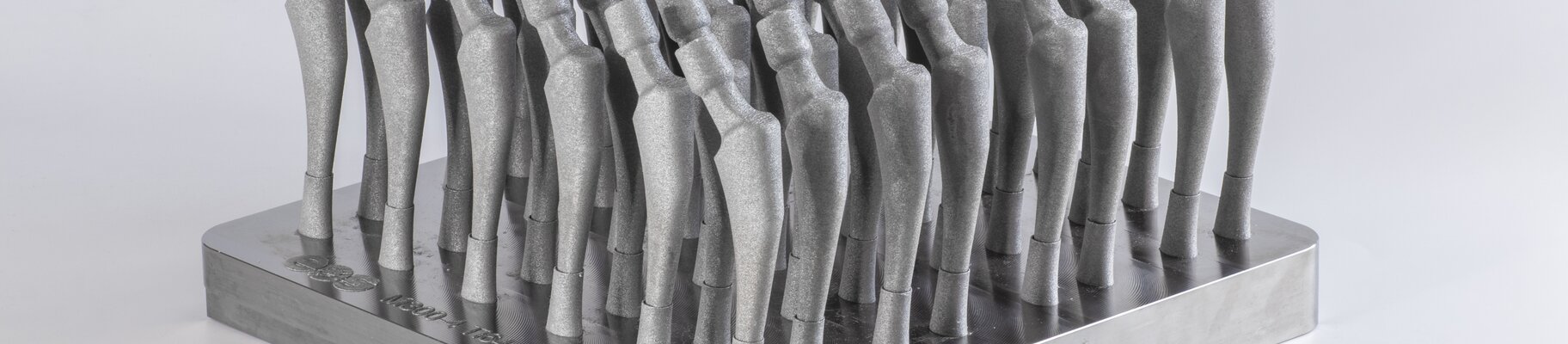
Implants orthopédiques : Nouvelles possibilités grâce à l'impression 3D de métaux
30 octobre 2020 | Temps de lecture : 4 min
EOS a mis au point un procédé Ti64 FA qui, associé à un traitement thermique par pressage isostatique à chaud (HIP), permet d'obtenir des propriétés de fatigue exceptionnelles. L'objectif de ce projet était de mettre en évidence et de tester ces propriétés de fatigue sur une conception d'implant réelle et de comparer les résultats aux tiges de hanche Ti64 forgées traditionnellement.
Ouvrir les possibilités de la fabrication additive
Les sections ci-dessous montrent comment les connaissances, l'expérience et les services offerts par le réseau EOS ont permis de réaliser ce bond en avant dans le domaine de la fabrication additive orthopédique :
Résultats de la fatigue
Les essais de fatigue ont été réalisés par l'OIC, Orthopedic Innovation Center, Winnipeg, Canada. Les tiges de hanche ont été testées sur les propriétés de fatigue du col conformément à la norme ISO 7206-6. Elles ont résisté à une charge de 5340 N pendant 10 millions de cycles. Dans cette étude, deux tiges de hanche fabriquées de manière additive ont été testées et ont toutes deux résisté à une déformation de 10 millions de cycles. Cela démontre que les propriétés de fatigue de ces implants fabriqués sur le site FA sont au moins aussi bonnes que celles de la tige de hanche Ti64 forgée traditionnelle. C'est la première fois que des propriétés de fatigue aussi élevées ont été mesurées sur un implant fabriqué par fabrication additive.
Préparation de la construction
Pour éviter de devoir retirer le support et faciliter le retrait de l'implant de la plate-forme, les tiges de hanche ont été fabriquées dans un "support". La principale fonction de ce support est d'offrir une protection contre les forces du recouvreur. (Pour obtenir les propriétés mécaniques les plus élevées, une lame HSS a été utilisée afin de garantir un comportement optimal et constant du revêtement). Cependant, il n'y a pas de connexion entre le support et la tige de la hanche, mais plutôt un espace d'environ 0,2 mm - 0,3 mm, la largeur idéale de l'espace a été déterminée par une étude de faisabilité. La taille de l'espace est un compromis entre la facilité d'enlèvement et l'empêchement de la tige de hanche de vibrer sous l'effet des forces du réapprovisionnement. La tige de hanche est maintenue en place grâce aux forces de friction entre le support, la poudre et la tige de hanche.
