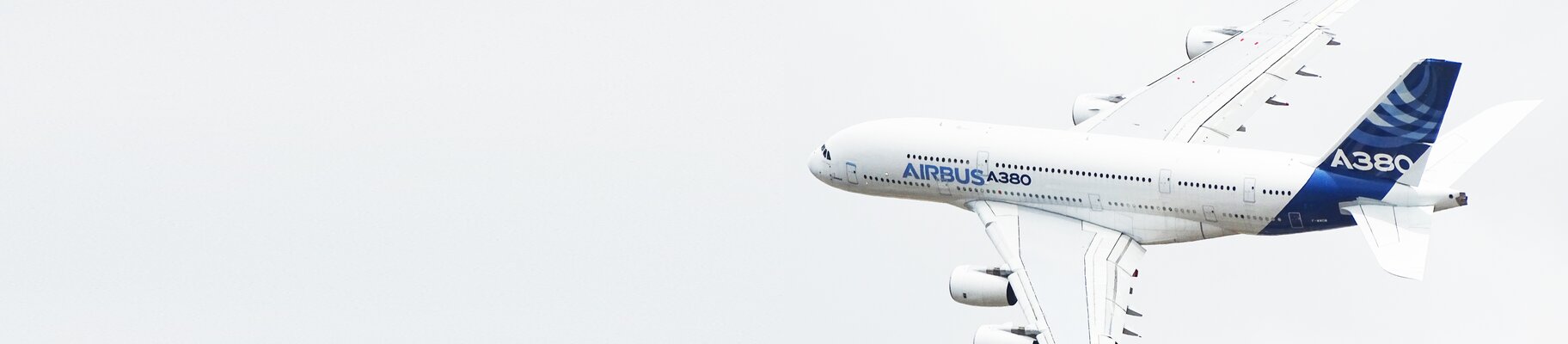
Liebherr | Primer componente hidráulico de control de vuelo primario de metal impreso en 3D
Vuela en un Airbus A380 | Historia de éxito
"Dentro de un par de años, creemos que las piezas metálicas impresas en 3D, como el bloque de válvulas, se fabricarán en serie en Lieberr- Aerospace y se entregarán a nuestros clientes. El bloque de válvulas impreso en 3D ha demostrado que la fabricación aditiva con tecnología EOS es factible para construir componentes de vuelo primarios críticos."
Alexander Altmann | Ingeniero jefe de fabricación aditiva, investigación y tecnología | Liebherr-Aerospace Lindenberg GmbH
Desafío
Sustituir un componente hidráulico de control de vuelo primario convencional por una pieza de fabricación aditiva, cumpliendo todos los requisitos de certificación para el vuelo.
En un contexto de creciente concienciación ecológica, aumento de los precios del combustible y falta de fuentes de energía alternativas, la industria aeroespacial necesita encontrar nuevas tecnologías para seguir siendo competitiva. La impresión 3D industrial basada en lecho de polvo tiene el potencial de provocar un cambio fundamental y facilitar componentes innovadores. Liebherr lanzó su programa de fabricación aditiva hace ya seis años. Ahora han demostrado que la tecnología de impresión 3D de metales EOS es aplicable a los colectores hidráulicos de los aviones. Junto con Airbus y un equipo de investigación de la Universidad Técnica de Chemnitz, Liebherr inició un proyecto financiado por el Ministerio Federal de Economía y Energía (BMWi).
El objetivo era sustituir un componente de vuelo primario convencional, un bloque de válvulas hidráulicas de alta presión, por otro de fabricación aditiva.
A bordo de un avión, muchos componentes trabajan juntos para garantizar un vuelo seguro. Un actuador de alerón mueve el alerón a la posición deseada para disminuir la sustentación del avión. Este tipo de componentes primarios de control de vuelo exigen los más altos niveles de calidad y precisión durante la producción. Convencionalmente, la fabricación de bloques de válvulas parte de materia prima forjada, que luego se mecaniza, recorta, taladra y finalmente se ensambla. Esta cadena de procesos es larga y compleja, lo que deja poco margen para la optimización. Sin embargo, el mero número de pasos del proceso ilustra el margen para las posibles mejoras que puede lograr la impresión 3D sobre metal. Está claro que la sustitución por sí sola no basta; la nueva pieza debe ser más ligera, eficiente en el uso de los recursos y respetuosa con el medio ambiente para demostrar la viabilidad de la fabricación aditiva como prometedora tecnología del futuro.
