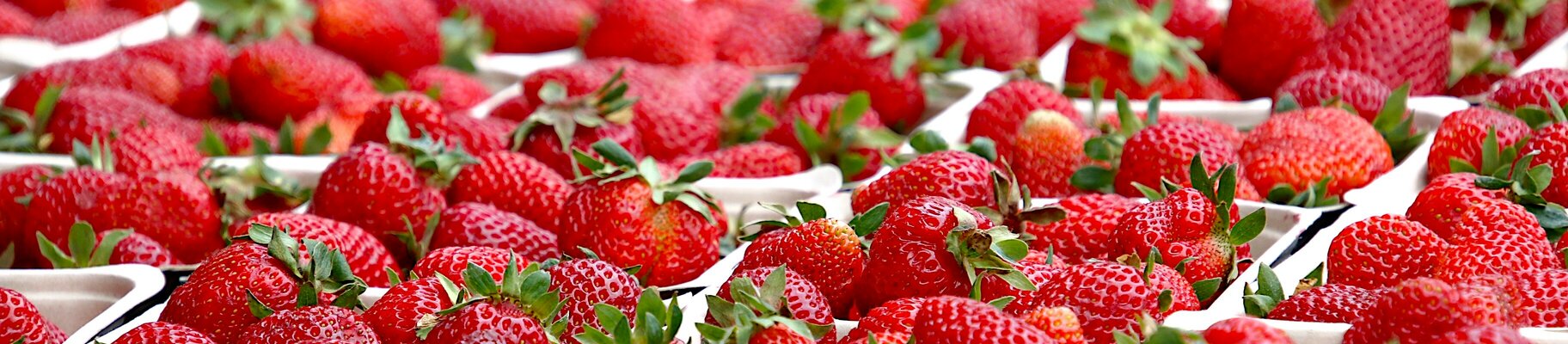
Redéfinition de la fabrication - Automatisation intelligente d'un système de remplissage imprimé en 3D
apc-tec | Étude de cas
Emballage conforme
- Réduction des coûts de 86
- Production plus rapide avec moins de composants et des temps d'assemblage plus courts
- Conformité réglementaire avec les normes (EU) 1935/2004, (EU) 10/2011 et BPF
- Amélioration de la fiabilité grâce à l'élimination des pièces mécaniques complexes et à la réduction de la complexité de la programmation
- Conception peu encombrante pour les environnements de production compacts
L'industrie de l'emballage alimentaire est soumise à une pression constante pour innover - en équilibrant l'efficacité, la réduction des coûts et la conformité à des réglementations de sécurité toujours plus strictes. Les méthodes d'automatisation traditionnelles reposent souvent sur des systèmes mécaniques complexes et encombrants qui nécessitent une maintenance et une programmation importantes.
Même de petits ajustements dans la chaîne de production peuvent se traduire par des avantages concurrentiels significatifs, et la fabrication additiveFA avec des matériaux déclarés sûrs pour les aliments s'avère permettre des avancées encore plus importantes. Un exemple en est un mécanisme innovant de rabat expansible qui a transformé la manipulation des produits en réduisant la complexité, les coûts et le temps de traitement. Cette approche qui change la donne permet non seulement d'améliorer l'automatisation, mais aussi de redéfinir ce qui est possible dans la production alimentaire moderne.

"En rationalisant la production grâce à l'impression 3D industrielle, nous avons non seulement réduit les coûts, mais aussi le risque de défaillance mécanique, ce qui garantit une fiabilité opérationnelle à long terme."
Paul Bocionek | Directeur général de apc-tec GmbH
Défi
Un fabricant de l'industrie alimentaire avait besoin d'une solution efficace pour placer de délicats bâtonnets de biscuits dans des boîtes de conserve tout en veillant à ce qu'une incrustation de papier empêche tout contact direct entre les biscuits et la surface de la boîte. Les méthodes traditionnelles utilisant des pinces externes nécessitaient un espace excessif, une programmation complexe et de nombreux composants individuels, ce qui posait des problèmes de coût, de temps de traitement et d'erreurs potentielles. En outre, l'ensemble de la solution devait être conforme aux réglementations strictes en matière de contact alimentaire tout en conservant une grande fiabilité mécanique dans des conditions de production rapides.
Solution
apc-tec GmbH a mis au point un système mécanique compact et intelligent pour automatiser efficacement le processus d'emballage. Au lieu d'utiliser des mécanismes de préhension externes traditionnels, apc-tec a intégré une pince extensible à l'intérieur de la boîte qui fixe l'insert en papier avant de la remplir de bâtonnets de biscuits. "Notre solution innovante a optimisé ce processus de production d'une manière que la fabrication traditionnelle ne pouvait pas réaliser. La combinaison d'une conception intelligente des composants mécaniques rendue possible par l'impression 3D d'EOS et d'une déclaration de contact alimentaire complet change la donne en matière d'automatisation de la sécurité alimentaire", explique Paul Bocionek, directeur général d'apc-tec GmbH.
