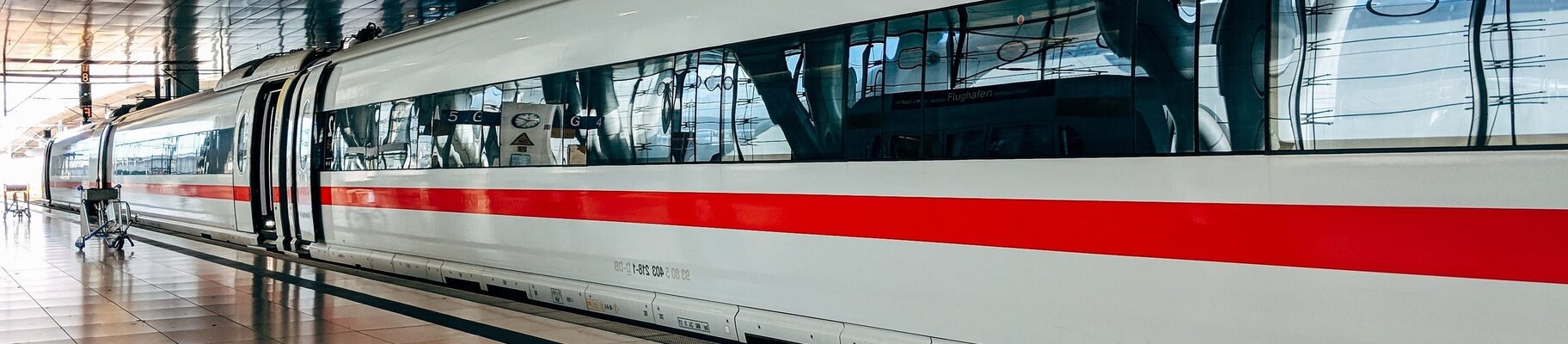
La vía rápida para obtener piezas de tren personalizadas impresas en 3D con la fabricación aditiva de EOS
Historia de éxito de Hasenauer & Hesser
Deutsche Bahn elige la fabricación aditiva para el mantenimiento de sus trenes
La flota de trenes ICE de tercera generación de Deutsche Bahn cuenta con algo menos de 160 unidades de distintas series. Todos y cada uno de ellos siguen pareciendo modernos, gracias a su elegante diseño y a la renovación periódica de sus interiores. A pesar de ello, la industria del transporte considera que todo lo fabricado antes de 1996 es un "youngtimer". Al igual que ocurre con los automóviles de esta época, encontrar piezas de repuesto para estos trenes puede resultar complicado. Sin embargo, Deutsche Bahn no se deja intimidar y cuenta con la tecnología de impresión industrial en 3D de EOS.

"La enorme ventaja de la fabricación aditiva es que siempre podemos fabricar piezas de repuesto que sean tan buenas como nuevas, lo que nos permite mantener nuestros trenes en buen estado durante décadas. No tenemos que renunciar a la calidad ni al rendimiento. El coste también es inferior al de los moldes a medida".
Florens Lichte | Director de impresión 3D | DB Fahrzeuginstandhaltung GmbH
Desafío
Los trenes ICE de tercera generación son un tanto desalentadores. Con un peso en vacío que oscila entre 270 y más de 400 toneladas y una velocidad de entre 140 y 190 millas por hora, es fácil pasar por alto la enorme variedad de componentes a bordo de cada tren. Los componentes más pequeños suelen ser los más difíciles. Mientras que los tornillos comerciales estándar son fáciles de sustituir, muchos otros pequeños productos hechos a medida no pueden simplemente volver a pedirse al fabricante si se desgastan o fallan. Para algunas piezas, la producción se ha interrumpido; para otras, los fabricantes son insolventes. Normalmente sólo se necesitan unos pocos ejemplares de cada pieza. Los elevados costes de las herramientas y los límites mínimos de compra hacen que no resulte rentable fabricarlas con métodos convencionales.
Un lote de 160 unidades es minúsculo comparado con pedidos de tamaño industrial. En comparación, cada año se fabrican cientos de miles de vehículos de tamaño medio; incluso en el caso de los aviones, las cifras de producción anual pueden alcanzar varios miles para los modelos de corto y medio recorrido que tienen éxito.
Aunque esto demuestra sin duda la sostenibilidad de los trenes como medio de transporte, las pequeñas escalas de producción complican la logística de fabricación y almacenamiento de las piezas de recambio. Problemas similares se plantean con muchos otros componentes de fabricación especial. En el ejemplo concreto que nos ocupa, se necesitaban piezas de repuesto para unos tubos fluorescentes muy delicados que se utilizan como luces de visualización en el sistema electrónico de información a bordo de los trenes ICE-3 e ICE-T. Los monitores muestran información sobre la velocidad, la velocidad y la velocidad de los trenes. Los monitores muestran a los pasajeros información sobre la velocidad, la hora del día y la próxima estación.
Con el tiempo, el desgaste normal y la fragilidad debilitan gradualmente las piezas moldeadas por inyección de 9,4 x 0,4 x 0,3 pulgadas, por lo que es necesario sustituirlas cada 10 o 15 años. Los vehículos ferroviarios están diseñados para tener una vida útil de más de 25 años, pero no es raro que un tren permanezca en servicio entre 40 y 50 años, o incluso más en casos excepcionales. A pesar de ello, el proveedor decidió dejar de fabricar estas piezas. Se necesitan unas 40 unidades al año. La empresa de mantenimiento encargada de esta responsabilidad, la Electronikzentralwerk (EZW) de Múnich/Alemania, se embarcó en la búsqueda de alternativas o socios que pudieran tener respuestas. Esta búsqueda condujo a sus expertos en tecnología ferroviaria directamente a la fabricación aditivay las posibilidades que ofrece.

