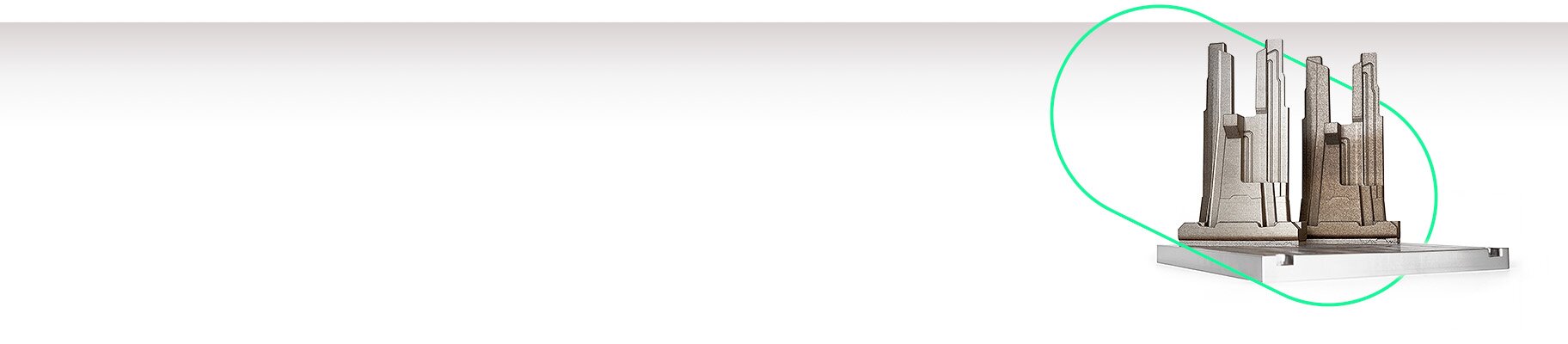
Smart Fusion - Contrôle de la boucle de rétroaction
pour les microstructures homogènes
24 mars 2025 | Temps de lecture : 7 min | Auteur : Tobias Novotny, Narges Mirzabeigi, Dominik Kunz, Ulrich Kleinhans
La surchauffe est un défi majeur dans la fusion laser de métaux sur lit de poudre (PBF-LB/M) qui affecte la constructibilité de caractéristiques complexes et de surplombs plats, la qualité des surfaces en contact avec le sol et les propriétés des matériaux des pièces finies. Bien que nous ayons démontré dans le passé comment la Smart Fusionnotre système de contrôle en boucle de rétroaction, peut réduire le besoin de structures de soutien, cet article vise à montrer son effet sur l'histoire thermique et la formation de la microstructure. En collaboration avec l'Institut des technologies photoniques (LPT), nous avons comparé les processus standard en boucle ouverte avec les processus en boucle fermée de Smart Fusion dans des géométries qui provoquent une accumulation de chaleur. Nous avons constaté que Smart Fusion améliore considérablement l'homogénéité des microstructures et la dureté en garantissant une signature thermique cohérente tout au long de la fabrication.
Principes de la surchauffe et de la Smart Fusion
Dans la technique PBF-LB/M, le laser délivre de l'énergie de manière répétée dans la pièce à chaque couche. Si l'énergie ne peut pas être transférée suffisamment loin de la zone de traitement, la chaleur s'accumulera pendant la construction et conduira finalement à une surchauffe. Les ingénieurs d'application de FA sont bien conscients des risques de surchauffe et ont toujours eu des options à leur disposition pour en atténuer les effets.
Les approches courantes pour faire face à la surchauffe sont les suivantes :
- ajouter des temps d'attente, par exemple des temps de couche ou de vecteur minimaux pour un temps de refroidissement plus long
- l'utilisation de plus de structures de soutien pour une meilleure conduction de la chaleur dans la plaque de construction
- réduire l'apport énergétique du processus, par exemple en réduisant la puissance du laser
Cependant, les temps d'attente et l'augmentation du volume de support entraînent des temps de construction plus longs et des coûts de pièces plus élevés, tandis qu'un paramètre avec un apport d'énergie réduit peut compromettre la densité des pièces. Une solution différente s'impose.
La figure 1 montre quelques travaux de construction exemplaires présentant des caractéristiques géométriques communes susceptibles de provoquer une surchauffe, ainsi que la signature thermique correspondante avec et sans Smart Fusion.

Dans les géométries complexes, telles que le support AlSi10Mg, l'accumulation de chaleur se produit là où les surplombs ou les petites caractéristiques limitent le flux de chaleur. Pour obtenir des conditions stables, la puissance du laser doit être réduite dans ces régions.
Dans les travaux de construction avec de petites zones d'exposition et donc des temps de couche courts, tels que le travail sur l'insert d'outillage MS1, la chaleur s'accumule généralement d'une couche à l'autre. Il en résulte une augmentation des températures de surface des pièces jusqu'à ce qu'un équilibre soit atteint. Par conséquent, une réduction progressive de l'apport d'énergie sur la hauteur de construction est nécessaire.
