, la flexibilité de la conception offre des avantages significatifs qui peuvent donner à nos clients des avantages presque inégalés sur le marché."
Hannes Kuhn | PDG | Kuhn-Stoff GmbH & Co KG
Résultats
En ce qui concerne l'objectif principal de réduction du poids, Kuhn-Stoff a obtenu une baisse de 86 % pour atteindre seulement 220 g. Malgré son faible poids, la pince est capable de supporter les charges nécessaires, même dans le cadre d'une utilisation exigeante et continue : après 5 millions de cycles, l'équipe a interrompu les essais sous contrainte, ayant atteint la durée de vie prévue. Au cours de cette période, il n'y a pas eu un seul défaut ou une seule défaillance. La raison en est la solidité de la construction, qui a été obtenue malgré les conduits d'air intégrés dans la plaque de base. En outre, la conception flexible garantit qu'en cas de petites collisions, celles-ci n'endommagent pas le système de préhension ou l'outil de moulage par injection. Dans certains cas, le poids plus léger permet également l'utilisation d'un type de robot plus petit, ce qui entraîne des réductions de coûts significatives. En outre, Wittmann a pu augmenter le nombre de cycles de travail grâce à la faible hauteur de la pince qui réduit la largeur d'ouverture nécessaire du plateau de serrage de la machine de moulage par injection. Il en résulte une réduction des coûts d'exploitation.
Les coûts de fabrication ont été réduits de 50 % par rapport au modèle précédent fabriqué de manière conventionnelle. Cela s'explique par le gain de poids et la réduction du nombre de composants de 21 à deux. La réduction du temps de production est tout aussi importante : la fabrication du système de préhension, qui prenait auparavant douze jours à Kuhn-Stoff, n'en nécessite plus que trois.
"Nous sommes extrêmement satisfaits du nouveau système de préhension. Il s'est avéré tout aussi efficace que l'ancien dans le cadre d'une utilisation intensive et continue, tout en étant moins cher, plus léger et plus rapide à produire. Je n'ai jamais vu d'avancée aussi importante dans la fabrication des poignées que celle que la fabrication additive a apportée à la production de notre pince bronchique. La méthode de production a eu un effet très positif sur nos solutions d'automatisation", résume Michael Tolz, responsable de la technologie et directeur de succursale chez Wittmann Robot Systeme GmbH. Parfois, la révolution peut présenter des avantages par rapport à l'évolution.
Les résultats en un coup d'œil
- -1350 grammes: Réduction du poids de 86 %
- -Coûts de 50 %: Réduction des coûts de production de 50
- -19 Composants: Réduction du nombre de composants individuels de 21 à 2
Études de cas EOS
Découvrez trois décennies d'excellence en matière d'impression 3D avec EOS