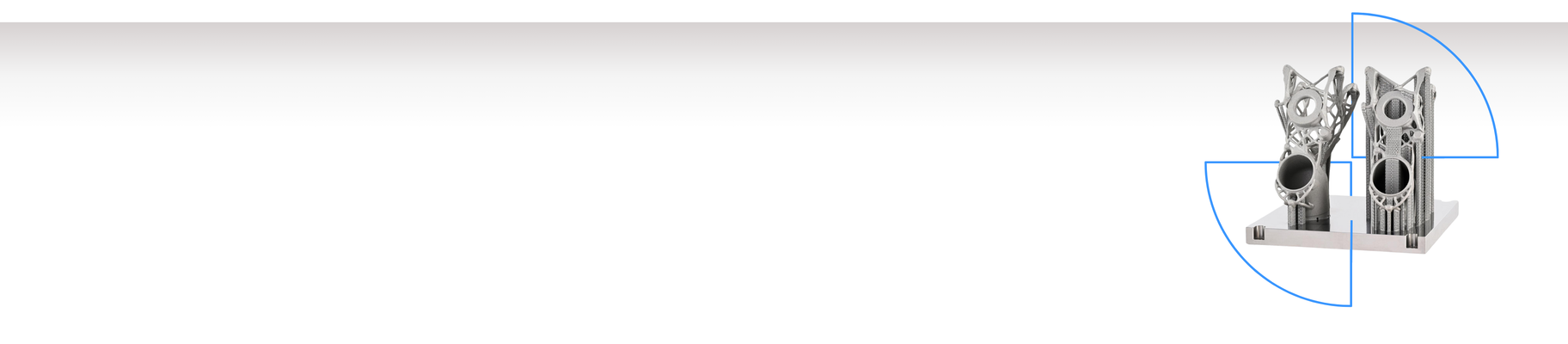
Moins de soutien -
FA pour le développement durable
16 SEPTEMBRE 2021 | Temps de lecture : 5 min | Auteur : Ho Kei-Leong
La fabrication additive (FA), également connue sous le nom d'impression 3D industrielle, est souvent considérée comme durable en raison de l'efficacité des matériaux, de la réduction de la consommation d'énergie, de la production locale, de la personnalisation et de l'optimisation de la conception, de la recyclabilité et de la réduction des exigences en matière d'outillage, entre autres. Bien que FA présente intrinsèquement ces avantages en matière de durabilité, de nombreux défis subsistent.
Dans le monde du DMLS ("Direct Metal Laser Melting "), le besoin de structures de soutien pendant le processus d'impression reste l'un des plus grands défis. Grâce à une gestion thermique avancée, il est possible de réduire les structures de soutien en ajustant la puissance du laser. Les structures de support sont essentielles pour éviter que les éléments en surplomb ou complexes ne se déforment ou ne s'effondrent lors de l'application des couches métalliques. Si les structures de support sont essentielles à la réussite du processus d'impression, elles entraînent également des inefficacités et des gaspillages sous forme de matériaux, de post-traitement et d'augmentation de la consommation d'énergie.
Pour relever ces défis, les chercheurs et les fabricants s'efforcent de mettre au point des structures de soutien plus efficaces afin d'optimiser l'ensemble du processus d'impression. L'une des approches les plus efficaces et les plus innovantes est la mise en œuvre de systèmes de surveillance et de contrôle en temps réel pour aider à identifier et à résoudre les problèmes au cours du processus d'impression, créant ainsi un système en boucle fermée pour des ajustements en temps réel.
EOS Smart Fusion
EOS Smart Fusion est une solution de contrôle en boucle fermée assistée par une surveillance en temps réel et des ajustements de processus adaptatifs pour faciliter l'impression de pièces avec des supports minimaux. Il s'agit d'une méthode intelligente de gestion thermique, conçue pour les fabricants afin de permettre l'impression de composants avec un support minimal. Cela permet de réduire le temps de fabrication, le temps de post-traitement et le gaspillage de matériaux. Basé sur un couplage de matériel et de logiciel de tomographie optique permettant d'obtenir des informations sur le processus par le biais d'une caméra proche infrarouge à haute résolution, Smart Fusion enregistre et mesure l'apport d'énergie en temps réel afin de faciliter une analyse plus précise des couches de construction individuelles.
