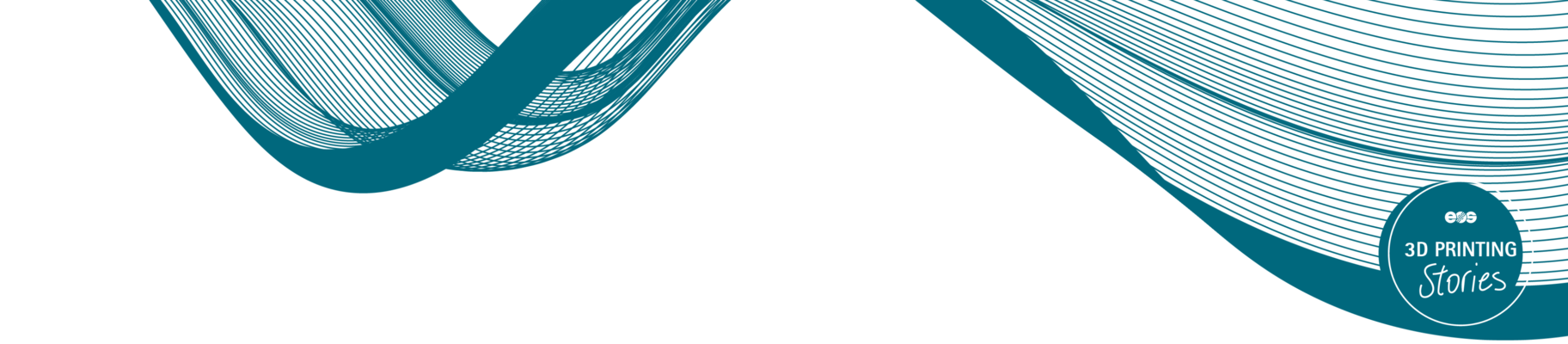
Wenn die Reise ins Unbekannte wieder beginnt
Dunlee und EOS erschließen das Potenzial von 3D-Wolframstrukturen
2. September 2024 | Lesezeit: 10 min
2007 war der Beginn der Zusammenarbeit zwischen Dunlee und EOS zum Thema Wolfram. Auslöser war die Suche nach einer Möglichkeit, die Qualität von CT-Bildern zu verbessern. Das Ergebnis waren Wolfram-Anti-Streu-Gitter - damals ein echter Durchbruch, der den Markt mehrere Jahre lang prägte. Seitdem wurde der Produktionsprozess perfektioniert, so dass heute mehr als 100.000 Gitter pro Jahr hergestellt werden. Wie es weitergeht und warum Wolfram in Luxusuhren, Teilchenbeschleunigern und im Weltraum eine Rolle spielen wird.
Zurück zu den Wurzeln: Der Weg zum Anti-Streu-Gitter
Aufgrund seiner hohen Dichte ist Wolfram ein ideales Material zur Absorption unerwünschter Streustrahlung. Dunlee wollte sich diese Eigenschaft zunutze machen, um ein Pionier bei Wolfram-Streugittern zu werden und die Bildqualität von CT-Bildern deutlich zu verbessern. Jan Philippe Grage, Business Manager 3D Printing bei Dunlee, erklärt die ersten Schritte: "Meine damaligen Kollegen waren sich schnell einig, dass eine Feinstruktur aus Wolfram nur über den 3D-Druck realisiert werden kann - doch der steckte 2007 noch in den Kinderschuhen. Bei EOS hingegen war man bereit, ins Unbekannte zu gehen.
Bis dahin waren Wände mit einer Dicke von 100 μm noch nicht mit 3D-Technik hergestellt worden. Der erste Meilenstein war erreicht, als EOS demonstrierte, dass solch feine Strukturen mit Stahl realisiert werden können. Parallel zu den technischen Machbarkeitsarbeiten wurde Dunlee davon überzeugt, in das innovative Konzept zu investieren. Es musste geklärt werden, wie die Technologie in die bestehenden Fabrikprozesse eines großen Medizintechnikkonzerns integriert werden kann. "Nachdem der Business Case genehmigt war, wurde ein weiterer wichtiger Schritt getan", sagt Grage.
Wenige Tage nach der Entscheidung lieferte EOS ein auf die Anwendung zugeschnittenes EOS M 270 3D-Drucksystem, und die Arbeit an der Prozesskette begann. Der Proof of Concept wurde 2012 erbracht, und 2014 war der erste Kunde an Bord. "Als klar war, was wir erreicht hatten - eine bis zu viermal höhere Bildqualität - war der Kunde sofort an Bord. Das war ein Durchbruch, der den Markt mehrere Jahre lang stark beeinflusst hat." In der Zwischenzeit, EOS M 290 Systeme im Einsatz, die von der EOS-Tochter AMCM auf die Bedürfnisse des Kunden zugeschnitten wurden.
