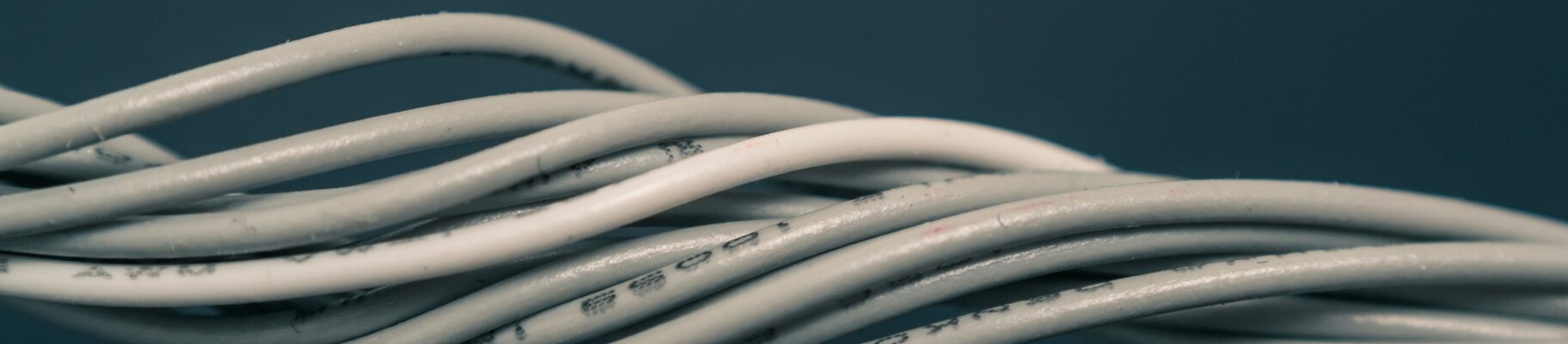
Precisión y estabilidad: El futuro de los conectores eléctricos, posible gracias a la impresión 3D FDR
WAGO | Estudio de caso
Alcanzar la excelencia
- Entrega rápida con componentes disponibles en días, no semanas
- Calidad de primera, casi indistinguible del producto final
- Eficacia racionalizada con una mínima necesidad de posprocesamiento
- La resolución detallada cumple los requisitos del
prueba de laboratorio del prototipo
Sin electricidad, casi nada funciona en nuestra sociedad y economía: los cables eléctricos de las casas, fábricas, barcos, trenes, etc. son los salvavidas de nuestro tiempo. Para que los electrones transporten su energía, deben llegar al lugar adecuado a través de cables. Para ello se necesitan componentes de conexión fiables, como los que fabrica WAGO en Westfalia Oriental. En referencia al bastión informático californiano Silicon Valley, el cluster electrónico de allí también recibe el nombre de "Terminal Valley". Y con razón, como demuestra WAGO: En el ámbito de la fabricación aditivaFA), la construcción de prototipos utiliza un proceso de alta resolución para la fabricación de prototipos de tecnología de conexión, la denominada Fine Detail Resolution (FDR). De este modo, WAGO pudo crear prototipos de las abrazaderas de resorte para un nuevo producto en la EOS FORMIGA P 110 FDR con PA 1101 de forma muy rápida y precisa - y acortar así con éxito el plazo de comercialización de una nueva caja de empalmes y distribución eléctrica.

"Los humanos necesitamos modelos. Si quieres progresar rápidamente, no hay forma de evitar la impresión industrial en 3D. Es nuestro caballo de batalla. El sinterizado selectivo por láser normal ya nos ha impresionado, pero la FDR ha subido un peldaño en términos de finura, precisión y velocidad...".."
Olaf Zoschke | Jefe de construcción de prototipos WAGO GmbH & Co. KG
Desafío
Conectar dos conductores eléctricos puede parecer sencillo a primera vista, pero en detalle exige grandes dosis de innovación, funcionalidad, seguridad y calidad. Donde fluye la electricidad, hay normas justas y precisas. Las conexiones deben cumplir requisitos de seguridad prácticos, fácticos y legales: "Un cable no debe salirse del punto de contacto, ni siquiera bajo carga", explica Olaf Zoschke, Director de Construcción de Prototipos de WAGO GmbH & Co. KG. "Además, el contorno de contacto debe tener la calidad adecuada. Si esto no estuviera garantizado, podrían producirse daños personales y materiales". Dirige la construcción de prototipos en WAGO: con su equipo de siete miembros, crea prototipos de diseño y funcionales, así como muestras de prueba que deben superar pruebas funcionales y de seguridad en laboratorios internos y externos; ningún producto nuevo puede venderse antes.
En consecuencia, las pruebas de seguridad de los productos desarrollados por WAGO y sus compañeros de mercado son extensas y frecuentes. Hay que superar varios retos: Ya sea en la estación de contadores de la casa o en el armario de distribución del vagón, el espacio para las distribuciones eléctricas es cada vez menor. Al mismo tiempo, cada vez se dispone de menos tiempo para desarrollar, probar y sacar al mercado los productos correspondientes. "Para ser rápido, no se puede eludir la fabricación aditiva", resume Olaf Zoschke. Además, las muestras deben corresponder lo más fielmente posible al producto final de serie, porque no sólo deben convencer a los ingenieros de pruebas, sino también a los minoristas especializados y otros compradores.