Afin de tester le principe de Smart Fusion par rapport à notre modèle de base et à un autre logiciel tiers disponible sur le marché, une étude a été entreprise avec notre partenaire de recherche, l'Advanced Remanufacturing and Technology Center (ARTC) d'A*STAR, basé à Singapour. L'objectif était de fournir des données concluantes pour quantifier les améliorations apportées. La validation de l'impact sur le développement durable et la désignation de la fabrication additive comme l'avenir de la fabrication ne peuvent se faire que sur la base de données empiriques.

La méthodologie commence par une veille technologique et une recherche sur le marché des différents logiciels d'impression sans support. L'acier inoxydable 316L a été choisi pour cette étude, car ce matériau est connu pour nécessiter des structures de support solides afin d'imprimer les composants avec succès.* Des coupons coudés et une roue fermée de démonstration ont ensuite été construits et comparés selon différentes approches, y compris la quantification de la précision dimensionnelle. La roue a été sectionnée pour obtenir des micrographies du surplomb, tandis que les coupons angulaires ont été sectionnés pour évaluer la rugosité et la porosité de la surface. Enfin, une analyse comparative des émissions de carbone a été réalisée à l'aide du calculateur de carbone EOS afin d'examiner les différences entre les différentes approches. Tous les résultats sont mis en évidence dans le tableau et l'illustration suivants.
EOS Standard |
EOS avec Smart Fusion |
OEM avec Logiciel A |
|
---|---|---|---|
Coupon angulaire en surplomb | xx | xxx | x |
Précision dimensionnelle | xx | xxx | x |
Rugosité de surface | xx | xxx | x |
Porosité # | xx | xxx | x |
Empreinte carbone | x | xxx | Pas de données |
Temps d'impression | x | xxx | xx |
Volume de soutien | x | xxx | xx |
La roue EOS M 290 a été utilisée comme référence pour comparer et évaluer trois approches différentes : une impression standard, une impression standard avec Smart Fusion et une machine OEM différente intégrée avec un logiciel tiers de réduction de support disponible dans le commerce, appelé "logiciel A" dans cette étude. Smart Fusion surpasse à la fois le logiciel disponible dans le commerce et la roue imprimée de manière conventionnelle en termes d'utilisation du volume de support, réussissant ainsi à fabriquer la pièce correctement dès la première fois.
L'impression basée sur le logiciel A a nécessité de multiples tentatives, au moins 4 essais avant de réussir à imprimer la roue. Avec Smart Fusion , la pièce a été fabriquée en un temps de traitement global nettement plus court, nécessitant un volume de supports réduit et une précision dimensionnelle supérieure (voir figure X). La comparaison des coupons angulaires fabriqués avec Smart Fusion a montré une meilleure rugosité de surface et une porosité réduite (voir figure Y). Fait remarquable, Smart Fusion a permis d'obtenir l'angle de surplomb le plus faible qui ressemble le plus au modèle CAO du coupon.
Le résultat de l'évaluation comparative quantifie et met en évidence les avantages substantiels d'EOS Smart Fusion. Par rapport à l'impression conventionnelle sur métal, on constate une réduction de 38 % du volume de support et une réduction considérable de 62 % du temps d'impression, ce qui représente presque une journée entière. Le coût de production de chaque pièce est ainsi réduit de 76%! En outre, Smart Fusion répond à l'appel à la durabilité et à la réduction de l'empreinte carbone avec une réduction de 62 % des émissions de CO2 pendant l'impression (de 29 à 11 kgCO2-eq) et une réduction substantielle de 84 % des émissions pendant le post-traitement (de 187 à 30 kgCO2-eq).
Avec sa gestion intelligente de la chaleur, Smart Fusion propose un logiciel qui permet de modifier la contrainte résiduelle FA des métaux. En minimisant la perte de matière et en réduisant le temps de traitement, il est possible de réaliser des économies et de rendre la production plus durable. Notre objectif est de collaborer avec nos clients et partenaires pour tester, mettre en œuvre et optimiser cette solution, en leur donnant un avantage concurrentiel pour exploiter pleinement les avantages de FA.
Alors que la technologie continue d'évoluer et que son adoption se développe, EOS continuera à développer des solutions de pointe sur le site FA , en mettant l'accent sur la durabilité et en les adaptant aux besoins du marché pour façonner l'avenir de la fabrication.
Vous souhaitez en savoir plus ? N'hésitez pas à nous contacter pour une discussion approfondie sur la façon dont EOS et Smart Fusion peuvent vous permettre de réaliser une fabrication durable grâce à la fabrication additive !
* L'acier inoxydable 316L est actuellement en phase de test sur Smart Fusion. Par conséquent, aucun processus standardisé n'est actuellement disponible.
