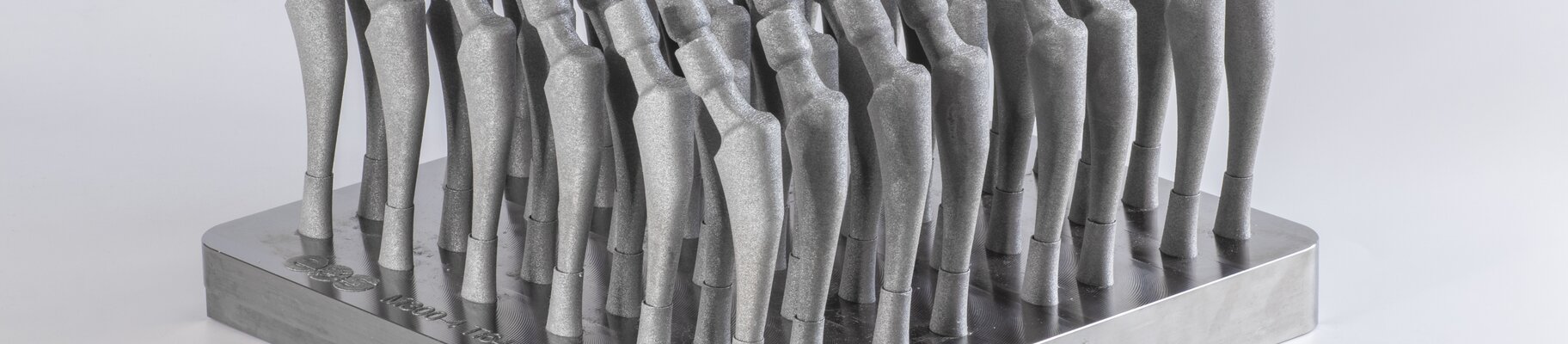
Impianti ortopedici: Nuove possibilità con la stampa 3D del metallo
30 ottobre 2020 | Tempo di lettura: 4 min
EOS ha sviluppato un processo AM di Ti64 che, combinato con il processo di trattamento termico Hot Isostatic Pressing (HIP), crea proprietà di fatica eccezionali. L'obiettivo di questo progetto era quello di evidenziare e testare queste proprietà di fatica su un impianto reale e di confrontare i risultati con gli steli d'anca Ti64 forgiati tradizionalmente.
Aprire le possibilità della produzione additiva
Le sezioni seguenti mostrano come le conoscenze, l'esperienza e i servizi offerti dalla rete EOS si siano uniti per realizzare questo salto di qualità nella produzione ortopedica additiva:
Risultati della fatica
Le prove di fatica sono state eseguite dall'OIC, Orthopedic Innovation Center, Winnipeg Canada. Gli steli dell'anca sono stati testati per le proprietà di fatica del collo secondo la norma ISO 7206-6. Hanno sopportato un carico di 5340 N per 10 milioni di cicli. In questo studio sono stati testati 2 steli per anca prodotti in modo additivo ed entrambi hanno superato un runout di 10 milioni di cicli. Ciò dimostra che le proprietà di fatica di questi impianti prodotti con AM erano almeno pari a quelle dello stelo dell'anca Ti64 forgiato tradizionalmente. È la prima volta che vengono misurate proprietà di fatica così elevate su un impianto prodotto con la fabbricazione additiva.
Preparazione alla costruzione
Per evitare la rimozione del supporto e facilitare la rimozione dell'impianto dalla piattaforma, gli steli dell'anca sono stati prodotti in un "supporto". La funzione principale di questo supporto è quella di fornire una protezione contro le forze del recoater. (Per ottenere le massime proprietà meccaniche, è stata utilizzata una lama in HSS per garantire un comportamento ottimale e costante della ricopertura). Tuttavia, non vi è alcuna connessione tra il supporto e lo stelo dell'anca, ma piuttosto uno spazio di circa 0,2 mm - 0,3 mm; l'ampiezza ideale dello spazio è stata determinata attraverso un DoE. La dimensione della fessura è un compromesso tra la facilità di rimozione e la possibilità di evitare che lo stelo dell'anca vibri a causa delle forze di ricopertura. Lo stelo dell'anca è tenuto in posizione grazie alle forze di attrito tra il supporto, la polvere e lo stelo dell'anca.
