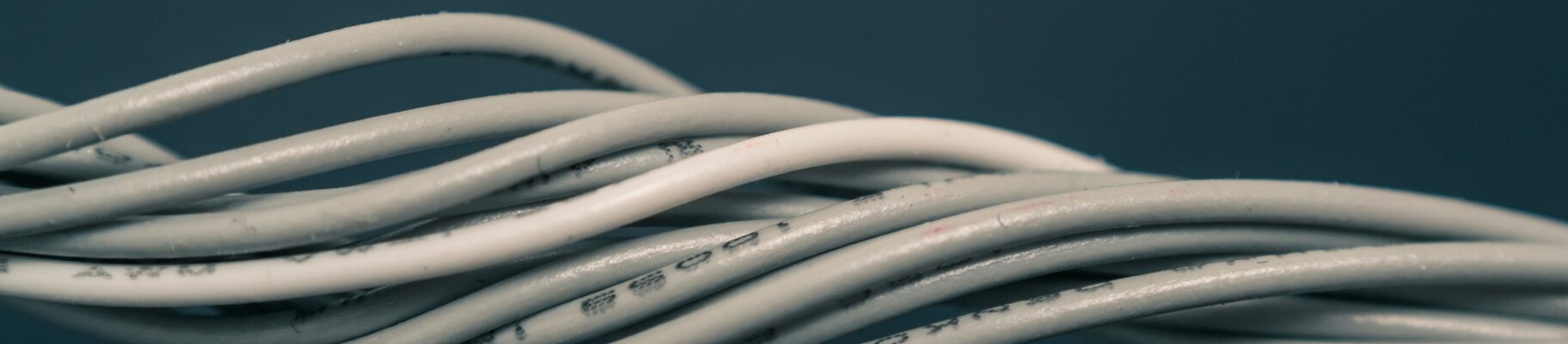
Precisione e stabilità: Il futuro dei connettori elettrici reso possibile dalla stampa 3D FDR
Studio del caso WAGO
Raggiungere l'eccellenza
- Consegna rapida con componenti disponibili in giorni, non in settimane
- Qualità di prim'ordine, quasi indistinguibile dal prodotto finale
- Efficienza ottimizzata con una post-elaborazione minima.
- La risoluzione dei dettagli soddisfa i requisiti del
test di laboratorio del prototipo
Senza elettricità non funziona quasi nulla nella nostra società ed economia: le linee elettriche nelle case, nelle fabbriche, nelle navi, nei treni, ecc. sono la linea di vita del nostro tempo. Affinché gli elettroni possano trasportare la loro energia, devono raggiungere il posto giusto attraverso i cavi. Ciò richiede componenti di connessione affidabili, come quelli prodotti da WAGO in Vestfalia orientale. In riferimento alla Silicon Valley, roccaforte californiana dell'IT, il cluster dell'elettronica è chiamato anche "Terminal Valley". E a ragione, come dimostra WAGO: Nel campo della produzione additiva (AM), la costruzione di prototipi utilizza un processo ad alta risoluzione per la produzione di prototipi con tecnologia di connessione, la cosiddetta Fine Detail Resolution (FDR). In questo modo, WAGO è stata in grado di prototipare i morsetti a molla per un nuovo prodotto sulla EOS FORMIGA P 110 FDR utilizzando la PA 1101 in modo molto rapido e preciso, riducendo così con successo i tempi di commercializzazione di una nuova scatola di giunzione e distribuzione elettrica.

"Gli esseri umani hanno bisogno di modelli. Se si vogliono fare progressi rapidi, non c'è modo di evitare la stampa 3D industriale. È il nostro cavallo di battaglia. La normale sinterizzazione laser selettiva ci ha già impressionato, ma la FDR ha fatto un salto di qualità in termini di finezza, precisione e velocità".."