El diseño de la descarga de tracción del cable resultó ser un reto especial en el desarrollo de una nueva caja de empalmes con el menor espacio de instalación posible: Cuando se inserta un conductor en la toma, debe encajar firmemente en su sitio. Esto se consigue mediante un mecanismo de sujeción. Éste se bloquea mediante un engranaje de enclavamiento. Cualquier fuerza de tracción sobre el conductor debe ser absorbida por esta fijación en su aislamiento. El contacto en sí no debe sufrir esfuerzos. Para cumplir los requisitos de tamaño, los engranajes aplicados a las lengüetas también deben ser lo más pequeños posible. Al mismo tiempo, se requiere un alto grado de estabilidad para cumplir las normas de seguridad pertinentes. En la producción en serie, este catálogo de requisitos puede aplicarse porque los costes de los procesos tradicionales pueden repartirse entre grandes cantidades. ¿Pero en la construcción de prototipos?
Preciso y rápido
La impresión 3D permitió a WAGO desarrollar en muy poco tiempo una caja de empalmes totalmente funcional hasta su madurez comercial.


Solución
"Naturalmente, cambiamos el componente durante el proceso de desarrollo en el curso de las pruebas iniciales y las optimizaciones. Se sabe que la fabricación aditiva tiene aquí una ventaja. Pero, sobre todo, necesitamos determinados tamaños de lote para las pruebas funcionales y de laboratorio. Hablamos de diez a 50 piezas, que por supuesto deben ser absolutamente equivalentes entre sí. La alta precisión necesaria para los engranajes finos, por ejemplo, no era posible hasta hace poco", explica Olaf Zoschke. Sólo la FDR ha hecho posible incorporar las ventajas de la impresión 3D industrial a aplicaciones con componentes muy filigranados.
En este punto, el proceso de fabricación aditiva con resolución de detalles finos con ayuda de la FORMIGA P 110 FDR es la elección perfecta: Debido a que los componentes son muy pequeños, sólo se necesita una pequeña cámara de construcción para producir las cantidades necesarias en una sola pasada. De este modo, también se consigue una "sincronización perfecta" con las demás piezas de los prototipos. En función de los requisitos, éstas se fabrican mediante otros procesos, incluido el sinterizado selectivo por láser (SLS), más grueso. "Para la pieza 1, por ejemplo, basta con el SLS convencional; para la pieza 2, más pequeña, utilizamos el FDR. El SLS es más rápido que la impresión 3D de alta resolución, pero, debido al tamaño de las piezas, obtenemos las muestras en aproximadamente el mismo tiempo", explica vivamente Olaf Zoschke.
El equipo de creación de prototipos determina de antemano qué proceso se va a utilizar en cada caso: La decisión al respecto, al igual que la relativa al material, se toma ya en la planificación CAD, en función del uso previsto posteriormente. En última instancia, la cuestión decisiva es cómo se puede suministrar de forma razonable la calidad requerida en la cantidad necesaria. De este modo, el equipo de Olaf Zoschke puede aprovechar específicamente los puntos fuertes de cada proceso y material. "La FDR es la media de oro de la precisión, la gran nitidez de los bordes y la integración funcional; la PA 1101 como material es muy adecuada para ello. Existen métodos de creación de prototipos que son incluso más precisos. Sin embargo, ahí falta, por ejemplo, la integración funcional. El SLS estándar sería más rápido, pero no es tan preciso", añade el jefe de construcción de prototipos.
Resultados
Y este medio de oro de alta resolución de los procesos de impresión 3D ha conducido al objetivo deseado: WAGO ha podido fabricar con éxito las muestras de los engranajes y las placas, en el plazo deseado, dentro de las tolerancias requeridas y en las cantidades necesarias. De este modo se ha creado un componente duradero que no tiene nada que envidiar al producto de serie posterior en cuanto a longevidad. La producción y el postprocesado sólo llevaron unos dos días; otros procedimientos requieren de una a dos semanas. Hablando de postprocesado: Debido a la alta resolución del proceso FDR para la fabricación aditiva, sólo fue necesario un pequeño trabajo posterior en el componente.
Olaf Zoschke lo confirma: "Los productos EOS siempre han ofrecido una calidad muy buena incluso sin FDR. Siempre hemos obtenido resultados impresionantes a través del postprocesado. Estos son aún mejores con Fine Detail Resolution. Conseguimos un valor extremadamente bueno para la creación de prototipos de alrededor del 80 por ciento de la calidad del componente de serie posterior. Esto también ha entusiasmado a nuestros desarrolladores de productos". Otra razón de la superioridad de la tecnología de alta resolución en SLS reside en el postprocesado: El proceso también permite suavizar químicamente las irregularidades. Esto provoca un ligero "desenfoque" y, por tanto, no es tan preciso como la producción por FDR.
De este modo, el componente WAGO también recibió las propiedades de producto necesarias para las pruebas de la muestra: Las delicadas lengüetas y sus dientes proporcionan la resistencia requerida. Al mismo tiempo, se fabrican con una calidad tan alta que encajan a la perfección y, por tanto, de forma robusta - el enganche conduce a la fuerza de sujeción del conductor requerida. Y múltiples pruebas internas y externas han demostrado que si un componente fabricado aditivamente dura, también durará en la producción en serie. Así pues, el innovador proceso FDR ha cumplido su promesa: aumentar aún más la precisión y la velocidad de la impresión 3D industrial, con una funcionalidad totalmente integrada.
Robustez y fiabilidad
La impresión 3D puede ofrecer una calidad de primera, casi indistinguible del producto final
"Los productos EOS siempre han ofrecido una calidad muy buena incluso sin FDR. Siempre hemos obtenido resultados impresionantes mediante el postprocesado. Éstos son aún mejores con Fine Detail Resolution. Conseguimos un valor extremadamente bueno para la creación de prototipos de alrededor del 80 por ciento de la calidad del componente de serie posterior. Esto también ha entusiasmado a nuestros desarrolladores de productos".
Olaf Zoschke | Jefe de construcción de prototipos WAGO GmbH & Co. KG
Casos prácticos de EOS
Explore tres décadas de excelencia pionera en impresión 3D con EOS