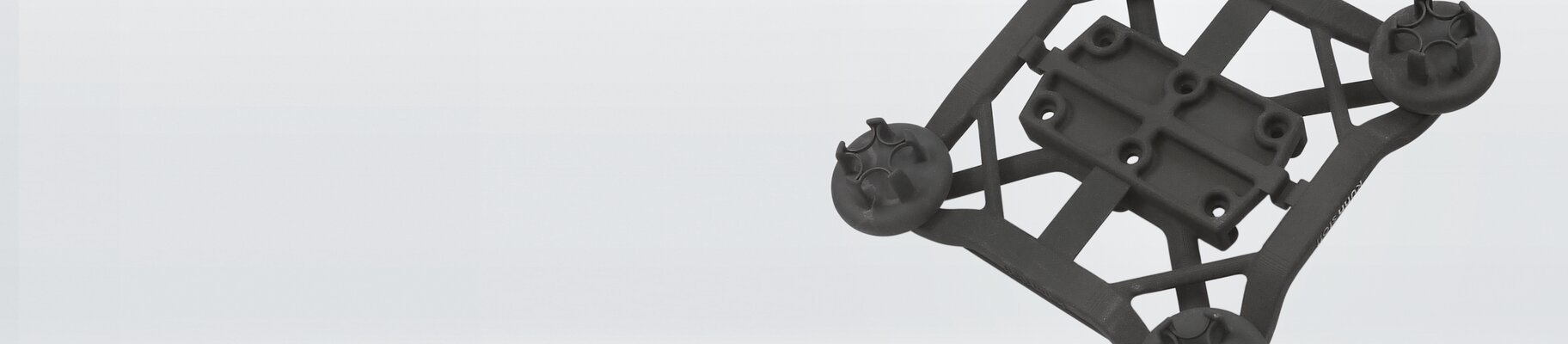
Sistema di impugnatura realizzato in modo additivo, leggero e resistente con la tecnologia EOS
Gruppo Wittmann e KuhnStoff - Studio di caso
Pinza bronchiale con piastra di base funzionale, leggera e durevole, con tecnologia EOS
La mano è una delle pietre miliari dell'evoluzione umana: con il pollice che si oppone alle altre dita, la mano umana è uno strumento ideale per afferrare, esplorare e lavorare. In quanto tale, è la chiave dell'attività culturale e del progresso tecnico. L'industria sfrutta spesso questo principio ingegnoso: uno dei processi per i quali si utilizzano le macchine è la presa automatizzata di quasi tutti i pezzi desiderati per trasportarli alla fase operativa successiva.
Tali macchine di presa sono capolavori di ingegneria. Kuhn-Stoff GmbH & Co KG si è dedicata all'ingegneria specializzata attraverso l'applicazione della tecnologia di produzione additiva EOS. Il processo prevede la formazione di parti di macchina, strato per strato, a partire da polvere di plastica che viene fusa con un raggio laser. In questo modo, Kuhn-Stoff ha sviluppato e prodotto una pinza bronchiale estremamente leggera, resistente e durevole per Wittmann Robot Systeme GmbH, a Norimberga, in Germania. Quattro di queste pinze si trovano su un telaio di supporto con condotti pneumatici integrati.

"Da anni utilizziamo parti costruite con l'Additive Manufacturing in vari settori dell'automazione. La pinza bronchiale soddisfa tutti i nostri requisiti, anzi li supera. Il pezzo è molto affidabile in termini di prestazioni quotidiane".
Michael Tolz | Responsabile tecnologia Germania e direttore di filiale | Wittmann Robot Systeme GmbH di Norimberga
Sfida
Il cliente è un produttore di robot e sistemi di automazione. A Kuhn-Stoff è stato chiesto di riprogettare una pinza meccanica che solleva, trasporta e deposita i pezzi di una macchina di produzione tramite un meccanismo pneumatico. I requisiti erano i seguenti: la pinza doveva essere più leggera del suo predecessore, pur essendo in grado di spostare i carichi richiesti. La complessità del progetto deve essere semplificata e il pezzo deve essere in grado di soddisfare i criteri di efficienza.
L'importanza del peso è dovuta alla fisica: i sistemi di presa come questo devono funzionare rapidamente per spostare il maggior numero possibile di parti di macchina in una determinata unità di tempo.
Il fatto che la massa sia inerte implica l'applicazione di una forza per metterla in movimento: più un carico è pesante e più si muove velocemente, maggiori sono le forze necessarie per l'accelerazione e la decelerazione.
A parte il punto di vista dell'efficienza energetica, questo fatto ha anche conseguenze particolarmente negative sulla durata del sistema: maggiori sono le forze in gioco, maggiore è l'usura della macchina.
La versione precedente della pinza era realizzata in alluminio, tubi di gomma e molteplici elementi di collegamento ed era costosa da produrre. Gli esperti di produzione di strati di Kuhn-Stoff si sono posti l'obiettivo di semplificare significativamente il progetto. La nuova struttura della macchina dovrebbe contribuire a una parte della riduzione di peso. Un'altra parte dovrebbe essere ottenuta attraverso l'ottimizzazione strutturale delle parti rimanenti, uno dei vantaggi principali della produzione additiva. All'inizio del lavoro è apparso subito chiaro che la nuova pinza poteva essere prodotta in un unico pezzo, senza bisogno di finiture post-produzione o di ulteriori assemblaggi.

