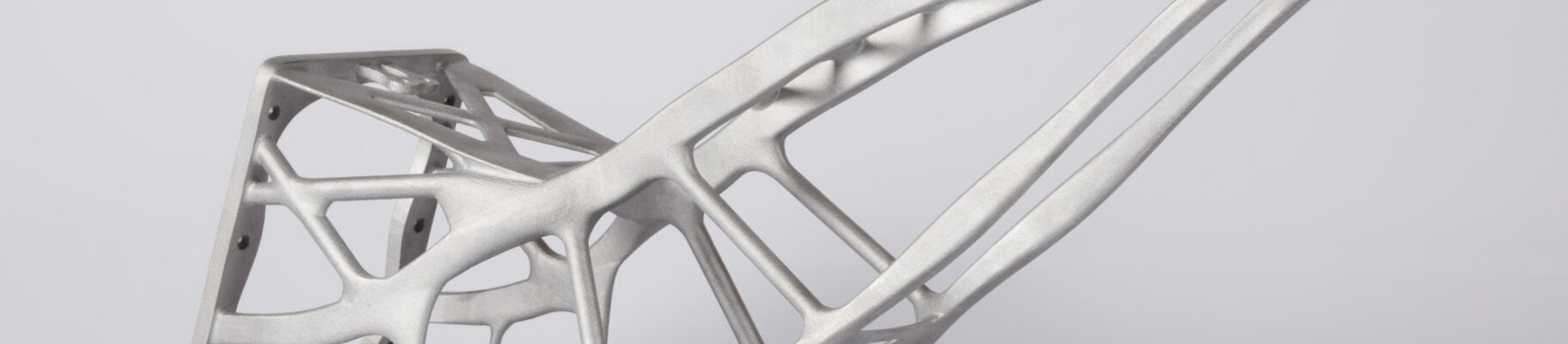
Piezas de satélites RUAG impresas en 3D
Soporte de antena para el satélite Sentinel de RUAG - Certificado para su despliegue en el espacio exterior | Innovation Story
Para mucha gente, hablar de la infinita vastedad del universo evoca historias de ciencia ficción, generalmente contadas por un estudio cinematográfico de Hollywood. Sin embargo, en la vida real, más que en ningún otro ámbito, es posiblemente en los viajes espaciales donde una voluntad firme y una visión clara son vitales para crear la tecnología necesaria y prepararla para su despliegue en el cosmos. Este fue el reto al que se enfrentó el grupo tecnológico suizo RUAG en la construcción de su satélite Sentinel, diseñado para observar nuestro planeta desde las alturas. Incluso aquí, más allá de la atmósfera terrestre, la fabricación aditiva está desempeñando un papel clave.
En cierto modo, es la cuadratura del círculo: hemos conseguido hacer un componente mucho más ligero y, al mismo tiempo, más robusto. Las características del componente han demostrado su valía en pruebas realizadas con el rigor exigido para el sector aeroespacial. En los próximos años oiremos hablar mucho más de la fabricación aditiva, ¡estoy convencido de ello!
Franck Mouriaux | Director General de Estructuras | RUAG
Desafío
Fabricación de un soporte de antena extremadamente ligero y robusto para los satélites Sentinel
Según informes del Centro Aeroespacial Alemán (DLR) de 2016, los costes de misión de la exploración espacial por kilogramo de carga útil transportada superan los 20.000 euros. Cada gramo ahorrado reduce los costes totales de lanzamiento, ya que el sistema requiere menos combustible para el ascenso. Por ello, los ingenieros aeroespaciales tienen que recortar cada gramo posible de cada componente, ya que el exceso de peso se acumula rápidamente. En este caso, el grupo suizo RUAG necesitaba un soporte de antena de diseño óptimo.
Pero no basta con optimizar el peso. Durante el lanzamiento de un cohete, la carga útil se sacude mucho y el nivel de vibración es considerable.
Además, las enormes velocidades de varios miles de kilómetros por hora, por no hablar de las elevadas fuerzas G, hacen que el vuelo no sea tan suave como cabría esperar en un avión de pasajeros. La estabilidad y la rigidez constituyen un segundo requisito esencial en cualquier hoja de especificaciones. Por desgracia, este requisito suele ser diametralmente opuesto a la necesidad de un diseño ligero.
Los ingenieros emplean estructuras complejas para encontrar un compromiso viable entre forma y peso.
El equipo de RUAG buscó la combinación óptima de resistencia y peso para la estructura de su soporte de antena, ya que se habían agotado los métodos de fabricación convencionales.
Afortunadamente, la fabricación aditiva ofrecía la posibilidad perfecta de lograr la libertad de diseño necesaria. Las pruebas de los componentes representaron un reto especial, entre otras cosas por la vibración antes mencionada. En el espacio exterior, la fiabilidad cuenta, ya que las reparaciones no suelen ser posibles. Esto explica también por qué la autorización de tales componentes es un proceso tan prolongado y complejo. Cada certificación representa un espaldarazo para los ingenieros que la han logrado.
