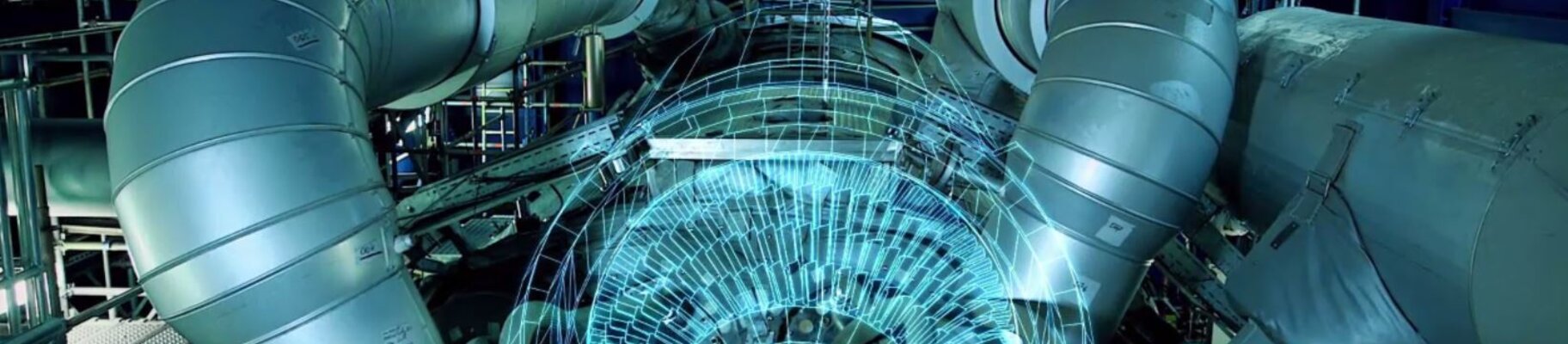
Impresión 3D para turbinas de gas industriales de alto rendimiento
Siemens | Estudio de caso
Siemens ENERGY, empresa con sede en Suecia, fabrica turbinas de gas para la generación de energía en aplicaciones industriales y de petróleo y gas. La gama de prestaciones de estas turbinas industriales de Siemens oscila entre 15 y 60 MW. Además de la construcción, la filial de Siemens también proporciona servicio y mantenimiento a largo plazo para estas obras maestras de la ingeniería. En un esfuerzo por ayudar a reducir los costes de mantenimiento, Siemens trabaja en el desarrollo y la implantación de la tecnología de fabricación aditiva, utilizando tecnología y equipos EOS.
"La fabricación aditiva nos abre nuevas dimensiones en el uso del diseño y la producción integrados. Esta tecnología nos permite fabricar y reparar componentes para nuestras turbinas de gas industriales mucho más rápido que antes. Al mismo tiempo, aumenta la funcionalidad y el rendimiento de la pieza".
Dr. Vladimir Navrotsky | Director de Tecnología e Innovación, Siemens Energy Service | Petróleo y Gas y Aplicaciones Industriales
Desafío
La turbina de gas consta de una entrada de aire, un compresor, una cámara de combustión, una turbina y una salida de gas caliente. El aire que pasa por el motor es comprimido por el compresor. En la cámara de combustión, el aire comprimido se mezcla con combustible y se quema para aumentar la energía cinética del flujo. En la turbina, la energía cinética del flujo se convierte en energía mecánica. Esta energía mecánica se utiliza para hacer girar el compresor y el generador de la turbina de gas (para generar electricidad) u otros equipos accionados (por ejemplo, el compresor para bombear el gas/petróleo a través de las tuberías). Durante el funcionamiento, los componentes del recorrido del gas caliente del motor están expuestos a altas temperaturas, a veces superiores a 1.000°C (por ejemplo, álabes y paletas). Esto, a su vez, provoca un alto nivel de desgaste de los componentes del recorrido de los gases calientes.
Lo mismo ocurre con la punta del quemador, el punto en el que se produce la ignición de la mezcla de combustible y aire. Aquí, los efectos del desgaste pueden verse y medirse claramente. El fabricante llevó a cabo pruebas rigurosas para establecer un periodo de funcionamiento prescrito tras el cual los quemadores normalmente necesitan ser reparados.
El procedimiento de reparación convencional requería la prefabricación de grandes secciones de la punta del quemador.
Esta unidad prefabricada se utiliza para sustituir la punta del quemador una vez transcurrido el tiempo de funcionamiento especificado (cortar la antigua y soldar la prefabricada). El procedimiento de reparación convencional puede llevar mucho tiempo e implicar un número significativo de subprocesos y exámenes. Para ayudar a simplificar y acelerar el procedimiento de reparación, Siemens implantó la tecnología de fabricación aditiva.

