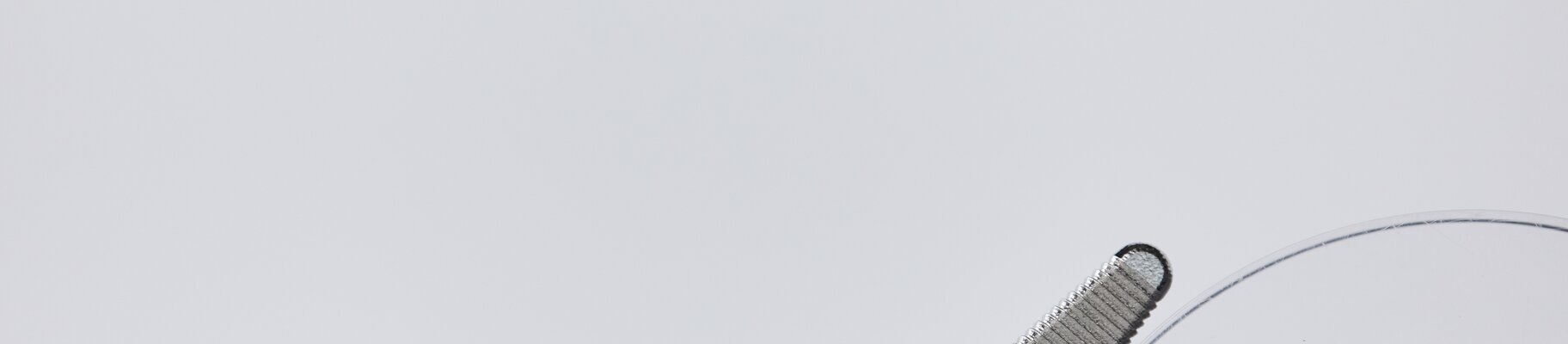
Impresión 3D para tecnología médica
Producción personalizada y optimizada
Crear innovaciones que marquen la diferencia
La fabricación aditiva ofrece a la industria médica una gran libertad de diseño, adaptabilidad e integración funcional. Para los fabricantes de prótesis dentales, productos de tecnología médica y ortopédica, órtesis y prótesis, esto crea muchas oportunidades de gran alcance. Existe un control total sobre las formas, los materiales y los diseños específicos basados en datos específicos del paciente, lo que hace posible ofrecer tratamientos más individuales, simplifica la reconstrucción biomecánica y permite aplicar rápidamente métodos terapéuticos innovadores.
"Con más de 30 años de experiencia en la fabricación de todo tipo de máquinas y soluciones para la fabricación aditiva, hemos acompañado y apoyado a nuestros clientes a través de una diversa gama de proyectos médicos emocionantes e innovadores. Al hacerlo, hemos aprendido a entender los requisitos específicos de este mercado."
Diseñamos nuestra tecnología de producción para reflejar nuestro conocimiento de los retos asociados a las certificaciones y los requisitos específicos de los materiales. Para una mejor atención al paciente.
Pasar de las soluciones estandarizadas a un enfoque específico para cada paciente
Con la fabricación aditiva, las prótesis, órtesis e implantes dentales pueden fabricarse directamente a partir de los datos anatómicos individuales de cada paciente. El resultado son productos personalizados disponibles rápidamente, lo que mejora notablemente el proceso de curación y el pronóstico.
La impresión 3D industrial abre oportunidades de gran alcance para los fabricantes de prótesis dentales, productos de tecnología médica y ortopédica, órtesis y prótesis: el potencial de personalización de los productos, combinado con la rentabilidad, permite fabricar productos mejores y más viables económicamente y desarrollar nuevos modelos de negocio.

