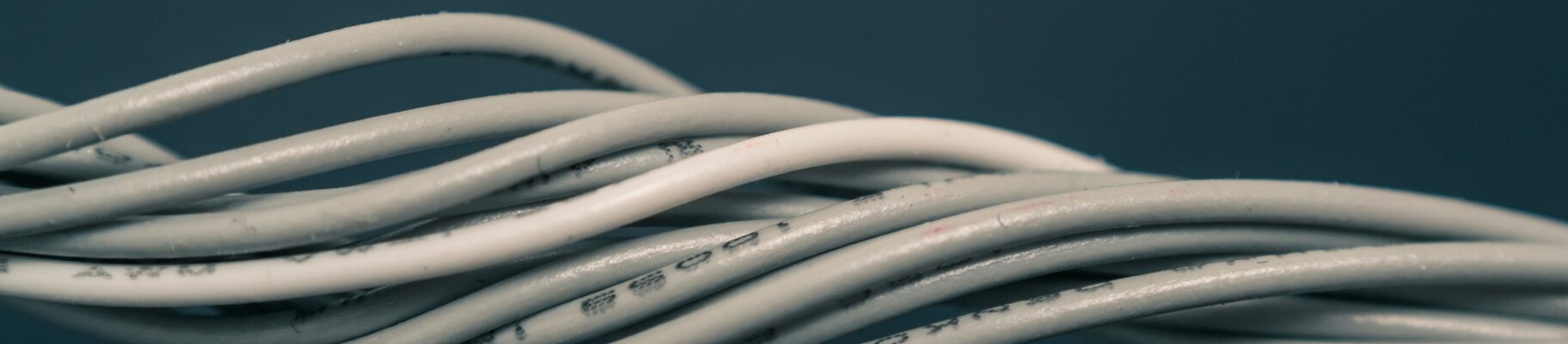
Précision et stabilité : L'avenir des connecteurs électriques grâce à l'impression 3D de FDR
WAGO | Étude de cas
Atteindre l'excellence
- Livraison rapide avec des composants disponibles en quelques jours, et non en quelques semaines
- Qualité supérieure, presque impossible à distinguer du produit final
- Efficacité rationalisée avec un minimum de post-traitement nécessaire
- La résolution des détails répond aux exigences de la
Essai en laboratoire du prototype
Sans électricité, presque rien ne fonctionne dans notre société et notre économie. Les lignes électriques dans les maisons, les usines, les bateaux, les trains, etc. sont les lignes de vie de notre époque. Pour que les électrons puissent transporter leur énergie, ils doivent arriver au bon endroit par le biais de câbles. Pour cela, il faut des composants de connexion fiables, tels que ceux fabriqués par WAGO en Westphalie orientale. En référence à la Silicon Valley, le bastion californien des technologies de l'information, le pôle électronique de cette région est également appelé "Terminal Valley". Et ce à juste titre, comme le prouve WAGO : Dans le domaine de la fabrication additiveFA, la construction de prototypes utilise un processus de haute résolution pour la fabrication de prototypes de technologie de connexion, appelé Fine Detail Resolution (FDR). WAGO a ainsi pu prototyper très rapidement et avec une grande précision les pinces à ressort d'un nouveau produit sur l'EOS FORMIGA P 110 FDR en utilisant le PA 1101 - et ainsi raccourcir avec succès le délai de mise sur le marché d'une nouvelle boîte de dérivation et de distribution électrique.

"L'homme a besoin de modèles. Si vous voulez progresser rapidement, vous ne pouvez pas faire l'économie de l'impression 3D industrielle. C'est notre cheval de bataille. Le frittage laser sélectif régulier nous a déjà impressionnés, mais le FDR l'a fait monter d'un cran en termes de finesse, de précision et de rapidité.."
