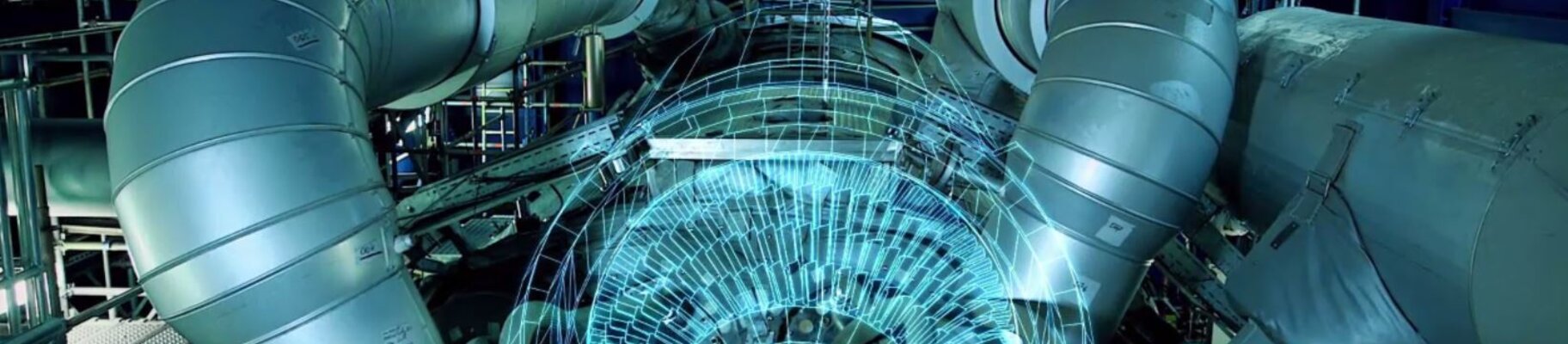
Stampa 3D per turbine a gas industriali ad alte prestazioni
Studio di caso Siemens
L'azienda svedese Siemens ENERGY produce turbine a gas per la generazione di energia in applicazioni industriali e nel settore oil & gas. Lo spettro di prestazioni di queste turbine industriali Siemens va da 15 a 60 MW. Oltre alla costruzione, la filiale Siemens fornisce anche assistenza e manutenzione a lungo termine per questi capolavori di ingegneria. Nel tentativo di ridurre i costi di manutenzione, Siemens lavora allo sviluppo e all'implementazione della tecnologia di produzione additiva, utilizzando la tecnologia e le attrezzature EOS.
"L'Additive Manufacturing ci apre nuove dimensioni nell'uso della progettazione e della produzione integrata. Questa tecnologia ci permette di produrre e riparare i componenti delle nostre turbine a gas industriali molto più rapidamente di prima. Allo stesso tempo, la funzionalità e le prestazioni del pezzo sono aumentate".
Dr. Vladimir Navrotsky | Responsabile Tecnologia e Innovazione, Siemens Energy Service | Oil & Gas e Applicazioni Industriali
Sfida
La turbina a gas è composta da ingresso dell'aria, compressore, combustore, turbina e uscita del gas caldo. L'aria che attraversa il motore viene compressa dal compressore. Nella camera di combustione l'aria compressa viene miscelata con il combustibile e bruciata per aumentare l'energia cinetica del flusso. Nella turbina l'energia cinetica del flusso viene convertita in energia meccanica. Questa energia meccanica viene utilizzata per far girare il compressore e il generatore della turbina a gas (per generare elettricità) o altre apparecchiature azionate (ad esempio, il compressore per pompare il gas/olio attraverso le condutture). Durante il funzionamento, i componenti del percorso del gas caldo del motore sono esposti a temperature elevate, a volte superiori a 1.000°C (ad esempio, le pale e le alette). Questo, a sua volta, porta a un elevato livello di usura dei componenti del percorso dei gas caldi.
Questo vale anche per la punta del bruciatore, il punto in cui avviene l'accensione della miscela combustibile-aria. Qui gli effetti dell'usura sono chiaramente visibili e misurabili. Il produttore ha effettuato test rigorosi per stabilire un periodo di funzionamento prescritto dopo il quale i bruciatori devono essere riparati.
La procedura di riparazione convenzionale richiedeva la prefabbricazione di grandi sezioni della punta del bruciatore.
Questa unità prefabbricata viene utilizzata per la sostituzione della punta del bruciatore dopo il tempo di funzionamento specificato (taglio della punta vecchia e saldatura di quella prefabbricata). La procedura di riparazione convenzionale può richiedere molto tempo e comporta un numero significativo di sottoprocessi ed esami. Per semplificare e velocizzare la procedura di riparazione, la tecnologia Additive Manufacturing è stata implementata da Siemens.

