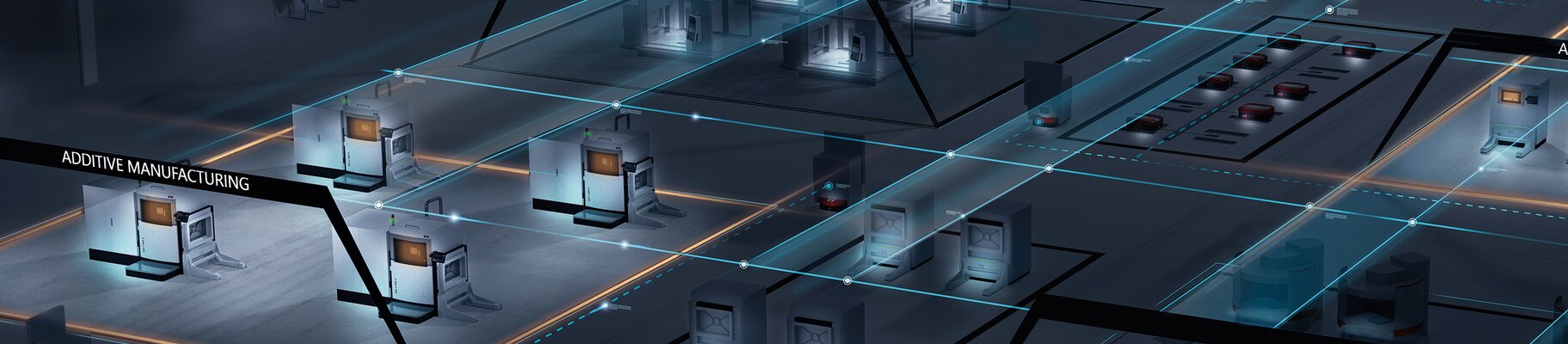
Faites évoluer votre production de fabrication additive
23 août 2021 | Temps de lecture : 9 min
Comment augmenter et optimiser la productivité d'une usine d'impression 3D industrielle avec un minimum d'efforts ? Nous avons utilisé un logiciel de simulation pour simuler le processus de fabrication additive et les étapes de post-traitement. Le cas d'utilisation de notre client rend le processus de mise à l'échelle facile à suivre.
Comment obtenir le meilleur retour sur investissement ?
La mise à l'échelle de la production de fabrication additive (FA) est une tâche ardue, car il faut tenir compte de nombreux facteurs avant de décider d'une stratégie de mise à l'échelle.
Cet article s'adresse à ceux qui souhaitent augmenter et optimiser la productivité de leur usine FA avec un minimum d'efforts. Nous décrirons un cas d'utilisation réel qui rendra le processus de mise à l'échelle facile à suivre.
Le principal défi
Le client souhaitait augmenter sa production en ajoutant trois systèmes EOS P 396 396 à ses deux machines EOS P396 existantes. Cependant, l'équipe n'était pas sûre que les machines de post-traitement existantes puissent supporter le débit le plus élevé avec une équipe d'un seul ouvrier. Le produit FA est resté le même, ce qui signifie que le flux de travail et le type d'équipement sont restés les mêmes. Le principal défi consistait à optimiser l'équipement et les ressources de post-traitement supplémentaires afin d'obtenir le débit le plus élevé possible tout en maintenant le coût par pièce à un niveau aussi bas que possible.
Nous avons aidé le client à développer un modèle de production personnalisé avec des paramètres d'entrée variables appropriés. Différents scénarios peuvent être générés en faisant varier ces paramètres d'entrée afin de vérifier la sensibilité du débit et du coût par pièce. Ces informations aident le client à décider du scénario optimisé avec l'investissement supplémentaire le plus faible pour mettre à l'échelle la production FA .
En résumé, nous avons identifié les goulets d'étranglement dans l'usine. En apportant de petites modifications au post-traitement, nous avons augmenté la production de 24 %, la marge de 124 %, le retour sur investissement (ROI) de 115 % et le coût par pièce (CPP) de 18 %.
Utiliser la simulation pour résoudre le problème de l'optimisation de la production
Une analyse de rentabilité réussie pour la production en série nécessite une analyse approfondie de tous les paramètres de production qui ont un impact sur le rendement et les coûts. Ces paramètres de production sont souvent liés les uns aux autres de manière non linéaire, et il n'est donc guère possible de les optimiser à l'aide d'une feuille de calcul Excel. En revanche, les logiciels de simulation prennent en compte toutes les complexités liées à la production et résolvent le problème d'optimisation de manière plus directe.
