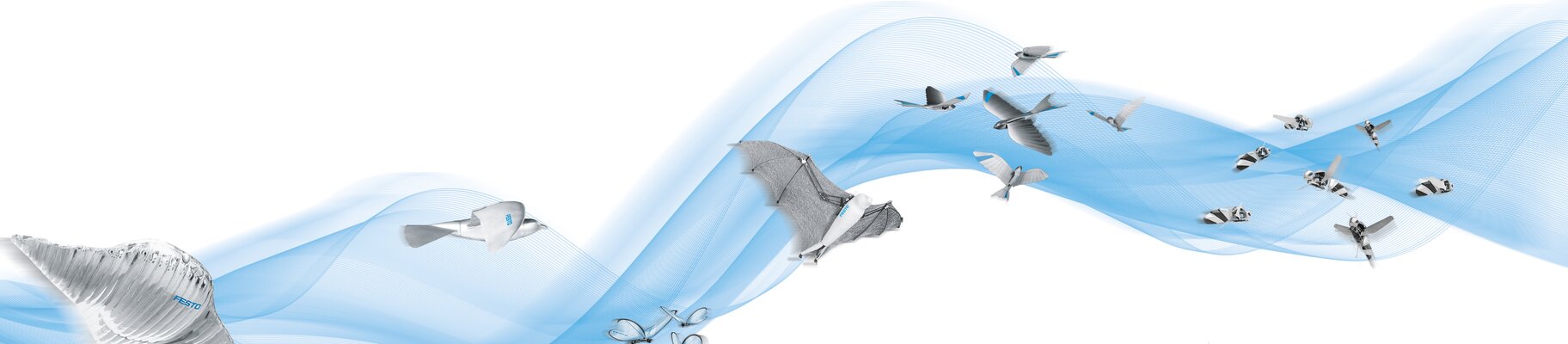
Droni ape bionici: Il futuro della tecnologia degli sciami autonomi prende il volo
Studio di caso Festo
Pionieri del volo leggero
- 75% di riduzione del peso del telaio a soli 3 grammi
- Volo di sciame autonomo di successo con 20 unità
- Rapide iterazioni di progettazione e tempi di consegna ridotti
- Ha aperto la strada a progetti leggeri più complessi in futuro
In applicazioni ad alto rischio come la ricerca e il salvataggio, le prestazioni dei droni possono fare la differenza tra successo e fallimento. Sistemi leggeri e autonomi in grado di navigare con precisione in ambienti complessi sono molto richiesti e spingono i confini dell'ingegneria e della scienza dei materiali. Ma se la risposta alla ricerca di nuove possibilità seriali non fosse affatto un tipico drone?
Ecco l'Ape bionica, un microaereo ispirato alla natura, progettato da Festo e reso possibile dalla produzione additiva (AM) all'avanguardia. Questo straordinario progetto non è solo una vetrina di biomimetica, ma una dimostrazione di come il design avanzato e la stampa 3D rivoluzionino il volo leggero. Festo ha sviluppato il concetto, mentre 1zu1 ed EOS hanno fornito le competenze e la tecnologia per trasformare un'idea ambiziosa in realtà. Il risultato: uno sciame ultraleggero e agile di api robotiche che ridefinisce le possibilità di volo autonomo.