Solución
Fabricación de un componente ligero impreso en 3D con menos piezas y una cadena de procesos eficiente
La solución consistió en desarrollar una cadena de diseño y procesos para su aplicación en la industria aeronáutica utilizando la tecnología de impresión 3D industrial de EOS, fiable y de alta calidad. En primer lugar, se analizó la pieza convencional. Se identificaron las estructuras hidráulicas y se eliminaron las secciones auxiliares. Se reconsideró el posicionamiento de los componentes principales a la luz de sus requisitos de espacio de instalación e interfaz con el objetivo de optimizar las líneas de conexión inteligentes y cortas. Esto sentó las bases para el diseño de la nueva pieza. "Con la impresión industrial en 3D, la complejidad deja de ser un problema. En el sistemaEOS M 290 , los componentes se construyen a partir de un gran número de capas finas, cada una de 30 a 60 μm de grosor, lo que nos permite construir geometrías complejas", explica Alexander Altmann, Ingeniero Jefe de Fabricación Aditiva, Investigación y Tecnología en Liebherr-Aerospace Lindenberg GmbH. "Los elementos funcionales se conectaron directamente entre sí mediante tubos curvados. Esto evita la necesidad de un complejo sistema de tubos con muchos orificios transversales, lo que ahorra tiempo en la producción."
El material elegido, una aleación de titanio, es especialmente adecuado para la aviación, ya que ofrece toda una serie de ventajas. Permite ahorrar peso y reducir costes durante el funcionamiento, ya que es muy ligero y mecánicamente estable y tiene muy buena resistencia a la corrosión. Entre los pasos de postprocesado se incluyen, por ejemplo, el tratamiento térmico para aliviar tensiones, así como un tratamiento especial para los canales hidráulicos.
Por último, "no debe existir ni la más mínima duda sobre la fiabilidad y seguridad de los componentes y el material con el que están fabricados. Con la tecnología EOS, podemos fabricar de forma fiable componentes de titanio de la máxima calidad, lo que es un requisito previo para el siguiente paso de la producción en serie", explica Alexander Altmann.
Bloque de válvulas fabricado aditivamente por Liebherr | Construido en un EOS M 290: Mismo rendimiento, 35% menos de peso
Resultados
El nuevo bloque de válvulas de fabricación aditiva ofrece las mismas prestaciones que el convencional, pero es un 35 % más ligero y está fabricado con menos piezas. Fue posible integrar 10 elementos funcionales en el nuevo bloque de válvulas, eliminando el complejo sistema de tuberías con multitud de orificios transversales.
"Este podría ser el eslogan de la fabricación aditiva: fabricar lo mismo pero con menos masa y menos piezas. Sin embargo, para Liebherr-Aerospace se trata de un paso importante", afirma Altmann. La nueva pieza impresa en 3D ya ha sido probada con éxito en un vuelo de prueba del avión A380.
La impresión industrial en 3D es menos compleja y extremadamente eficiente en cuanto al material en comparación con el proceso de fresado tradicional, y ayuda a reducir al mínimo los residuos de titanio. "Hoy en día, se tarda aproximadamente un día en fabricar un bloque de válvulas y vemos el potencial de reducir el tiempo de construcción en más de un 75 % con la EOS M 400-4", afirma Alexander Altmann.
Pero eso no es todo: el bloque de válvulas ligero impreso en 3D y las futuras piezas impresas en 3D también contribuirán a reducir el consumo de combustible y las emisiones de CO2 y NOX. Las exigencias que se plantean a los componentes aeronáuticos son extremadamente altas, por lo que Liebherr se centra firmemente en comprender los métodos de fabricación aditiva hasta el último detalle para establecer procesos de producción que sean absolutamente fiables. Con EOS, Liebherr dispone de un proveedor tecnológico y socio que facilita el aseguramiento de la calidad durante el proceso de fabricación aditiva. Al participar en una fase piloto, Liebherr pudo contribuir al desarrollo de EOSTATE Exposure OT , un nuevo módulo de la suite de monitorización EOS que permite la inspección de componentes sin fisuras y en tiempo real.
"En el futuro, esto acelerará la identificación de defectos de material durante el proceso de impresión 3D industrial y ayudará a reducir la necesidad de procesos posteriores de garantía de calidad, como la tomografía por ordenador", afirma Alexander Altmann.
Resumen de los resultados
- -75% Tiempo de producción
- -35% Reducción de peso
- -10 Piezas únicas Integración funcional
Historias de innovación de EOS
Explore tres décadas de excelencia pionera en impresión 3D con EOS