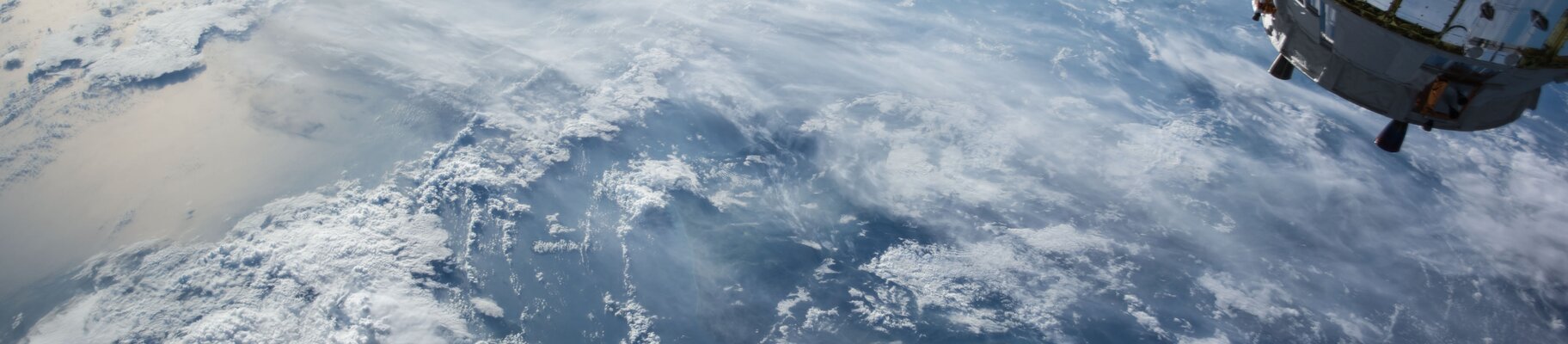
Motores para cohetes
Datos meteorológicos, comunicaciones, sistemas de posicionamiento global, imágenes y mapas mundiales: cada vez son más los servicios que aprovechan los pequeños satélites o que, en algunos casos, dependen completamente de ellos. Para poner en órbita estos microsatélites se necesitan pequeños lanzadores. La demanda de estos lanzadores no deja de aumentar. En los últimos años, esta industria del "Nuevo Espacio" ha florecido rápidamente con muchas empresas de nueva creación y especializadas en su desarrollo. La empresa que consiga lanzar al espacio la mayor carga útil con el motor más eficiente ganará la carrera.
La fabricación aditiva es el método clave para mantener bajos los costes sin renunciar a un diseño óptimo del motor, pero esto sólo funciona si el motor puede imprimirse en 3D como una sola pieza.
Impresión en 3D de un motor de cohete
La impresión 3D ofrece ventajas decisivas a la hora de construir motores para cohetes. Además, la funcionalidad de las piezas se puede reimaginar y reinventar por completo: por ejemplo, se pueden integrar canales de refrigeración integrales en una cámara de combustión o consolidar varias piezas en un único diseño todo en uno.
"Con el apoyo de EOS y AMCM, la empresa de nueva creación estadounidense LAUNCHER trabaja en el lanzamiento al espacio de cargas útiles de tamaño pequeño y mediano de forma más eficiente que nunca. Los resultados incluyen diseños de cohetes novedosos e innovadores - y el motor de cohete más grande del mundo que jamás se haya fabricado aditivamente en una sola pieza."
El motor se basa en un diseño de cohete estándar, pero se ha ampliado con nervaduras internas para una refrigeración óptima. LAUNCHER construyó, probó y siguió desarrollando con éxito este nuevo diseño de forma rápida y rentable, íntegramente gracias a la impresión 3D.

El motor cohete impreso en 3D de una sola pieza más grande del mundo
Los obstáculos eran, entre otros, el tamaño del espacio de construcción y las difíciles propiedades del material. AMCM, una empresa del grupo EOS que ofrece máquinas especializadas adaptadas a las necesidades del cliente, aceptó este reto.
"La cámara de combustión, impresa en 3D a partir de una aleación de cobre en las máquinas M4K de AMCM, es la mayor cámara de combustión de una sola pieza para motores de cohetes líquidos del mundo".
La cámara tiene una altura de 86 cm y un diámetro de la tobera de salida de 41 cm. El propulsor ganó recientemente un premio de 1,5 millones de dólares en el US Air Force Space Pitch Day, celebrado para acelerar el programa de desarrollo y pruebas del propulsor E-2. Ya se han planificado los primeros ensayos a gran escala. La animación muestra la cámara de combustión completa con piezas de fabricación aditiva y convencional.

"Tradicionalmente, la fabricación de este tipo de piezas requiere millones de dólares de inversión en máquinas a medida. Ahora, con la impresión 3D existe la opción de imprimir la cámara de combustión, la boquilla y el cuello combinados en una sola pieza. Gracias a este avance, nuestro trabajo es más fácil que nunca".
Max Haot, Fundador Launcher
Estudio de caso
Cabezal de inyección para motores de cohetes Ariane 6
ArianeGroup eligió la impresión 3D industrial para producir un componente crucial del motor de su nuevo cohete propulsor Ariane 6, con el objetivo de consolidar las 248 piezas originales y reducir los costes unitarios. En colaboración con el equipo de EOS Additive Minds, analizaron los riesgos, estimaron los costes y optimizaron el proceso de producción, incluido el diseño de la disposición y la planificación del flujo.
La colaboración dio muy buenos resultados:
- -2165 horas de reducción del tiempo de producción
- -50 % de reducción de costes
- -247 piezas individuales reducidas a una sola pieza
- integración funcional
Vea el siguiente vídeo para obtener más información.
"El programa Ariane combina nuestra fuerza innovadora con la experiencia de EOS. Juntos estamos preparando la fabricación aditiva de la cabeza de inyección de un motor cohete. Los resultados son impresionantes: un tiempo de producción significativamente menor y una reducción de costes del 50 %."
Dr.-Ing. Steffen Beyer, Jefe de Tecnología de Producción - Materiales y Procesos en ArianeGroup