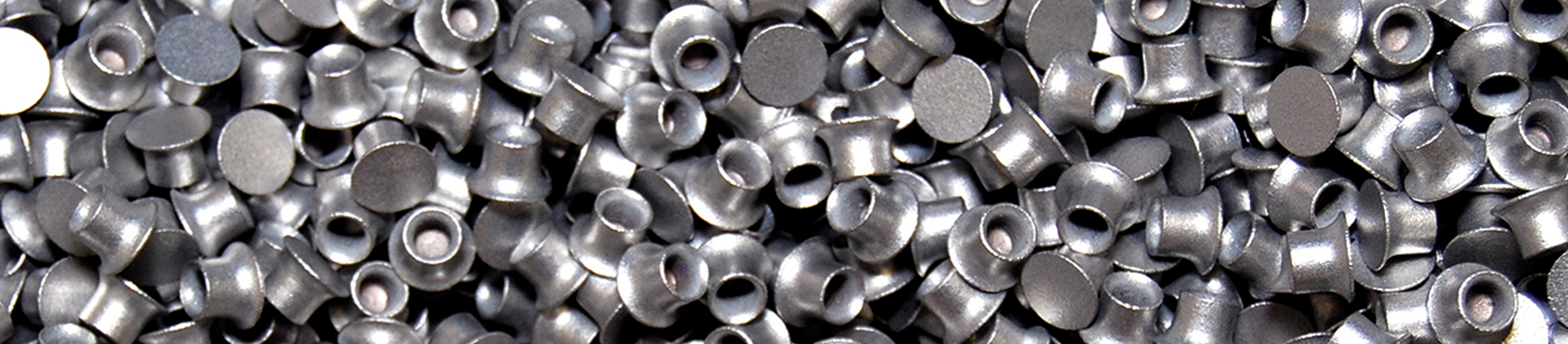
Dai colli di bottiglia alle innovazioni: Il viaggio di Atlas Copco nella stampa 3D
Studio di caso Atlas Copco
Migliorare l'efficienza della produzione
- 92% di riduzione dei tempi di consegna da 6-12 settimane a soli 3-4 giorni
- 30 % di risparmio sui costi di produzione grazie all'eliminazione delle spese per i fornitori esterni e alla riduzione delle ore di lavoro.
- Riduzione dei rifiuti di materiale da circa il 7 % a quasi zero
- Maggiore agilità nel rispondere a ordini non pianificati e a richieste urgenti dei clienti
Tempi di consegna lunghi, interruzioni della catena di fornitura e aumento dei costi di produzione sono sfide comuni nella produzione moderna. I metodi tradizionali spesso faticano a tenere il passo con la crescente domanda di flessibilità, velocità ed efficienza. Per le aziende che si affidano a componenti in outsourcing, ritardi e inefficienze possono portare a costose battute d'arresto e a opportunità perse.
Atlas Copco, leader nelle soluzioni industriali, ha affrontato proprio queste sfide con la produzione della sua bacinella per la consegna dei rivetti, un componente essenziale dei sistemi di rivettatura autoperforante utilizzati nell'industria automobilistica. Adottando la produzione additiva (AM) interna, l'azienda non solo ha superato questi ostacoli, ma ha anche ottenuto significativi risparmi sui costi, ridotto gli scarti e accorciato drasticamente i tempi di consegna. Utilizzando il EOS P 396 e il materiale polimerico PA 2200, Atlas Copco ha trasformato il suo approccio alla produzione. Questo caso di studio analizza come la produzione additiva abbia apportato miglioramenti misurabili e rimodellato la strategia di produzione.

"La collaborazione con EOS ci ha fornito una soluzione "chiavi in mano" e ci ha aiutato ad adattare i nostri processi in modo tale che ora siamo in produzione di serie con diversi componenti, stiamo rapidamente prototipando altre centinaia di componenti e abbiamo raggiunto il ROI in soli 18 mesi".
Jason Edwards, Responsabile tecnico di Atlas Copco
Sfida
Tradizionalmente, Atlas Copco si affidava a fornitori esterni per componenti come la vaschetta di erogazione dei rivetti, una parte fondamentale dei suoi sistemi di rivettatura autoperforante utilizzati ampiamente nel settore automobilistico. Questa dipendenza comportava tempi di consegna più lunghi, da 6 a 12 settimane, un aumento dei costi di produzione e complessità della catena di fornitura. Inoltre, i processi di produzione convenzionali contribuivano a produrre circa il 7% di scarti di materiale, evidenziando la necessità di una soluzione più sostenibile.
Lavorare con EOS e Additive Minds ci ha fornito una soluzione "chiavi in mano" e ci ha aiutato ad adattare i nostri processi in modo tale che ora stiamo producendo in serie diversi componenti, stiamo prototipando rapidamente altre centinaia di componenti e abbiamo raggiunto il ROI in soli 18 mesi", ha spiegato Jason Edwards, Technical Manager di Atlas Copco.
Ordinamento e alimentazione
La ciotola stampata in 3D fornisce in modo efficiente i rivetti, ottimizzando i processi di produzione automatizzati


