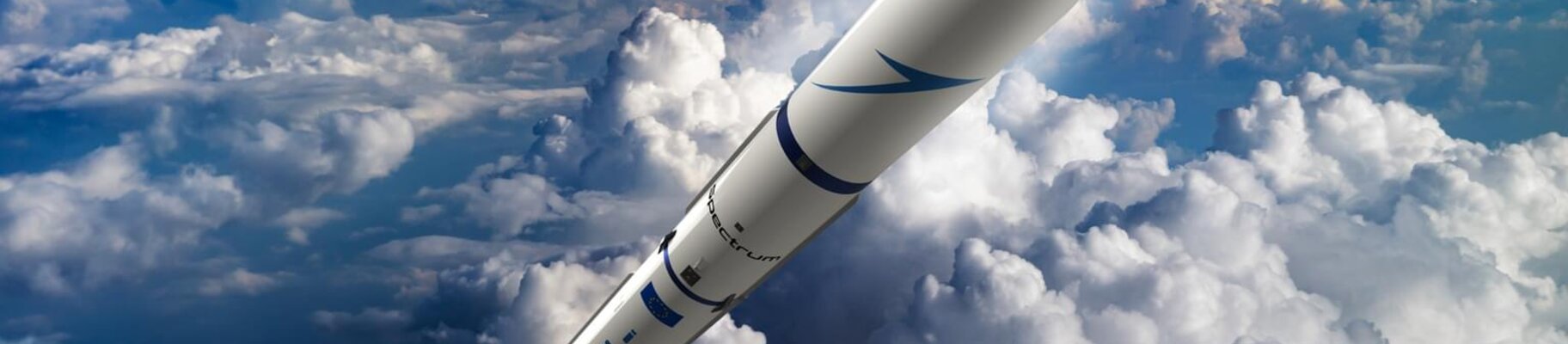
Additive Fertigung für die neue europäische Raumfahrt
16. Januar 2023 | Lesedauer: 5 min
Die New-Space-Industrie war von Anfang an stark auf die USA ausgerichtet. Doch mit dem Aufkommen neuer Technologien und privater Unternehmen, die in diese Branche investieren, hat sich dieser geografische Fokus erweitert und umfasst nun zunehmend auch andere Teile der Welt. In diesem Artikel beleuchten wir die Globalisierung von New Space durch innovative Technologien wie die additive Fertigung sowie Europas wachsende Rolle in diesem Sektor.
Der Aufstieg von New Space in Europa
Im ursprünglichen Wettlauf um den Weltraum traten die Länder gegeneinander an, um als erste die Atmosphäre zu verlassen, als erste auf dem Mond zu landen, usw. Doch mit New Space beginnen diese nationalen Grenzen zu verschwinden. Die Raumfahrtindustrie ist nicht mehr nur eine Unternehmung, die von staatlichen Institutionen betrieben wird, sondern unabhängige Unternehmen beginnen allmählich, einen größeren Teil der Branche zu besetzen, wobei sie das Fachwissen, den Pioniergeist, riesige Mengen an privaten Finanzmitteln und Risikokapital sowie (buchstäblich) weltfremde Ambitionen mitbringen. Es gab viele technische Durchbrüche, die diese neue Weltraumwelle vorantrieben, wie fortschrittliche Fertigungstechnologien, Miniaturisierung von Satelliten und ihren Komponenten, wiederverwendbare Startsysteme, laserbasierte Kommunikationsgeräte, laserbasierte Zündung und künstliche Intelligenz.
Europa verfügt über eine der fortschrittlichsten Raumfahrtinfrastrukturen weltweit. Viele staatliche und private Akteure tragen zur Weiterentwicklung der Branche bei. Dies überrascht nicht, da Europas industrielle, wissenschaftliche und akademische Exzellenz seit Jahrzehnten technologische Grenzen verschiebt. Technologien wie die additive Fertigung haben dabei direkten und enormen Nutzen für die Raumfahrt. Angesichts der starken Raumfahrthistorie und der vorhandenen Infrastruktur ist es nur logisch, dass Europa eine Schlüsselrolle in der New-Space-Industrie spielt.
Der europäische – insbesondere der deutsche – Markt für New-Space-Unternehmen wächst rasant. Die neue Welle der Begeisterung für kommerzielle Raumfahrt, ausgelöst durch visionäre Startups, hat in den letzten Jahren auch Europa erreicht. Mehrere vielversprechende Unternehmen haben sich etabliert, darunter Isar Aerospace, HyImpulse und Rocket Factory in Deutschland, Orbex und Skyrora in Großbritannien sowie PLD Space und Pangea Aerospace in Spanien.
