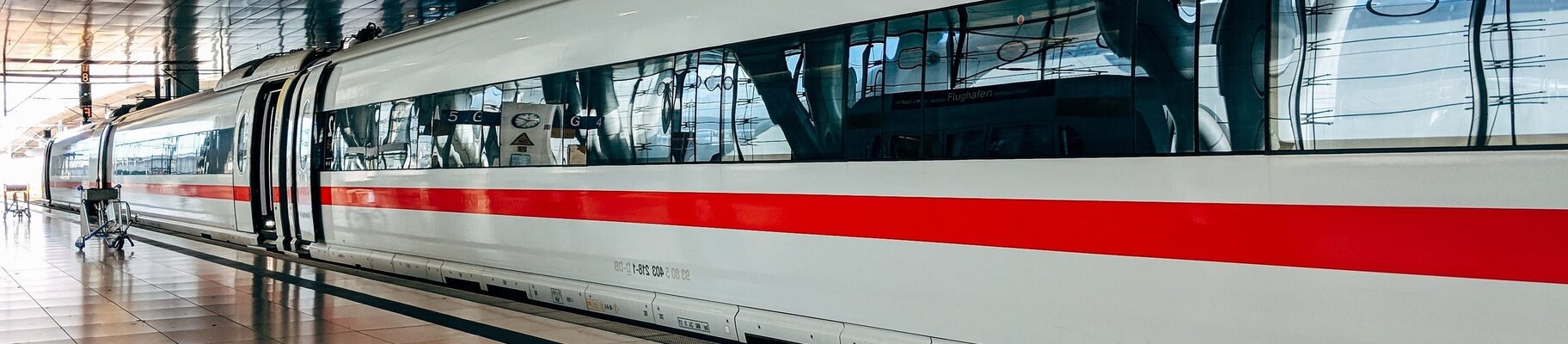
La corsia preferenziale per la stampa 3D di parti di treni personalizzati con la produzione additiva di EOS
Hasenauer & Hesser | Storia di successo
Deutsche Bahn sceglie la produzione additiva per la manutenzione dei treni
La flotta di treni ICE di terza generazione gestita da Deutsche Bahn conta poco meno di 160 unità di varie serie. Ognuno di essi ha ancora un aspetto moderno, grazie al design elegante e agli interni regolarmente rinnovati. Ciononostante, l'industria dei trasporti considera tutto ciò che è stato costruito prima del 1996 come un prodotto giovane. Come per le automobili di questo periodo, trovare pezzi di ricambio per questi treni può essere difficile. Ma la Deutsche Bahn non si lascia scoraggiare, grazie alla tecnologia di stampa 3D industriale di EOS.

"L'enorme vantaggio della produzione additiva è che possiamo sempre produrre parti di ricambio pari al nuovo, consentendoci di mantenere i nostri treni in buone condizioni per decenni. Non dobbiamo scendere a compromessi sulla qualità o sulle prestazioni. Il costo è inoltre inferiore a quello degli stampi personalizzati".
Florens Lichte | Responsabile Stampa 3D | DB Fahrzeuginstandhaltung GmbH
Sfida
I treni ICE di terza generazione sono piuttosto scoraggianti. Con un peso a vuoto che varia da 270 tonnellate a oltre 400 tonnellate e una velocità di percorrenza compresa tra 140 e 190 miglia orarie, è facile ignorare l'enorme varietà di componenti a bordo di ogni treno. I componenti più piccoli sono spesso i più difficili. Mentre le viti commerciali standard sono facili da sostituire, molti altri piccoli prodotti personalizzati non possono essere semplicemente riordinati dal produttore in caso di usura o guasto. Per alcuni pezzi la produzione è stata interrotta, per altri i produttori sono insolventi. In genere sono necessarie solo poche copie di ogni pezzo. Gli elevati costi degli utensili e i limiti minimi di acquisto rendono antieconomica la produzione con metodi convenzionali.
Un lotto di 160 unità è un'inezia rispetto agli ordini di dimensioni industriali. A titolo di paragone, ogni anno vengono prodotte centinaia di migliaia di veicoli di medie dimensioni; anche per gli aerei, i numeri di produzione annuali possono raggiungere diverse migliaia per i modelli di successo a breve e medio raggio.
Sebbene questo dimostri certamente la sostenibilità dei treni come mezzo di trasporto, le piccole scale di produzione complicano la produzione e la logistica di magazzino dei pezzi di ricambio. Problemi simili si incontrano con molti altri componenti realizzati ad hoc. Nell'esempio specifico qui considerato, erano necessarie parti di ricambio per alcuni tubi fluorescenti molto delicati per le luci di visualizzazione all'interno del sistema elettronico di informazioni di bordo dei treni ICE-3 e ICE-T. I monitor mostrano ai passeggeri informazioni sulla velocità, sull'ora del giorno e sulla stazione in arrivo.
Con il tempo, l'usura e la fragilità standard indeboliscono gradualmente le parti stampate a iniezione da 9,4 x 0,4 x 0,3 pollici, rendendo necessaria la loro sostituzione ogni 10-15 anni. I veicoli ferroviari sono progettati per avere una vita utile di oltre 25 anni, ma non è raro che un treno rimanga in servizio per 40-50 anni, o anche di più in casi eccezionali. Nonostante ciò, il fornitore ha deciso di interrompere la produzione di questi componenti. Sono necessarie circa 40 unità all'anno. La società di manutenzione a cui è stata affidata questa responsabilità, la Electronikzentralwerk (EZW) di Monaco di Baviera/Germania, ha intrapreso una ricerca di alternative o di partner che potessero avere delle risposte. Questa ricerca ha portato i loro esperti di tecnologia ferroviaria direttamente alla produzione additivae alle possibilità che essa offre.

