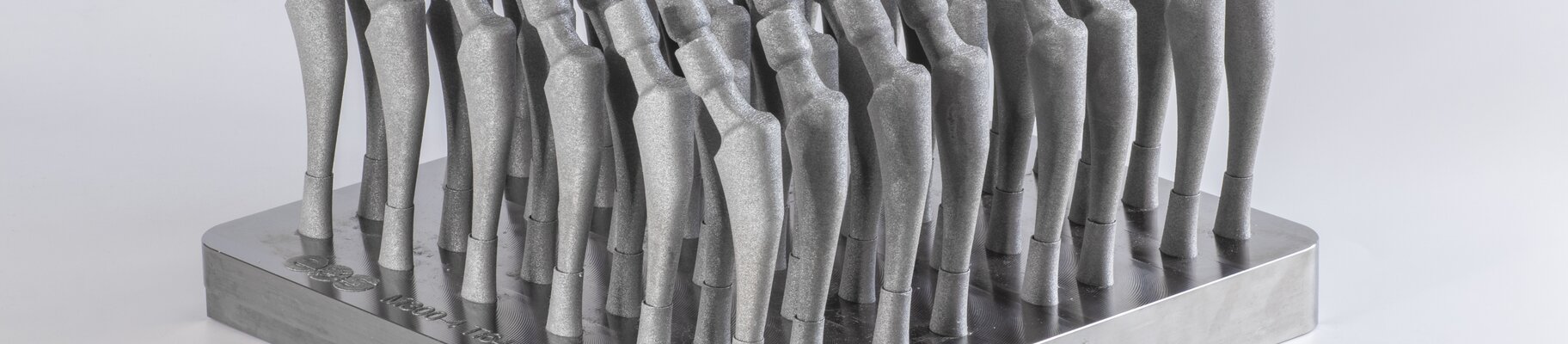
Orthopädische Implantate: Neue Möglichkeiten mit Metall-3D-Druck
30. Oktober 2020 | Lesezeit: 4 min
EOS hat ein Ti64-AM-Verfahren entwickelt, das in Kombination mit dem Wärmebehandlungsverfahren Hot Isostatic Pressing (HIP) hervorragende Ermüdungseigenschaften aufweist. Das Ziel dieses Projekts war es, diese Ermüdungseigenschaften an einem aktuellen Implantatdesign zu testen und die Ergebnisse mit traditionell geschmiedeten Ti64-Hüftschäften zu vergleichen.
Erschließung der Möglichkeiten der additiven Fertigung
Die folgenden Abschnitte zeigen, wie das Wissen, die Erfahrung und die Dienstleistungen des EOS Netzwerks zusammenkamen, um diesen Sprung in der additiven Fertigung in der Orthopädie zu realisieren:
Müdigkeitsergebnisse
Die Ermüdungstests wurden von OIC, Orthopedic Innovation Center, Winnipeg, Kanada, durchgeführt. Die Hüftschäfte wurden gemäß ISO 7206-6 auf die Ermüdungseigenschaften des Halses getestet. Sie hielten einer Belastung von 5340 N für 10 Millionen Zyklen stand. In dieser Studie wurden 2 additiv gefertigte Hüftschäfte getestet, die beide einen Runout von 10 Millionen Zyklen überstanden. Dies zeigt, dass die Ermüdungseigenschaften dieser AM-gefertigten Implantate mindestens so gut sind wie die eines herkömmlichen geschmiedeten Ti64-Hüftschaftes. Dies ist das erste Mal, dass solch hohe Ermüdungseigenschaften bei einem mit Additive Manufacturing hergestellten Implantat gemessen wurden.
Vorbereitung des Baus
Um die Entfernung der Stütze zu vermeiden und das Herausnehmen des Implantats aus der Plattform zu erleichtern, wurden die Hüftschäfte in einem "Halter" hergestellt. Die Hauptfunktion dieses Halters besteht darin, Schutz vor den Kräften der Wiederbeschichtung zu bieten. (Um die besten mechanischen Eigenschaften zu erzielen, wurde eine HSS-Klinge verwendet, die ein optimales und gleichmäßiges Wiederbeschichtungsverhalten gewährleistet). Es besteht jedoch keine Verbindung zwischen dem Halter und dem Hüftschaft, sondern ein Spalt von ca. 0,2 mm - 0,3 mm; die ideale Spaltbreite wurde durch eine DoE ermittelt. Die Spaltgröße ist ein Kompromiss zwischen der leichten Entnehmbarkeit und dem sicheren Schutz der Hüftschäfte vor Vibrationen aufgrund von Rückstellkräften. Der Hüftschaft wird durch die Reibungskräfte zwischen dem Halter, dem Pulver und dem Hüftschaft in seiner Position gehalten.
Inspiriert wurde ich zu dieser Aufbaustrategie durch den Beitrag Bauen ohne Stütze von meinem Kollegen Michael Wohlfart. Es ist sehr lohnend, diese innovativen Ideen in einer realen Anwendung zum Leben zu erwecken!
