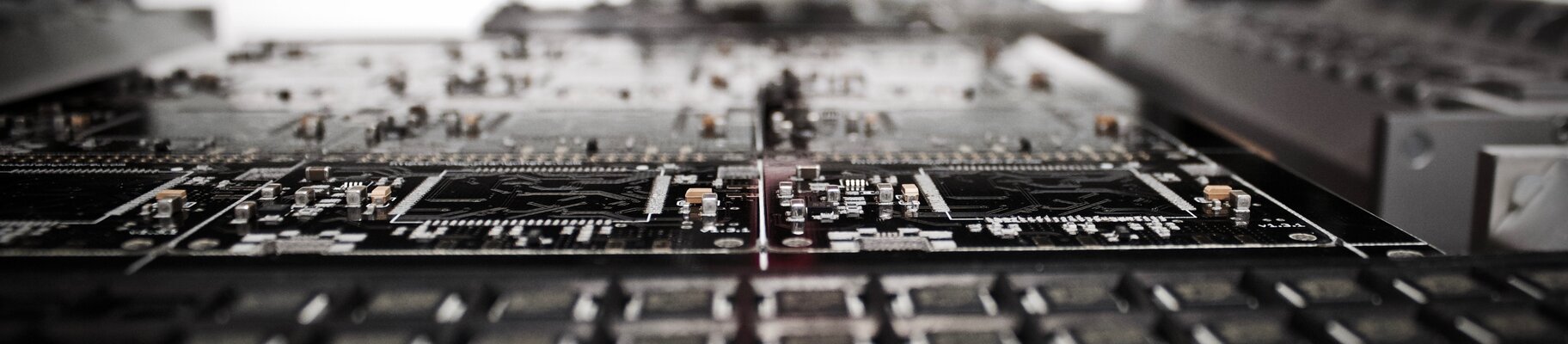
Portacircuiti multidimensionali grazie alla fabbricazione additiva
Beta LAYOUT | Studio di caso
Prototipi di nuovi circuiti stampati (PCB) creati con la tecnologia EOS
All'inizio del 2016, molti scrivevano della fine della Legge di Moore, anticipando che le prestazioni dei chip per computer non sarebbero più raddoppiate ogni due anni. Il motivo è che le strutture dei processori stessi sono già a pochi nanometri dal possibile. Ulteriori riduzioni sono quasi impossibili dal punto di vista tecnico. Per continuare a migliorare le prestazioni, i produttori stanno lavorando sull'architettura che sovrappone più strati strutturali. Un approccio simile è già stato adottato nel campo dei supporti per circuiti. L'azienda tedesca Beta LAYOUT GmbH ha sfruttato con successo la tecnologia EOS per produrre e testare i prototipi di questi innovativi supporti.
"Grazie ai suoi numerosi vantaggi, la tecnologia di produzione additiva offre un elevato valore aggiunto per un'ampia gamma di operatori di mercato. La ricerca e lo sviluppo traggono profitto dai nostri servizi, il che, a sua volta, ha un impatto positivo sul nostro modello di business. Questo ci permette di offrire i vantaggi di una tecnologia avanzata a un gran numero di utenti".
Manuel Martin | Responsabile del prodotto 3D-MID | Beta LAYOUT GmbH
Sfida
Produzione di prototipi individuali per i portatori di circuito
I supporti per circuiti e i circuiti stampati tradizionali sono sempre stati un po' messi in ombra dai microprocessori che vi operano. Questo è un po' ingiusto perché, ovviamente, avere il miglior cervello è poco utile senza i benefici di un sistema nervoso centrale ad alte prestazioni. La storia è simile nel settore della microelettronica: quasi tutti i dispositivi contemporanei richiedono un circuito stampato per incorporare uno o più chip, oltre ai componenti elettrici necessari. In questo modo si crea una rete che svolge una serie di compiti, dalla fornitura di elettricità, alla circuiteria, fino all'emissione di segnali.
Nei nuovi dispositivi, lo spazio disponibile per l'installazione delle schede elettroniche convenzionali è spesso molto ridotto. Uno dei motivi è che molte apparecchiature elettroniche stanno diventando sempre più piccole e, anche quando la forma stessa è più grande, tende a rimanere poco spazio per l'elettronica vera e propria. Il volume esistente è necessario per alloggiare, ad esempio, schermi, un numero sempre maggiore di interfacce e punti di uscita, nonché batterie più grandi. I tempi in cui un semplice PCB da laboratorio era sufficiente per la costruzione sperimentale di nuovi circuiti sono ormai lontani, nella maggior parte dei casi e dei settori. Oltre allo spazio disponibile per l'installazione, il peso è un fattore chiave: anche le schede di circuito compatte e tridimensionali hanno un ruolo importante.