De las soluciones estandarizadas a la mejora de la funcionalidad
La capacidad de crear geometrías complejas e integrar la funcionalidad con el proceso de fabricación aditiva genera grandes ventajas en la tecnología ortopédica y a la hora de fabricar equipos médicos complejos.
Nuestras tecnologías se utilizan en implantes personalizados desde hace varios años. En casos complejos, tratamiento del cáncer, revisión de implantes o accidentes graves, estos pacientes pueden beneficiarse de la tecnología de fabricación aditiva de EOS, que permite diseñar y disponer rápidamente de un producto específico y potencialmente muy complejo en función de su diagnóstico individual. La tecnología de impresión EOS 3D también puede utilizarse para crear una amplia variedad de estructuras superficiales, lo que puede simplificar procesos como la osteointegración, es decir, el crecimiento entre el tejido óseo vivo y la superficie del implante óseo.
En el caso de los equipos médicos de alta tecnología y las máquinas especializadas, la libertad de diseño permite simplificar los ensamblajes e integrar la funcionalidad en la pieza. En estos casos, la fabricación aditiva puede resultar rentable incluso con lotes pequeños. Se eliminan los costes de herramientas, así como los de montaje y logística.
Con la impresión 3D, el diseño se rige por la funcionalidad y ya no por la fabricabilidad. Ya sea para fabricar implantes, instrumentos quirúrgicos o productos complejos de tecnología médica: la fabricación aditiva le permite reimaginar la geometría. Como resultado, puede diseñar y fabricar sus productos de forma más eficiente para sus aplicaciones específicas.

Impresión 3D de implantes e instrumentos quirúrgicos
Implantes e instrumentos quirúrgicos específicos para cada paciente y de gran precisión gracias a la impresora 3D
La tecnología de fabricación aditiva EOS crea instrumentos e implantes de ajuste preciso directamente a partir de datos CAD.
El proceso fabrica implantes a partir de datos anatómicos recogidos del usuario y permite entregarlos rápidamente. Esto evita tiempos de espera o complicaciones debidas a largos periodos de inactividad, por lo que los implantes se ajustan mejor. También acelera el proceso de cicatrización en su conjunto y tiene un efecto positivo duradero en la calidad de vida del paciente.
"Los productos pueden diseñarse para reflejar el diagnóstico, sin importar su nivel de complejidad, pueden fabricarse y entregarse en la clínica en el menor tiempo posible. La fabricación convencional tarda unas 6 semanas, mientras que con la fabricación aditiva, la producción es posible en solo 10 días."
La fabricación aditiva mediante EOS también puede utilizarse para crear una amplia variedad de estructuras superficiales, lo que puede simplificar procesos como la osteointegración, es decir, el crecimiento entre el tejido óseo vivo y la superficie del implante óseo. Las aplicaciones de los implantes impresos en 3D incluyen implantes de columna vertebral, articulaciones de hombro (reemplazo glenoideo, implantes de cadera) e implantes para el área OMF (cirugía oral y maxilofacial).
Para las intervenciones complicadas, los cirujanos recurren cada vez más a instrumentos de un solo uso específicos para cada paciente. Esto permite insertar los implantes con mayor precisión, lo que aumenta el éxito de la operación para pacientes, cirujanos y hospitales. Estos instrumentos personalizados también pueden fabricarse con una impresora 3D. El cirujano se beneficia de un producto de alta calidad y precisión que cumple las estrictas normas asociadas a las aplicaciones médicas.
La alternativa impresa en 3D permite una mayor variedad ("personalización masiva"), y la producción puede realizarse "bajo demanda". En comparación con los instrumentos de uso múltiple, los hospitales ahorran en costes de esterilización y almacenamiento y se benefician de una mayor productividad.







La impresión 3D en la práctica
Permedica: impresión en 3D de un cotilo de cadera artificial