Olaf Zoschke | Responsabile costruzione prototipi WAGO GmbH & Co. KG
Sfida
Il collegamento di due conduttori elettrici può sembrare semplice all'inizio, ma nel dettaglio richiede requisiti elevati in termini di innovazione, funzionalità, sicurezza e qualità. Dove c'è corrente elettrica, ci sono norme giustamente precise. Le connessioni devono soddisfare requisiti di sicurezza pratici, fattuali e legali: "Un cavo non deve semplicemente scivolare fuori dal punto di contatto, anche sotto carico", spiega Olaf Zoschke, responsabile della costruzione di prototipi di WAGO GmbH & Co. KG. "Inoltre, il contorno del contatto deve essere di qualità adeguata. Se questo non fosse garantito, potrebbero verificarsi danni a persone e cose". Zoslaf Zoschke è a capo della costruzione di prototipi presso WAGO: con il suo team di sette persone, crea prototipi di design e funzionali, nonché campioni di prova che devono superare test funzionali e di sicurezza in laboratori interni ed esterni; nessun nuovo prodotto può essere venduto prima di questo.
Di conseguenza, i test di sicurezza per i prodotti sviluppati da WAGO e dai suoi partner di mercato sono ampi e frequenti. È necessario affrontare diverse sfide: Sia che si tratti della stazione di misurazione in casa o dell'armadio di controllo nel vagone ferroviario, lo spazio per le distribuzioni elettriche diventa sempre più piccolo. Allo stesso tempo, il tempo a disposizione per sviluppare, testare e immettere sul mercato i prodotti corrispondenti è sempre meno. "Per essere veloci, non si può prescindere dalla produzione additiva", riassume Olaf Zoschke. Inoltre, i campioni devono corrispondere il più possibile al prodotto finale di serie, perché devono convincere non solo gli ingegneri addetti ai test, ma anche i rivenditori specializzati e altri acquirenti.
La progettazione del dispositivo antistrappo per cavi si è rivelata particolarmente impegnativa nello sviluppo di una nuova scatola di giunzione con il minor spazio di installazione possibile: Se un conduttore viene inserito nella presa, deve scattare saldamente in posizione. Ciò avviene tramite un meccanismo di bloccaggio. Questo si blocca in posizione grazie a un ingranaggio di interblocco. Eventuali forze di trazione sul conduttore devono essere assorbite da questo fissaggio al suo isolamento. Il contatto stesso non deve essere sollecitato. Per soddisfare i requisiti dimensionali, anche gli ingranaggi applicati alle linguette devono essere il più piccoli possibile. Allo stesso tempo, è necessario un elevato grado di stabilità per soddisfare le norme di sicurezza pertinenti. Nella produzione di serie è possibile implementare un catalogo di requisiti di questo tipo, perché i costi dei processi tradizionali possono essere distribuiti su grandi quantità. Ma nella costruzione di prototipi?
Preciso e veloce
La stampa 3D ha permesso a WAGO di sviluppare una scatola di giunzione completamente funzionale fino alla maturità del mercato in tempi molto brevi.


Soluzione
"Naturalmente cambiamo il componente durante il processo di sviluppo, nel corso dei test iniziali e delle ottimizzazioni. La produzione additiva è notoriamente un vantaggio in questo caso. Soprattutto, però, abbiamo bisogno di determinati lotti per i test funzionali e di laboratorio. Si parla di 10-50 pezzi, che ovviamente devono essere assolutamente equivalenti tra loro. L'alta precisione richiesta per gli ingranaggi di precisione, ad esempio, non era possibile fino a poco tempo fa", spiega Olaf Zoschke. Solo FDR ha permesso di incorporare i vantaggi della stampa 3D industriale in applicazioni con componenti molto filigranati.
Il processo di risoluzione dei dettagli per la produzione additiva con l'aiuto della FORMIGA P 110 FDR è la scelta perfetta a questo punto: A causa dei componenti molto piccoli, è necessaria solo una piccola camera di costruzione per produrre le quantità richieste in un unico passaggio. In questo modo si crea anche una "perfetta corrispondenza temporale" con le altre parti dei prototipi. A seconda dei requisiti, questi vengono prodotti con altri processi, tra cui la sinterizzazione laser selettiva (SLS) più grossolana. "Per la parte più grande 1, ad esempio, è sufficiente la SLS convenzionale, mentre per la parte più piccola 2 ci affidiamo alla FDR. La SLS è più veloce della stampa 3D ad alta risoluzione, ma a causa delle dimensioni dei pezzi, otteniamo i campioni in circa lo stesso tempo", spiega vivacemente Olaf Zoschke.