Nei prodotti elettronici contemporanei, i circuiti devono spesso competere per lo spazio limitato all'interno dell'alloggiamento. Se impilati in modo convenzionale, i circuiti stampati non sono più in grado di ospitare tutti i componenti necessari, per cui i già citati supporti per circuiti tridimensionali diventano la soluzione preferita. Anche in questo caso, i cicli di vita sempre più brevi di molti dispositivi pongono ulteriori sfide: lo stampaggio a iniezione è troppo costoso per produrre prototipi. Per questo motivo, Beta LAYOUT GmbH ha deciso di cercare un'alternativa più economica e performante.
Soluzione
Non esiste tecnologia più adatta alle esigenze dell'architettura multistrato della produzione additiva. Perché utilizza un laser per costruire un componente, strato per strato. Per questo Beta LAYOUT si affida a questa tecnologia e utilizza parti in plastica prodotte con la stampa 3D. L'innovazione avviene dopo il processo di stampa vero e proprio: una volta realizzati, i modelli vengono rivestiti con una speciale finitura fornita da un additivo. La successiva cosiddetta "strutturazione diretta al laser" (LDS) genera dei layout, che possono essere trasformati in tracce conduttrici attivando la finitura.
Il laser innesca una reazione fisico-chimica che crea spore metalliche e contemporaneamente irruvidisce la superficie. Dopo la strutturazione diretta con il laser, i modelli vengono posti in un bagno di rame privo di corrente elettrica. Le particelle di rame vengono depositate sulle aree precedentemente attivate per creare tracce conduttrici. Dopo il rivestimento in rame, le tracce conduttrici possono essere sottoposte a un'ulteriore ramatura attraverso la galvanizzazione, oppure essere dotate direttamente di una finitura superficiale. Successivamente, Beta LAYOUT aggiunge i singoli componenti all'unità nel reparto di assemblaggio interno dell'azienda. I pezzi finiti servono come prototipi e modelli iniziali, consentendo di testare il funzionamento e di verificare il layout del progetto.
"Offriamo la produzione di 3D-MID (dispositivi integrati meccatronici) come prototipi per diverse aziende", spiega Manuel Martin, Product Manager 3D-MID di Beta LAYOUT GmbH. "Lavorando con la FORMIGA P 110 di EOS, siamo in grado di fornire rapidamente prodotti di alta qualità ai nostri clienti. L'aspetto particolarmente pratico di tutto ciò è che siamo in grado di gestire anche gli ordini di modelli 3D tramite siti web e negozi online. La produzione additiva ci ha permesso di espandere con successo il nostro modello di business".

Risultati
Che si tratti di singoli sviluppatori o di grandi aziende affermate, la produzione additiva garantisce l'utilizzo di supporti per circuiti personalizzati per i prototipi di nuovi dispositivi elettronici. I componenti in plastica possono essere prodotti rapidamente e a un prezzo interessante. Il processo offre contemporaneamente il livello di precisione necessario e un'elevata qualità dei componenti, consentendo di produrre il corpo di base richiesto come se fosse già un prodotto quasi di serie - un aspetto da non sottovalutare, soprattutto per le serie di prova.
La tecnologia EOS offre inoltre un elevato grado di flessibilità: la macchina utilizzata è in grado di lavorare diversi materiali, tra cui, ad esempio, la PA 3200 GF riempita con perle di vetro o la poliammide riempita di alluminio. Alumide. Sono disponibili anche polimeri ad alte prestazioni come il PEEK e vari metalli. Il punto cruciale è che tutti i materiali sono in grado di resistere alle alte temperature, un limite del processo di stampaggio a iniezione nella produzione in serie.
Grazie a questa flessibilità, Beta LAYOUT è in grado di soddisfare le diverse esigenze individuali dei suoi clienti, ad esempio rispondendo alle caratteristiche particolari della destinazione d'uso del supporto del circuito. In questo modo, l'azienda è in grado di sviluppare soluzioni individuali e ottimizzate, sia in termini di costi inferiori, che di maggiore resistenza alla temperatura o di altri requisiti specifici.
Oltre a questi vantaggi, la produzione additiva offre anche un ulteriore bonus: "In definitiva, ciò che stiamo vivendo è una democratizzazione della tecnologia avanzata. Senza innovazioni come questa, non saremmo affatto in grado di offrire il 3D-MID come servizio", afferma Manuel Martin. "Ciò significherebbe che molte piccole aziende e case di sviluppo non avrebbero la possibilità di realizzare tali prototipi. Di conseguenza, il tanto chiacchierato potere innovativo e creativo delle piccole e medie imprese perderebbe slancio e il settore della ricerca e dello sviluppo sarebbe molto meno dinamico".
La produzione additiva è un catalizzatore per ulteriori innovazioni e, in questo modo, forse un punto di partenza per stabilire una nuova Legge di Moore.

I risultati in sintesi
- Semplice: l'accesso a tecnologie avanzate per la ricerca e lo sviluppo.
- Personalizzato: fornitore di servizi di prodotti su misura
- Economicità: la produzione senza utensili riduce i costi
Casi di studio EOS
Esplorate tre decenni di eccellenza pionieristica nella stampa 3D con EOS