Soluzione
Un'operazione di questo tipo richiede un partner innovativo. Siemens ha trovato proprio questo in EOS: oltre a disporre della giusta tecnologia di Additive Manufacturing, EOS è stata anche in grado, in tempi brevi, di adattare individualmente una delle sue macchine interne - una EOSINT M 280 - per la lavorazione del metallo.

Le modifiche hanno riguardato, in particolare, la scala dell'interno della macchina, che ha dovuto essere ingrandita per ospitare il bruciatore da 800 mm. Il produttore ha inoltre modificato altri componenti hardware, come il sistema di telecamere e il sistema di misurazione ottica, e ha apportato le corrispondenti modifiche al software. EOS ha realizzato l'ampia rielaborazione del sistema EOSINT in meno di un anno.
Fin dall'inizio è stato chiaro che l'approccio stava dando i suoi frutti. Invece di sostituire gran parte della punta del bruciatore, Siemens ha iniziato a rimuovere solo il materiale danneggiato. Inoltre, durante la riparazione, le versioni precedenti dei bruciatori della flotta potevano essere ricostruite secondo il design più recente. Ciò significava che le versioni più vecchie dei bruciatori della flotta potevano non solo essere riparate, ma anche migliorate, dando così un nuovo significato al termine "Additive Manufacturing".
Risultati
Cifre, dati e fatti illustrano chiaramente il successo del nuovo processo di riparazione. Siemens ENERGY sarà in grado di avere un impatto significativo sulla questione centrale, ovvero la riduzione dei tempi di riparazione: per l'operatore è altrettanto importante che le turbine siano rapidamente pronte a tornare in servizio. Questo apre anche ulteriori opportunità di potenziale riduzione dei costi per quanto riguarda il processo di riparazione e la manutenzione.
Oltre a migliorare il proprio processo di riparazione, Siemens può ora offrire ai propri clienti vantaggi strategici: Grazie a questo nuovo processo, gli esperti possono apportare miglioramenti alla tecnologia delle turbine integrando i componenti nel processo di riparazione. In questo modo, gli operatori possono avvalersi della tecnologia più recente, anche se le loro turbine sono in servizio da anni.
Il Dr. Vladimir Navrotsky, responsabile della tecnologia e dell'innovazione di Siemens Energy Service, Oil & Gas and Industrial Applications, riassume: "con questa nuova tecnologia di riparazione, vogliamo eseguire questi lavori di alta precisione in modo molto più rapido".
Non è solo la filiale svedese di Siemens a considerare il progetto come un risultato significativo. "Abbiamo spinto con successo la nostra tecnologia nell'arena delle riparazioni. Abbiamo dimostrato di essere in grado di modificare rapidamente il nostro sistema per soddisfare le esigenze specifiche dei clienti. In questo caso, le modifiche all'hardware e al software sono state significative. Tutte le persone coinvolte possono guardare con soddisfazione non solo al risultato finale, ma anche al percorso seguito per raggiungerlo", afferma Stefan Oswald di EOS.

I risultati in sintesi
- Innovativo: le vecchie versioni dei masterizzatori possono essere rapidamente adeguate agli standard tecnologici più recenti
- Efficace dal punto di vista dei costi: potenziali riduzioni dei costi già visibili in fase iniziale
- -90 % di riduzione del tempo necessario per il processo di riparazione
Casi di studio EOS
Esplorate tre decenni di eccellenza pionieristica nella stampa 3D con EOS