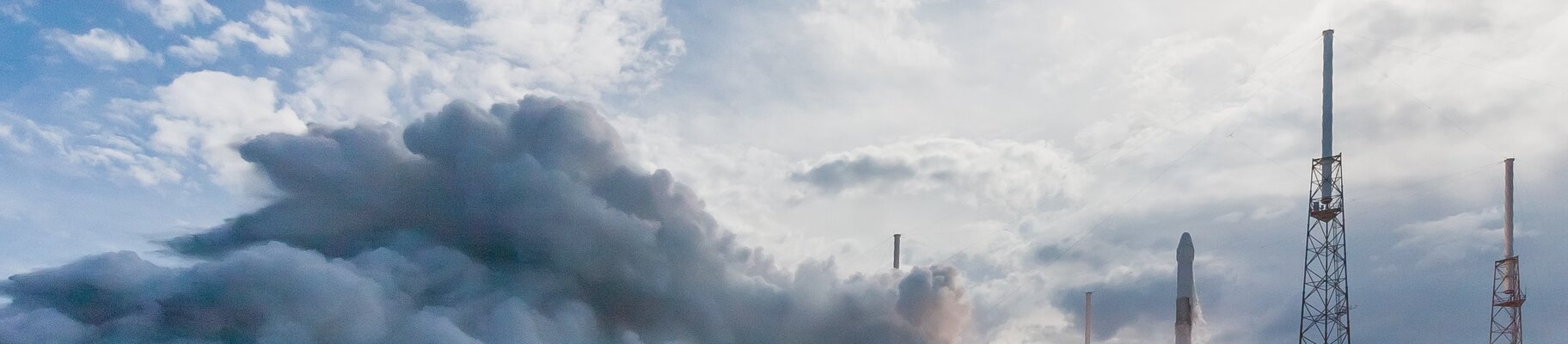
Simplificación del futuro módulo de propulsión de Ariane
ArianeGroup | Historia de innovación
Diseño todo en uno - 122 boquillas de inyección y otras piezas como un componente integrado
"Misión crítica" describe a la perfección los componentes de Clase 1 utilizados en la industria aeroespacial. De estos componentes dependen misiones que cuestan cientos de millones. En consecuencia, los ingenieros buscan constantemente desarrollar componentes de la máxima calidad, funcionalidad y robustez, simplificando al mismo tiempo la cadena de fabricación y reduciendo el número de elementos individuales. Gracias a la tecnología de fabricación aditiva EOS, ArianeGroup ha conseguido llevar esto a un nivel completamente nuevo: En lugar de 248 elementos, la cabeza del inyector de un motor de cohete de un futuro módulo de propulsión de la etapa superior cuenta ahora con un solo componente. La cabeza del inyector se ha simplificado y reducido a lo que es literalmente un diseño todo en uno (AiO).

"En el programa Ariane, estamos combinando nuestra fuerza innovadora con la experiencia de EOS. Juntos trabajamos en la fabricación aditiva de un cabezal inyector para un motor de cohete. Los resultados son impresionantes: Reducción significativa del tiempo de producción y reducción de los costes en un 50 %."
Dr.-Ing. Steffen Beyer | Jefe de Tecnología de Producción, Materiales y Procesos | ArianeGroup
Desafío
Fabricación de un cabezal de inyección para motores cohete con el menor número posible de componentes y menores costes unitarios.
La Agencia Espacial Europea (ESA) desea asumir una posición fuerte e independiente en el transporte espacial utilizando una tecnología eficiente de vehículos de lanzamiento. Para lograrlo, ArianeGroup, una empresa conjunta de la compañía aeroespacial europea Airbus Group y el grupo francés Safran, recibió el encargo de construir la próxima generación. Ariane es una serie de lanzadores europeos diseñados para poner en órbita alrededor de la Tierra cargas pesadas, como satélites de comunicaciones.
En un módulo de propulsión se desarrollan enormes fuerzas en condiciones extremas. Esto exige niveles máximos de fiabilidad y precisión en un espacio reducido. El cabezal de inyección es uno de los elementos centrales del módulo de propulsión, ya que alimenta la mezcla de combustible a la cámara de combustión.
Su diseño tradicional consta de 248 componentes, producidos y ensamblados en varias fases de fabricación. Los distintos pasos de procesamiento, como fundición, soldadura fuerte, soldadura y perforación, pueden dar lugar a puntos débiles que pueden constituir un riesgo bajo cargas extremas. Además, se trata de un proceso largo y complejo. En el campo de los elementos inyectores, la producción convencional requiere taladrar más de 8.000 orificios transversales en manguitos de cobre que luego se atornillan con precisión a los 122 elementos inyectores para mezclar con oxígeno el hidrógeno que fluye a través de ellos.
