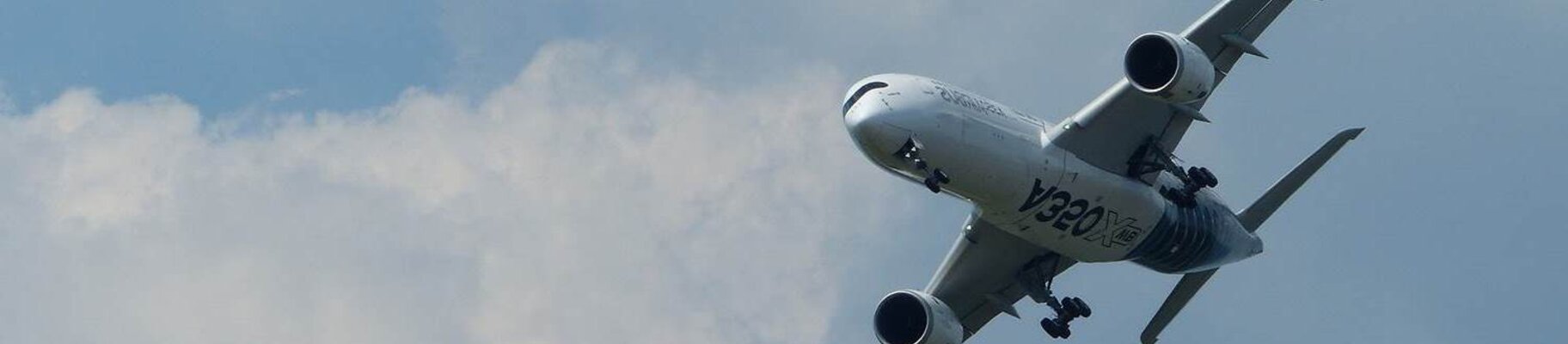
Fabricación aditiva de alta tecnología de Sogeti para el nuevo Airbus A350 XWB
Ruteado de cables del A350 XWB: del diseño al componente en dos semanas | Historia de éxito
El momento en que un avión comercial completamente nuevo surca los cielos por primera vez es siempre especial, y esto fue especialmente cierto en el caso del Airbus A350 XWB. Como hijo del nuevo milenio, estaba claro desde el principio que el trabajo de desarrollo se centraría en materiales y procesos de producción innovadores: el objetivo no era otro que construir el avión más eficiente del mundo. Como tecnología del futuro, la fabricación aditiva era otra posibilidad que había que tener en cuenta durante el desarrollo. Como parte de un proyecto piloto, los expertos de Sogeti High Tech consiguieron desarrollar un soporte de cable en el larguero delantero del estabilizador vertical para el avión de pasajeros en un tiempo récord, tardando sólo dos semanas desde el boceto inicial hasta la pieza acabada. La tecnología y los conocimientos de EOS fueron un aspecto fundamental de este proceso de desarrollo.
"Conseguir un componente existente 'FA-ready' en sólo dos semanas significaba que teníamos que tener éxito a la primera. La excelente y proactiva colaboración con EOS hizo posible esta ambiciosa empresa, con resultados extraordinarios."
Carlos Ribeiro Simoes | Additive Manufacturing Offering Leader | Sogeti High Tech
Desafío
Desarrollo y producción en tiempo crítico de un soporte de guiado de cables para una cámara en el estabilizador vertical del A350 mediante fabricación aditiva.
En concreto, el proyecto consistía en fabricar un soporte de conducción de cables para el último modelo de Airbus. En última instancia, el soporte era necesario para la alimentación eléctrica y el transporte de datos de una cámara situada en el estabilizador vertical, que proporciona una vista del exterior a los pasajeros y orientación sobre el terreno a los pilotos.
El documento de requisitos del producto exigía un componente funcionalmente operativo y apto para la producción en serie. Esta tarea se confió a Sogeti High Tech, filial al 100% de Cap Gemini S.A., que cotiza en la bolsa de París.
El reto particular en este caso era el breve plazo de entrega, de sólo dos semanas. Había que completar todo el desarrollo en este plazo: Desde el análisis de la pieza y de la configuración actual del montaje, un estudio de parámetros destinado a optimizar la topología y su interpretación, y el diseño y producción de la pieza acabada. Además, el montaje debía tener el menor número posible de estructuras de soporte para evitar el postprocesado.
Además, las especificaciones del componente exigían la integración del portacables a presión, la reducción del peso y el cumplimiento de los estrictos requisitos para la posterior certificación de la industria aeronáutica.
