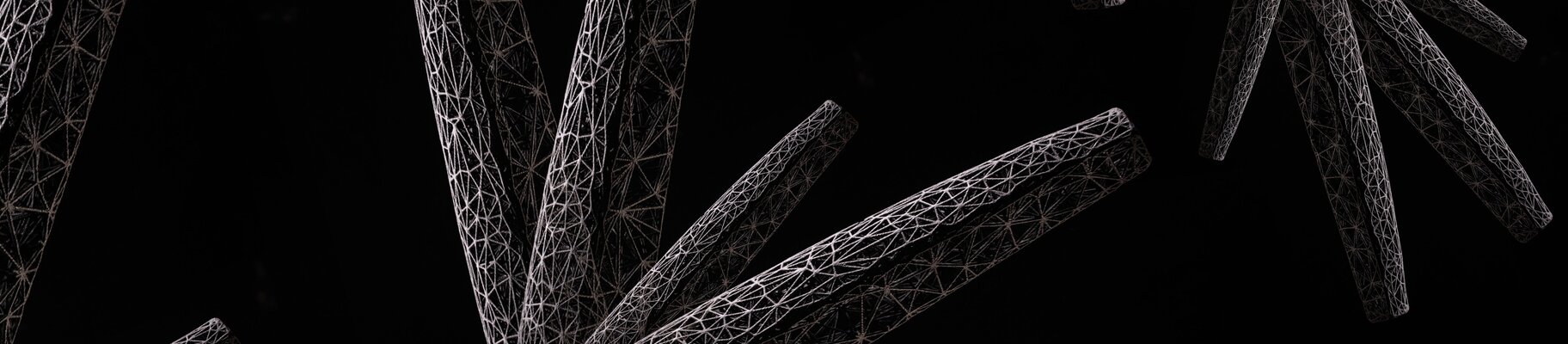
Leuchtturmprojekt zur Produktion von Ersatz- und Serienteilen gestartet
Bundesministerium für Bildung und Forschung fördert POLYLINE mit 10,7 Mio. Euro Euro - Kick-off Meeting des Konsortiums zur Automatisierung der additiven Fertigung in der Automobilindustrie.
____ Krailling, Deutschland, 5. Mai 2020
Das Projekt POLYLINE bringt 15 Industrie- und Forschungspartner aus Deutschland zusammen, um eine digitalisierte Produktionslinie der nächsten Generation zu entwickeln. Auf dieser Anlage sollen Kunststoffteile für die Automobilindustrie hergestellt werden. Ziel ist es, konventionelle Fertigungstechniken (z.B. Zerspanung, Gießen, etc.) durch additive Fertigung (AM) in Form von Hochdurchsatz-Fertigungsliniensystemen zu ergänzen. Das Projekt wird vom Bundesministerium für Bildung und Forschung mit insgesamt 10,7 Mio. Euro gefördert. Euro. Das Projekt hat eine Laufzeit von drei Jahren. POLYLINE wurde offiziell mit dem Kick-off-Meeting aller Konsortialpartner am 4. März 2020 bei EOS in Krailling bei München gestartet.

Hintergrund des POLYLINE-Projekts
Mit der additiven Fertigung lassen sich nahezu beliebige Geometrien und auch komplexe Strukturen ohne nennenswerten Mehraufwand realisieren - ein großer Schritt in Richtung Massenproduktion individualisierter Produkte. Sowohl die vertikale als auch die horizontale Integration additiver Fertigungsverfahren in konventionelle Anlagen ist derzeit jedoch nur bedingt umsetzbar, da es an prozesskettenübergreifenden Standards mangelt. Dies liegt an AM-spezifischen Abläufen (z.B. Produktionszeit im "Batch-Prozess") und dem generell geringen Automatisierungsgrad der physischen Handhabungs- und Transportprozesse.
Andererseits ist die digitale Datenkette entlang der horizontalen Prozesskette an vielen Schnittstellen nicht durchgängig, was derzeit zu mangelnder Transparenz, Fehleranfälligkeit und eingeschränkter Überwachung entlang der Prozesskette führt und die Integration in relevante Produktionssteuerungssysteme erschwert. Diese Hindernisse begrenzen das offensichtlich hohe Potenzial additiver Fertigungsverfahren in bestehenden Serien- und Montagelinien.

Von flexiblen Lösungen für das Prototyping
bis hin zu skalierbaren additiven Produktionsketten
Um das Projektziel zu erreichen, strebt das Projekt einen digitalen und physischen Systemdurchbruch an. Dazu ist es wichtig, alle zentralen Kennwerte und Qualitätskriterien (inklusive Identifikation, Historie und Messwerte) vom CAD-Modell bis zum fertigen Bauteil zu erfassen und zu dokumentieren. Die einzelnen Teilprozesse der Produktion - von der Prozessvorbereitung über den selektiven Laser-Sinter-Prozess, das Kühlen und Auspacken bis hin zur Reinigung und Nachbearbeitung - werden automatisiert und in die geplante Produktionslinie integriert, in der erstmals alle technologischen Elemente einer SLS-Fertigungskette vollständig miteinander verknüpft werden.
POLYLINE verfolgt einen neuen Lösungsansatz, der eine ganzheitliche Betrachtung vornimmt und alle erforderlichen Prozesse implementiert. Die angestrebte Produktionslinie soll mit einem hohen Reifegrad entsprechend den Anforderungen des Anwendungspartners umgesetzt werden. Die Anwendungsfälle umfassen sowohl kundenspezifische Bauteile als auch Serienbauteile in großen Stückzahlen.
Um die additive Fertigung als echte Verfahrensalternative für die Serienproduktion zu etablieren, fördert das Bundesministerium für Bildung und Forschung das Projekt mit insgesamt 10,7 Mio. Euro. Euro. Das Projekt ist Teil der Fördermaßnahme "Linienintegration von additiven Fertigungsverfahren" im Rahmen des Förderprogramms "Photonik Forschung Deutschland - Licht mit Zukunft". POLYLINE wird von EOS geleitet, dem weltweit führenden Technologieanbieter im industriellen 3D-Druck von Metallen und Kunststoffen.