"L'utilizzo della tecnologia FDR ha cambiato le carte in tavola per il BionicBee. Spingendo la produzione additiva ai suoi limiti, siamo riusciti a ridurre il peso del telaio da 12 a soli 3 grammi, senza compromettere la stabilità".
Mattias-Manuel Speckle | Responsabile della produzione additiva di prototipi presso Festo
Sfida
La creazione del BionicBee ha rappresentato una sfida unica. Con un'apertura alare di 240 millimetri e un peso di soli 34 grammi, l'obiettivo era progettare una struttura che bilanciasse la costruzione ultraleggera con la durata e la funzionalità. Il corpo dell'ape doveva ospitare un motore brushless, tre servomotori, una batteria, un riduttore e diverse schede elettroniche per consentire un movimento preciso delle ali. Il team di sviluppo di Festo ha adottato la tecnologia AM per ottimizzare la struttura del telaio, ma i primi prototipi hanno spesso incontrato limiti di robustezza o flessibilità. I sistemi convenzionali di sinterizzazione laser selettiva (SLS) non erano in grado di produrre le geometrie fini e intricate necessarie per il funzionamento del telaio in condizioni reali. Anche le più piccole differenze nel comportamento dei materiali o le incongruenze di produzione avrebbero potuto influire sulle prestazioni di volo. Inoltre, i tempi stretti hanno aggiunto ulteriore pressione per ottenere risultati in modo rapido ed efficiente.
Soluzione
Festo si è rivolta a 1zu1 per la produzione e 1zu1 ha scelto il sistema EOS FORMIGA P 110 FDR per fornire i componenti intricati e leggeri richiesti. Combinando l'approccio di Festo alla progettazione bionica con le capacità di alta risoluzione del FORMIGA P 110 FDR, il team ha sviluppato un telaio che bilancia efficacemente massa minima e resistenza strutturale. Questa configurazione ha anche permesso a Festo di iterare rapidamente e perfezionare la delicata struttura reticolare dell'ape, anche in tempi ristretti. Come spiega Philipp Schelling, Production Manager SLS di 1zu1, "Il BionicBee richiedeva caratteristiche estremamente fini e prestazioni costanti dei pezzi in volo. La tecnologia di fine detail resolution (FDR) di EOS con il laser CO unico nel suo genere, che ha un fascio ultrafine grande la metà rispetto ai sistemi SLS standard, era ideale per soddisfare questi requisiti e realizzare la visione di Festo."
L'uso del PA 1101 - un polimero più resistente e flessibile - ha garantito che la struttura a reticolo fosse leggera e resistente, in grado di soddisfare le rigorose esigenze del volo autonomo. Le parti in PA 1101 mostrano un'elevata resistenza agli urti e alla deformazione a rottura, mantenendo costanti le proprietà meccaniche in un ampio intervallo di temperature. Questo materiale basato su risorse rinnovabili offre prestazioni superiori rispetto al PA 12, compresa la capacità di sopportare i carichi meccanici più elevati senza scheggiarsi.
Festo ha ulteriormente ottimizzato il telaio con una modellazione guidata da algoritmi, eliminando il materiale non necessario per ottenere una drastica riduzione di peso del 75%. Il team ha anche implementato una funzione di calibrazione automatica che mette a punto i parametri di controllo di ogni BionicBee dopo un breve volo di prova, attenuando le variazioni residue nel comportamento dei materiali. "Abbiamo visto il BionicBee come la sfida perfetta per mostrare ciò che l'FDR può fare. Questo progetto evidenzia come le strutture precise e ultrasottili consentite dal sistema FORMIGA P 110 FDR possano rivoluzionare la progettazione leggera, anche per i pezzi di dimensioni maggiori", afferma Philipp Schelling, Production Manager SLS di 1zu1.
Grazie a una stretta collaborazione e a un processo di produzione agile, 1zu1 ha consegnato prototipi e componenti in tempi stretti. Questo approccio collaborativo ha permesso a Festo di assemblare e testare il telaio del BionicBee in tempo reale.
Risultati
La collaborazione tra Festo, 1zu1 ed EOS ha aperto nuove strade per la progettazione, la produzione e il funzionamento di oggetti volanti autonomi. La struttura reticolare ottimizzata ha ridotto il peso del telaio, un fattore chiave per estendere la durata del volo e migliorare la manovrabilità. "Spingendo l'AM ai suoi limiti, siamo stati in grado di ridurre il peso del nostro telaio da 12 grammi a soli 3 grammi, senza compromettere la stabilità", ha dichiarato Mattias-Manuel Speckle, responsabile del settore Additive Manufacturing Prototyping di Festo. Le capacità di volo di BionicBee sono state dimostrate da uno sciame sincronizzato di 20 unità, che ha evidenziato sistemi avanzati di localizzazione, comunicazione e controllo. Nel frattempo, l'AM ha accelerato i cicli di innovazione consentendo la prototipazione rapida e la produzione on-demand, riducendo significativamente i tempi di sviluppo. Questa collaborazione di successo è diventata un modello per i futuri sforzi di leggerezza, sottolineando l'impatto della progettazione funzionale e dell'AM ad alta risoluzione sul raggiungimento di livelli di efficienza e prestazioni senza precedenti.
Luce e Agil
Il BionicBee è il più piccolo oggetto volante della Festo Bionic Learning Network. Pesa circa 34 grammi, è lungo 22 centimetri e ha un'apertura alare di 24 centimetri.


"Abbiamo visto il BionicBee come la sfida perfetta per mostrare ciò che l'FDR può fare. Questo progetto evidenzia come le strutture precise e ultrasottili consentite dal sistema FORMIGA P 110 FDR possano rivoluzionare la progettazione leggera, anche per i pezzi di dimensioni maggiori".
Philipp Schelling | Direttore di produzione SLS presso 1zu1
Naturale e autonomo
Con il BionicBee il team di Festo ha sviluppato un oggetto volante che può volare in gran numero e in modo completamente autonomo in uno sciame.


Casi di studio EOS
Esplorate tre decenni di eccellenza pionieristica nella stampa 3D con EOS