Un vistazo a estas cifras muestra claramente que, un componente funcionalmente integrado que combine todos los elementos debe ser el objetivo obvio pero ambicioso. Esto también podría liberar un importante potencial económico y reducir el número de pasos de procesamiento, así como el tiempo de producción, especialmente para un componente de clase 1.
Solución
Producto de fabricación aditiva que consta de un único elemento en lugar de 248 piezas individuales gracias a la integración funcional.
La solución a estos retos la aporta la fabricación aditiva. "La fabricación del cabezal inyector en una sola pieza es posible gracias a la tecnología EOS", afirma el Dr.-Ing. Steffen Beyer, responsable de Tecnología de Producción - Materiales y Procesos de ArianeGroup, explicando por qué se optó por la impresión industrial en 3D. "Solo la fabricación aditiva puede combinar funcionalidad integrada, construcción ligera, un diseño más sencillo y plazos de entrega más cortos en un solo componente". El equipo del proyecto volvió a elegir como material una aleación a base de níquel resistente al calor y a la corrosión (IN718). Este material proporciona una excelente resistencia a la tracción, resistencia, fluencia y fractura a altas temperaturas y también se utilizará con la nueva tecnología de producción.
"Tras desarrollar con éxito el componente, centramos nuestra atención en la eficiencia de costes", informa el Dr. Fabian Riss, Tecnología de Producción - Materiales y Procesos. El requisito clave de ArianeGroup era reducir los plazos de entrega y los costes unitarios. La fabricación se realizó inicialmente mediante un proceso incremental con el EOS M 290. Tras el éxito de las pruebas piloto, la producción se amplió al sistema EOS M 400-4 de mayor tamaño. La tecnología láser 4 permitió fabricar el componente del módulo de propulsión hasta cuatro veces más rápido. "El escalado del proceso de construcción al sistema de alta productividad EOS M 400-4 fue un paso importante para nosotros con el fin de avanzar en la industrialización y competitividad del proyecto Ariane. La colaboración se desarrolló de forma muy eficiente gracias a la experiencia y los conocimientos industriales del personal de EOS. Los resultados hablan por sí solos y son prueba del gran rendimiento del equipo", añade el Dr. Steffen Beyer.
Resultados
Los resultados del nuevo cabezal inyector producido mediante fabricación aditiva son extremadamente impresionantes: en lugar de 248 piezas, consta de una sola, con la misma funcionalidad y reduciendo al mínimo el tiempo necesario.
La tecnología de impresión 3D industrial basada en lecho de polvo de EOS permitió, por ejemplo, imprimir las 122 boquillas de inyección, las placas base y frontal y la cúpula de distribución con los correspondientes conductos de alimentación para los combustibles hidrógeno y oxígeno como un componente integrado. En comparación con los sistemas de un solo láser, la productividad significativamente mayor del sistema multiláser EOS M 400-4 permitió reducir el tiempo de construcción en un factor de 3 y los costes en un 50 % en el ejemplo del cabezal inyector AiO.
El equipo del proyecto pudo cosechar toda una serie de éxitos adicionales. La simplificación del diseño y la mejora de las propiedades de los materiales en comparación con la calidad de las piezas de fundición permitieron a la tecnología aditiva reducir considerablemente el grosor de las paredes sin perder resistencia.
Una reducción significativa del peso también implica una mayor reducción del tiempo de construcción y, por supuesto, de los costes.
Por último, pero no por ello menos importante, los procesos de fabricación aditiva permiten acelerar considerablemente los ciclos de innovación. Las mejoras estructurales, las modificaciones de diseño y la fabricación de componentes de prueba en la fase de desarrollo pueden ponerse directamente en producción a partir de datos CAD sin que los ingenieros tengan que dedicar tiempo a preparar herramientas, como ocurre con las piezas de fundición. De este modo, la impresión 3D industrial da un salto cualitativo en términos de plazos de entrega. Mientras que cada iteración solía requerir alrededor de medio año, ahora sólo se tarda unos días. Además, toda la cadena de fabricación se desarrolla ahora internamente en las instalaciones de ArianeGroup. En pocas palabras: Misión cumplida.
Ventajas
- -131 Días Iteración
- -247 Integración funcional de piezas únicas
- -50% de reducción de costes
Historias de innovación de EOS
Explore tres décadas de excelencia pionera en impresión 3D con EOS