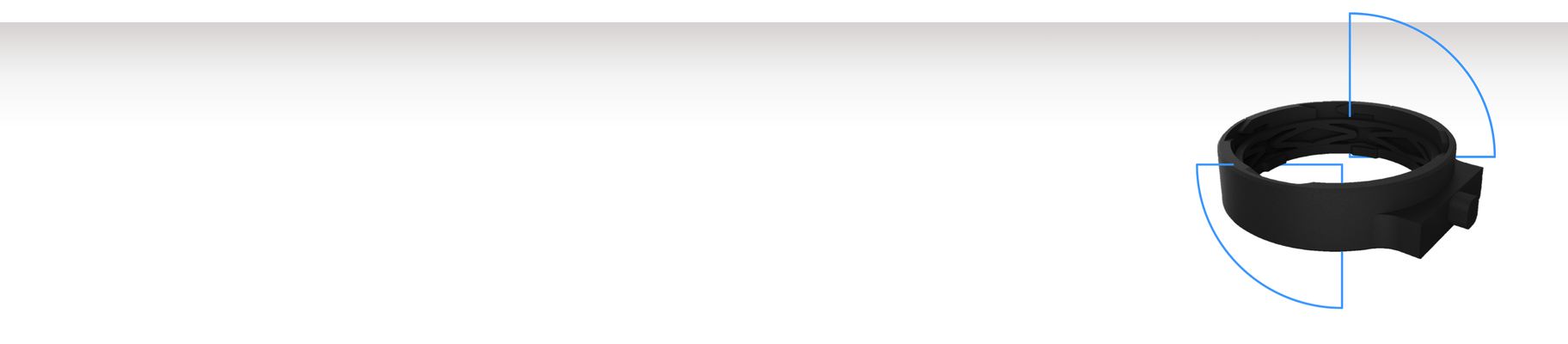
Gehäuse
Komplexes Design und flexible Produktion
Ein stabiles Gehäuse schützt das Innere. Vor allem bei empfindlicher Elektronik sind robuste Gehäuse oft unerlässlich. Sie müssen stabil, dicht und möglichst passgenau sein, und sie müssen schnell genug gefertigt werden, um kurze Produktionszyklen zu erreichen. Mit dem Spritzgussverfahren ist die Herstellung von Gehäusen mit diesen Eigenschaften jedoch nur in sehr großen Serien realisierbar.
Der industrielle 3D-Druck bietet eine kostengünstige Alternative für die Klein- und Mittelserienfertigung von Kunststoffgehäusen. Ob aus Materialien mit isolierenden oder besonders ableitfähigen Eigenschaften, die additive Fertigung von Gehäusen zeichnet sich durch Kosteneffizienz, Designfreiheit und funktionale Integrationsmöglichkeiten aus.
Ob Prototypen, Nullserien oder Kleinserien von Gehäusen, die additive Fertigung eröffnet viele Möglichkeiten - nicht zuletzt auch durch geringere Produktionskosten.
Vorteile von 3D-gedruckten Gehäusen
- Integration von Funktionen zur Reduzierung der Anzahl von Komponenten
- Verkürzte Markteinführungszeit
- Wirtschaftlich attraktiver Herstellungsprozess
- Herstellung stabiler Komponenten für die Endanwendung
3D-gedrucktes Kameragehäuse für den Außeneinsatz
Die Herausforderung bestand darin, einen robusten Kamerahalter mit komplexem Design in geringer Stückzahl herzustellen. Das Gehäuse musste flexibel genug sein, um sechs Kameras aufnehmen zu können. Gleichzeitig musste der Produktionsprozess offen sein, um spätere Design-Iterationen zu unterstützen, ohne Probleme zu verursachen.
Dank der EOS-Technologie wurde ein Produktdesign erfolgreich umgesetzt, das zuvor unmöglich gewesen wäre.
Durch die Partnerschaft mit Freedom360 konnten Designänderungen schnell vorgenommen werden. Midwest Prototyping war in der Lage, eine kostengünstige Produktion in kleinen Stückzahlen zu realisieren.
Canto
Die entwickelte Unterwasser-Tauchlampe ist kleiner, leichter und robuster als alles andere auf dem Markt. Canto ist es gelungen, diese Herausforderung mit einem FORMIGA P 110 Velocis Material PA 2200 zu lösen.
Das interne System der additiv gefertigten Lampenverbindung, das über einen Federverriegelungsmechanismus verfügt, wird in einem einzigen Stück hergestellt. Dadurch konnte die Anzahl der Montageteile von 3 auf 1 reduziert werden. Mit einem Gewicht von nur 580 Gramm setzt die Lampe neue Maßstäbe. Ein weiterer Vorteil: Die Canto Ing. GmbH die Herstellung eines teuren Spritzgusswerkzeugs erspart, das bis zu 35.000 Euro gekostet hätte.
