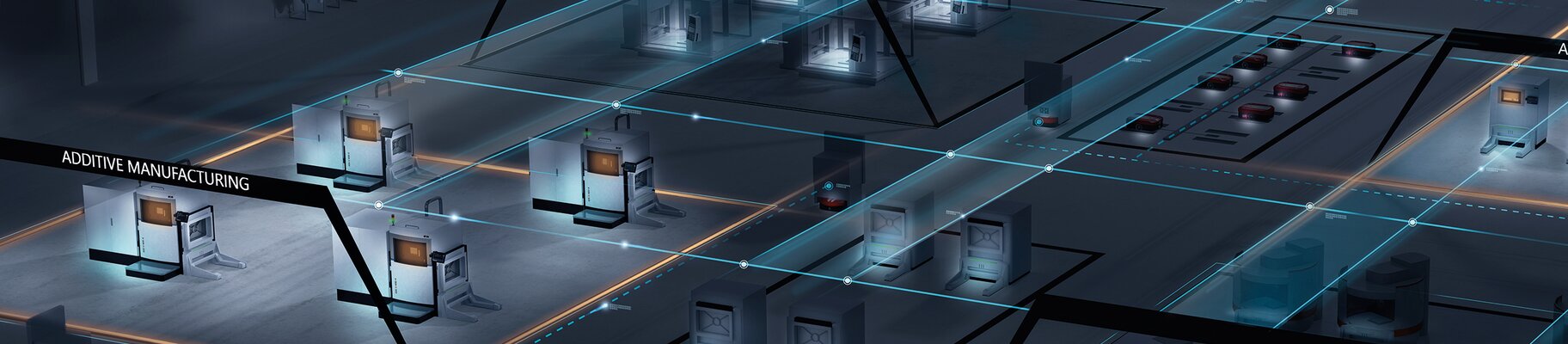
Scalare la produzione di manifattura additiva
23 agosto 2021 | Tempo di lettura: 9 min
Come aumentare e ottimizzare la produttività di una fabbrica industriale di stampa 3D con il minimo sforzo? Abbiamo utilizzato un software di simulazione per simulare il processo di produzione additiva e le fasi di post-elaborazione. Il caso d'uso del nostro cliente rende il processo di scalatura facile da seguire.
Come ottenere il massimo ritorno sugli investimenti?
Scalare la produzione di Additive Manufacturing (AM) è un compito arduo, poiché è necessario tenere conto di diversi fattori prima di decidere una strategia di scalata.
Questo articolo si rivolge a coloro che desiderano aumentare e ottimizzare la produttività della propria fabbrica AM con il minimo sforzo. Descriveremo un caso d'uso reale del cliente che renderà il processo di scalatura facile da seguire.
La sfida principale
Il cliente voleva aumentare la produzione aggiungendo tre sistemi EOS P 396 alle due macchine EOS EOS P 396 esistenti. Tuttavia, il team non era sicuro che le macchine di post-elaborazione esistenti fossero in grado di gestire la massima produttività con un turno di lavoro di un solo operatore. Il prodotto AM è rimasto lo stesso, il che significa che anche il flusso di lavoro e il tipo di attrezzatura sono rimasti gli stessi. La sfida principale consisteva nell'ottimizzare le attrezzature e le risorse di post-elaborazione aggiuntive per ottenere la massima produttività, mantenendo il costo per pezzo il più basso possibile.
Abbiamo supportato il cliente sviluppando un modello di produzione personalizzato con parametri di input variabili adeguati. Variando questi parametri di input si possono generare diversi scenari per verificare la sensibilità della produzione e del costo per pezzo. Queste informazioni guidano il cliente nella scelta dello scenario ottimizzato con il minor investimento aggiuntivo per scalare la produzione AM.
In sintesi, abbiamo identificato i colli di bottiglia della fabbrica. Apportando piccole modifiche alla post-elaborazione, abbiamo aumentato la produzione del 24%, il margine del 124%, il ritorno sull'investimento (ROI) del 115% e ridotto il costo per pezzo (CPP) del 18%.
Utilizzare la simulazione per risolvere il problema dell'ottimizzazione della produzione
Un business case di successo per la produzione in serie richiede un'analisi approfondita di tutti i parametri di produzione che influiscono sulla produzione e sui costi. Questi parametri di produzione sono spesso correlati tra loro in modo non lineare e quindi è difficile ottimizzarli utilizzando un foglio di calcolo Excel. Il software di simulazione, invece, tiene conto di tutte le complessità legate alla produzione e risolve il problema dell'ottimizzazione in modo più semplice.
Noi di EOS utilizziamo Tecnomatix Plant Simulation di Siemens e offriamo il nostro servizio per aiutare i nostri clienti a simulare soluzioni personalizzate per avere una buona comprensione del processo per una decisione di acquisto o di vendita.