Solución
La tecnología de fabricación aditiva es la solución perfecta, dado el pequeño tamaño de los lotes. No requiere grandes trabajos preparatorios, por ejemplo para configurar las herramientas de fabricación. "Según nuestra experiencia, una solución basada en un molde de aluminio equivalente y descarga manual costaría varios miles de euros, incluso sin contar los costes de manipulación y preparación de cada pedido, ni los costes anuales de almacenamiento y mantenimiento de los moldes. Además, los moldes tardarían unos tres meses en fabricarse, y las primeras muestras requerirían otro mes más", explica Florens Lichte, responsable de impresión 3D de DB Fahrzeuginstandhaltung GmbH.
Si una empresa desea fabricar un componente de forma aditiva, no necesita adquirir sus propias impresoras 3D industriales ni desarrollar sus propios conocimientos: el modelo de negocio de los fabricantes por contrato beneficia a todos. Este fue el camino elegido por Deutsche Bahn. Su empresa de logística ha colaborado con éxito con Hasenauer & Hesser GmbH en múltiples ocasiones. Hans-Jörg Hesser, Director General de Hasenauer & Hesser GmbH, explica: "Nuestro principal objetivo era preservar la funcionalidad del componente. Para ello, hubo que rediseñar las especificaciones del componente y adaptarlas al proceso de fabricación por capas. La impresión 3D suele ser fácil, pero este proyecto exigía una enorme experiencia". El componente utilizado en los trenes ICE es largo, estrecho y de paredes finas. Por ello, se deforma con una facilidad increíble. El posicionamiento de las piezas dentro de la cámara de construcción era esencial, sobre todo porque queríamos fabricar más de 200 accesorios al mismo tiempo para este pedido".

"Tenemos más de 10 años de experiencia en fabricación aditiva y llevamos utilizando sistemas EOS desde que tenemos uso de razón. Estamos encantados con la calidad de los componentes y la fiabilidad del sistema. Nos permiten suministrar a tiempo piezas de repuesto de primera calidad a nuestros clientes."
Hans-Jörg Hesser | Director General | Hasenauer & Hesser GmbH
Resultados
Los dispositivos se fabricaron con la FORMIGA P 110. Dado que no se disponía de datos CAD en 3D ni de planos de diseño, el paso de reingeniería supuso unos gastos de cuatro dígitos inferiores. Los costes de fabricación fueron entonces inferiores en más de un 80 % a los del moldeo por inyección. El proyecto requirió un total de un mes, desde el inicio hasta la primera entrega, lo que significa que las piezas impresas en 3D estuvieron disponibles cuatro veces más rápido. Cualquier pedido posterior podía realizarse en 24 horas. Los propios empleados de EZW Múnich comprobaron in situ la forma, el ajuste y el funcionamiento de las piezas impresas. Los resultados fueron muy convincentes: los accesorios remanufacturados de forma aditiva cumplían todos y cada uno de los requisitos del cliente. "Las piezas encajaban perfectamente y no se deformaban. Ya hemos montado al menos 20 unidades", añade Florens Lichte.
Sin embargo, el Sr. Lichte y sus colegas de Alemania tenían que preocuparse de algo más que de superar las pruebas funcionales. Todos los plásticos destinados a la industria ferroviaria deben cumplir los requisitos de protección contra incendios definidos en la norma EN 45545-2 / DIN 5510-2 (para vehículos existentes). Existen diferentes conjuntos de requisitos con excepciones adicionales en algunos casos, dependiendo del tamaño de cada componente, así como de su peso, ubicación dentro del vehículo y distancia de otros componentes. El material EOS PA 2210 FR seleccionado para este proyecto tuvo que someterse a exhaustivas pruebas de fuego para garantizar que cumple los requisitos específicos de su finalidad de aplicación. Estas nuevas piezas no sólo mantienen a los pasajeros al día, sino que los mantienen seguros mientras recorren las vías a velocidades de vértigo.
Resumen de los resultados
- 75 % Reducción del tiempo de producción
- 80 % Reducción de los costes de producción
Casos de éxito de EOS
Explore tres décadas de excelencia pionera en impresión 3D con EOS