Cette approche a permis de réduire considérablement le nombre de composants requis, éliminant ainsi le besoin de capteurs supplémentaires et d'automates programmables complexes. L'ensemble du système a été conçu et produit à l'aide de matériaux déclarés sûrs pour l'alimentation, notamment le PA 2200, qui est conforme aux normes(EU) 1935/2004,(EU) 10/2011 et aux bonnes pratiques de fabrication (BPF). En outre, le rabat expansible a été fabriqué à l'aide d'une impression 3D industrielle de haute précision, ce qui permet un prototypage, une itération et une production rapides. "Nos machines EOS offrent non seulement une grande fiabilité mécanique, mais le matériau PA 2200 conforme garantit que chaque pièce répond aux exigences rigoureuses de l'industrie alimentaire sans compromettre l'efficacité", souligne M. Bocionek.
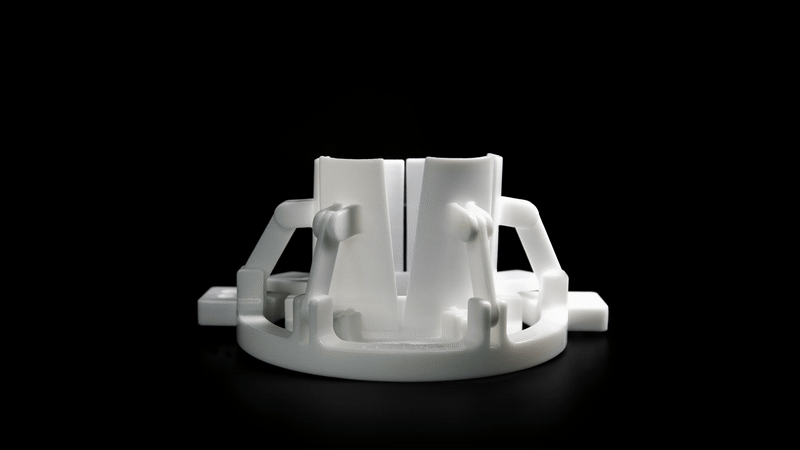
Résultats
La mise en œuvre du volet d'expansion d'apc-tec a transformé le processus de production en le rendant nettement plus efficace, plus rentable et plus conforme aux réglementations en matière de sécurité alimentaire. La conception compacte, qui ne pouvait être réalisée que par la FA, a éliminé le besoin de mécanismes de préhension externes, permettant une approche plus rationalisée et moins encombrante. Grâce au nombre réduit de composants, apc-tec a minimisé non seulement les coûts des matériaux, mais aussi le temps et la complexité associés à l'assemblage et à la programmation. "En rationalisant la production grâce à l'impression 3D industrielle, nous avons non seulement réduit les coûts, mais aussi le risque de défaillance mécanique, ce qui garantit une fiabilité opérationnelle à long terme", déclare M. Bocionek.
L'impact financier a été substantiel, avec des coûts d'installation initiaux réduits de 15 000 € à seulement 2 000 €, grâce à l'élimination de multiples pièces mécaniques et à la simplification de l'intégration du système. En outre, l'ensemble du volet ayant pu être fabriqué en une seule étape grâce à l'impression 3D industrielle, les délais de production et de mise en œuvre ont été considérablement raccourcis, car la technologie a permis des itérations de conception rapides, a minimisé les besoins en outillage et a facilité la fabrication à la demande sans les retards associés aux chaînes d'approvisionnement traditionnelles.
Au-delà des améliorations en termes de coûts et d'efficacité, le nouveau composant est entièrement conforme aux réglementations de l'UE en matière de contact alimentaire et aux normes BPF, ce qui garantit que tous les matériaux utilisés dans le processus ainsi que l'ensemble de la chaîne d'approvisionnement répondent aux exigences les plus strictes en matière d'hygiène et de sécurité. Il s'agit donc d'un exemple novateur de la manière dont l FA peut stimuler l'innovation dans la production alimentaire.
"Notre solution a optimisé ce processus de production d'une manière que la fabrication traditionnelle ne pouvait pas réaliser. La combinaison d'une conception intelligente des composants mécaniques rendue possible par l'impression 3D d'EOS et d'une déclaration de contact alimentaire complet change la donne en matière d'automatisation de la sécurité alimentaire."
Paul Bocionek | Directeur général de apc-tec GmbH
Études de cas EOS
Découvrez trois décennies d'excellence en matière d'impression 3D avec EOS