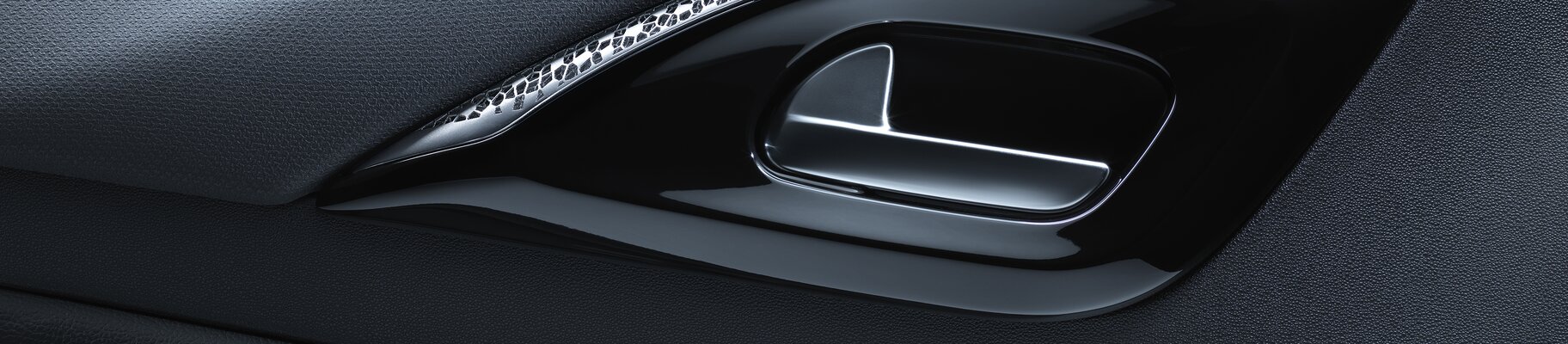
Fabricación aditiva de accesorios personalizados para automóviles
Spartacus3D | Historia de éxito
DS 3 Dark Side Edición Limitada - Innovación avanzada mediante fabricación aditiva
En el sector de la automoción, las ediciones limitadas de modelos de éxito son un inteligente movimiento de marketing. Pero los fabricantes de automóviles siempre buscan formas específicas de distinguirse de sus competidores dentro de sus segmentos de mercado. DS Automobiles, una marca del Grupo PSA, consiguió establecerse en el segmento premium en pocos años gracias a una serie de modelos icónicos. El modelo compacto DS 3 ha recibido un amplio reconocimiento en este segmento, con la presentación periódica de modelos de edición limitada. Para la edición Dark Side, DS Automobile quiso ir más allá del equipamiento habitual incluyendo piezas impresas en 3D para destacar su continua dedicación a la innovación. La fabricación aditiva dio total libertad creativa al equipo de diseño de DS, así como una implementación y producción muy rápidas y sencillas gracias a los expertos de Spartacus3D que trabajan con una máquinaEOS M 290 .
"Ha sido un proyecto tremendo de principio a fin, tan emocionante como desafiante para nuestra experiencia. Nos emociona imaginar que todos estos coches están ahora por todo el mundo. Y a lo largo de todo este proyecto, sabíamos que podíamos contar con la fiabilidad, la calidad y el apoyo de EOS."
Charles de Forges | Director General | Spartacus3D