Producción de un componente mediante fabricación aditiva que, gracias a sus estructuras complejas, cumple todos los requisitos de peso y estabilidad.
En estos casos, la cadena de producción completa desempeña un papel importante, sobre todo en el sector aeroespacial. "Obviamente, las inmensas ventajas de producir componentes mediante fabricación aditiva eran de gran interés para nosotros", explicó Franck Mouriaux, Director General de Estructuras de RUAG. "Por ejemplo, la libertad de diseño y los componentes complejos nos ayudan a ahorrar peso. La posibilidad de integrar funciones también es muy útil. Al final, sin embargo, se trata de identificar estas ventajas potenciales, aplicarlas de forma idónea y obtener la autorización correspondiente. El componente más sencillo no sirve de nada si no se puede utilizar".
Las pruebas básicas de idoneidad y rigidez constituyeron el punto de partida del diseño del soporte de antena. El siguiente paso consistió en la selección del material, la definición de los procesos y las pruebas básicas iniciales respecto a las características del material. A continuación se construyeron las primeras estructuras de prueba, que sirvieron de punto de partida para la optimización topológica del componente. RUAG consiguió finalmente la forma -teóricamente- perfecta para el soporte de la antena, gracias a una combinación de trabajo intensivo con un sistema CAD y FEM de Altair y la orientación de EOS sobre el diseño y la construcción mediante fabricación aditiva.

El soporte de la antena, de unos 40 cm de longitud, fue fabricado por citim GmbH de Barleben (Alemania) utilizando el sistema EOS M 400. Con un volumen de construcción de 400 x 400 x 400 mm, fue posible fabricar dos antenas, 30 piezas de ensayo de tracción y diversos elementos de ensayo en un solo pedido de construcción. El tiempo de construcción fue de aproximadamente 80 horas. El conjunto de parámetros utilizado fue para un grosor de capa de 60 µm, optimizado para la calidad de la superficie y la productividad.
La aleación de aluminio utilizada, EOS Aluminium AlSi10Mg, se caracteriza por su alta resistencia y su gran resistencia a la tensión dinámica, lo que hace que el material sea perfectamente adecuado para su uso en componentes sometidos a grandes esfuerzos. Se realizaron pruebas exhaustivas para demostrar las características requeridas, que en el sector aeroespacial suponen hasta el 80% del alcance total de un proyecto. Para las pruebas se utilizaron estructuras fabricadas especialmente. Entre otras cosas, los ingenieros examinaron los soportes en tomógrafos computerizados. También se realizaron diversos procedimientos mecánicos y físicos. En ocasiones, las tensiones ejercidas sobre el componente superaron deliberadamente los límites de carga, lo que en última instancia provocó la destrucción de las piezas de prueba.
EOS combina la innovación con una gran experiencia en fabricación aditiva. Los sistemas ofrecen posibilidades realmente interesantes para todos los mercados de todos los sectores.
Dipl.-Ing. Andreas Berkau | CEO | citim GmbH
Resultado
El resultado de estos esfuerzos fue que el nuevo soporte de antena para los satélites Sentinel superó todas las expectativas. El componente obtuvo la certificación y, con ella, la aprobación para su utilización en el espacio exterior. El logro es aún más notable si se tiene en cuenta que el uso de la fabricación aditiva en el espacio está todavía en pañales.
Por ejemplo, se superaron en más de un 30 % los requisitos mínimos de rigidez del componente, un margen fácilmente suficiente para asegurar que, incluso tras un vuelo turbulento, se pudiera alcanzar una posición ideal de la antena, y garantizar la comunicación por radio con la Tierra. El nivel de estabilidad exigido se logró, en parte, gracias a la distribución altamente uniforme de las tensiones.
Además, el uso de la fabricación aditiva permitió reducir considerablemente el peso del componente final: de 1,6 kg a 940 g, lo que representa un ahorro de más del 40 %.
En este caso, el uso de tecnología innovadora logró una combinación improbable: mejores características de los componentes y menores costes del sistema. "Estamos muy contentos con los resultados de este proyecto. Nos adentramos en un territorio desconocido en lo que respecta al proceso y nos vimos recompensados con un componente estable y ligero", afirma el ingeniero aeroespacial Mouriaux.
"La fabricación aditiva ha demostrado que puede satisfacer las exigencias de procedimiento fundamentales de los viajes espaciales. Las múltiples ventajas de diseño y las características del propio componente así lo han demostrado. Veo un gran potencial para esta tecnología de cara al futuro".
Resumen de los resultados
- 30% Rigidez - Los requisitos mínimos se superan en un 30%.
- 40% Reducción de peso
Otras ventajas
- Inteligente: la libertad de diseño permite una distribución uniforme de las fuerzas
- Acreditado: requisitos del sector aeroespacial verificados mediante pruebas exhaustivas
Más información
Explore tres décadas de excelencia pionera en impresión 3D con EOS