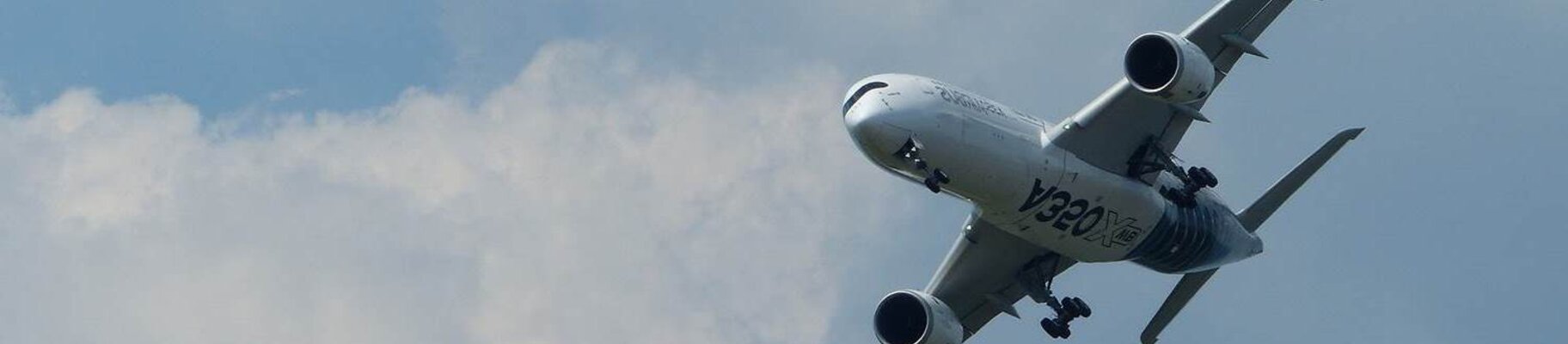
Sogeti High Tech Additive Manufacturing per il nuovo Airbus A350 XWB
Passaggio dei cavi dell'A350 XWB: dalla progettazione al componente in due settimane | Storia di successo
Il momento in cui un aereo commerciale completamente nuovo si alza in volo per la prima volta è sempre speciale, e questo è stato particolarmente vero per l'Airbus A350 XWB. Essendo figlio del nuovo millennio, è stato chiaro fin dall'inizio che il lavoro di sviluppo si sarebbe concentrato su materiali e processi produttivi innovativi: l'obiettivo era nientemeno che costruire l'aereo più efficiente del mondo. In quanto tecnologia del futuro, la produzione additiva era un'altra possibilità da prendere in considerazione durante lo sviluppo. Nell'ambito di un progetto pilota, gli esperti di Sogeti High Tech sono riusciti a sviluppare un supporto per cavi sul longherone anteriore dello stabilizzatore verticale dell'aereo passeggeri in tempi record, impiegando solo due settimane dallo schizzo iniziale al pezzo finito. La tecnologia e l'esperienza di EOS hanno rappresentato un aspetto fondamentale di questo processo di sviluppo.
"Ottenere un componente esistente 'pronto per l'AM' in sole due settimane significava avere successo al primo tentativo. L'eccellente e proattiva collaborazione con EOS ha reso possibile questa ambiziosa impresa, con risultati eccezionali".
Carlos Ribeiro Simoes | Additive Manufacturing Offering Leader | Sogeti High Tech
Sfida
Sviluppo e produzione, in tempi critici, di un supporto per il passaggio dei cavi di una telecamera nello stabilizzatore verticale dell'A350 utilizzando la fabbricazione additiva
Il progetto prevedeva in particolare la produzione di un supporto per il passaggio dei cavi per l'ultimo modello di Airbus. Il supporto era necessario per l'alimentazione e il trasporto dei dati di una telecamera posizionata nello stabilizzatore verticale, che fornisce una visione dell'esterno ai passeggeri e l'orientamento a terra ai piloti.
Il documento dei requisiti di prodotto richiedeva un componente funzionalmente operativo e adatto alla produzione in serie. Questo compito è stato affidato a Sogeti High Tech, una società interamente controllata da Cap Gemini S.A., quotata alla Borsa di Parigi.
La sfida particolare in questo caso era rappresentata dal breve tempo di consegna di appena due settimane. L'intero sviluppo doveva essere completato entro questo lasso di tempo: Dall'analisi del pezzo e dell'attuale configurazione dell'installazione, allo studio dei parametri per ottimizzare la topologia e la sua interpretazione, fino alla progettazione e alla produzione del pezzo finito. Il supporto doveva inoltre avere il minor numero possibile di strutture di supporto per evitare la post-elaborazione.
Inoltre, le specifiche del componente richiedevano l'integrazione del portacavi a scatto, la riduzione del peso e la conformità ai severi requisiti per la successiva certificazione dell'industria aeronautica.
