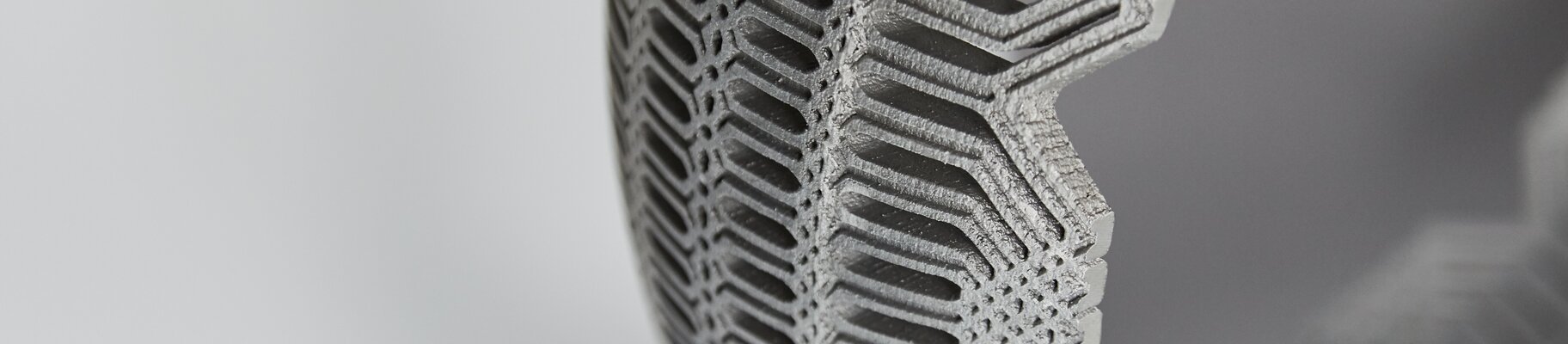
La impresión 3D en el sector manufacturero
Aplicaciones y ejemplos prácticos
Buenas prácticas para la impresión 3D en entornos de fabricación y producción
La presión de los costes, los requisitos normativos, las crecientes exigencias de los clientes y mucho más. Las empresas de la producción y la industria se enfrentan a una colección de retos en constante expansión. Al mismo tiempo, cuestiones como la eficiencia energética y de los recursos son cada vez más importantes.
La fabricación aditiva ofrece un amplio espectro de posibles ventajas rentables y sostenibles a las empresas de la producción y la industria.
La impresión 3D industrial abre nuevas oportunidades y ofrece soluciones de muchas formas distintas, desde la producción de piezas hasta la optimización del retorno de la inversión. En EOS, ofrecemos soluciones personalizadas de un único proveedor para la tecnología y todo lo que necesite para una transición rápida y segura.