Utilizziamo un software di simulazione per simulare il processo AM e le fasi di post-lavorazione. Un'azienda di successo nel settore AM deve analizzare la produttività e i costi della post-lavorazione, che a volte possono essere determinanti per il business case. La simulazione facilita l'esame della complessa catena di processo.
La simulazione dell'impianto è una simulazione a eventi discreti che esamina tutti gli eventi pianificati. Ad esempio, se un lavoro richiede 1 ora per essere elaborato, il simulatore prenderà in considerazione l'ora di inizio e l'ora di fine del lavoro. Non simulerà come viene elaborato il lavoro, ma a che ora si verifica un evento. Altri eventi pianificati sono gli orari dei turni dei lavoratori, il tempo di allestimento, il tempo di manutenzione di una macchina, ecc.
Introduzione al caso di studio
La simulazione dell'impianto è una simulazione a eventi discreti che esamina tutti gli eventi pianificati. Ad esempio, se un lavoro richiede 1 ora per essere elaborato, il simulatore prenderà in considerazione l'ora di inizio e l'ora di fine del lavoro. Non simulerà come viene elaborato il lavoro, ma a che ora si verifica un evento. Altri eventi pianificati sono gli orari dei turni dei lavoratori, il tempo di allestimento, il tempo di manutenzione di una macchina, ecc.
Stazione di disimballaggio | x1 |
Sistema di gestione delle polveri | x1 |
DyeMansion Powershot C | x1 |
DyeMansion Powershot S | x1 |
DyeMansion DM60 | x2 |
Trattamento UV | x1 |
Finitura della superficie | x2 |
Area di asciugatura | x1 |
Tabella di ispezione | x1 |
Con EOS P 396 il cliente può stampare lavori che contengono 144 pezzi. Due EOS P 396 possono produrre 426 lavori all'anno o 61.344 pezzi all'anno. Il cliente ha bisogno di produrre altri 600 lavori all'anno o 66.400 pezzi in più all'anno. Un primo calcolo mostra che per raggiungere l'obiettivo sarebbero necessari altri tre EOS P 396 , il che significa un investimento elevato per l'azienda. Pertanto, l'obiettivo della simulazione della produzione era capire se la produzione poteva essere raggiunta utilizzando la quantità di apparecchiature di post-trattamento disponibili e tenendo conto di tutte le complessità della produzione, come guasti, manutenzione e modelli di turni di lavoro.
Come abbiamo proceduto:
L'intero layout è stato suddiviso in 3 aree (vedi figura 1):
- Stampanti AM
- Gestione della polvere
- Post-elaborazione
Il cliente preferisce avere tre regioni per ridurre al minimo il rischio di contaminazione incrociata delle polveri. Abbiamo costruito prima un modello di simulazione con i due EOS P 396 esistenti e poi un secondo modello con tre EOS P 396 aggiuntivi insieme alle attrezzature sopra elencate. Il cliente utilizza un turno di un lavoratore dal lunedì al venerdì. Durante il processo di analisi, abbiamo adattato con cura tutti i tipi di variabili, come i materiali di consumo e gli operatori per l'impianto di produzione.
Una simulazione a eventi discreti può simulare tutti gli eventi che si verificano in un determinato momento. Considera l'ora di inizio e l'ora di fine, ma non considera ciò che accade nel mezzo.
Ad esempio, supponiamo che si entri nel bancomat alle 17:50 e si esca dal bancomat alle 17:53. La simulazione mostra un evento alle 17:50 e un evento alle 17:50. La simulazione mostra un evento alle 17:50, che è l'inizio dell'evento, e poi salta alle 17:53, che è la fine dell'evento. Nella simulazione di un impianto, l'orologio salta da un evento programmato a quello successivo.
Nel contesto della produzione, si tratta di un pezzo che entra in una macchina per essere lavorato e ne esce una volta terminato il processo. La lavorazione di un pezzo può comportare diverse fasi (tempo di preparazione, tempo di carico, tempo di scarico) che possono essere incluse nella simulazione. Lo studio di simulazione aiuta ad aumentare la produttività e l'utilizzo delle macchine. Può anche aiutare a determinare il numero di lavoratori, le attrezzature, le macchine e le dimensioni del magazzino per ottenere il miglior business case.
Analisi e risultati della simulazione
Ottimizzazione dell'area di AM e gestione delle polveri
Abbiamo iniziato simulando l'area AM e l'area di gestione delle polveri prima di includere le apparecchiature di post-elaborazione. Il modello di spostamento è rimasto invariato rispetto all'originale:
- Turno: 1 turno (8 ore), lunedì - venerdì
- Tempo di costruzione: 20 ore.