EOS arbeitet weltweit mit großen Raumfahrtunternehmen und Start-ups zusammen – sowohl als Partner für Machbarkeitsstudien als auch als Anbieter zuverlässiger additiver Serienfertigungslösungen, die an die spezifischen Anforderungen der Branche angepasst sind. Der zentrale Beitrag von EOS besteht darin, New-Space-Unternehmen den Zugang zu essenziellen Fertigungstechnologien zu ermöglichen, um ihre ambitionierten Konzepte schnell, zuverlässig und kosteneffizient umzusetzen – ohne dabei Kompromisse bei der Leistung einzugehen.
Dieser unternehmerische Geist wird in Europa auch durch die Europäischen Weltraumorganisation (ESA) gefördert – insbesondere durch ESA Space Solutions mit einem Netzwerk aus zahlreichen Business Incubation Centers (BICs) in ganz Europa. Im Folgenden finden Sie zwei hervorragende Beispiele für New Space Organisationen und Projekte, die derzeit in Europa florieren und bei denen die additive Fertigung einen wichtigen Beitrag zu ihrer Entwicklung geleistet hat:
Die Prometheus der ESA
Die Ariane Group, das französische Nationale Zentrum für Weltraumstudien (CNES) und die ESA arbeiten gemeinsam am PROMETHEUS-Projekt – einer Reihe neuer Flüssigraketenantriebe, bei denen niedrige Kosten, Flexibilität und Wiederverwendbarkeit im Mittelpunkt stehen. Ziel des Projekts ist es, einen fortschrittlichen Flüssigsauerstoff- (LOx) und Methan- (LCH4) Antrieb der 100-Tonnen-Klasse zu entwerfen, zu produzieren und zu testen. Dieser Antrieb wird wiederverwendbar konzipiert, um Kosten und Umweltbelastung zu reduzieren. Zudem soll er flexibel einsetzbar sein, mit variabler Schubkraft und mehreren Zündmodi, um ihn für unterschiedliche Starttypen optimal nutzbar zu machen.
Bisher wurden nur wenige Raketentriebwerkskomponenten mit einer wesentlichen funktionalen und strukturellen Rolle mittels Additiver Fertigung (AM) hergestellt. Das PROMETHEUS-Projekt will dies ändern, um die Designflexibilität und die verkürzte Produktionszeit der AM-Technologie zu nutzen. Bis zu 70 % des Triebwerksgewichts im PROMETHEUS-Projekt sollen additiv gefertigt werden. Dadurch sollen Prozesse optimiert werden, die eine schnelle Produktion kostengünstiger Triebwerkskomponenten ermöglichen, während gleichzeitig die Anzahl der Bauteile reduziert, die Fertigungszeit verkürzt und Materialabfälle minimiert werden. Ein gutes Beispiel dafür, wie die additive Fertigung die Komponenten in diesem Projekt weiterentwickelt, ist die Ariane-Turbopumpe mit einer Welle, die speziell für die PROMETHEUS-Triebwerke entwickelt und hergestellt wurde. Diese Entwicklungen führen zu einer erheblichen Reduzierung der Kosten und Komplexität von Raketenstarts und stärken somit die internationale Wettbewerbsfähigkeit der europäischen Raumfahrtindustrie.
Isar Aerospace
Eine der herausragenden Erfolgsgeschichten aus dem ESA BIC Bavaria ist das Münchner Unternehmen Isar Aerospace Technologies GmbH, benannt nach der Isar, die durch München fließt. Isar Aerospace arbeitet daran, den Zugang zum Weltraum für kleine und mittlere Satelliten sowie für Satellitenkonstellationen flexibler und erschwinglicher zu machen. Die Spectrum-Trägerrakete von Isar wurde vollständig im eigenen Haus entwickelt, wobei eine Kombination aus fortschrittlichen Materialien und Technologien zum Einsatz kommt. Eines der Ziele von Isar ist es, die Emissionen von Raketenstarts drastisch zu senken, indem herkömmliche giftige Raketentreibstoffe durch Kohlenwasserstoffmischungen ersetzt werden. Zu diesem Zweck will Isar das erste LOX/Kohlenwasserstoff-Hochleistungstriebwerk als Alternative zu Triebwerken mit toxischen Treibstoffen bauen. Isar Aerospace testet derzeit die erste seiner Raketen und ist auf dem Weg, den ersten Start im Jahr 2023 sicherzustellen.
