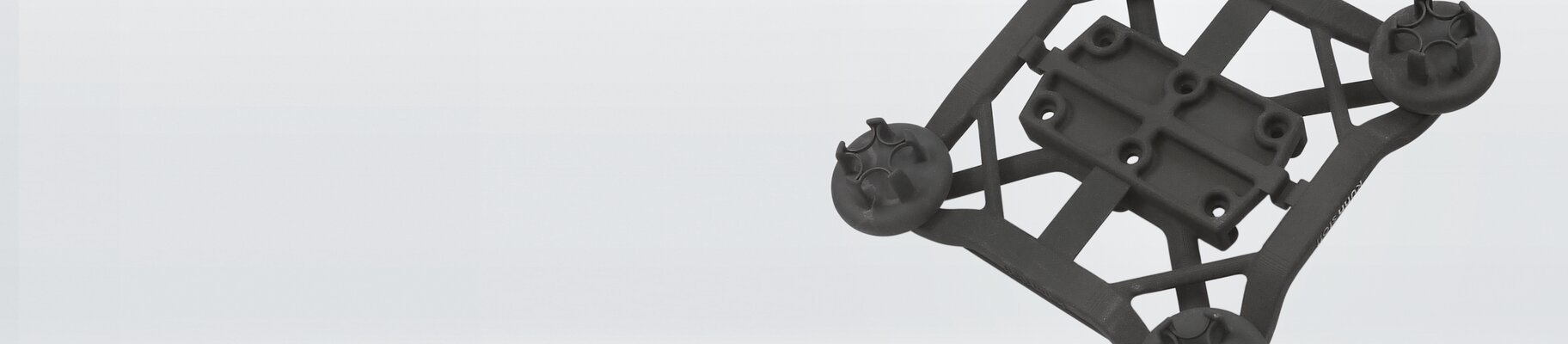
Sistema de agarre fabricado por aditivos, ligero y duradero gracias a la tecnología EOS
Grupo Wittmann y KuhnStoff | Estudio de caso
Pinza Bronquial Con Placa Base Funcional Ligera y Duradera Con Tecnología EOS
La mano es uno de los peldaños definitorios de la evolución humana: con su pulgar opuesto a los demás dedos, la mano humana es una herramienta ideal para agarrar, explorar y trabajar. Como tal, es la clave de la actividad cultural y el progreso técnico. La industria explota a menudo este ingenioso principio: uno de los procesos para los que se utilizan máquinas es el agarre automatizado de casi cualquier pieza deseada para transportarla al siguiente paso operativo.
Estas máquinas de agarre son obras maestras de la ingeniería. Kuhn-Stoff GmbH & Co KG se ha dedicado a la ingeniería especializada mediante la aplicación de la tecnología de fabricación aditiva EOS. El proceso consiste en la formación de piezas de máquinas, capa a capa, a partir de polvo de plástico que se funde con un rayo láser. De este modo, Kuhn-Stoff ha desarrollado y producido una pinza bronquial extremadamente ligera, resistente y duradera para Wittmann Robot Systeme GmbH, en Núremberg (Alemania). Cuatro de estas pinzas se asientan sobre un bastidor de soporte con conductos neumáticos integrados.

"Llevamos años utilizando piezas construidas mediante fabricación aditiva en diversos sectores de la automatización. La pinza bronquial cumple todos nuestros requisitos, de hecho los supera. La pieza es muy fiable en cuanto a su rendimiento diario".
Michael Tolz | Director de Tecnología, Alemania y Director de Sucursal | Wittmann Robot Systeme GmbH en Nuremberg
Desafío
El cliente es un fabricante de robots y sistemas de automatización. Se pidió a Kuhn-Stoff que rediseñara una pinza mecánica que elevara, transportara y depositara piezas de una máquina de producción mediante un mecanismo neumático. Se establecieron los siguientes requisitos: la pinza debía ser más ligera que su predecesora, sin dejar de ser capaz de mover las cargas requeridas. La complejidad del diseño debía simplificarse y la pieza debía satisfacer criterios de eficiencia.
La importancia del peso se reduce a la física: los sistemas de agarre de este tipo deben trabajar con rapidez para mover el mayor número posible de piezas de la máquina en una unidad de tiempo determinada.
El hecho de que la masa sea inerte significa que hay que aplicar una fuerza para ponerla en movimiento: cuanto más pesada sea una carga y más rápido se mueva, mayores serán las fuerzas necesarias tanto para la aceleración como para la deceleración.
Aparte del punto de vista de la eficiencia energética, este hecho también tiene consecuencias especialmente negativas en la durabilidad del sistema: cuanto mayores son las fuerzas en juego, mayor es el desgaste de la máquina.
La versión anterior de la pinza estaba fabricada con aluminio, tubos de goma y múltiples elementos de conexión, y su producción resultaba cara. Los expertos en fabricación por capas de Kuhn-Stoff se fijaron el objetivo de simplificar considerablemente el diseño. La nueva estructura de la pieza de la máquina debía contribuir a una parte de la reducción de peso. Otra parte debería conseguirse mediante la optimización estructural de las piezas restantes, una de las principales ventajas de la fabricación aditiva. Al iniciarse los trabajos, pronto quedó claro que la nueva pinza podía fabricarse como una sola pieza, sin necesidad de acabado posterior a la producción ni de ensamblaje posterior.

