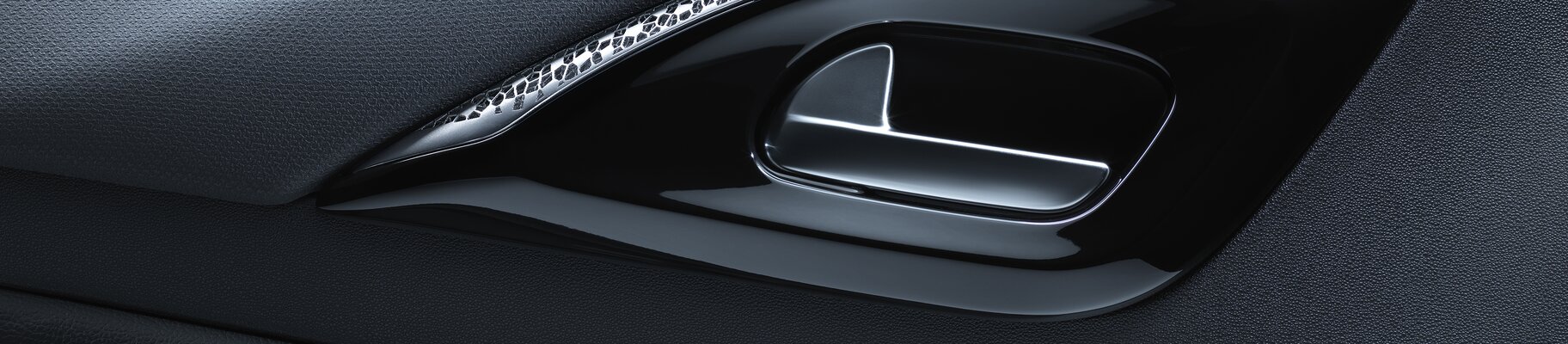
Produzione additiva per accessori auto personalizzati
Spartacus3D | Storia di successo
DS 3 Dark Side Limited Edition - Innovazione avanzata attraverso la produzione additiva
Nel settore automobilistico, le edizioni limitate di modelli di successo sono una mossa di marketing intelligente. Ma le case automobilistiche sono sempre alla ricerca di modi specifici per distinguersi dalla concorrenza nei rispettivi segmenti di mercato. DS Automobiles, un marchio del Gruppo PSA, è riuscito ad affermarsi nel segmento premium in pochi anni grazie a una serie di modelli iconici. Il modello compatto DS 3 ha ottenuto un ampio riconoscimento in questo segmento, con la presentazione regolare di modelli in edizione limitata. Per l'edizione Dark Side, DS Automobile ha voluto spingersi oltre i soliti equipaggiamenti, includendo parti stampate in 3D per sottolineare la sua continua dedizione all'innovazione. La produzione additiva ha dato piena libertà creativa al team di progettazione di DS, oltre a un'implementazione e una produzione molto rapide e semplici grazie agli esperti di Spartacus3D che lavorano con una macchinaEOS M 290 .
"È stato un progetto straordinario dall'inizio alla fine, tanto emozionante quanto impegnativo per le nostre competenze. Siamo entusiasti di immaginare che tutte queste auto siano ora in giro per il mondo. E durante tutto questo progetto, sapevamo di poter contare sull'affidabilità, la qualità e il supporto di EOS".
Charles de Forges | Amministratore delegato | Spartacus3D