Soluzione
Per affrontare queste sfide, Atlas Copco ha collaborato con EOS e la sua divisione di consulenza, Additive Minds, per portare le capacità AM all'interno dell'azienda. È stata scelta la stampante 3D EOS P 396 , nota per la sua flessibilità e precisione, e si è utilizzato il materiale polimerico PA 2200 per la produzione della vasca di consegna dei rivetti. Questa transizione ha permesso ad Atlas Copco di snellire la propria catena di fornitura, ridurre la dipendenza da fornitori terzi e ottenere un controllo più stretto sui programmi di produzione. L'approccio AM interno ha inoltre facilitato la prototipazione rapida, consentendo rapide iterazioni e ottimizzazioni del progetto.
Risultati
Il passaggio alla produzione additiva in-house ha prodotto risultati trasformativi per Atlas Copco. Uno dei miglioramenti più significativi è stata la drastica riduzione dei tempi di consegna. In precedenza, la produzione della ciotola per la consegna dei rivetti richiedeva dalle 6 alle 12 settimane, soprattutto a causa della dipendenza da fornitori esterni e della complessità dei processi di produzione tradizionali. Con l'implementazione della stampante 3D EOS P 396 , i tempi di consegna sono stati ridotti a soli 3 o 4 giorni, con una notevole riduzione del 92%. Questo miglioramento ha consentito una risposta più rapida alle richieste di produzione e una maggiore flessibilità nel soddisfare le richieste urgenti dei clienti.
Un altro risultato importante è stato il risparmio sui costi. Eliminando la necessità di ricorrere a fornitori esterni, riducendo le ore di lavoro e snellendo l'intero processo produttivo, Atlas Copco ha ottenuto una riduzione del 30% dei costi di produzione. L'efficienza della produzione additiva ha ridotto al minimo le spese di riattrezzaggio, di cambio di configurazione e di gestione della catena di fornitura. Inoltre, la precisione e l'affidabilità del processo AM hanno ridotto significativamente gli scarti di materiale. Mentre i metodi di produzione tradizionali producevano circa il 7% di scarti di materiale, il nuovo processo ha ridotto questa cifra quasi a zero. Questa riduzione non solo ha contribuito all'efficienza dei costi, ma ha anche sostenuto gli obiettivi di sostenibilità riducendo al minimo il consumo di risorse.
Grazie all'adozione della produzione additiva, Atlas Copco ha ottenuto una maggiore agilità di produzione, efficienza dei costi e vantaggi ambientali, dimostrando il potente potenziale della AM nelle applicazioni industriali. "L'AM è stata una trasformazione per noi. Ci stiamo aggiudicando nuovi contratti in tutto il mondo perché possiamo fornire direttamente, a costi inferiori e con tempi di consegna brevi. Con EOS abbiamo un partner che ci ha supportato durante tutta la nostra transizione, ci offre un'assistenza rapida e continua a consigliarci sulla progettazione dei componenti per ottenere i migliori risultati con la nostra stampante 3D", conclude Jason Edwards, Technical Manager di Atlas Copco.
Efficiente e affidabile
Il passaggio alla stampa 3D interna ha fatto sì che Atlas Copco abbia bisogno di meno componenti di terze parti e non sia più vincolata dai tempi di consegna della catena di fornitura e dai ritardi nei trasporti.


"La produzione additiva ci ha trasformato. Ci stiamo aggiudicando nuovi contratti in tutto il mondo perché possiamo fornire direttamente, a costi inferiori e con tempi di consegna brevi".
Jason Edwards, Responsabile tecnico di Atlas Copco
Casi di studio EOS
Esplorate tre decenni di eccellenza pionieristica nella stampa 3D con EOS