J'ai puisé mon inspiration pour cette stratégie de construction dans l'article Building without support de mon collègue Michael Wohlfart. Il est très gratifiant de donner vie à ces idées novatrices dans une application réelle !
Utilisation du logiciel de fabrication additive Amphyon
L'étape suivante consistait à s'assurer que cette idée fonctionnerait dans la pratique. Amphyon a été utilisé pour confirmer que la stratégie d'installation ne posait aucun problème, éliminant ainsi la nécessité d'une stratégie de construction par "essais et erreurs". Les nouveaux utilisateurs de FA , et même les utilisateurs expérimentés de FA qui essaient de nouvelles applications, se plaignent souvent de la nécessité d'utiliser une stratégie "d'essai et d'erreur" pour les premières constructions.
Des simulations ont été effectuées pour vérifier l'absence de collision avec le dispositif de recouvrement, pour s'assurer que les déformations étaient dans les limites de tolérance et pour vérifier les contraintes thermiques. Cette analyse permet d'obtenir une construction de haute qualité avant la réalisation d'un seul travail, ce qui réduit les coûts et les délais.
Ce logiciel permet de pré-déformer la tige de la hanche afin de créer une pièce très précise directement à la sortie de l'imprimante, dès la première fois. D'après mon expérience, cela fonctionne bien, en particulier pour les déformations faibles et contrôlées qui sont attendues pour la tige de la hanche pendant l'impression.
Atteindre d'excellentes propriétés de fatigue
Processus de pointe FA
Les tiges de hanche ont été fabriquées à l'aide du procédé EOS Titanium Ti64 Grade 23 en couche de 40µm d'épaisseur sur un EOS M 290 L'EOS M 290 a été choisi pour ce projet parce qu'il s'agit du système de fabrication additive industrielle le plus qualifié sur le marché. En outre, la fiabilité et la répétabilité de la machine sont exactement ce qu'il faut pour obtenir d'excellentes propriétés de résistance à la fatigue, où un seul défaut peut réduire les propriétés de manière significative. Il serait judicieux à l'avenir d'optimiser davantage le processus pour la fabrication en série, en améliorant potentiellement le taux de fabrication et la stabilité compte tenu des exigences uniques d'une application de tige de hanche.
Traitement thermique HIP optimisé
Les excellentes propriétés de fatigue sont obtenues grâce à la combinaison d'un processus de pointe ( FA ) (mentionné ci-dessus) et d'un traitement thermique optimisé par pression isostatique à chaud (HIP). Les traitements thermiques HIP conventionnels sont optimisés pour améliorer les propriétés mécaniques de la qualité et de la microstructure des pièces coulées ou semblables à des pièces coulées. La qualité d'un EOS M 290 EOS a donc développé un traitement thermique HIP qui tient compte de la microstructure unique de FA.
Le traitement conventionnel est effectué à 920 °C à 100 MPa pendant 2 heures et est largement répandu dans différentes industries. Le processus développé par EOS est effectué à 820 °C à 140 MPa pendant 2 heures. Ce cycle HIP combiné au processus DMLS d'EOS permet d'obtenir une résistance à la fatigue de 795 Mpa pour 10^7 cycles (N=9).
Post-traitement
Le post-traitement est assez simple et a été réalisé par Precision ADM, Winnipeg, Canada. Le processus FA a été conçu de manière à ce que les mêmes étapes de post-traitement qu'une tige de hanche fabriquée de manière conventionnelle puissent être utilisées. C'est pourquoi l'approche sans appui a été choisie. Le cône est usiné et le col de la tige de hanche est poli pour obtenir des propriétés de fatigue optimales, comme pour un dispositif prédicat déjà sur le marché. Les résultats sont visibles à droite.
Conclusion
Le fait qu'il soit possible d'obtenir des propriétés mécaniques forgées sur une application réelle aujourd'hui est un grand pas en avant dans la fabrication additive pour l'orthopédie. Ce développement passionnant nous permet de libérer le potentiel de la fabrication additive pour, une fois de plus, un autre groupe d'implants. Il appartient désormais aux concepteurs d'appareils des entreprises orthopédiques, et à d'autres, de repousser les limites de FA et de réaliser des idées que l'on croyait impossibles. Additive Minds se réjouit de travailler avec vous, de débloquer ces possibilités et de rendre possible la prochaine génération d'implants.
Auteur : Davy Orye