Idéalement, l'apport d'énergie devrait être ajusté dynamiquement en fonction de la géométrie de la pièce et de la charge du travail de construction (c'est-à-dire le temps de couche). Cela doit se faire de manière à ce que les conditions thermiques de la pièce restent stables.
Une solution possible consiste à mesurer les signatures thermiques pendant le travail de construction et à utiliser un contrôleur pour réguler l'apport d'énergie localement sur la base des données de mesure acquises. Notre système de contrôle en boucle fermée, Smart Fusion, surveille les valeurs de gris enregistrées par tomographie optique (EOS Exposure OT), les compare à une valeur de gris cible spécifique au matériau et au processus, et ajuste la puissance du laser en conséquence au niveau d'un microvecteur dans la couche suivante.
La figure 2 illustre le principe de fonctionnement de Smart Fusion. La différence apportée par Smart Fusion est immédiatement visible lorsqu'on observe l'aspect du processus.
La vidéo suivante montre l'exposition d'une couche exemplaire pour une géométrie difficile à l'aide de Smart Fusion et d'un processus standard en boucle ouverte à des fins de comparaison. La figure 3 montre cette géométrie et des instantanés comparatifs des deux processus.

Pour montrer les effets de la surchauffe dans cette étude, une géométrie d'essai composée de trois cônes renversés ("démonstrateur d'accumulation de chaleur"), qui avait également été utilisée dans des études précédentes, a été sélectionnée. Dans ce démonstrateur, la chaleur s'accumule rapidement dans les cônes en raison des minces cylindres de raccordement qui agissent comme un goulot d'étranglement thermique. Sans Smart Fusion , cela conduit à des surfaces de pièces chaudes et incandescentes visibles pendant une longue période de temps après l'exposition de la pièce.
Bien que nos paramètres de processus standard soient résistants à la surchauffe, ils représentent le meilleur compromis entre de nombreux facteurs et ne sont donc pas idéaux pour les géométries extrêmes ou les temps de couche excessivement courts. L'utilisation de la signature du processus (c.-à-d. le GV moyen) que ces paramètres de processus produisent généralement comme cible pour Smart Fusion garantit des résultats idéaux, même pour des pièces très complexes.

Historique thermique et son effet sur la microstructure
Les pièces traitées par PBF-LB/M présentent un historique thermique unique défini par des taux de refroidissement extrêmement rapides dans le bain de fusion et un réchauffement cyclique du matériau précédemment solidifié lorsque les vecteurs de balayage adjacents et les couches suivantes sont exposés. En cas de surchauffe, les modifications du refroidissement initial et le maintien ultérieur à des températures élevées affectent l'évolution de la microstructure.
La température de surface de la couche précédente solidifiée du matériau détermine la température à laquelle la couche actuelle du matériau peut se refroidir. Si ces températures atteignent des niveaux où des changements de phase se produisent, tels que la température de démarrage de la martensite (Ms) pour les aciers, la composition de la phase telle qu'elle est construite peut être affectée de manière significative. Si la transformation de la martensite est initialement supprimée ou ne peut se terminer complètement, des niveaux plus élevés d'austénite conservée peuvent être observés, ce qui entraîne une réduction de la dureté.
Le durcissement par précipitation en cours de processus peut se produire si des températures élevées sont maintenues dans une région d'une pièce pendant une période suffisamment longue. Par conséquent, les temps de couche peuvent être critiques pour la formation de précipités au cours du processus et la précipitation est susceptible de changer en fonction des conditions actuelles dans la construction. La précipitation locale entraîne une dureté inhomogène et une fragilité potentiellement accrue.
À des températures élevées, les structures de solidification typiques formées dans le PBF-LB/M, telles que le réseau riche en Si dans l'AlSi10Mg, commencent à devenir plus grossières ou même à se dissoudre. Cela peut réduire considérablement la résistance à l'état monté (jusqu'à 44 % de perte de dureté lors des essais).
Une forte accumulation de chaleur peut conduire à une trempe du matériau déjà solidifié au cours du processus. Dans les géométries difficiles fabriquées en Ti6Al4V, on a observé une martensite tempérée, plus grossière et plus lattée, au lieu de la martensite aciculaire traditionnelle.
Le réchauffement cyclique des couches suivantes affecte également la microstructure en "tempérant" le matériau déjà solidifié. Les différences entre la couche supérieure et le reste de la construction sont souvent attribuées à cet effet. La surchauffe peut affecter le résultat du réchauffage cyclique puisqu'un refroidissement entre les couches peut être nécessaire pour que l'effet de trempe se produise.
Dans l'ensemble, des conditions thermiques incohérentes au cours de la fabrication peuvent entraîner des changements microstructuraux locaux et des variations correspondantes des propriétés mécaniques. Ces changements peuvent entraîner des écarts inattendus dans les propriétés lorsque l'on compare les échantillons d'essai avec les pièces réelles et nécessitent des étapes supplémentaires de traitement thermique (par exemple, traitement en solution) pour les résoudre.
