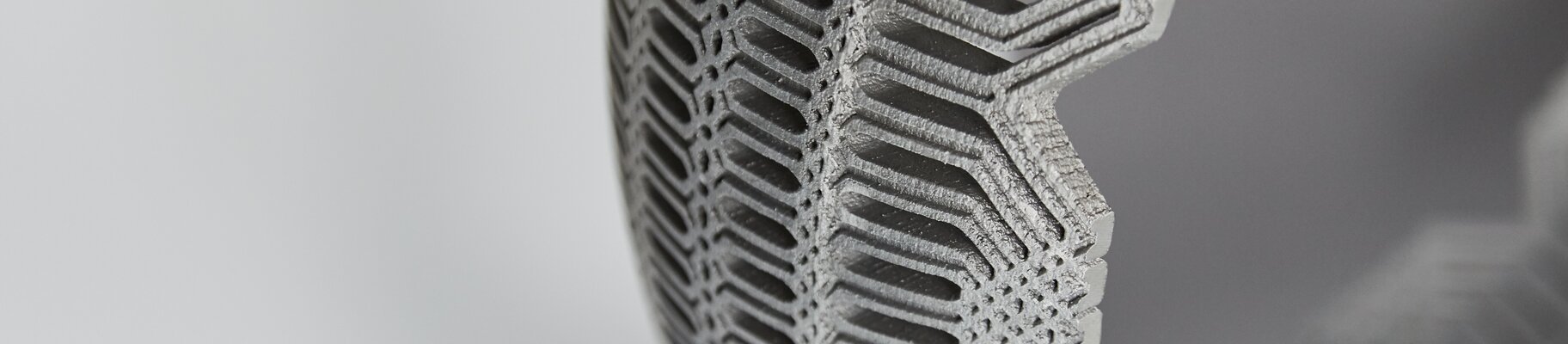
La stampa 3D nel settore manifatturiero
Applicazioni ed esempi pratici
Le migliori pratiche per la stampa 3D negli ambienti di produzione e lavorazione
Pressione sui costi, requisiti normativi, richieste crescenti da parte dei clienti e molto altro ancora. Le aziende del settore produttivo e industriale si trovano ad affrontare una serie di sfide in continua espansione. Allo stesso tempo, questioni come l'efficienza energetica e delle risorse stanno diventando sempre più importanti.
La produzione additiva offre un ampio spettro di potenziali vantaggi economici e sostenibili alle aziende del settore produttivo e industriale.
La stampa 3D industriale apre nuove opportunità e fornisce soluzioni in molti modi diversi, dalla produzione di pezzi all'ottimizzazione del ritorno sugli investimenti. Noi di EOS offriamo soluzioni personalizzate da un'unica fonte per la tecnologia e tutto ciò che serve per una transizione rapida e sicura.