Effizienter, schneller, besser: Nur der perfekte Prozess zählt
Wie überall schliefen auch in diesem Produktsegment die Konkurrenten nicht in einen Tiefschlaf ein. Akteure in Europa, China und den Vereinigten Staaten begannen, ähnliche Produkte auf den Markt zu bringen, und der Wettbewerb wurde härter. "Einerseits sind wir auf die Medizintechnik spezialisiert und kennen unsere Kunden daher viel besser als allgemeine Dienstleister. Zum anderen haben wir in den letzten Jahren intensiv an all unseren Prozessen gearbeitet, um immer effizienter zu werden", erläutert Grage die Marktstrategie von Dunlee.
Dabei wurde der gesamte Prozess berücksichtigt, von der Eingangskontrolle über den 3D-Druckprozess selbst bis hin zur Handhabung und Messung des fertigen Produkts. Ein hoher Automatisierungsgrad trug zu einer weiteren Effizienzsteigerung bei. Die Produktion läuft nun rund um die Uhr in fünf Schichten mit einem jährlichen Ausstoß von über 100.000 Gittern. Der Bauprozess selbst ist jetzt mit einem 80-µm-Prozess hocheffizient und die Toleranzen wurden auf +/-15µm reduziert. Bis 2027 soll das Volumen auf eine Million Gitter pro Jahr steigen - hergestellt mit der 3D-Drucktechnologie von EOS und AMCM.
"Wir haben unsere Kapazität mit EOS in den letzten Jahren zweimal verdoppelt, so dass wir auf beiden Seiten viel gelernt haben", erklärt Grage. "Ich denke, es ist positiv, dass wir uns gegenseitig herausfordern und mit Innovationen aufwarten. Ein EOS-Servicetechniker ist fünf Tage lang vor Ort, und wenn wir etwas anderes brauchen, kommt EOS zu uns. Das ist großartig."

Wo wollen Sie hin? Mit Wolfram neue Märkte erobern
Durch Prozessverfeinerungen und umfangreiche Datenanalysen bei der Herstellung von Antistreugittern hat Dunlee im Laufe der Jahre ein großes Fachwissen über die Verarbeitung von Wolfram entwickelt. Die Frage ist nun, wie dieses Prozesswissen für eine weitere Reise ins Unbekannte genutzt werden kann. Auch wenn der Schwerpunkt von Dunlee auf der Medizintechnik liegt, können die Technologie und das Wissen für Anwendungen in vielen anderen Branchen genutzt werden. Diese verschiedenen Märkte können nur dann in Betracht gezogen werden, wenn der gemeinsam mit EOS entwickelte Kernprozess geeignet ist. Workflow, Komponentenhandling und Verarbeitung sind unterschiedlich, aber viele Anforderungen werden bereits durch die ISO-Zertifizierung ISO13485 von Dunlee abgedeckt.
"Wir prüfen derzeit zum Beispiel Anwendungen in der zerstörungsfreien Prüfung. Auch hier müssen die CT-Systeme eine hohe Bildqualität liefern, sei es im Sicherheitsscanner am Flughafen oder beim Scannen von Produkten. Ein weiterer interessanter Bereich, so Jan Philippe Grage, ist die Kernfusion, an der weltweit intensiv geforscht wird. Mit seinem hohen Schmelzpunkt (3.422 °C) und seiner sehr hohen Materialdichte hat Wolfram zwei Eigenschaften, die für Bauteile wie Ablenkplatten, Kühlkanäle oder andere Feinstrukturen in der Infrastruktur von Teilchenbeschleunigern benötigt werden. Und dann hat Dunlee noch ein ganz anderes Segment im Auge, nämlich Luxusuhren. Warum ist das so? Grage erklärt: "Wolfram hat eine hohe Dichte und eignet sich daher für sehr kleine Bauteile, die schwer sein müssen. So kann ein Gegengewicht aus Wolfram sehr gut auf dem kleinen Raum einer Uhr eingesetzt werden.
Alles in allem gibt es viele Gründe für EOS und Dunlee, weiterhin eng an 3D-Wolframstrukturen zusammenzuarbeiten. Grage schließt ab: "Wir schätzen die Zusammenarbeit sehr und hoffen, dass wir gemeinsam die Anforderungen für die Herstellung von noch stabileren Wolframstrukturen erfüllen können. So kann die Reise weitergehen."
#3dprintingstories