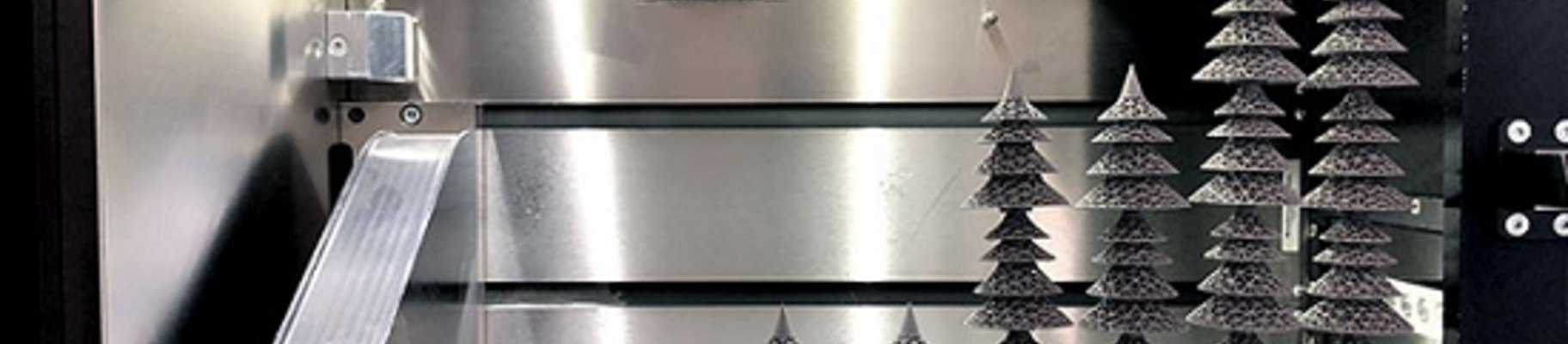
Costruire senza supporto
30 settembre 2021 | Tempo di lettura: 5 min
Costruire senza supporti o con un minimo di supporti è un tema caldo nella fusione a letto di polvere metallica. Il motivo è evidente: riduzione dei costi. Il numero di supporti influisce non solo sulla post-elaborazione, ma anche sui tempi di costruzione e sul consumo di materiale.
Una guida passo passo
Per strutturare l'articolo, utilizzerò l'approccio del Design Thinking. Vorrei innanzitutto sottolineare l'aspetto progettuale.
Enfatizzare
Definizione
Per evitare i supporti nella vostra applicazione, dovremmo chiederci quale sia il loro scopo. Le tre ragioni del supporto sono:
- Trasferimento di calore
- Sollecitazione residua
- Forze di recupero
Trasferimento di calore: A causa della ridotta conducibilità termica della polvere rispetto al materiale solido, l'apporto di energia deve essere adattato nelle aree sporgenti. Come ho mostrato nell'articolo precedente, l'argomento del trasferimento di calore può essere mitigato con una strategia di esposizione DownSkin adattata e parametri di processo ottimizzati.
Sollecitazioni residue: Poiché la fusione del letto di polvere metallica è tipicamente un processo a freddo, le tensioni residue sono il risultato delle leggi della fisica. Le sollecitazioni si verificano a causa del gradiente di temperatura dovuto all'immissione di energia concentrata localmente e alla differenza di temperatura tra gli strati appena solidificati e quelli sottostanti già raffreddati. Anche il ritiro del materiale è parzialmente limitato dal materiale precedentemente solidificato e può portare a distorsioni.
Piuttosto che intervenire sulla causa delle tensioni residue aumentando la temperatura di costruzione (con lo svantaggio di un maggiore prelievo di ossigeno) o con strategie di scansione speciali (con svantaggi sulle proprietà meccaniche o sulla produttività), è più facile compensare gli effetti derivanti. Le soluzioni sono la pre-deformazione o, se possibile, progetti meno inclini alla deformazione. Di seguito sono riportati due esempi simulati con Amphyon di Additive Works: Una piastra piatta e un cono rovesciato. Entrambi i pezzi hanno dimensioni simili (50 mm di diametro contro 50 x 50 mm). Si può notare chiaramente che il cono mostra una deformazione minore a causa della sua geometria. Inizia in un punto e poi cresce continuamente in direzione z. Anche la forma circolare negli strati x-y agisce da auto-stabilizzatore.
Forze di ricopertura: Durante la ricopertura, le forze agiscono sul pezzo mentre si sparge la polvere. Se un pezzo non è collegato alla piastra di base, verrà spazzato via dalla ricopertura. A seconda della geometria e del processo, queste forze saranno maggiori o minori. L'uso di una ricopertura morbida è un'opzione soprattutto per i pezzi in filigrana, ma solo una ricopertura dura può garantire uno spessore costante dello strato. L'esperienza insegna: Se si riesce a costruirlo con una ricopertura dura, è facile che si riesca a costruirlo con una ricopertura morbida. Per questo motivo, la seguente prova è stata eseguita con una ribattitrice dura (lama HSS).
Idea
Le soluzioni tipiche per ridurre l'effetto delle forze di ricopertura sono, ad esempio, i supporti a puntello, spesso utilizzati per le barre di trazione alte per aumentare la stabilità dei lavori di stampa riducendo le vibrazioni delle barre di trazione durante la ricopertura. Se sviluppiamo ulteriormente il concetto di supporto per puntelli, possiamo utilizzare un guscio per proteggere e stabilizzare un pezzo. In questo modo, non sarebbe necessario alcun collegamento alla piastra di base.
Per iniziare con un semplice esempio, possiamo partire dai coni. Un semplice booleano con un gioco di 0,2 mm fornirà uno spazio sufficientemente grande da impedire la fusione tra pezzo e guscio.
Prototipo
I coni sono stati costruiti su un EOS M 290 in EOS Titanium Ti64 ed erano facilmente rimovibili a mano.
Si potrebbe obiettare che il volume del guscio è maggiore del volume del pezzo. Pertanto, è necessaria un'ulteriore ottimizzazione per trovare la configurazione più vantaggiosa. All'inizio, non è necessario avvolgere l'intero pezzo, ma solo una certa area. L'attrito tra il pezzo e il guscio dovrebbe essere sufficiente a tenerlo in posizione anche per i pezzi alti. Un'altra idea è quella di impilare i pezzi e utilizzare il precedente come guscio per il pezzo successivo.
Prova
Passiamo a un progetto più avanzato e incorporiamo anche lo stacking. Visto che il Natale è alle porte, che ne dite di un albero di Natale progettato con Siemens NX e arricchito con nTopology? Capovolgendolo, l'albero è autoportante e il tronco può fungere da guscio per l'albero successivo. È possibile notare una piccola sovrapposizione di 0,1 mm in direzione x-y tra il reticolo e le parti solide per garantire una buona connessione.
Per gli esperti di nTopology: No, non ho esportato il reticolo come mesh, questo è solo per le immagini.
L'implementazione
Il mio articolo ha trattato le prime cinque fasi, da Empathize a Test, ma Additive Minds può supportarvi anche nell'implementazione. Ci sono già molti esempi che utilizzano un supporto minimo o nullo.