Il team di prototipazione stabilisce in anticipo quale processo utilizzare in ogni caso: La decisione in merito a questo e al materiale viene presa già in fase di progettazione CAD, a seconda dell'uso successivo previsto. In definitiva, la questione decisiva è come la qualità richiesta possa essere fornita in modo ragionevole nella quantità richiesta. Il team di Olaf Zoschke può così sfruttare in modo specifico i punti di forza dei singoli processi e materiali. "L'FDR è il mezzo d'oro della precisione, dell'elevata nitidezza dei bordi e dell'integrazione funzionale; il materiale PA 1101 è molto adatto a questo scopo. Esistono metodi di prototipazione ancora più precisi. Tuttavia, in questo caso manca, ad esempio, l'integrazione funzionale. La SLS standard sarebbe più veloce, ma non è altrettanto precisa", aggiunge il responsabile della costruzione dei prototipi.
Risultati
E questo mezzo d'oro ad alta risoluzione dei processi di stampa 3D ha portato all'obiettivo desiderato: WAGO è stata in grado di produrre con successo i campioni degli ingranaggi e delle piastre - nei tempi, nelle tolleranze e nelle quantità richieste. In questo modo è stato creato un componente durevole che non ha nulla da invidiare ai prodotti di serie successivi in termini di longevità. La produzione e la post-elaborazione hanno richiesto solo due giorni, mentre altre procedure richiedono da una a due settimane. A proposito di post-elaborazione: Grazie all'alta risoluzione del processo FDR per la produzione additiva, sono stati necessari solo pochi interventi sul componente.
Olaf Zoschke lo conferma: "I prodotti EOS hanno sempre fornito un'ottima qualità anche senza FDR. Abbiamo sempre ottenuto risultati impressionanti con la post-elaborazione. Con la Fine Detail Resolution sono ancora migliori. Otteniamo un valore estremamente buono per la prototipazione, pari a circa l'80% della qualità dei componenti della serie successiva. Questo ha entusiasmato anche i nostri sviluppatori di prodotti". Un'altra ragione della superiorità della tecnologia ad alta risoluzione in SLS risiede nella post-elaborazione: Il processo consente anche di smussare chimicamente le irregolarità. Questo comporta una leggera "sfocatura" e non è quindi altrettanto preciso della produzione con FDR.
In questo modo, anche il componente WAGO ha ottenuto le proprietà del prodotto necessarie per i test sui campioni: Le delicate alette e i loro denti forniscono la forza necessaria. Allo stesso tempo, sono prodotti con una qualità così elevata che si incastrano senza soluzione di continuità e quindi in modo robusto - l'aggancio porta alla necessaria forza di serraggio del conduttore. Inoltre, numerosi test interni ed esterni hanno dimostrato che se un componente prodotto in modo additivo dura, durerà anche nella produzione in serie. L'innovativo processo FDR ha quindi mantenuto la sua promessa: aumentare ulteriormente la precisione e la velocità della stampa 3D industriale, con funzionalità completamente integrate.
Robusto e affidabile
La stampa 3D è in grado di fornire una qualità di altissimo livello, quasi indistinguibile dal prodotto finale
"I prodotti EOS hanno sempre fornito un'ottima qualità anche senza FDR. Abbiamo sempre ottenuto risultati impressionanti con la post-elaborazione. Con la Fine Detail Resolution sono ancora migliori. Otteniamo un valore estremamente buono per la prototipazione, pari a circa l'80% della qualità dei componenti della serie successiva. Questo ha entusiasmato anche i nostri sviluppatori di prodotti".
Olaf Zoschke | Responsabile costruzione prototipi WAGO GmbH & Co. KG
Casi di studio EOS
Esplorate tre decenni di eccellenza pionieristica nella stampa 3D con EOS