Additive Fertigung spielte eine zentrale Rolle bei der erfolgreichen Entwicklung sowohl der Spectrum-Trägerrakete als auch des Triebwerks von Isar Aerospace – ein Projekt, bei dem EOS direkt beteiligt war. Als die Anforderungen des Unternehmens an die additive Fertigung die Möglichkeiten von „Standard“-Maschinen überschritten, ging Isar Aerospace eine Partnerschaft mit EOS und AMCM ein, um eine maßgeschneiderte Maschine zu entwickeln, die es ihnen ermöglicht, die additive Fertigung exklusiv im Haus zu nutzen und die Grenzen des Machbaren zu erweitern. Für Isar Aerospace bietet die additive Fertigung die perfekte Balance aus Formbarkeit und Weiterentwicklung. Sie ermöglicht die Entwicklung komplexer Geometrien, die schnell ihre ehrgeizten Leistungsziele erreichen, herausfordernde Fristen im Prototyping- und Fertigungsprozess einzuhalten und gleichzeitig eine höhere Teilelieferung während der Skalierung sicherzustellen.
Die additive Fertigung hat direkt zur Reduzierung der Komplexitätskosten in der Raumfahrtindustrie beigetragen, indem sie die schwersten, zeitaufwendigsten, komplexesten und teuersten Teile wie die Schubkammerbaugruppe optimiert hat. Dies erfordert eine anwendungsspezifische System- und Prozessanpassung, die durch EOS und AMCM ermöglicht wurde. Die AMCM M 450 und EOS M 290 spielen eine Schlüsselrolle bei diesem Vorhaben.
Die AMCM M 450 hat sich bereits in der New Space-Lieferkette als zuverlässiges System für missionskritische Teile etabliert und verfügt über eine der größten installierten Basis. Er ermöglicht ein großes Bauvolumen von 450 x 450 x 400 mm mit Pulverhandhabungsoption für manuelle oder halbautomatische Bedienung.
Die EOS M 290 ist für sein robustes Systemdesign und seinen leistungsstarken 400-Watt-Faserlaser bekannt, der zuverlässig Tag für Tag hohe Leistung liefert. Mit seinem mittelgroßen Aufbau und seinem vielseitigen Ansatz ist der EOS M 290 der Industriestandard für qualifizierte 3D-gedruckte Metallteile und stellt sicher, dass Isar Aerospace die Raumfahrttechnologie durch kontinuierliche Innovation weiterentwickelt.
„Als wir unsere Additive-Fertigung-Prozesse verbessern wollten, haben wir uns für die AMCM M 450 entschieden. Diese stabile Maschine von EOS, die dank der Anpassungen durch AMCM nun den erforderlichen Bauraum für unser Triebwerksdesign bietet. Wir wollen eine hohe Auslastung der Maschinen erreichen, daher ist die Nichtnutzungszeit zwischen den Druckaufträgen ein wichtiger Parameter, der reduziert werden muss. Konkret denke ich an ein vollautomatisches Pulvermanagement (d.h. Absaugen, Sieben und Nachfüllen), an dem wir mit AMCM arbeiten, um effektivere Ergebnisse zu erzielen.“
Christian Wenzl, Leiter der Fertigung bei Isar Aerospace
Die Zukunft der neuen Raumfahrt gestalten
Additive Fertigung hat sich als ein bedeutender Enabler für das Design und die Produktion von Bauteilen in der New-Space-Industrie etabliert. Sie hat es Unternehmen ermöglicht, ihre Produktionsprozesse kontinuierlich zu verbessern und die Leistungsfähigkeit der gefertigten Bauteile zu steigern. Um jedoch das volle Potenzial dieser Entwicklungen auszuschöpfen, müssen sie mit anderen Technologien integriert werden.
Die nächste Generation von Trägersystemen, Triebwerken und Modulen von New-Space-Unternehmen wird maßgeblich durch die fortlaufende Weiterentwicklung von Technologien wie digitalem Design, Künstlicher Intelligenz, neuen Materialien und Fertigungsmethoden wie der Additiven Fertigung ermöglicht. Die upstream-Anwendungen der New-Space-Industrie wachsen stark, zusätzlich zu den Mega-Satellitenkonstellationen wie Starlink von SpaceX oder Kuiper von Amazon hat kürzlich auch die EU ihre eigene Konstellation IRIS² angekündigt. Da immer mehr Unternehmen in Europa entstehen, die sich auf den Weltraum und verwandte Industrien spezialisieren, ist die Zukunft des Weltraums zweifellos global.
Autor: Vinu Vijayan