Il componente prodotto in modo convenzionale era costituito da parti in lamiera sagomata e da numerosi rivetti, per un totale di oltre 30 pezzi singoli. I connettori a spina nell'area superiore erano realizzati in plastica, quindi in un materiale diverso da quello delle altre singole parti del supporto. L'obiettivo era quello di sviluppare una soluzione integrata costituita da un unico pezzo che comprendesse anche i connettori a spina, riducendo così in modo significativo i tempi di costruzione e installazione. L'obiettivo di riduzione del peso per la produzione additiva è stato determinato da uno studio dei parametri basato sull'ottimizzazione della topologia.
Soluzione
La riduzione a un singolo componente e la produzione su EOS M 400 riducono il tempo di produzione a 19 ore.
Per il nuovo componente, Sogeti High Tech ha seguito il collaudato processo di sviluppo per la progettazione di parti prodotte in modo additivo. Il progetto ha preso il via con un'analisi del componente esistente, prodotto in modo convenzionale, in termini di processo di produzione imminente, con un risultato estremamente positivo. La funzionalità, il materiale e la struttura precedentemente complessa del componente lo rendevano un candidato ideale per la tecnologia di stampa 3D a letto di polvere di EOS. La libertà di progettazione offerta da questa tecnologia consente di produrre strutture complesse in un unico pezzo, il che significa che è possibile scegliere un design a peso ridotto senza trascurare l'integrazione funzionale.
Questa analisi ha poi permesso di definire il cosiddetto spazio di progettazione, ovvero lo spazio che il supporto per il passaggio dei cavi può occupare. Come materiale è stata scelta la lega di alluminio AlSi10Mg, ideale per strutture complesse a pareti sottili. Le interfacce con le aree esterne sono rimaste invariate, formando lo spazio di non progettazione, il che significa che non è stato necessario apportare modifiche. I carichi definiti sono stati presi come condizioni al contorno per l'ottimizzazione della topologia nello studio dei parametri, fornendo la base per un nuovo progetto.
Come di consueto, per i calcoli di ottimizzazione della topologia è stato utilizzato un software CAE; per la riprogettazione, invece, è stata impiegata una soluzione dedicata alla progettazione di strutture con superfici a forma libera. Sogeti High Tech ha realizzato direttamente il progetto. Per rispettare il lead time di due settimane, EOS ha calcolato il tempo di costruzione e i parametri ottimizzati dai risultati dell'ottimizzazione topologica utilizzando il software EOSPRINT. In questo modo è stata creata l'implementazione CAE per il pezzo fabbricato, tenendo conto anche delle possibilità e dei limiti del processo di produzione e della necessità di evitare strutture di supporto.
"Oltre a un hardware eccezionale, EOS offre anche un'esperienza completa nella realizzazione di componenti fabbricati in modo additivo, un aspetto che valutiamo molto positivamente".
Carlos Ribeiro Simoes | Additive Manufacturing Offering Leader | Sogeti High Tech
Risultati
Grazie alla collaborazione tra Sogeti ed EOS, è stato possibile sviluppare un componente ottimizzato per la produzione additiva che sfrutta appieno la libertà di progettazione offerta dalla tecnologia DMLS, pur tenendo conto delle sue limitazioni. Ciò ha permesso di integrare nel progetto connettori a spina per il passaggio dei cavi e di incorporare un rinforzo locale in specifiche aree critiche, al fine di ottimizzare la struttura. Le aperture e i montanti autoportanti all'interno del componente contribuiscono a ridurre al minimo lo sforzo e quindi i costi di post-lavorazione.
Inoltre, il supporto può essere prodotto con estrema rapidità, ogni volta che è necessario. La produzione, che viene eseguita su un EOS M 400 con spessori di strato di 90μm - richiede solo 19 ore invece dei 70 giorni necessari in precedenza.
Ciò corrisponde a una riduzione dei tempi di produzione ben superiore al 90%. Ciò è dovuto in gran parte al fatto che i numerosi passaggi individuali e i 30 pezzi precedenti sono stati riuniti in un componente centrale che ora può essere prodotto in un unico ciclo. Inoltre, i singoli pezzi non devono più essere costruiti e tenuti a magazzino, il che può essere costoso. Anche lo stoccaggio dell'intero gruppo di componenti è ora molto più semplice.
Sogeti è riuscita a risparmiare non solo un'enorme quantità di tempo nella produzione, ma anche nello sviluppo. L'intero processo, dallo schizzo iniziale al componente finito, ha richiesto solo due settimane. Si tratta di un tempo di realizzazione fenomenale. Allo stesso tempo, il design si traduce in una maggiore efficienza in termini di peso.
Mentre il pezzo originale prodotto in modo convenzionale pesava 452 grammi, il supporto per cavi prodotto in modo additivo pesa solo 317 grammi - e si sa che l'industria aeronautica conta ogni singolo grammo nell'interesse di ridurre al minimo il consumo di carburante. Il cliente, Airbus, è stato più che soddisfatto dei risultati.
Il risultato in sintesi
- -29 Parti singole Integrazione funzionale
- -90% Riduzione dei tempi di produzione
- -135 grammi Riduzione di peso
Per saperne di più
Esplorate tre decenni di eccellenza pionieristica nella stampa 3D con EOS