Chez EOS, nous utilisons Tecnomatix Plant Simulation de Siemens et offrons notre service pour aider nos clients à simuler des solutions personnalisées afin d'avoir une bonne compréhension du processus pour une décision d'achat ou de vente.
Nous utilisons un logiciel de simulation pour simuler le processus FA et les étapes de post-traitement. Une entreprise prospère sur le site FA doit analyser le débit et les coûts du post-traitement, ce qui peut parfois faire pencher la balance en sa faveur. La simulation facilite l'examen minutieux de la chaîne de traitement complexe.
La simulation d'usine est une simulation à événements discrets qui examine tous les événements planifiés. Par exemple, si le traitement d'une tâche dure 1 heure, le simulateur prendra en compte l'heure de début et l'heure de fin de la tâche. Il ne simulera pas la manière dont le travail est traité, mais l'heure à laquelle un événement se produit. D'autres événements planifiés sont les heures de travail des employés, le temps de préparation, le temps de maintenance d'une machine, etc.
Introduction à l'étude de cas
La simulation d'usine est une simulation à événements discrets qui examine tous les événements planifiés. Par exemple, si le traitement d'une tâche dure 1 heure, le simulateur prendra en compte l'heure de début et l'heure de fin de la tâche. Il ne simulera pas la manière dont le travail est traité, mais l'heure à laquelle un événement se produit. D'autres événements planifiés sont les heures de travail des employés, le temps de préparation, le temps de maintenance d'une machine, etc.
Station de déballage | x1 |
Système de gestion des poudres | x1 |
DyeMansion Powershot C | x1 |
DyeMansion Powershot S | x1 |
DyeMansion DM60 | x2 |
Traitement UV | x1 |
Finition de surface | x2 |
Zone de séchage | x1 |
Table d'inspection | x1 |
Avec l'imprimante EOS P 396, le client peut imprimer des travaux contenant 144 pièces. Deux EOS P 396 peuvent produire 426 travaux par an ou 61 344 pièces par an. Le client doit produire 600 travaux supplémentaires par an, soit 66 400 pièces supplémentaires par an. Un premier calcul montre que trois EOS P 396 supplémentaires seraient nécessaires pour atteindre l'objectif, ce qui représente un investissement important pour l'entreprise. L'objectif de la simulation de production était donc de déterminer si le rendement pouvait être atteint en utilisant la même quantité d'équipement de post-traitement et en tenant compte de toutes les complexités de la production telles que les défaillances, la maintenance et les modèles d'équipes de travailleurs.
Comment nous avons procédé :
L'ensemble de l'aménagement a été divisé en trois zones (voir figure 1) :
- FA imprimantes
- Gestion des poudres
- Post-traitement
Le client préfère avoir trois régions pour minimiser le risque de contamination croisée de la poudre. Nous avons d'abord construit un modèle de simulation avec les deux sites EOS P 396 existants, puis un second modèle avec trois sites EOS P 396 supplémentaires et les équipements mentionnés ci-dessus. Le client utilise une équipe d'un travailleur du lundi au vendredi. Au cours du processus d'analyse, nous avons soigneusement adapté toutes sortes de variables telles que les consommables et les opérateurs pour l'installation de production.
Une simulation d'événements discrets peut simuler tous les événements qui se produisent à un moment donné. Elle prend en compte l'heure de début et l'heure de fin, mais ne tient pas compte de ce qui se passe entre les deux.
Par exemple, disons que vous entrez dans le distributeur de billets à 17:50 et que vous en sortez à 17:53. La simulation montre un événement à 17:50, qui est le début de l'événement, puis saute à 17:53, qui est la fin de l'événement. Dans une simulation d'usine, l'horloge passe d'un événement programmé au suivant.
Dans le contexte de la fabrication, il s'agit d'une pièce qui entre dans une machine pour y être traitée et qui en sort une fois le processus terminé. Le traitement d'une pièce peut comporter plusieurs étapes (temps de préparation, temps de chargement, temps de déchargement) qui peuvent toutes être incluses dans la simulation. L'étude de simulation permet d'augmenter le débit et l'utilisation des machines. Elle peut également aider à déterminer le nombre de travailleurs, d'équipements, de machines et la taille des entrepôts afin d'obtenir la meilleure analyse de rentabilité.
Analyse et résultats de la simulation
Optimisation de la zone FA et de la zone de gestion des poudres
Nous avons commencé par simuler la zone FA et la zone de gestion des poudres avant d'inclure l'équipement de post-traitement. Le modèle de poste est resté inchangé par rapport à l'original :
- Poste : 1 poste (8 heures), du lundi au vendredi
- Temps de construction : 20 heures.