Desafío
Fabricar accesorios de alta calidad para las ediciones limitadas de DS 3 con diseños únicos y plazos de comercialización rápidos
El proyecto comenzó cuando el equipo de DS Design empezó a buscar mejoras innovadoras para el interior de la edición limitada del DS 3. Los accesorios debían poner de relieve la constante búsqueda de innovación del fabricante de automóviles y, al mismo tiempo, satisfacer los más altos estándares de calidad exigidos por el segmento premium. Desde el principio, los diseñadores decidieron aprovechar el potencial de la fabricación aditiva para presentar una primicia mundial en este campo. La fabricación aditiva abre nuevas posibilidades de diseño;
DS Automobiles presenta cada año varias ediciones limitadas para el DS 3, por lo que contar con estas nuevas opciones supone un verdadero cambio para el equipo. El equipo de diseño también eligió el titanio, un material que da un toque de lujo, es resistente y permite un acabado fácil y de buen aspecto.
Pero aunque la impresión 3D se utiliza habitualmente en el sector de la automoción para la creación de prototipos, la producción en serie con fabricación aditiva sigue siendo muy poco frecuente, especialmente para piezas metálicas. Por lo tanto, DS Automobiles tenía que encontrar un socio con experiencia en fabricación aditiva y capacidad de producción suficiente para satisfacer sus necesidades de volumen. El objetivo era entregar unos 700 coches en los mercados de todo el mundo. El proyecto también tenía un plazo de desarrollo limitado para ajustarse a la planificación de la producción del coche, con objetivos muy precisos en términos de salida al mercado.
Cada edición limitada tiene un objetivo de precio específico, por lo que todas las piezas de fabricación aditiva deben ajustarse al presupuesto global. La fase de investigación dio como resultado la elección de dos piezas: el tirador de la puerta y el llavero.
Spartacus3D, filial del grupo francés de transformación de materiales Farinia, cumplía todos estos requisitos: al utilizar la impresión 3D desde hace años, la empresa tiene un conocimiento muy profundo de la fabricación aditiva para ayudarles a trasladar a la producción los diseños proporcionados por el equipo de DS. Con su máquina EOS M 290 y EOS Titanium Ti64, Spartacus3D disponía de todas las competencias necesarias para responder a las exigencias de diseño y calidad a las que aspiraba DS Automobiles, así como de las capacidades de producción y postratamiento necesarias para entregar el proyecto a tiempo.
Solución
Producción en serie de las piezas en una EOS M 290 en EOS Titanium Ti64
El equipo de diseño de DS utilizó un innovador diseño paramétrico para crear las cubiertas interiores de los tiradores de las puertas y el detalle del portallaves electrónico en una malla de titanio muy intrincada, que pone de relieve la innovación y la dedicación a la calidad de DS Automobiles.
Para encontrar el mejor compromiso entre calidad, coste y diseño, fueron necesarias muchas iteraciones entre el equipo de diseño de DS y Spartacus3D. Esto incluyó la fabricación de varios prototipos, algo que la fabricación aditiva hace especialmente fácil de realizar en un solo lote de producción.
Como parte de este proceso, el equipo de diseño de DS también seleccionó el acabado de las piezas; finalmente se decantaron por un atractivo acabado mate obtenido mediante pulido manual. El equipo de calidad definió criterios de aceptación precisos para la distorsión, la calidad de la superficie (por ejemplo, porosidad y brillo) y los bordes de corte. Paralelamente a este vaivén, Spartacus3D también trabajó en la optimización de la producción de las piezas; para reducir los costes, Spartacus3D no sólo tenía que determinar la mejor orientación y estructura de soporte, sino también perfeccionar su estrategia patentada de fusión por láser. Se sabe que el titanio genera algunas tensiones residuales durante el proceso de fusión, y la larga y delgada cubierta de la manilla de la puerta era una buena candidata para sufrir la máxima distorsión. Añadir un tratamiento térmico para aliviar tensiones no era viable desde el punto de vista económico; en su lugar, se utilizaron algunos parámetros específicos para evitar este riesgo. Otras formas de reducir el coste son aumentar las piezas por lote o reducir el número de soportes, el consumo de polvo, el tiempo de postprocesado, etc.

La experiencia en fabricación aditiva de Spartacus3D fue inestimable en cada paso del proceso, desde la ingeniería de diseño hasta la optimización de la impresión 3D, lo que permitió acortar los ciclos de vida de desarrollo del producto y acelerar su comercialización. La selección del material óptimo ayudó a asegurar la rigidez y garantizar la máxima calidad de la pieza tras el posprocesamiento. "Haber sido seleccionados para colaborar con DS Automobiles en este proyecto tan innovador es un privilegio. Su marca lleva años representando fielmente la elegancia y el saber hacer en la industria automovilística francesa. Esto también significa que nuestros esfuerzos se ven recompensados y demuestra que Spartacus3D es capaz de ofrecer soluciones robustas para la producción en serie. Utilizando los sistemas DMLS que tenemos en nuestro taller, sabíamos que seríamos capaces de producir las mejores piezas", afirma Charles de Forges, Director General de Spartacus3D.
Resultados
Gracias a la experiencia en impresión 3D de Spartacus3D, fue posible desarrollar una estrategia de fabricación aditiva optimizada para los requisitos del equipo de diseño de DS. El diseño paramétrico aprovechó plenamente el potencial de la tecnología EOS: el complejísimo diseño original de las dos piezas pudo producirse casi una a una gracias a la fabricación aditiva y se optimizó para que pudieran fabricarse varias unidades al mismo tiempo. Esto redujo al mínimo los costes de producción.
El material, EOS Titanium Ti64, también permitió el acabado posterior a la producción, dando una superficie brillante y un aspecto premium a las cubiertas de los tiradores de las puertas y al soporte de las llaves. El resultado podría describirse casi como arte, con un diseño elegante y refinado y una estructura muy intrincada que combina a la perfección la elegancia francesa, la innovación y la exclusividad premium, todo lo que DS Automobiles representa.
Se realizaron unas 10 series de producción para un total de 2.000 piezas -3 elementos en cada coche-, lo que supuso unas 2.000 horas de fabricación. Todo el proyecto se completó en pocas semanas, desde la validación del diseño por el equipo de diseño de DS hasta la entrega de las piezas finales.
DS Automobiles fue capaz de crear algo único en el sector de la automoción yendo más allá de los límites de la fabricación tradicional, permitiendo que el DS 3 Dark Side destacara sobre su competencia. El equipo de diseño de DS fue capaz de gestionar un proyecto complejo en muy poco tiempo gracias a la experiencia aportada por Spartacus3D y a las capacidades de las soluciones de fabricación aditiva EOS.

Resumen de los resultados
- Rentabilidad: producción de 200 piezas por trabajo de fabricación sin merma de la calidad
- Precisión: mejoras en los parámetros del proceso para evitar la distorsión de la cubierta de la manilla de la puerta de 30 cm de longitud y poco grosor durante la construcción en posición vertical.
- Rapidez: menos de una hora de producción por pieza
- Libertad de diseño: la intrincada malla tridimensional de titanio cumple los requisitos de innovación y exclusividad de DS Automobiles.
Casos de éxito de EOS
Explore tres décadas de excelencia pionera en impresión 3D con EOS