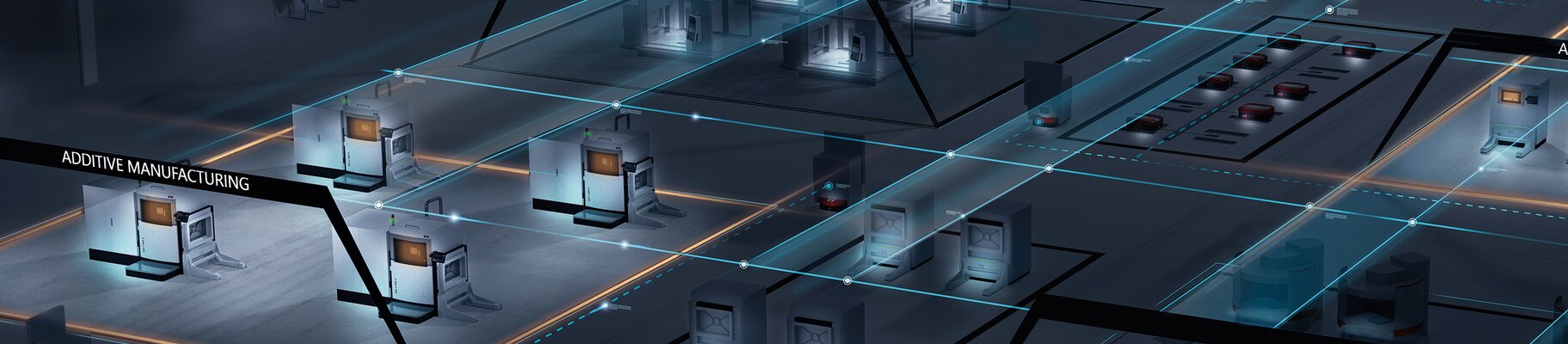
扩大增材制造 生产规模
2021 年 8 月 23 日 | 阅读时间:9 分钟
如何以最小的代价提高和优化工业 3D 打印工厂的生产率?我们使用仿真软件来模拟增材制造 流程和后处理步骤。我们的客户使用案例让缩放过程变得简单易懂。
如何获得最高的投资回报?
扩大增材制造 (AM) 生产规模是一项艰巨的任务,因为在决定扩大战略之前必须考虑多种因素。
本文针对那些希望以最小的代价提高和优化其 AM 工厂生产率的人。我们将介绍一个实际的客户使用案例,使扩展过程变得简单易行。
主要挑战
客户希望在现有两台 EEOS P 396 机器的基础上增加三台 EOS P396 系统,从而提高产量。但是,团队不确定现有的后处理设备是否能在一个工人轮班的情况下处理最高的吞吐量。AM 产品保持不变,这意味着工作流程和设备类型也保持不变。主要的挑战是如何优化额外的后处理设备和资源,以获得最高的吞吐量,同时尽可能降低每个零件的成本。
我们为客户开发了一个定制的生产模型,其中包含合适的可变输入参数。通过改变这些输入参数,可以生成不同的方案,以检查每个零件的产量和成本的敏感性。这些信息可指导客户决定优化方案,以最低的额外投资来扩大 AM 生产规模。
总之,我们找出了工厂的瓶颈。通过对后处理进行微小的改动,我们将产量提高了 24%,利润率提高了 124%,投资回报率提高了 115%,每个零件的成本降低了 18%。
利用仿真技术解决生产优化问题
批量生产的成功商业案例需要对影响产量和成本的所有生产参数进行深入分析。这些生产参数通常以非线性方式相互关联,因此很难通过 Excel 电子表格对其进行优化。而模拟软件则能考虑到所有与生产相关的复杂因素,更直接地解决优化问题。
我们 EOS 使用西门子公司的 Tecnomatix 工厂仿真技术,并提供服务帮助客户仿真定制的解决方案,以充分了解工艺流程,从而决定是否购买。
我们正在使用仿真软件模拟 AM 工艺和后处理步骤。成功的 AM 企业需要分析后处理的吞吐量和成本,这有时会决定一个商业案例的成败。仿真使我们更容易仔细检查复杂的工艺链。
工厂模拟是一种离散事件模拟,可检查所有计划事件。例如,如果一项工作的处理时间为 1 小时,模拟器将考虑工作的开始时间和结束时间。它不会模拟工作是如何处理的,而是事件发生的时间。其他计划事件包括工人的轮班时间、设置时间、机器维护时间等。
案例研究简介
工厂模拟是一种离散事件模拟,可检查所有计划事件。例如,如果一项工作的处理时间为 1 小时,模拟器将考虑工作的开始时间和结束时间。它不会模拟工作是如何处理的,而是事件发生的时间。其他计划事件包括工人的轮班时间、设置时间、机器维护时间等。
拆包站 | x1 |
粉末管理系统 | x1 |
DyeMansion Powershot C | x1 |
DyeMansion Powershot S | x1 |
DyeMansion DM60 | x2 |
紫外线处理 | x1 |
表面处理 | x2 |
干燥区 | x1 |
检查表 | x1 |
随着EOS P 396 ,客户可以打印包含 144 个零件的作业。两EOS P 396 每年可生产 426 个作业或 61.344 个零件。客户每年需要额外生产 600 个作业或 66,400 个零件。第一次计算显示,另外三个EOS P 396 达到目标需要 1000 万台设备,这意味着公司需要投入大量资金。因此,生产模拟的目标是确定是否可以使用相同数量的后处理设备实现产量,并考虑所有生产复杂性,如故障、维护和工人轮班模型。
我们是如何进行的:
整个布局分为 3 个区域(见图 1):
- AM 打印机
- 粉末管理
- 后期处理
客户希望有三个区域,以尽量减少粉末交叉污染的风险。我们首先建立了一个模拟模型,其中有两个现有的EOS P 396 然后是第二个模型,其中有三个EOS P 396 连同上面列出的设备。客户从周一到周五采用单班制。在分析过程中,我们仔细调整了生产设施的各种变量,例如消耗品和操作员。
离散事件模拟可以模拟特定时间点发生的所有事件。它只考虑开始时间和结束时间,而不会考虑中间发生的事情。
例如,假设您在 17:50 进入自动取款机,并在 17:53 离开自动取款机。模拟在 17:50 显示事件的开始时间,然后跳转到 17:53 显示事件的结束时间。在工厂模拟中,时钟会从一个预定事件跳转到下一个事件。