Solución
El equipo de Kuhn-Stoff empezó por examinar la funcionalidad y los requisitos de trabajo de la pinza: cuando fluye aire comprimido en una membrana flexible, las garras de la pinza se abren; del mismo modo, el sistema se cierra cuando se apaga el aire comprimido. Además de la flexibilidad del plástico, la pieza debe poder girar 90° para realizar la secuencia de movimiento necesaria. Teniendo en cuenta estos requisitos, fue posible reducir el número de piezas necesarias a sólo dos componentes.
Una vez finalizado el proceso de diseño, Kuhn-Stoff comenzó a trabajar en la producción del nuevo sistema de agarre utilizando una FORMIGA P 100. En pocas horas se fabricaron en poliamida los dos componentes del sistema de agarre. Gracias a la tecnología EOS, los conductos neumáticos y los conectores se integraron completamente en la placa base.
"Como de costumbre, la producción con el sistema EOS fue fluida y sin problemas. El resultado final, una vez más, impresionó a todos los implicados. En un solo paso del proceso fuimos capaces de crear una pieza funcionalmente integrada que superaba todos los requisitos del cliente. En resumen: la fabricación aditiva es ya una realidad cotidiana, pero los resultados siguen siendo extraordinarios", afirma Hannes Kuhn, Director General de Kuhn-Stoff GmbH.

"Llevamos más de ocho años utilizando la tecnología EOS y los resultados han sido exclusivamente positivos. Cuando se aplica correctamente, la flexibilidad del diseño ofrece ventajas significativas que pueden dar a nuestros clientes ventajas casi inigualables en el mercado."
Hannes Kuhn | Director General | Kuhn-Stoff GmbH & Co KG
Resultados
En cuanto al objetivo principal de reducción de peso, Kuhn-Stoff logró una disminución del 86 % hasta sólo 220 g. A pesar de su ligereza, la pinza sigue siendo capaz de soportar las cargas necesarias, incluso en un uso exigente y continuo: después de 5 millones de ciclos, el equipo detuvo las pruebas de esfuerzo, habiendo alcanzado la vida útil designada. Durante este periodo, no se ha producido ni un solo defecto o fallo. La razón es la resistencia de la construcción, que se consiguió a pesar de los conductos de aire integrados en la placa base. Además, el diseño flexible garantiza que, en caso de producirse pequeñas colisiones, éstas no provoquen daños en el sistema de agarre ni en la herramienta de moldeo por inyección. En algunos casos, el menor peso también permite utilizar un tipo de robot más pequeño, lo que se traduce en importantes reducciones de costes. Además, Wittmann ha podido aumentar el número de ciclos de trabajo gracias a la baja altura de la pinza, que reduce la anchura de apertura necesaria de la platina de sujeción de la máquina de moldeo por inyección. El resultado final es una reducción de los costes de explotación.
Los costes de fabricación se han reducido en un 50 % en comparación con el predecesor fabricado convencionalmente. Esto se debe al ahorro de peso, así como a la reducción del número de componentes de 21 a dos. Igualmente importante es el corto tiempo de producción: el sistema de agarre, cuya fabricación antes llevaba a Kuhn-Stoff doce días, ahora sólo requiere tres.
"Estamos muy contentos con el nuevo sistema de agarre. Ha demostrado ser igual de eficaz que la unidad anterior en el uso continuo y pesado, pero es más barata y ligera y puede fabricarse con mayor rapidez. Nunca había visto un avance tan significativo en la fabricación de pinzas como el que la fabricación aditiva ha aportado a la producción de nuestra pinza bronquial. El método de producción ha tenido un efecto muy positivo en nuestras soluciones de automatización", resume Michael Tolz, Jefe de Tecnología y Director de Sucursal de Wittmann Robot Systeme GmbH. En ocasiones, la revolución puede tener sus ventajas sobre la evolución.
Resumen de los resultados
-
-1350 gramos: Reducción de peso del 86
-
-50 % Costes: Reducción de los costes de producción en un 50
-
-19 Componentes: Reducción de los componentes individuales de 21 a 2

Casos prácticos de EOS
Explore tres décadas de excelencia pionera en impresión 3D con EOS