Olaf Zoschke | Responsable de la construction de prototypes WAGO GmbH & Co. KG
Défi
La connexion de deux conducteurs électriques peut sembler simple à première vue, mais dans les détails, elle pose des exigences élevées en matière d'innovation, de fonction, de sécurité et de qualité. Là où l'électricité circule, il existe à juste titre des réglementations précises. Les connexions doivent répondre à des exigences pratiques, factuelles et légales en matière de sécurité : "Un câble ne doit pas glisser du point de contact, même sous charge", explique Olaf Zoschke, responsable de la construction de prototypes chez WAGO GmbH & Co. KG. "En outre, le contour du contact doit être d'une qualité appropriée. Si cela n'était pas garanti, des dommages corporels et matériels pourraient survenir." Olaf Zoschke dirige la construction de prototypes chez WAGO : avec son équipe de sept personnes, il crée des prototypes de conception et de fonctionnement ainsi que des échantillons d'essai qui doivent passer des tests de fonctionnement et de sécurité dans des laboratoires internes et externes ; aucun nouveau produit ne peut être vendu avant cela.
Par conséquent, les tests de sécurité des produits développés par WAGO et ses partenaires commerciaux sont nombreux et fréquents. Plusieurs défis doivent être relevés : Qu'il s'agisse de la station de comptage dans la maison ou de l'armoire de commande dans le wagon, l'espace pour les distributions électriques devient de plus en plus petit. Dans le même temps, il reste de moins en moins de temps pour développer, tester et commercialiser les produits correspondants. "Pour être rapide, on ne peut pas faire l'impasse sur la fabrication additive", résume Olaf Zoschke. En outre, les échantillons doivent correspondre le plus possible au produit de série final, car ils doivent non seulement convaincre les ingénieurs d'essai, mais aussi les détaillants spécialisés et les autres acheteurs.
La conception de la décharge de traction du câble s'est avérée particulièrement difficile dans le cadre du développement d'une nouvelle boîte de jonction avec un espace d'installation aussi réduit que possible : Lorsqu'un conducteur est inséré dans la prise, il doit s'enclencher fermement. Cela se fait par l'intermédiaire d'un mécanisme de serrage. Celui-ci s'enclenche par l'intermédiaire d'un engrenage d'emboîtement. Les forces de traction exercées sur le conducteur doivent être absorbées par cette fixation au niveau de l'isolation. Le contact lui-même ne doit pas être sollicité. Pour répondre aux exigences de taille, les engrenages appliqués aux languettes doivent également être aussi petits que possible. Dans le même temps, un haut degré de stabilité est requis pour respecter les règles de sécurité en vigueur. Dans la production en série, un tel catalogue d'exigences peut être mis en œuvre parce que les coûts des processus traditionnels peuvent être répartis sur de grandes quantités. Mais pour la construction de prototypes ?
Précision et rapidité
L'impression 3D a permis à WAGO de développer une boîte de jonction entièrement fonctionnelle jusqu'à la maturité du marché dans un délai très court.


Solution
"Nous modifions naturellement le composant au cours du processus de développement, lors des premiers essais et des optimisations. On sait que la fabrication additive présente un avantage à cet égard. Mais surtout, nous avons besoin de certaines tailles de lots pour les tests fonctionnels et de laboratoire. Il s'agit de 10 à 50 pièces, qui doivent bien sûr être absolument équivalentes les unes aux autres. La haute précision requise pour les engrenages fins, par exemple, n'était pas possible jusqu'à récemment", explique Olaf Zoschke. Seul FDR a permis d'intégrer les avantages de l'impression 3D industrielle dans des applications avec des composants très filigranes.
Le processus de fabrication additive à résolution fine avec la FORMIGA P 110 FDR est le choix idéal à ce stade : Les composants étant très petits, seule une petite chambre de construction est nécessaire pour produire les quantités requises en un seul passage. Cela permet également d'obtenir une " synchronisation parfaite " avec les autres pièces des prototypes. En fonction des besoins, celles-ci sont produites à l'aide d'autres procédés, notamment le frittage sélectif par laser (SLS), plus grossier. "Pour la grande pièce 1, par exemple, le SLS conventionnel est suffisant, tandis que pour la petite pièce 2, nous avons recours au FDR. Le SLS est plus rapide que l'impression 3D à haute résolution, mais en raison de la taille des pièces, nous obtenons les échantillons à peu près dans le même temps", explique Olaf Zoschke avec vivacité.
