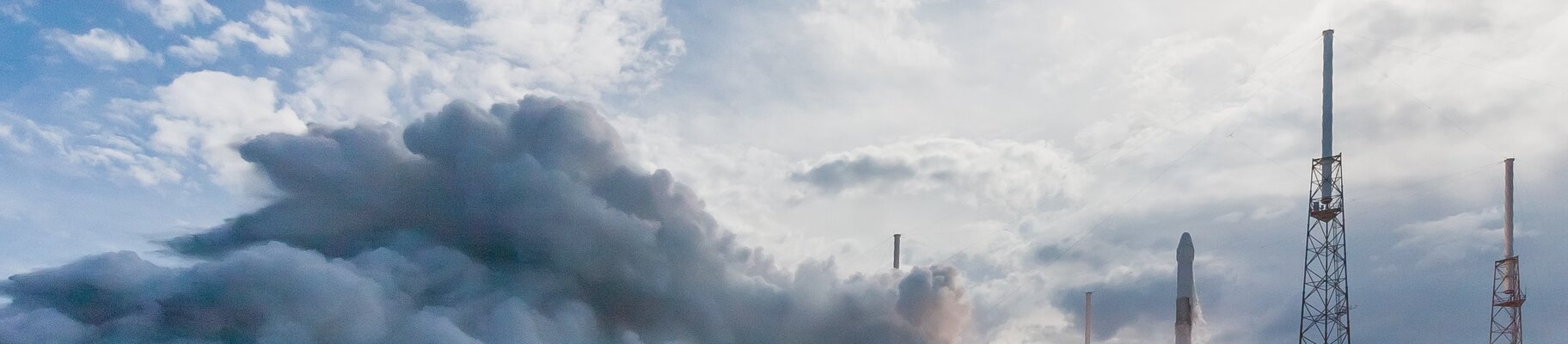
Il futuro modulo di propulsione di Ariane semplificato
ArianeGroup | Storia dell'innovazione
Design all-in-one - 122 ugelli di iniezione e altre parti come un unico componente integrato
Il termine "Mission Critical" descrive perfettamente i componenti di Classe 1 utilizzati nell'industria aerospaziale. Da questi componenti dipendono missioni che costano centinaia di milioni. Di conseguenza, gli ingegneri cercano costantemente di sviluppare componenti della massima qualità, funzionalità e robustezza, semplificando al contempo la catena di produzione e riducendo il numero di singoli elementi. Grazie alla tecnologia di produzione additiva EOS, ArianeGroup è riuscita a raggiungere un nuovo livello: Invece di 248 elementi, la testa dell'iniettore di un motore a razzo di un futuro modulo di propulsione dello stadio superiore conta ora un solo componente. La testa dell'iniettore è stata semplificata e ridotta a quello che è letteralmente un progetto all-in-one (AiO).

"Nel programma Ariane, stiamo combinando la nostra forza innovativa con l'esperienza di EOS. Insieme, lavoriamo alla produzione additiva di una testa di iniettore per un motore a razzo. I risultati sono impressionanti: Riduzione significativa dei tempi di produzione e costi inferiori del 50%".
Dr.-Ing. Steffen Beyer | Responsabile Tecnologia di Produzione, Materiali e Processi | ArianeGroup
Sfida
Produzione di una testa di iniezione per motori a razzo con il minor numero possibile di componenti e costi unitari inferiori
L'Agenzia Spaziale Europea (ESA) vuole assumere una posizione forte e indipendente nel trasporto spaziale utilizzando una tecnologia efficiente per i veicoli di lancio. Per raggiungere questo obiettivo, ArianeGroup, una joint venture tra l'azienda aerospaziale europea Airbus Group e il gruppo francese Safran, è stata incaricata di costruire la prossima generazione. Ariane è una serie di veicoli di lancio europei progettati per consentire la messa in orbita intorno alla Terra di carichi pesanti, come i satelliti per le comunicazioni.
In un modulo di propulsione si sviluppano forze enormi in condizioni estreme. Ciò richiede i massimi livelli di affidabilità e precisione in uno spazio ridotto. La testa di iniezione è uno degli elementi centrali del modulo di propulsione, che alimenta la miscela di carburante nella camera di combustione.
Il suo design tradizionale consiste in 248 componenti, prodotti e assemblati in varie fasi di lavorazione. Le diverse fasi di lavorazione, come la fusione, la brasatura, la saldatura e la foratura, possono generare punti deboli che possono costituire un rischio in caso di carichi estremi. Inoltre, si tratta di un processo lungo e complesso. Nel campo degli elementi iniettori, la produzione convenzionale richiede l'esecuzione di oltre 8.000 fori trasversali nei manicotti di rame che vengono poi avvitati con precisione ai 122 elementi iniettori per miscelare l'idrogeno che li attraversa con l'ossigeno.