Para ver el vídeo tiene que aceptar las cookies de marketing.
Estructura superficial para mejorar la osteointegración
El implante puede optimizarse considerablemente gracias a la impresión en 3D. La copa de la cadera consta de secciones fijas para proporcionar la estabilidad necesaria y elementos con estructuras rugosas. Estos elementos se estructuran directamente para garantizar un anclaje firme del implante: las estructuras rugosas son ventajosas en términos de transmisión de la presión, mientras que las estructuras más pequeñas favorecen la fijación inicial. De este modo, la compleja estructura simplifica la osteointegración, acelerando el proceso de cicatrización.
Es posible una producción flexible
Junto con el equipo de EOS Additive Minds y el consolidado sistema de EOS M 290 para metales, Permedica consiguió crear un producto completamente nuevo. Todo el implante se fabrica en un único paso de producción en la impresora 3D y sería increíblemente difícil de reproducir con métodos de fabricación convencionales. Gracias a la gran flexibilidad de la fabricación aditiva, la superficie y el tamaño de la copa de la cadera pueden especificarse individualmente para cada paciente.
informe técnico :Estudio de capacidad de múltiples máquinas para estructuras reticulares
Este informe técnico investiga el rendimiento de un diseño de trabajo estandarizado con estructuras reticulares impreso en tres sistemas EOS M 290 diferentes utilizando EOS Titanium Ti64ELI. En pocas palabras, los resultados verifican que
-
La capacidad de repetición de máquina a máquina queda demostrada, ya que tanto la densidad relativa como la resistencia a la compresión alcanzan el nivel de confianza Six Sigma.
-
Existe una alta correlación entre la densidad relativa y la resistencia a la compresión.
-
El alcance y el esfuerzo de las pruebas pueden reducirse gracias a esta alta correlación
¿Quieres saber más? Obtén la versión gratuita informe técnico aquí.

Casos de éxito de EOS
Productos implantológicos con sistemas de fabricación de EOS

Desarrollo de materiales biocompatibles para implantes
Caso de éxito|Universidad de Michigan
La Universidad de Michigan utiliza una FORMIGA P 100 para fabricar implantes individualizados que salvan vidas de niños. Junto con EOS desarrollan nuevos materiales biocompatibles.

Implantes craneales producidos con fabricación aditiva
Historia de éxito de un cliente | Alphaform
Desarrollo y fabricación de un implante de ajuste de precisión para la zona craneal con especial permeabilidad para líquidos y disipación de calor.
Instrumentos para medicina fabricados aditivamente




BodyCad: Sistema de guías quirúrgicas para operaciones de rodilla
Para ver el vídeo tiene que aceptar las cookies de marketing.
Junto con BodyCad, EOS ha desarrollado una plantilla de fresado quirúrgico para artroplastia de rodilla personalizada. El sistema ofrece un método más preciso y controlado para preparar el hueso para el implante. Se desarrolló una combinación de un implante específico para el paciente y una plantilla de perforación quirúrgica para facilitar intervenciones precisas de sustitución o restauración de la rodilla que reflejen las características anatómicas y el sistema musculoesquelético del paciente.
El resultado fue un revolucionario sistema unicompartimental de rodilla (UKS) con instrumental quirúrgico específico para cada paciente. Los instrumentos de nueva fabricación, con plantillas de perforación personalizadas, garantizan una mayor precisión a menor coste, tiempos de operación reducidos y mejores resultados clínicos. Fabricado en una FORMIGA P 110 con el material PA 2201.
- Eficaz: los instrumentos pueden crearse rápidamente
- Rentable: menores costes en comparación con los procesos convencionales
- Puntualidad: el instrumental específico para cada paciente puede entregarse en 21 días
Plataformas estereotácticas para neurocirugía
Producción en serie reducida de componentes quirúrgicos de precisión con una FORMIGA P 100.