Soluzione
La tecnologia di produzione additiva è la soluzione perfetta, viste le dimensioni ridotte dei lotti. Non richiede un lungo lavoro di preparazione, ad esempio per impostare gli strumenti di produzione. "In base alla nostra esperienza, ci aspettiamo che una soluzione basata su uno stampo di alluminio equivalente e sullo scarico manuale costi diverse migliaia di euro, anche al lordo dei costi di gestione e allestimento per ogni ordine e dei costi annuali di stoccaggio e manutenzione degli stampi. Inoltre, la realizzazione degli stampi richiederebbe circa tre mesi e i primi campioni un altro mese", spiega Florens Lichte, responsabile della stampa 3D presso DB Fahrzeuginstandhaltung GmbH.
Se un'azienda desidera produrre in modo additivo un componente, non deve acquistare le proprie stampanti 3D industriali o sviluppare le proprie competenze: il modello commerciale dei produttori a contratto è vantaggioso per tutti. Questa è la strada scelta da Deutsche Bahn. La loro società di logistica ha collaborato con successo con Hasenauer & Hesser GmbH in diverse occasioni. Ma il diavolo si nascondeva nei dettagli, rivela Hans-Jörg Hesser, amministratore delegato di Hasenauer & Hesser GmbH: "Il nostro obiettivo primario era quello di preservare la funzionalità del componente. A tal fine, le specifiche del componente dovevano essere rielaborate e adattate al processo di produzione a strati. La stampa 3D di solito è facile, ma questo progetto ha richiesto una grande esperienza. Il componente utilizzato nei treni ICE è lungo, stretto e con pareti sottili. Per questo motivo, si deforma con estrema facilità. Il posizionamento dei pezzi all'interno della camera di costruzione è stato essenziale, soprattutto perché per questo ordine volevamo realizzare oltre 200 dispositivi contemporaneamente."

"Abbiamo oltre 10 anni di esperienza nella produzione additiva e utilizziamo i sistemi EOS da sempre. Siamo entusiasti della qualità dei componenti e dell'affidabilità del sistema. Ci permettono di consegnare tempestivamente ai nostri clienti pezzi di ricambio di prima qualità".
Hans-Jörg Hesser | Amministratore delegato | Hasenauer & Hesser GmbH
Risultati
Le attrezzature sono state realizzate con la FORMIGA P 110. Poiché non erano disponibili né dati CAD 3D né disegni di progetto, la fase di reingegnerizzazione ha comportato spese a quattro cifre. I costi di produzione sono stati quindi inferiori di oltre l'80% rispetto a quelli dello stampaggio a iniezione. Il progetto ha richiesto in totale un mese, dall'inizio alla prima consegna, il che significa che i pezzi stampati in 3D sono stati disponibili quattro volte più rapidamente. Eventuali ordini successivi potrebbero essere completati entro 24 ore. I dipendenti di EZW Munich hanno testato in loco i pezzi stampati per verificarne la forma, l'adattamento e il funzionamento. I risultati sono stati molto convincenti: i dispositivi rigenerati additivamente soddisfacevano ogni singolo requisito del cliente. "I pezzi si adattavano perfettamente e non si deformavano. Abbiamo già montato almeno 20 unità", aggiunge Florens Lichte.
Tuttavia, Lichte e i suoi colleghi in Germania dovevano preoccuparsi di qualcosa di più del semplice superamento dei test funzionali. Tutte le materie plastiche destinate all'industria ferroviaria devono soddisfare i requisiti di protezione antincendio definiti dalla norma EN 45545-2 / DIN 5510-2 (per i veicoli esistenti). Esistono diverse serie di requisiti, con eccezioni aggiuntive in alcuni casi, che dipendono dalle dimensioni di ciascun componente, dal peso, dalla posizione all'interno del veicolo e dalla distanza da altri componenti. Il materiale EOS PA 2210 FR selezionato per questo progetto ha dovuto essere sottoposto a test antincendio approfonditi per garantire che soddisfi i requisiti specifici del suo scopo di applicazione. Questi nuovi componenti non solo tengono aggiornati i passeggeri, ma li proteggono anche quando sfrecciano sui binari a velocità vertiginose.
I risultati in sintesi
- 75 % Riduzione dei tempi di produzione
- 80 % Riduzione dei costi di produzione
Storie di successo di EOS
Esplorate tre decenni di eccellenza pionieristica nella stampa 3D con EOS