Ho tratto ispirazione per questa strategia di costruzione dal post Costruire senza supporto del mio collega Michael Wohlfart. È molto gratificante dare vita a queste idee innovative in un'applicazione reale!
Utilizzo del software per lavori additivi Amphyon
Il passo successivo è stato quello di garantire che questa idea funzionasse nella pratica. Amphyon è stato utilizzato per confermare che la strategia di impostazione non comportava alcun problema, eliminando la necessità di una strategia di costruzione "per tentativi". Una lamentela comune dei nuovi utenti AM, e anche di quelli esperti che provano nuove applicazioni, è la necessità di utilizzare una strategia "per tentativi ed errori" per le prime costruzioni.
Le simulazioni sono state eseguite per verificare l'eventuale collisione della ricopertura, per verificare che le deformazioni rientrassero nella tolleranza e per controllare le sollecitazioni termiche. Questa analisi consente di ottenere una costruzione di alta qualità prima di realizzare un singolo lavoro, riducendo i costi e i tempi di consegna.
Questo software consente la pre-deformazione dello stelo dell'anca per creare un pezzo altamente preciso direttamente dalla stampante, la prima volta. Secondo la mia esperienza, questo funziona bene, soprattutto per le deformazioni piccole e controllate previste per lo stelo dell'anca durante la stampa.
Ottenere eccellenti proprietà di fatica
Processo AM all'avanguardia
Gli steli dell'anca sono stati prodotti con il processo EOS Titanium Ti64 Grade 23 con uno spessore di 40 µm su un EOS M 290. La EOS M 290 è stata scelta per questo progetto perché è il sistema di produzione additiva industriale più qualificato sul mercato. Inoltre, l'affidabilità e la ripetibilità della macchina sono esattamente ciò che serve per ottenere grandi proprietà di fatica, dove un singolo difetto può ridurre le proprietà in modo significativo. In futuro sarebbe opportuno ottimizzare ulteriormente il processo per la produzione in serie, migliorando potenzialmente la velocità di produzione e la stabilità, dati i requisiti unici di un'applicazione per lo stelo dell'anca.
Trattamento termico HIP ottimizzato
Le eccellenti proprietà di fatica sono ottenute grazie alla combinazione di un processo AM all'avanguardia (menzionato in precedenza) con un trattamento termico ottimizzato a pressione isostatica calda (HIP). I trattamenti termici HIP convenzionali sono ottimizzati per migliorare le proprietà meccaniche della qualità e della microstruttura della colata o della fusione. La qualità di un EOS M 290 è di gran lunga superiore e pertanto EOS ha sviluppato un trattamento termico HIP che tiene conto della microstruttura unica di AM.
Il trattamento convenzionale dell'anca viene effettuato a 920 °C a 100 MPa per 2 ore ed è ampiamente diffuso in diverse industrie. Il processo sviluppato da EOS viene eseguito a 820 °C a 140 MPa per 2 ore. Questo ciclo HIP combinato con il processo DMLS di EOS produce una resistenza a fatica di 795 Mpa per 10^7 cicli (N=9).
Postelaborazione
Il post-trattamento è piuttosto semplice ed è stato eseguito da Precision ADM, Winnipeg, Canada. Il processo AM è stato impostato in modo tale da poter utilizzare le stesse fasi di post-trattamento di uno stelo per anca fabbricato in modo convenzionale. Pertanto, è stato scelto l'approccio senza supporti. La conicità è stata lavorata e il collo dello stelo dell'anca è stato lucidato per ottenere proprietà di fatica ottimali, analogamente a un dispositivo di riferimento già presente sul mercato. I risultati sono visibili a destra.
Conclusione
Il fatto che oggi sia possibile ottenere proprietà meccaniche forgiate su un'applicazione reale rappresenta un enorme passo avanti nella produzione additiva per l'ortopedia. Questo entusiasmante sviluppo ci permette di sbloccare il potenziale della produzione additiva per un altro gruppo di impianti. Spetta ora ai progettisti di dispositivi delle aziende ortopediche, e non solo, spingere i confini dell'AM e realizzare idee che si pensavano impossibili. Additive Minds non vede l'ora di lavorare insieme a voi, di sbloccare queste possibilità e di rendere possibile la prossima generazione di impianti.
Autore: Davy Orye