Sfida
Produrre accessori di alta qualità per le auto DS 3 in edizione limitata, con un design unico e un rapido time-to-market
Il progetto è iniziato quando il team di DS Design ha iniziato a cercare miglioramenti innovativi per gli interni della DS 3 in edizione limitata. Gli accessori dovevano evidenziare la costante ricerca di innovazione della casa automobilistica e soddisfare i più alti standard di qualità richiesti dal segmento premium. Fin dall'inizio, i designer hanno deciso di sfruttare il potenziale della produzione additiva per presentare una prima mondiale in questo campo. La produzione additiva apre nuove possibilità di progettazione;
DS Automobiles presenta ogni anno diverse edizioni limitate per la DS 3, quindi queste nuove opzioni rappresentano una vera e propria svolta per il team. Il team di progettazione ha scelto anche il titanio, un materiale che conferisce un tocco di lusso, è resistente e consente una finitura facile e di bell'aspetto.
Ma mentre la stampa 3D è comunemente utilizzata nel settore automobilistico per la prototipazione, la produzione in serie con la fabbricazione additiva è ancora molto rara, soprattutto per le parti in metallo. Pertanto, DS Automobiles ha dovuto trovare un partner con esperienza nella produzione additiva e con una capacità produttiva sufficiente a soddisfare i suoi requisiti di volume. L'obiettivo era quello di consegnare circa 700 vetture sui mercati di tutto il mondo. Il progetto prevedeva inoltre tempi di sviluppo limitati, in modo da coincidere con la pianificazione della produzione dell'auto, con obiettivi molto precisi in termini di go-to-market.
Ogni edizione limitata ha un obiettivo di prezzo specifico, quindi tutti i pezzi prodotti in modo additivo devono rientrare nel budget complessivo. La fase di indagine ha portato alla scelta di due componenti: la maniglia della porta e il portachiavi.
Spartacus3D, una filiale del gruppo francese di trasformazione dei materiali Farinia, ha soddisfatto tutti questi requisiti: avendo utilizzato la stampa 3D per anni, l'azienda ha una conoscenza molto approfondita della produzione additiva che l'ha aiutata a tradurre in produzione i progetti forniti dal team DS. Con la sua macchina EOS M 290 e la EOS Titanium Ti64, Spartacus3D possedeva tutte le competenze necessarie per soddisfare i requisiti di progettazione e qualità a cui DS Automobiles puntava, nonché le capacità di produzione e post-trattamento richieste per consegnare il progetto in tempo.
Soluzione
Produzione in serie dei componenti su un EOS M 290 in EOS Titanium Ti64
Il team di progettazione DS ha utilizzato un innovativo design parametrico per creare i coperchi delle maniglie interne delle porte e il dettaglio del portachiavi elettronico in una intricata maglia di titanio, evidenziando l'innovazione e la dedizione alla qualità di DS Automobiles.
Per trovare il miglior compromesso tra qualità, costi e design, sono state necessarie molte iterazioni tra il team di progettazione DS e Spartacus3D. Ciò ha comportato la realizzazione di diversi prototipi, cosa che la produzione additiva rende particolarmente facile da realizzare in un unico lotto di produzione.
Nell'ambito di questo processo, il team di progettazione DS ha scelto anche la finitura dei pezzi, optando per un'attraente finitura opaca ottenuta mediante lucidatura manuale. Il team di qualità ha definito criteri di accettazione precisi per la distorsione, la qualità della superficie (ad esempio, porosità e lucentezza) e i bordi di taglio. Parallelamente a questo tira e molla, Spartacus3D ha lavorato anche all'ottimizzazione della produzione dei pezzi; per ridurre i costi, Spartacus3D non solo doveva determinare l'orientamento e la struttura di supporto migliori, ma anche perfezionare la strategia di fusione laser proprietaria. Il titanio è noto per generare alcune tensioni residue durante il processo di fusione e il coperchio della maniglia della porta, lungo e sottile, era un buon candidato alla massima distorsione. L'aggiunta di un trattamento termico di alleggerimento delle tensioni non era conveniente dal punto di vista dei costi; al contrario, sono stati utilizzati alcuni parametri specifici per evitare questo rischio. Altri modi per ridurre i costi sono l'aumento dei pezzi per lotto o la riduzione del numero di supporti, del consumo di polvere, del tempo di post-trattamento, ecc.

L'esperienza di Spartacus3D nella produzione additiva è stata preziosa in ogni fase del processo, dall'ingegnerizzazione del progetto all'ottimizzazione della stampa 3D, con il risultato di ridurre i cicli di vita dello sviluppo del prodotto e accelerare il time-to-market. La selezione del materiale ottimale ha contribuito ad assicurare la rigidità e a garantire la massima qualità dei pezzi dopo la post-elaborazione. "Essere scelti come partner di DS Automobiles per questo progetto così innovativo è un privilegio. Il loro marchio rappresenta fedelmente da anni l'eleganza e il know-how dell'industria automobilistica francese. Questo significa anche che i nostri sforzi vengono premiati e dimostra che Spartacus3D è in grado di offrire soluzioni robuste per la produzione in serie. Utilizzando i sistemi DMLS che abbiamo in officina, sapevamo che saremmo stati in grado di produrre i pezzi migliori", afferma Charles de Forges, amministratore delegato di Spartacus3D.
Risultati
Grazie all'esperienza di stampa 3D di Spartacus3D, è stato possibile sviluppare una strategia di produzione additiva ottimizzata per le esigenze del team di progettazione DS. La progettazione parametrica ha sfruttato appieno il potenziale della tecnologia EOS: il design originale molto complesso delle due parti ha potuto essere prodotto quasi uno a uno grazie alla produzione additiva ed è stato ottimizzato in modo da poter produrre più unità contemporaneamente. Questo ha ridotto al minimo i costi di produzione.
Il materiale, EOS Titanium Ti64, ha permesso anche una rifinitura in post-produzione, conferendo una superficie lucida e un aspetto premium ai coperchi delle maniglie delle porte e al portachiavi. Il risultato potrebbe quasi essere descritto come arte, con un design elegante e raffinato e una struttura molto intricata che combina perfettamente l'eleganza francese, l'innovazione e l'esclusività premium, tutto ciò che DS Automobiles rappresenta.
Ci sono state circa 10 serie di produzione per un totale di 2.000 pezzi - 3 elementi per ogni auto - che hanno richiesto circa 2.000 ore di produzione. L'intero progetto è stato completato in poche settimane, dalla convalida del progetto da parte del team di progettazione DS alla consegna dei pezzi finali.
DS Automobiles è riuscita a creare qualcosa di unico nel settore automobilistico superando i limiti della produzione tradizionale, permettendo alla DS 3 Dark Side di distinguersi dalla concorrenza. Il team di progettazione di DS è stato in grado di gestire un progetto complesso in tempi molto brevi grazie alle competenze fornite da Spartacus3D e alle capacità delle soluzioni di produzione additiva EOS.

I risultati in sintesi
- Efficienza in termini di costi: produzione di 200 pezzi per ogni lavoro di costruzione senza impatto sulla qualità
- Preciso: miglioramento dei parametri di processo per evitare la distorsione del coperchio della maniglia della porta, lungo 30 cm e sottile, durante la costruzione in posizione verticale.
- Veloce: meno di un'ora di produzione per pezzo
- Libertà di design: le intricate maglie tridimensionali in titanio soddisfano i requisiti di DS Automobiles per l'innovazione e l'esclusività premium.
Storie di successo di EOS
Esplorate tre decenni di eccellenza pionieristica nella stampa 3D con EOS