Nuestras soluciones de fabricación aditiva para tecnología ortopédica
La fabricación aditiva ayuda a optimizar el tratamiento de los pacientes, reducir las estancias hospitalarias y paliar los efectos secundarios. Con nuestros sistemas, puede fabricar implantes e instrumentos individuales a partir de materiales de alta calidad compatibles con la medicina y basados en datos CAD 3D. Ya sea a partir de materiales metálicos o poliméricos, nuestras soluciones de impresión 3D permiten la producción sin herramientas de productos altamente personalizados a bajo coste unitario dentro de un marco rentable.
Le ayudamos a implantar sus productos
Con el sistema de impresión 3D adecuado y nuestros completos servicios de consultoría y formación, nuestros clientes dominan con éxito su entrada en la fabricación de implantes e instrumentos de alta precisión y específicos para cada paciente.
Nuestra cartera de soluciones integradas
Su solución de producción de una sola mano
Ofrecemos soluciones de fabricación 3D específicas para cada cliente para toda la cadena de valor: desde la concepción, el diseño y la ingeniería hasta la producción y el posprocesamiento, pasando por la pieza acabada. Benefíciese de más de 30 años de experiencia en fabricación aditiva y aproveche nuestra completa cartera de sistemas, consultoría y servicios para la impresión 3D industrial de tecnología e instrumentos ortopédicos, todo de un único proveedor. Junto con usted y nuestra eficaz red de socios, podemos desarrollar las soluciones que necesita para su propia producción para conseguir una completa cartera de soluciones.
Fabricación aditiva para laboratorios y equipos médicos
Desarrollo y producción más rápidos, flexibles y rentables
Para los equipos de laboratorio y los sistemas de imagen médica (también conocidos como diagnóstico por imagen o simplemente imagen, por ejemplo, equipos de TC, TRM o rayos X), la fabricación aditiva es una tecnología de producción que ofrece nuevas oportunidades para optimizar tanto el producto como los costes de fabricación.
Muchos dispositivos médicos y piezas para equipos de laboratorio son productos nicho complejos que sólo se fabrican en pequeñas series. La producción convencional suele requerir herramientas caras cuyo coste hay que añadir a los productos. En cambio, la fabricación aditiva funciona sin herramientas, lo que permite fabricar piezas en series más pequeñas, de hasta un lote.
El proceso de producción se basa en los datos CAD de las piezas. Esta tecnología ofrece libertad de diseño, así como la opción de integrar funcionalidades directamente en la pieza. Los resultados son plazos de comercialización más cortos y un amplio abanico de posibilidades de optimización del producto.
Obtenga más información aquí sobre qué piezas de equipos de laboratorio y equipos de diagnóstico por imagen se pueden optimizar ya hoy con la impresión EOS 3D, y qué máquinas y materiales son los adecuados para su aplicación.
-
Producción sin herramientas y costes de montaje reducidos
-
Diseño flexible e integración funcional
-
Ciclos de desarrollo y plazos de comercialización más rápidos
3 piezas de montaje en lugar de 32: el rotor de lavado de Hettich
Los fabricantes de centrifugadoras Hettich mejoraron notablemente la rentabilidad de su producción en serie con la fabricación aditiva y aprovechan plenamente las ventajas de la impresión 3D. Hettich inventó y patentó un nuevo tipo de centrifugadora que permite sedimentar y separar los componentes sanguíneos en un único dispositivo.

Para ver el vídeo tiene que aceptar las cookies de marketing.
El ROTOMAT consta de un mototambor con seis contenedores y bandejas de recogida. Los contenedores tienen una geometría elaborada y se colocan a altas velocidades de rotación, con aceleraciones de hasta 1.200 veces la aceleración debida a la gravedad. Las centrifugadoras utilizan la fuerza centrífuga para separar las mezclas en sus componentes. Las aplicaciones típicas incluyen la preparación de muestras de sangre o la realización de un análisis de sangre. Cuando se fabrica de forma convencional, cada rotor de lavado consta de 32 piezas separadas que hay que ensamblar. Esto requiere herramientas complejas y un largo proceso de montaje, sobre todo porque hay que desbarbar minuciosamente los inyectores de acero inoxidable.
El cambio a la tecnología EOS ha merecido la pena para Hettich, con cifras excepcionales
- El rotor de lavado se rediseñó y ahora consta de 3 piezas de montaje en lugar de 32, con una funcionalidad mejorada.
- Los contenedores se fabrican sin herramientas, lo que reduce los costes de producción.
- Las pequeñas producciones en serie y los ajustes regionales pueden realizarse fácilmente.
- El montaje ya no requiere herramientas y se elimina por completo el paso de desbarbado, que lleva mucho tiempo.
Estructuras complejas, detalles delicados, integración funcional
La fabricación aditiva abre un amplio abanico de oportunidades para los equipos de diagnóstico médico por imagen. Con el proceso de impresión 3D pueden realizarse geometrías individuales muy complejas, incluidas estructuras que no serían posibles con la fabricación convencional. Por ejemplo, se pueden mejorar y fabricar de forma más rentable piezas para sistemas de tomografía computarizada o resonancia magnética o equipos de rayos X.