El componente fabricado convencionalmente estaba compuesto por piezas de chapa conformada y numerosos remaches: más de 30 piezas individuales en total. Los conectores de la zona superior eran de plástico y, por tanto, de un material distinto al de las demás piezas del soporte. El objetivo era desarrollar una solución integrada consistente en una única pieza que incluyera también los conectores, reduciendo así significativamente los tiempos de construcción e instalación. El objetivo de reducción de peso para la fabricación aditiva se determinó mediante un estudio de parámetros basado en la optimización de la topología.
Solución
La reducción a un solo componente y la fabricación en una EOS M 400 minimiza el tiempo de producción a 19 horas.
Para el nuevo componente, Sogeti High Tech siguió el proceso de desarrollo probado para diseñar piezas de fabricación aditiva. El proyecto comenzó con un análisis del componente existente, fabricado convencionalmente, en términos del proceso de fabricación futuro, con un resultado extremadamente positivo. La funcionalidad, el material y la compleja estructura anterior del componente lo convirtieron en un candidato ideal para la tecnología de impresión 3D basada en lecho de polvo de EOS. La libertad de diseño que ofrece esta tecnología permite fabricar estructuras complejas en una sola pieza, lo que significa que se puede optar por un diseño que ahorre peso sin descuidar la integración funcional.
Este análisis permitió definir el llamado espacio de diseño, es decir, el espacio que puede ocupar el soporte para el paso de cables. Se eligió como material la aleación de aluminio AlSi10Mg, ideal para estructuras complejas de paredes finas. Las interfaces con las zonas externas permanecieron inalteradas, formando el espacio no diseñado, lo que significa que no fue necesario realizar cambios en ellas. Las cargas definidas se tomaron como condiciones límite para la optimización de la topología en el estudio de parámetros, proporcionando la base para un nuevo diseño.
Como es habitual, se utilizó software CAE para los cálculos de optimización topológica; en cambio, para el rediseño se empleó una solución dedicada al diseño de estructuras con superficies de forma libre. Sogeti High Tech se encargó del diseño. Para cumplir el plazo de entrega de dos semanas, EOS calculó el tiempo de construcción y los parámetros optimizados a partir de los resultados de la optimización topológica utilizando el software EOSPRINT. De este modo se creó la implementación CAE para la pieza fabricada, al tiempo que se tenían en cuenta las posibilidades y limitaciones del proceso de fabricación y la necesidad de evitar estructuras de soporte.
"Además de un hardware excepcional, EOS también ofrece una amplia experiencia en hacer realidad componentes fabricados de forma aditiva, algo que valoramos muy positivamente."
Carlos Ribeiro Simoes | Additive Manufacturing Offering Leader | Sogeti High Tech
Resultados
Gracias a la cooperación entre Sogeti y EOS, fue posible desarrollar un componente optimizado para la fabricación aditiva que aprovecha plenamente la libertad de diseño que ofrece la tecnología DMLS y, al mismo tiempo, tiene en cuenta sus restricciones. Esto permitió integrar en el diseño conectores para el paso de cables e incorporar refuerzos locales en zonas críticas específicas con el fin de optimizar la estructura. Las aberturas autoportantes y los puntales dentro del componente ayudan a mantener al mínimo el esfuerzo y, por tanto, los costes de postprocesado.
Además, el soporte puede fabricarse con extrema rapidez, siempre que se necesite. La fabricación -que se realiza en un EOS M 400 con espesores de capa de 90μm- sólo lleva 19 horas, en lugar de los 70 días que se necesitaban antes.
Esto corresponde a una reducción del tiempo de producción muy superior al 90 %. Esto se debe en gran parte a que los numerosos pasos individuales y las antiguas 30 piezas se han reunido en un componente central que ahora puede fabricarse en una sola tirada. Además, ya no es necesario fabricar y almacenar las piezas individuales, lo que puede resultar caro. El almacenamiento de todo el conjunto de componentes también es ahora mucho más sencillo.
Sogeti no sólo pudo ahorrar una enorme cantidad de tiempo en la producción, sino también en el desarrollo. Todo el proceso, desde el boceto inicial hasta el componente acabado, duró sólo dos semanas. Es un plazo de entrega fenomenal. Al mismo tiempo, el diseño también supone una mayor eficiencia en cuanto al peso.
Mientras que la pieza original de fabricación convencional pesaba 452 gramos, el soporte de cable de fabricación aditiva pesa sólo 317 gramos, y es bien sabido que la industria aeronáutica cuenta cada gramo para reducir al mínimo el consumo de combustible. El cliente, Airbus, quedó más que satisfecho con los resultados.
Resumen de los resultados
- -29 Piezas únicas Integración funcional
- -90% Reducción del tiempo de producción
- -135 Gramos Reducción de peso
Más información
Explore tres décadas de excelencia pionera en impresión 3D con EOS