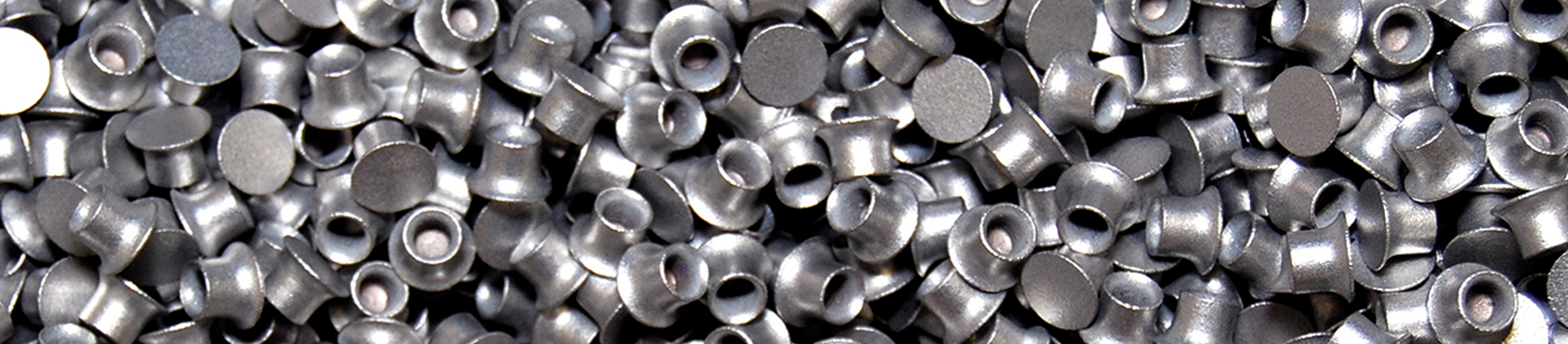
De los cuellos de botella a los avances: El viaje de Atlas Copco a la impresión 3D
Atlas Copco | Estudio de caso
Mejorar la eficiencia de la producción
- Reducción del plazo de entrega en un 92 %, de 6-12 semanas a sólo 3-4 días
- Un 30 % de ahorro en los costes de producción gracias a la eliminación de los gastos de proveedores externos y a la reducción de las horas de trabajo.
- Reducción de los residuos de material de aproximadamente un 7 % a casi cero
- Mayor agilidad para responder a pedidos imprevistos y necesidades urgentes de los clientes.
Los largos plazos de entrega, las interrupciones en la cadena de suministro y el aumento de los costes de producción son retos habituales en la fabricación moderna. Los métodos tradicionales a menudo tienen dificultades para seguir el ritmo de la creciente demanda de flexibilidad, velocidad y eficiencia. Para las empresas que dependen de componentes subcontratados, los retrasos y la ineficacia pueden provocar costosos contratiempos y oportunidades perdidas.
Atlas Copco, líder en soluciones industriales, se enfrentó a estos mismos retos con la producción de su recipiente de entrega de remaches, un componente esencial en los sistemas de remachado autoperforante utilizados en la industria del automóvil. Al adoptar la fabricación aditivaFA) interna, la empresa no solo superó estos obstáculos, sino que también consiguió importantes ahorros de costes, redujo los residuos y acortó drásticamente los plazos de entrega. Con la EOS P 396 y el material polimérico PA 2200, Atlas Copco transformó su enfoque de la producción. Este caso práctico explora cómo la fabricación aditiva aportó mejoras cuantificables y reconfiguró su estrategia de fabricación.