Impresora 3D para rejillas antidispersión
Las rejillas de rayos X (rejillas antidispersión) capturan los rayos X desviados por el tejido corporal del paciente antes de que lleguen a la película o placa de imagen. Esto mejora el contraste y la precisión de las radiografías. La fabricación convencional de rejillas de rayos X es extremadamente difícil y requiere mucho tiempo, por lo que resulta muy costosa.
Pero la impresión en 3D permite fabricar el sofisticado diseño según un enfoque nuevo y optimizado. El sistema EOS M 290 combinado con el material EOS Tungsteno W1 es la primera y única solución disponible actualmente en el mercado para el exigente reto de fabricar rejillas de rayos X. Supone una gran ventaja y tiene un coste por unidad más atractivo que la fabricación por métodos convencionales.

Fabricación aditiva para un ajuste perfecto
Producción de prótesis y órtesis mediante impresión 3D
Ofrecemos sistemas, materiales y procesos, software y servicios: todo lo que necesita para la impresión 3D de prótesis y órtesis. Con nuestras soluciones, los técnicos ortopédicos y las empresas se benefician de datos fiables, procesos estables y décadas de experiencia en el mercado.
¿Por qué impresión 3D? Con los procesos de fabricación convencionales, el modelo debe adaptarse manualmente a cada paciente. El gran número de pasos necesarios hace que la producción sea cara y lleve mucho tiempo.
En términos de personalización y rentabilidad, los métodos de producción convencionales como la fundición, el moldeado, el modelado y el fresado alcanzan rápidamente sus límites.
La fabricación aditiva ofrece las máximas ventajas para pacientes y fabricantes. El proceso de fabricación se basa en los datos de escaneado individuales de cada paciente, lo que significa que las prótesis y órtesis impresas en 3D se adaptan de forma óptima a la anatomía y los requisitos del usuario.
"Las órtesis y prótesis ayudan a sus usuarios a conseguir una mejor movilidad. Pero cada usuario tiene una anatomía, un uso y unas necesidades terapéuticas diferentes. Las soluciones de impresión 3D de EOS combinan con éxito procesos de fabricación rápidos y una comodidad óptima para el usuario."






Ventajas de la fabricación aditiva para órtesis y prótesis
- Posibilidades de personalización prácticamente ilimitadas en términos de diseño y funcionalidad
- Comodidad óptima para el usuario: diseño ligero y estable a pesar de las estructuras complejas
- Sostenible: menos consumo de material, ya que el material sobrante puede reutilizarse.
- Los ajustes necesarios pueden aplicarse rápidamente, por ejemplo con niños que aún están creciendo.
- Mayor comodidad gracias a la integración funcional para una mayor elasticidad, diseños transpirables, etc.
- Proceso totalmente digital, desde el escaneado hasta el producto acabado, para una disponibilidad más rápida
Fabricación de prótesis de pie a medida
Mecuris ofrece una plataforma digital para pacientes, médicos, talleres ortopédicos y proveedores médicos. A partir de los datos que se les envían, ofrecen la fabricación por encargo de prótesis impresas en 3D en sistemas EOS.
Los pies protésicos personalizados permiten caminar con naturalidad. El proceso de fabricación aditiva reduce significativamente el plazo de entrega, consigue la máxima comodidad y permite un diseño personalizado.

Para ver el vídeo tiene que aceptar las cookies de marketing.
La ciclista paralímpica Denise Schindler
Prótesis óptimas gracias a la impresión 3D de EOS y Mecuris
Para ver el vídeo tiene que aceptar las cookies de marketing.
Ortesis infantiles de ajuste perfecto
La empresa británica Andiamo utiliza sistemas EOS para fabricar órtesis a medida para niños. Tradicionalmente, las órtesis se fabrican a partir de impresiones de yeso. Este proceso es lento, consume muchos recursos y ofrece poco margen de personalización.
Algunos pacientes, especialmente los jóvenes que aún están creciendo, tienen que someterse a este procedimiento repetidamente. El tiempo de espera puede durar hasta seis meses, para una órtesis que quizá ni siquiera encaje cuando esté lista. La fabricación aditiva reduce el tiempo de espera al mínimo. Con un escáner corporal en 3D se fabrica una órtesis precisa y perfectamente ajustada, que se entrega en una semana.