Solución
Emprender una operación de este tipo requiere un socio innovador. Siemens encontró precisamente eso en EOS: además de disponer de la tecnología de fabricación aditiva adecuada, EOS también fue capaz, en un breve plazo de tiempo, de adaptar individualmente una de sus máquinas internas -una EOSINT M 280- para el procesamiento de metales.

Las modificaciones afectaron, en particular, a la escala del interior de la máquina, que tuvo que ampliarse para dar cabida al quemador de 800 mm. El fabricante también modificó otros componentes de hardware, como un sistema de cámaras y un sistema óptico de medición, e introdujo los correspondientes ajustes en el software. EOS llevó a cabo la extensa remodelación del sistema EOSINT en menos de un año.
Desde el principio quedó claro que el planteamiento estaba dando sus frutos. En lugar de sustituir gran parte de la punta del quemador, Siemens empezó retirando únicamente el material dañado. Además, durante la reparación, las versiones anteriores de los quemadores de la flota pudieron reconstruirse con el diseño más reciente. Esto significaba que las versiones anteriores de los quemadores de la flota no sólo podían repararse, sino también mejorarse, lo que daba un nuevo significado al término "fabricación aditiva".
Resultados
Las cifras, los datos y los hechos detallan claramente el éxito del nuevo proceso de reparación. Siemens ENERGY podrá influir significativamente en la preocupación central: la reducción del plazo de reparación: para el operador es igualmente importante que las turbinas estén rápidamente listas para volver al servicio. Esto también abre oportunidades adicionales para posibles reducciones de costes en relación con el proceso de reparación, así como con el mantenimiento.
Además de mejorar su propio proceso de reparación, Siemens puede ofrecer ahora a sus clientes ventajas estratégicas: Gracias a este nuevo proceso, los expertos pueden introducir mejoras en la tecnología de las turbinas integrando los componentes en el proceso de reparación. De este modo, los operadores pueden hacer uso de la última tecnología, aunque sus turbinas lleven años en servicio.
El Dr. Vladimir Navrotsky, Director de Tecnología e Innovación de Siemens Energy Service, Oil & Gas and Industrial Applications, resume: "Con esta nueva tecnología de reparación pretendemos realizar estos trabajos de alta precisión mucho más rápidamente".
No sólo la filial sueca de Siemens considera el proyecto un logro significativo. "Hemos impulsado con éxito nuestra tecnología en el ámbito de la reparación. Hemos demostrado que somos capaces de modificar nuestro sistema rápidamente para satisfacer los requisitos específicos del cliente. En este caso, las modificaciones tanto del hardware como del software han sido significativas. Todos los implicados pueden mirar atrás con satisfacción, no sólo por el resultado final, sino también por el camino recorrido para conseguirlo", afirma Stefan Oswald, de EOS.

Resumen de los resultados
- Innovador: las versiones antiguas de los quemadores pueden adaptarse rápidamente a los últimos estándares tecnológicos.
- Rentabilidad: ya se han observado posibles reducciones de costes en una fase temprana.
- -90 % de reducción del tiempo necesario para el proceso de reparación
Casos prácticos de EOS
Explore tres décadas de excelencia pionera en impresión 3D con EOS