Una volta costruito il modello, la prima sfida è stata quella di individuare il numero ottimale di lavoratori per queste due attività. Abbiamo fatto cinque esperimenti (Exp.) e abbiamo stabilito che un lavoratore è sufficiente per queste due aree, come mostrato nella Tabella 1. Sia che abbiamo 1 o 5 operatori, la produzione rimane la stessa (1.065 lavori all'anno). Che si tratti di 1 o 5 operatori, la produttività rimane la stessa (1.065 lavori all'anno).
Numero di operatori | Lavori prodotti |
---|---|
Exp 1 1 | 1065 |
Exp 2 2 | 1065 |
Exp 3 3 | 1065 |
Exp 4 4 | 1065 |
Exp 5 5 | 1065 |
Tabella 1: Numero di operatori per l'area di gestione di AM e polveri e rispettiva produzione annuale
Successivamente, ci siamo concentrati sull'ottimizzazione del numero di cassette per il trasporto della polvere (EOS Multi-box, vedi figura 1), che consentono a un lavoratore di distribuire la polvere alle macchine EOS. In dieci iterazioni, abbiamo individuato che sette EOS Multi-box sono il numero ottimale per ottenere una produttività di 1062 lavori all'anno (vedi Tabella 2). L'aumento della produzione con più di sette Multibox non giustifica i costi aggiuntivi. Il guadagno è di soli tre lavori all'anno (da 1062 a 1065) e l'aumento dei costi, non illustrato in questo rapporto, non giustifica questo piccolo guadagno di produzione.
Numero di Multi-box | Lavori prodotti |
---|---|
Exp 01 1 | 184 |
Exp 02 2 | 367 |
Exp 03 3 | 551 |
Exp 04 4 | 732 |
Exp 05 5 | 911 |
Exp 06 6 | 983 |
Exp 07 7 | 1062 |
Exp 08 8 | 1064 |
Exp 09 9 | 1064 |
Exp 10 10 | 1065 |
Tabella 2: Numero di Multibox e rispettivi lavori
Ottimizzazione dell'area di post-elaborazione:
Dopo aver ottimizzato l'area di gestione dell'AM e delle polveri, l'area di post-trattamento è stata la sfida successiva. Si trattava di sette diverse stazioni di processo con dieci fasi:
- Pulizia dei pezzi in DyeMansion* Powershot C
- Pulizia a ultrasuoni
- Finitura della superficie
- Pulizia a ultrasuoni
- Asciugatura
- Trattamento superficiale in DyeMansion* Powershot S
- Trattamento UV
- Colorazione in DyeMansion DM60
- Trattamento superficiale in DyeMansion* Powershot S
- Trattamento UV
(*DyeMansion fa parte dell'ecosistema EOS)
Inoltre, ci sono state alcune sfide relative al flusso di lavoro del cliente. Ad esempio, le stazioni di sabbiatura (Powershot S e C) del nostro partner DyeMansion devono lavorare solo la metà dei pezzi prodotti in una build (72 pezzi su 144), in altre parole, due lotti per build. Tuttavia, per tutte le altre stazioni, come il sistema di colorazione DyeMansion DM60, la finitura delle superfici, l'asciugatura e così via, tutti i lavori devono essere lavorati, in altre parole, un lotto per costruzione.
Una volta esteso il modello originale all'area di post-elaborazione, ci siamo concentrati sulla ricerca del numero ottimale di operatori. Partendo dall'optimum AM di 1062 lavori all'anno, abbiamo eseguito cinque diverse configurazioni con 1-5 operatori. Come si vede nella Tabella 3, sarebbero necessari 4 operatori perché l'area di post-elaborazione abbia una produttività notevolmente superiore rispetto al numero precedente di lavoratori. 4 lavori in più non giustificano il costo aggiuntivo (non mostrato qui) di un operatore in più (848 contro 849 lavori).
Numero di operatori | I posti di lavoro si costruiscono con l'AM | Lavori prodotti tramite AM + Postelaborazione |
---|---|---|
Exp 1 1 | 1062 | 228 |
Exp 2 2 | 1062 | 666 |
Exp 3 3 | 1062 | 787 |
Exp 4 4 | 1062 | 848 |
Exp 5 5 | 1062 | 849 |
Tabella 3: Numero di operatori per l'area di post-elaborazione e rispettive mansioni
Conclusione
Il messaggio chiave è che scalare e ottimizzare la strategia di produzione AM può essere un compito complicato. Si tratta di una sfida unica, adattata a un layout specifico con parametri chiave diversi per ogni scenario. Non analizzare e prendere in considerazione la vostra strategia può portare a conclusioni errate. Grazie alle nostre competenze in materia di simulazione e ai 30 anni di esperienza nel settore AM, possiamo elaborare una strategia di scalatura vincente per ottenere il massimo utilizzo della macchina e il minor costo per pezzo.