L'équipe de prototypage détermine à l'avance le processus à utiliser dans chaque cas : La décision concernant ce procédé et le matériau est déjà prise lors de la planification de la CAO - en fonction de l'utilisation prévue ultérieurement. En fin de compte, la question décisive est de savoir comment la qualité requise peut être raisonnablement fournie dans la quantité requise. L'équipe d'Olaf Zoschke peut ainsi utiliser de manière ciblée les points forts des différents processus et matériaux. "Le FDR est le juste milieu entre la précision, la netteté des arêtes et l'intégration fonctionnelle ; le PA 1101 est un matériau qui s'y prête très bien. Il existe des méthodes de prototypage qui sont encore plus précises. Cependant, l'intégration fonctionnelle fait défaut, par exemple. Le SLS standard serait plus rapide, mais il n'est pas aussi précis", ajoute le responsable de la construction de prototypes.
Résultats
Cette méthode d'impression 3D à haute résolution a permis d'atteindre l'objectif souhaité : WAGO a pu produire avec succès les échantillons d'engrenages et de plaques dans les délais, avec les tolérances et dans les quantités requises. De cette manière, un composant durable a été créé, qui n'est en aucun cas inférieur au produit de série ultérieur en termes de longévité. La production et le post-traitement n'ont pris que deux jours environ, alors que d'autres procédures nécessitent une à deux semaines. À propos de post-traitement : Grâce à la haute résolution du processus FDR pour la fabrication additive, peu de travail sur le composant a été nécessaire par la suite.
Olaf Zoschke le confirme : "Les produits EOS ont toujours fourni une très bonne qualité, même sans FDR. Nous avons toujours obtenu des résultats impressionnants par le biais du post-traitement. Ils sont encore meilleurs avec la Fine Detail Resolution. Nous obtenons un excellent rapport qualité-prix pour le prototypage d'environ 80 % de la qualité des composants des séries ultérieures. Cela a également enthousiasmé nos développeurs de produits". Une autre raison de la supériorité de la technologie haute résolution de la SLS réside dans le post-traitement : Le processus permet également de lisser chimiquement les irrégularités. Ce procédé entraîne un léger "flou" et n'est donc pas aussi précis que la production par FDR.
De cette manière, le composant WAGO a également reçu les propriétés de produit nécessaires pour les tests d'échantillons : Les ergots délicats et leur denture offrent la résistance nécessaire. En même temps, elles sont fabriquées avec une telle qualité qu'elles s'emboîtent parfaitement et sont donc robustes - l'accrochage conduit à la force de serrage nécessaire du conducteur. De plus, de nombreux tests internes et externes ont prouvé que si un composant fabriqué additivement dure, il durera également dans la production en série. Le processus innovant FDR a donc tenu sa promesse : augmenter encore la précision et la vitesse de l'impression 3D industrielle, avec des fonctionnalités entièrement intégrées.
Robuste et fiable
L'impression 3D permet d'obtenir une qualité de premier ordre, presque impossible à distinguer du produit final.
"Les produits EOS ont toujours fourni une très bonne qualité, même sans FDR. Nous avons toujours obtenu des résultats impressionnants par le biais du post-traitement. Ces résultats sont encore meilleurs avec la Fine Detail Resolution. Nous obtenons une valeur extrêmement bonne pour le prototypage d'environ 80 % de la qualité du composant de série ultérieur. Cela a également enthousiasmé nos développeurs de produits.
Olaf Zoschke | Responsable de la construction de prototypes WAGO GmbH & Co. KG
Études de cas EOS
Découvrez trois décennies d'excellence en matière d'impression 3D avec EOS