Verwendung der Additive Works Software Amphyon
Der nächste Schritt bestand darin, sicherzustellen, dass diese Idee in der Praxis funktionieren würde. Amphyon wurde eingesetzt, um zu bestätigen, dass die Einrichtungsstrategie keine Probleme verursachte, wodurch die Notwendigkeit einer "Trial-and-Error"-Baustrategie entfiel. Eine häufige Beschwerde von neuen AM-Benutzern und sogar von erfahrenen AM-Benutzern, die neue Anwendungen ausprobieren, ist die Notwendigkeit einer "Versuch-und-Irrtum"-Strategie für den ersten Bau.
Es wurden Simulationen durchgeführt, um zu prüfen, ob es zu Kollisionen mit dem Recoater kommt, ob die Verformungen innerhalb der Toleranz liegen und ob thermische Spannungen auftreten. Diese Analyse ermöglicht eine qualitativ hochwertige Konstruktion, bevor ein einzelner Auftrag erstellt wird, was Kosten und Vorlaufzeit reduziert.
Diese Software ermöglicht die Vorverformung des Hüftschaftes, um direkt beim ersten Mal ein hochpräzises Teil aus dem Drucker zu erstellen. Meiner Erfahrung nach funktioniert dies gut, insbesondere bei kleinen und kontrollierten Verformungen, die für den Hüftschaft während des Drucks zu erwarten sind.
Erzielung hervorragender Ermüdungseigenschaften
AM-Verfahren auf dem neuesten Stand der Technik
Die Hüftschäfte wurden mit dem EOS Titanium Ti64 Grade 23 Prozess in 40µm Schichtdicke auf einer EOS M 290 hergestellt. Die EOS M 290 wurde für dieses Projekt ausgewählt, weil sie das qualifizierteste industrielle additive Fertigungssystem auf dem Markt ist. Darüber hinaus ist die Zuverlässigkeit und Wiederholbarkeit der Maschine genau das, was für hervorragende Ermüdungseigenschaften benötigt wird, bei denen ein einziger Fehler die Eigenschaften erheblich beeinträchtigen kann. In Zukunft wäre es sinnvoll, den Prozess für die Serienfertigung weiter zu optimieren, um die Fertigungsrate und die Stabilität angesichts der besonderen Anforderungen einer Hüftschaftanwendung zu verbessern.
Optimierte HIP Wärmebehandlung
Die ausgezeichneten Ermüdungseigenschaften werden durch die Kombination eines hochmodernen AM-Verfahrens (siehe oben) mit einer optimierten HIP-Wärmebehandlung (Hot Isostatic Pressure) erzielt. Herkömmliche HIP-Wärmebehandlungen sind optimiert, um die mechanischen Eigenschaften der Guss- oder gussähnlichen Qualität und des Gefüges zu verbessern. Die Qualität aus einer EOS M 290 Daher hat EOS eine HIP-Wärmebehandlung entwickelt, die der einzigartigen Mikrostruktur von AM Rechnung trägt.
Die herkömmliche Hüftbehandlung wird bei 920 °C und 100 MPa für 2 Stunden durchgeführt und ist in verschiedenen Branchen weit verbreitet. Das von EOS entwickelte Verfahren wird bei 820 °C und 140 MPa für 2 Stunden durchgeführt. Dieser HIP-Zyklus in Kombination mit dem DMLS-Verfahren von EOS führt zu einer Dauerfestigkeit von 795 MPa für 10^7 Zyklen (N=9).
Nachbearbeitung
Die Nachbearbeitung ist recht einfach und wurde von Precision ADM, Winnipeg, Kanada, durchgeführt. Das AM-Verfahren wurde so eingerichtet, dass die gleichen Nachbearbeitungsschritte wie bei einem konventionell hergestellten Hüftschaft durchgeführt werden konnten. Daher wurde der Ansatz ohne Stützen gewählt. Der Konus wurde bearbeitet und der Hals des Hüftschaftes wurde poliert, um optimale Ermüdungseigenschaften zu erzielen, ähnlich wie bei einem bereits auf dem Markt befindlichen Prädikatsprodukt. Die Ergebnisse sind auf der rechten Seite zu sehen.
Schlussfolgerung
Die Tatsache, dass es heute möglich ist, gefälschte mechanische Eigenschaften für eine konkrete Anwendung zu erzielen, ist ein großer Sprung in der additiven Fertigung für die Orthopädie. Diese spannende Entwicklung ermöglicht es uns, das Potenzial der additiven Fertigung für eine weitere Gruppe von Implantaten zu erschließen. Es liegt nun an den Geräteentwicklern in orthopädischen Unternehmen und anderen, die Grenzen der additiven Fertigung zu erweitern und Ideen zu verwirklichen, die bisher als unmöglich galten. Additive Minds freut sich darauf, mit Ihnen zusammenzuarbeiten, diese Möglichkeiten zu erschließen und die nächste Generation von Implantaten möglich zu machen.
Autor: Davy Orye