Des propriétés plus homogènes dans l'EOS MaragingSteel MS1 d'EOS MaragingSteel grâce à la Smart Fusion
Les microstructures typiques des matériaux PBF-LB/M courants sont désormais bien connues. À titre d'exemple, la figure 6 met en évidence certaines caractéristiques de la microstructure telle que construite de l'EOS MaragingSteel MS1 d'EOS MaragingSteel (similaire au 1.2709).
La gravure révèle un motif de bassin de fusion en forme d'écaille de poisson, avec des limites claires du bassin de fusion. Des groupes de lattes de martensite sont visibles sur les images détaillées. Le MS1 est typiquement martensitique à l'état construit avec une petite fraction volumique d'austénite conservée. À des grossissements plus importants sous le MEB, les structures de solidifications cellulaires et colonnaires deviennent visibles.
La figure 7 compare la microstructure d'un démonstrateur d'accumulation de chaleur avec et sans Smart Fusion.
Lorsque Smart Fusion est activé, une réponse de gravure cohérente est observée sur l'ensemble de l'échantillon. En revanche, pour l'échantillon sans Smart Fusion, une région de gravure sombre est observée au-dessus du goulot d'étranglement thermique, au lieu de la réponse de gravure brillante traditionnelle. En y regardant de plus près, on observe une décomposition partielle des structures cellulaires de solidification. La dureté était significativement plus élevée dans la région de gravure sombre, atteignant des niveaux jusqu'à 540 HV (plus de 100 HV de plus que d'habitude). Cela indique qu'une précipitation in situ significative a lieu.
Afin d'éviter tout contact de la machine à recouvrir avec les bords recourbés de la pièce en surchauffe sans Smart Fusion, un temps d'exposition minimum de 40 secondes a été utilisé pour ce travail de construction. Avec Smart Fusion activé, il a également été possible de fabriquer la pièce sans temps d'attente. La figure 8 montre une micrographie, ainsi qu'une comparaison du profil de dureté entre les différents réglages.
Les micrographies démontrent que même sans temps de couche minimum, la boucle de rétroaction peut contrôler efficacement les conditions thermiques et produire une pièce très dense. En outre, une dureté exceptionnellement constante a été obtenue sur toute la hauteur de construction. L'absence de temps d'attente entre les couches a probablement empêché la formation de précipités, qui peuvent se produire lorsque le matériau est tempéré par les couches suivantes.

Conclusion
La surchauffe au cours du processus PBF-LB/M entraîne des altérations significatives des microstructures en fonction de la géométrie de la pièce et des temps de couche. Smart Fusion garantit un profil thermique cohérent, même dans les conditions les plus difficiles. En réduisant l'apport d'énergie de manière dynamique uniquement lorsque cela est nécessaire, il est possible d'obtenir des propriétés plus homogènes sans perte de productivité pour MS1 et Ti6Al4V.
Nos résultats montrent que la Smart Fusion est particulièrement pertinente pour :
- Des microstructures plus cohérentes pour les pièces complexes à flux thermique restreint
- Microstructures plus cohérentes pour des charges de travail faibles avec des temps de couche minimaux réduits ou nuls
- Les traitements thermiques qui conservent dans une certaine mesure la microstructure telle qu'elle a été construite (comme le vieillissement direct).
- Exploration de microstructures et de propriétés sur mesure
Comment Smart Fusion affecte-t-il les microstructures d'autres matériaux ? Nous menons en permanence des tests approfondis sur les performances de Smart Fusion avec nos différents matériaux. N'hésitez pas à nous contacter!
Sources et lectures complémentaires :
Nahr F, Novotny T, Kunz D, Kleinhans U, Chechik L, Bartels D, Schmidt, M. Advanced process control in laser-based powder bed fusion–Smart Fusion feedback-loop control as a path to uniform properties for complex structures?. JMRT 2025;34:604-618. https://doi.org/10.1016/j.jmrt.2024.12.014.
Nahr F, Rasch M, Burkhardt C, Renner J, Baumgärtner B, Hausotte T, et al. Geometrical influence on material properties for Ti6Al4V parts in powder bed fusion. JMMP 2023;7(3):82. https://doi.org/10.3390/jmmp7030082.
Yağmur, A, Pääkkönen, I, Miles, A. The Hitchhiker’s Guide to Smart Fusion. 2023. https://3d.eos.info/eguide-smart-fusion
Kürnsteiner P, Wilms MB, Weisheit A, Gault B, Jägle EA, Raabe D. High-strength Damascus steel by additive manufacturing. Nature 2020;582(7813):515–9. https://doi.org/10.1038/s41586-020-2409-3.
Mohr G, Altenburg SJ, Hilgenberg K. Effects of inter layer time and build height on resulting properties of 316L stainless steel processed by laser powder bed fusion. Addit Manuf 2020;32:101080. https://doi.org/10.1016/j.addma.2020.101080
Bartels D, Albert ME, Nahr F, Schmidt M. On the influence of volumetric energy density and inter-layer time on the material properties of case-hardening steels. Alloys 2023;2(3):168–83. https://doi.org/10.3390/alloys2030013.