Une fois le modèle construit, le premier défi consistait à identifier le nombre optimal de travailleurs pour ces deux activités. Nous avons effectué cinq expériences (Exp.) et déterminé qu'un travailleur est suffisant pour ces deux domaines, comme le montre le tableau 1. Que nous ayons 1 ou 5 opérateurs, le débit reste le même (1,065 travail par an).
Nombre d'opérateurs | Emplois produits |
---|---|
Exp 1 1 | 1065 |
Exp 2 2 | 1065 |
Exp 3 3 | 1065 |
Exp 4 4 | 1065 |
Exp 5 5 | 1065 |
Tableau 1 : Nombre d'exploitants dans la zone de gestion FA & Powder et production annuelle respective
Ensuite, nous nous sommes concentrés sur l'optimisation du nombre de boîtes de transport de poudre (EOS Multi-box, voir image 1), permettant à un travailleur de distribuer la poudre aux machines EOS. En dix itérations, nous avons identifié que sept Multiboxes EOS sont le nombre optimal pour atteindre un débit de 1062 travaux par an (voir Tableau 2). L'augmentation de la production obtenue avec plus de sept Multibox ne justifie pas les coûts supplémentaires. Il n'y a qu'un gain de trois travaux par an (de 1062 à 1065), et l'augmentation des coûts, qui n'apparaît pas dans ce rapport, ne justifie pas ce petit gain de production.
Nombre de boîtes multiples | Emplois produits |
---|---|
Exp 01 1 | 184 |
Exp 02 2 | 367 |
Exp 03 3 | 551 |
Exp 04 4 | 732 |
Exp 05 5 | 911 |
Exp 06 6 | 983 |
Exp 07 7 | 1062 |
Exp 08 8 | 1064 |
Exp 09 9 | 1064 |
Exp 10 10 | 1065 |
Tableau 2 : Nombre de Multibox et emplois respectifs
Optimisation de la zone de post-traitement :
Après l'optimisation de la zone FA et de la gestion des poudres, la zone de post-traitement a constitué la tâche suivante. Elle comprenait sept stations de traitement différentes avec dix étapes :
- Nettoyage partiel à DyeMansion* Powershot C
- Nettoyage par ultrasons
- Finition de surface
- Nettoyage par ultrasons
- Séchage
- Traitement de surface à DyeMansion* Powershot S
- Traitement UV
- Coloration dans DyeMansion DM60
- Traitement de surface à DyeMansion* Powershot S
- Traitement UV
(*DyeMansion fait partie de l'écosystème EOS)
En outre, il y a eu quelques défis concernant le flux de travail du client. Par exemple, les stations de sablage (Powershot S et C) de notre partenaire DyeMansion ne doivent traiter que la moitié des pièces produites dans une construction (72 pièces sur 144), c'est-à-dire deux lots par construction. En revanche, pour toutes les autres stations telles que le système de coloration DyeMansion DM60, la finition de surface, le séchage, etc., tous les travaux doivent être traités, c'est-à-dire un lot par construction.
Une fois le modèle original étendu à la zone de post-traitement, nous nous sommes attachés à trouver le nombre optimal d'opérateurs. En partant de l'optimum FA de 1 062 emplois par an, nous avons exécuté cinq configurations différentes avec 1 à 5 opérateurs. Comme le montre le tableau 3, 4 opérateurs seraient nécessaires pour que la zone de post-traitement ait un débit considérablement plus élevé que le nombre précédent de travailleurs. 4 emplois supplémentaires ne justifient pas le coût supplémentaire (non indiqué ici) d'un opérateur supplémentaire (848 contre 849 emplois).
Nombre d'opérateurs | Les emplois se construisent grâce à FA | Emplois créés grâce à FA + Post-traitement |
---|---|---|
Exp 1 1 | 1062 | 228 |
Exp 2 2 | 1062 | 666 |
Exp 3 3 | 1062 | 787 |
Exp 4 4 | 1062 | 848 |
Exp 5 5 | 1062 | 849 |
Tableau 3 : Nombre d'opérateurs pour la zone de post-traitement et emplois respectifs
Conclusion
Le message clé ici est que la mise à l'échelle et l'optimisation de votre stratégie de production FA peut être une tâche compliquée. Il s'agit d'un défi unique, adapté à une configuration spécifique, avec des paramètres clés différents pour chaque scénario. Ne pas analyser et prendre en compte votre stratégie peut conduire à des conclusions erronées. Grâce à notre expertise en matière de simulation et à nos 30 ans d'expérience sur FA , nous pouvons élaborer pour vous une stratégie de dimensionnement gagnante afin d'obtenir la meilleure utilisation de la machine et le coût le plus bas par pièce.