"Trabajar con EOS nos ha proporcionado una solución llave en mano y nos ha ayudado a adaptar nuestros procesos de tal forma que ahora estamos en producción en serie con varios componentes, estamos prototipando rápidamente cientos más y hemos logrado el retorno de la inversión en solo 18 meses."
Jason Edwards, Director técnico de Atlas Copco
Desafío
Tradicionalmente, Atlas Copco dependía de proveedores externos para componentes como el recipiente de entrega de remaches, una pieza crítica en sus sistemas de remachado autoperforante utilizados ampliamente en el sector de la automoción. Esta dependencia se traducía en plazos de entrega prolongados de 6 a 12 semanas, mayores costes de producción y complejidades en la cadena de suministro. Además, los procesos de fabricación convencionales generaban aproximadamente un 7% de residuos de material, lo que ponía de manifiesto la necesidad de una solución más sostenible.
"Trabajar con EOS y Additive Minds nos ha proporcionado una solución llave en mano, y nos ha ayudado a adaptar nuestros procesos de tal forma que ahora estamos en producción en serie con varios componentes, estamos creando rápidamente prototipos de cientos más, y hemos logrado el retorno de la inversión en sólo 18 meses", explicó Jason Edwards, Director Técnico de Atlas Copco.
Clasificar y alimentar
Un cuenco impreso en 3D suministra remaches de forma eficiente agilizando los procesos de fabricación automatizados


Solución
Para hacer frente a estos retos, Atlas Copco colaboró con EOS y su división de consultoría, Additive Minds, para incorporar internamente las capacidades FA . Seleccionaron la impresora 3D EOS P 396 , conocida por su flexibilidad y precisión, y utilizaron el material polimérico PA 2200 para fabricar la cubeta de entrega de remaches. Esta transición permitió a Atlas Copco racionalizar su cadena de suministro, reducir la dependencia de proveedores externos y obtener un control más estricto de los plazos de producción. El enfoque interno FA también facilitó la creación rápida de prototipos, permitiendo rápidas iteraciones y optimizaciones del diseño.
Resultados
El cambio a la fabricación aditiva interna produjo resultados transformadores para Atlas Copco. Una de las mejoras más significativas fue la drástica reducción de los plazos de entrega. Anteriormente, la producción de la cubeta de entrega de remaches requería de 6 a 12 semanas, debido en gran parte a la dependencia de proveedores externos y a la complejidad de los procesos de fabricación tradicionales. Con la implantación de la impresora 3D EOS P 396 , los plazos de entrega se redujeron a sólo 3 ó 4 días, una notable reducción del 92%. Esta mejora permitió una respuesta más rápida a las demandas de producción y una mayor flexibilidad para satisfacer los requisitos urgentes de los clientes.
El ahorro de costes fue otro resultado importante. Al eliminar la necesidad de proveedores externos, reducir las horas de trabajo y racionalizar todo el proceso de producción, Atlas Copco consiguió una reducción del 30% en los costes de producción. La eficiencia de la fabricación aditiva minimizó los gastos relacionados con la puesta a punto, los cambios de configuración y la gestión de la cadena de suministro. Además, la precisión y fiabilidad del proceso FA redujo significativamente el desperdicio de material. Mientras que los métodos de fabricación tradicionales generaban aproximadamente un 7 % de residuos de material, el nuevo proceso redujo esta cifra casi a cero. Esta reducción no sólo contribuyó a la rentabilidad, sino que también apoyó los objetivos de sostenibilidad al minimizar el consumo de recursos.
Gracias a la adopción de la fabricación aditiva, Atlas Copco obtuvo una mayor agilidad de producción, eficiencia de costes y beneficios medioambientales, lo que demuestra el gran potencial de la FA en aplicaciones industriales. "FA ha supuesto una transformación para nosotros. Estamos consiguiendo nuevos contratos en todo el mundo porque podemos suministrar directamente, a menor coste y con plazos de entrega más cortos. En EOS, tenemos un socio que nos ha apoyado a lo largo de nuestra transición, nos ofrece asistencia rápida y sigue asesorándonos en el diseño de componentes para conseguir el mejor resultado con nuestra impresora 3D", concluye Jason Edwards, director técnico de Atlas Copco.
Eficaz y fiable
El paso a la impresión 3D interna ha supuesto que Atlas Copco necesite menos componentes de terceros y ya no se vea limitada por los plazos de entrega de la cadena de suministro y los retrasos en el transporte.


"La fabricación aditiva ha supuesto una transformación para nosotros. Estamos consiguiendo nuevos contratos en todo el mundo porque podemos suministrar directamente, a menor coste y con plazos de entrega cortos."
Jason Edwards, Director técnico de Atlas Copco
Casos prácticos de EOS
Explore tres décadas de excelencia pionera en impresión 3D con EOS