在制造过程中,它是进入机器进行加工并在加工完成后退出的部件。零件加工过程中可能会涉及各种步骤(设置时间、装载时间、卸载时间),这些都可以包含在模拟中。模拟研究有助于提高机器的吞吐量和利用率。它还可以帮助确定工人数量、设备、机器和仓库大小,以获得最佳的商业案例。
模拟分析与结果
优化 AM 和粉末管理区
在包括后处理设备之前,我们首先模拟了 AM 区域和粉末管理区域。转变模型与原来的模型相比没有变化,如下所示:
- 班次:1 班(8 小时),周一至周五
- 构建时间:20 小时。
模型建立后,第一个挑战是确定这两项活动的最佳工人数量。如表 1 所示,我们进行了五次实验(Exp.)无论是 1 个还是 5 个操作员,吞吐量都是一样的(每年 1.065 个工作)。
操作员人数 | 创造的就业机会 |
---|---|
Exp 1 1 | 1065 |
Exp 2 2 | 1065 |
Exp 3 3 | 1065 |
Exp 4 4 | 1065 |
Exp 5 5 | 1065 |
表 1:AM 和粉末管理区的经营者数量和各自的年产量
接下来,我们重点优化了粉末运输箱(EOS 多箱,见图 1)的数量,使工人能够将粉末分配到 EOS 机器上。经过 10 次反复试验,我们确定 7 个 EOS 多箱是实现每年 1062 个作业吞吐量的最佳数量(见表 2)。超过 7 台多箱机所增加的产量并不能证明所增加的成本是合理的。每年只增加 3 个工作岗位(从 1062 个增加到 1065 个),而增加的成本(本报告中未显示)并不能证明这种微小的产量增加是合理的。
多箱数量 | 创造的就业机会 |
---|---|
Exp 01 1 | 184 |
Exp 02 2 | 367 |
Exp 03 3 | 551 |
Exp 04 4 | 732 |
Exp 05 5 | 911 |
Exp 06 6 | 983 |
Exp 07 7 | 1062 |
Exp 08 8 | 1064 |
Exp 09 9 | 1064 |
Exp 10 10 | 1065 |
表 2:多箱数量及相应工作
优化后处理区域:
在优化 AM 和粉末管理区之后,后加工区是下一个具有挑战性的任务。它涉及七个不同的加工站,共有十个步骤:
- DyeMansion* 中的部件清洁 Powershot C
- 超声波清洗
- 表面处理
- 超声波清洗
- 干燥
- DyeMansion* 中的表面处理 Powershot S
- 紫外线处理
- 在 DyeMansion DM60 中着色
- DyeMansion* 中的表面处理 Powershot S
- 紫外线处理
(染坊是 EOS 生态系统的一部分)
此外,客户的工作流程也面临一些挑战。例如,我们的合作伙伴 DyeMansion 提供的喷砂站(Powershot S 和 C)只能处理一次生产中一半的零件(144 个零件中的 72 个),换句话说,每次生产只能处理两个批次。但是,对于所有其他工位,如 DyeMansion DM60 着色系统、表面处理、烘干等,则需要处理所有工作,换句话说,每次生产只需处理一个批次。
一旦原始模型扩展到包括后处理区域,我们就会集中精力寻找最佳操作员人数。从每年 1062 个工作岗位的调幅最佳值开始,我们运行了 5 个不同的设置,其中有 1-5 个操作员。如表 3 所示,后处理区需要 4 名操作员,其吞吐量才能大大高于之前的工人数量。增加 4 个工作岗位并不能证明增加一名操作员(848 个工作岗位对 849 个工作岗位)所需的额外成本(此处未显示)是合理的。
操作员人数 | 通过 AM 创造就业机会 | 通过 AM + 生产的工作 后处理 |
---|---|---|
Exp 1 1 | 1062 | 228 |
Exp 2 2 | 1062 | 666 |
Exp 3 3 | 1062 | 787 |
Exp 4 4 | 1062 | 848 |
Exp 5 5 | 1062 | 849 |
表 3:后处理区操作员人数及各自的工作岗位
结论
这里的关键信息是,调整和优化 AM 生产战略是一项复杂的任务。这是一项独特的挑战,需要针对特定的布局,每种方案都有不同的关键参数。如果不分析和考虑您的策略,可能会得出错误的结论。凭借我们的仿真专业技术和 30 年的 AM 经验,我们可以为您制定成功的扩展战略,以实现最高的设备利用率和最低的单件成本。