Uno sguardo a queste cifre mostra chiaramente che un componente funzionalmente integrato che combina tutti gli elementi deve essere l'obiettivo ovvio ma ambizioso. Questo potrebbe anche liberare un significativo potenziale economico e ridurre il numero di fasi di lavorazione e i tempi di produzione, soprattutto per un componente di Classe 1.
Soluzione
Un prodotto fabbricato in modo additivo che comprende un singolo elemento invece di 248 parti individuali grazie all'integrazione funzionale.
La soluzione a queste sfide è fornita dalla produzione additiva. "La produzione della testa dell'iniettore in un unico pezzo è possibile grazie alla tecnologia EOS", afferma il Dr.-Ing. Steffen Beyer, Head of Production Technology - Materials & Processes di ArianeGroup, spiegando perché è stata scelta la stampa 3D industriale. "Solo la produzione additiva può combinare funzionalità integrate, costruzione leggera, un design più semplice e tempi di consegna più brevi in un singolo componente". Il team del progetto ha scelto ancora una volta come materiale una lega a base di nichel resistente al calore e alla corrosione (IN718). Questo materiale offre un'eccellente resistenza alla trazione, alla resistenza, allo scorrimento e alla frattura ad alte temperature e sarà utilizzato anche con la nuova tecnologia di produzione.
"Dopo aver sviluppato con successo il componente, abbiamo rivolto la nostra attenzione all'efficienza dei costi", riferisce il Dr. Fabian Riss, Production Technology - Materials & Processes. La richiesta principale di ArianeGroup era di ridurre i tempi di consegna e i costi unitari. Inizialmente la produzione era stata eseguita con un processo incrementale con il EOS M 290. Dopo il successo dei test pilota, la produzione è stata scalata al sistema più grande EOS M 400-4. La tecnologia 4-laser ha permesso di produrre il componente del modulo di propulsione a una velocità fino a quattro volte superiore. "Scalare il processo di costruzione al sistema EOS M 400-4 ad alta produttività è stato per noi un passo importante per far progredire l'industrializzazione e la competitività del progetto Ariane. La collaborazione si è svolta in modo molto efficiente grazie all'esperienza e alla competenza industriale del personale EOS. I risultati parlano da soli e sono la prova di un grande lavoro di squadra", aggiunge il Dr. Steffen Beyer.
Risultati
I risultati della nuova testa dell'iniettore prodotta con la manifattura additiva sono estremamente impressionanti: invece di 248 parti, è composta da una sola, con la stessa funzionalità e riducendo al minimo il tempo necessario.
La tecnologia di stampa 3D industriale a letto di polvere di EOS ha permesso, ad esempio, di stampare i 122 ugelli di iniezione, la base e le piastre frontali e la cupola di distribuzione con i relativi tubi di alimentazione per i carburanti idrogeno e ossigeno come un unico componente integrato. Rispetto ai sistemi a laser singolo, la produttività significativamente più elevata del sistema multi-laser EOS M 400-4 ha permesso di ridurre i tempi di costruzione di un fattore 3 e i costi del 50% nell'esempio della testa dell'iniettore AiO.
Il team del progetto è stato in grado di registrare una serie di ulteriori successi. Il design semplificato e le migliori proprietà dei materiali rispetto alla qualità dei pezzi fusi hanno permesso alla tecnologia additiva di ridurre notevolmente lo spessore delle pareti, senza perdere in resistenza.
Una riduzione significativa del peso significa anche un'ulteriore riduzione dei tempi di costruzione e, naturalmente, dei costi.
Infine, i processi di produzione additiva consentono di accelerare notevolmente i cicli di innovazione. I miglioramenti strutturali, le modifiche progettuali e la produzione di componenti di prova nella fase di sviluppo possono essere messi direttamente in produzione sulla base dei dati CAD, senza che gli ingegneri debbano dedicare tempo alla preparazione degli strumenti, come avviene per le parti fuse. La stampa 3D industriale consente quindi un salto di qualità in termini di tempi di realizzazione. Se prima ogni iterazione richiedeva circa mezzo anno, ora è sufficiente qualche giorno. Inoltre, l'intera catena di produzione si svolge all'interno della sede di ArianeGroup. In poche parole: Missione compiuta!
Vantaggi
- -131 Giorni di iterazione
- -247 Integrazione funzionale di singole parti
- -50% di riduzione dei costi
Storie di innovazione EOS
Esplorate tre decenni di eccellenza pionieristica nella stampa 3D con EOS