Soluzione
Il team di Kuhn-Stoff ha iniziato esaminando la funzionalità e i requisiti di lavoro della pinza: quando l'aria compressa fluisce in una membrana flessibile, gli artigli della pinza si aprono; allo stesso modo il sistema si chiude quando l'aria compressa viene spenta. Oltre alla flessibilità della plastica, il pezzo deve essere in grado di ruotare di 90° per eseguire la sequenza di movimento necessaria. Tenendo conto di questi requisiti, è stato possibile ridurre il numero di parti necessarie a due soli componenti.
Una volta completato il processo di progettazione, Kuhn-Stoff ha iniziato a lavorare alla produzione del nuovo sistema di presa utilizzando una FORMIGA P 100. In poche ore, i due componenti sono stati realizzati in modo da poter essere utilizzati per la produzione di un sistema di presa. In poche ore i due componenti del sistema di presa sono stati prodotti in poliammide. Grazie alla tecnologia EOS, i condotti pneumatici e i connettori sono stati completamente integrati nella piastra di base.
"Come al solito, la produzione con il sistema EOS è stata fluida e senza problemi. Il risultato finale, ancora una volta, ha impressionato tutte le persone coinvolte. In un'unica fase del processo siamo stati in grado di creare un pezzo funzionalmente integrato che ha superato tutti i requisiti del cliente. In breve: la produzione additiva è ormai una realtà quotidiana, ma i risultati sono ancora straordinari", afferma Hannes Kuhn, CEO di Kuhn-Stoff GmbH.

"Utilizziamo la tecnologia EOS da oltre otto anni e abbiamo ottenuto risultati esclusivamente positivi. Se applicata correttamente, la flessibilità del design offre vantaggi significativi che possono dare ai nostri clienti vantaggi quasi impareggiabili sul mercato."
Hannes Kuhn | CEO | Kuhn-Stoff GmbH & Co KG
Risultati
Per quanto riguarda l'obiettivo principale della riduzione del peso, Kuhn-Stoff ha ottenuto una riduzione dell'86% a soli 220 g. Nonostante il peso ridotto, la pinza è ancora in grado di sopportare i carichi necessari, anche in caso di utilizzo impegnativo e continuo: dopo 5 milioni di cicli, il team ha interrotto lo stress-test, avendo raggiunto la vita utile prevista. In questo periodo non si è verificato un solo difetto o guasto. Il motivo è la resistenza della struttura, ottenuta nonostante i condotti dell'aria integrati nella piastra di base. Inoltre, il design flessibile garantisce che, in caso di piccole collisioni, queste non provochino danni al sistema di presa o all'utensile di stampaggio a iniezione. In alcuni casi, il peso ridotto consente anche di utilizzare un tipo di robot più piccolo, con una significativa riduzione dei costi. Inoltre, Wittmann è riuscita ad aumentare il numero di cicli di lavoro grazie all'altezza ridotta della pinza, che riduce l'apertura necessaria del piano di chiusura della pressa a iniezione. Il risultato finale è una riduzione dei costi operativi.
I costi di produzione sono stati ridotti del 50% rispetto al modello precedente prodotto in modo tradizionale. Ciò è dovuto al risparmio di peso e alla riduzione del numero di componenti da 21 a due. Altrettanto importante è il tempo di produzione ridotto: il sistema di impugnatura, che in precedenza richiedeva a Kuhn-Stoff dodici giorni di lavorazione, ora ne richiede solo tre.
"Siamo molto soddisfatti del nuovo sistema di presa. Ha dimostrato di essere altrettanto efficace nell'uso continuo e pesante dell'unità precedente, ma è più economico e leggero e può essere prodotto più rapidamente. Non ho mai visto un progresso così significativo nella produzione di impugnature come quello che l'Additive Manufacturing ha apportato alla produzione della nostra pinza bronchiale. Il metodo di produzione ha avuto un effetto molto positivo sulle nostre soluzioni di automazione", riassume Michael Tolz, responsabile della tecnologia e direttore di filiale di Wittmann Robot Systeme GmbH. A volte la rivoluzione può avere i suoi vantaggi rispetto all'evoluzione.
I risultati in sintesi
-
-1350 grammi: Riduzione del peso dell'86%.
-
-50 % Costi: Riduzione dei costi di produzione del 50%.
-
-19 Componenti: Riduzione dei singoli componenti da 21 a 2

Casi di studio EOS
Esplorate tre decenni di eccellenza pionieristica nella stampa 3D con EOS