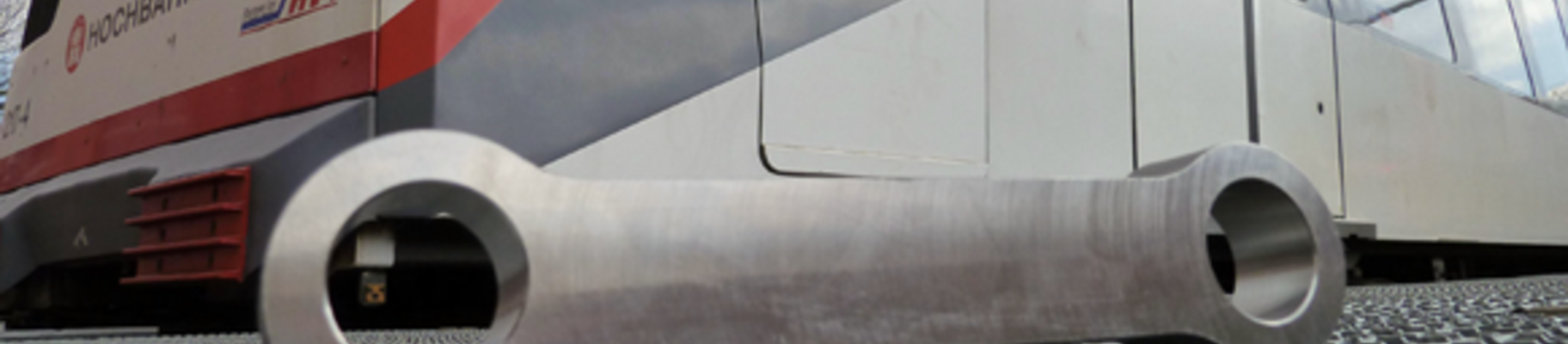
Repenser le chemin de fer : Stefanie Brickwede
Le pouvoir multimillionnaire de l'FA
17 AVRIL 2025 | Temps de lecture : 5 min
Dans un épisode récent de l'Additive Snack Podcast, l'animateur Fabian Alefeld a retrouvé Stefanie Brickwede, une personnalité de premier plan qui encourage l'adoption de l'FA non seulement au sein de la Deutsche Bahn (DB), la compagnie nationale des chemins de fer allemands, mais aussi dans divers secteurs grâce au réseau qu'elle dirige.
Cette discussion a permis de jeter un regard fascinant sur une décennie de mise en œuvre de l'FA à la DB, sur l'évolution stratégique des applications de niche vers un pilier essentiel de la fabrication, et sur le rôle critique de la collaboration dans l'accélération des progrès.
Le retour d'un pionnier dans le podcast
Fabian Alefeld a présenté Stefanie Brickwede, soulignant son double rôle de responsable de la fabrication additive à la Deutsche Bahn et de directrice générale du réseau Mobility Goes Additive (MGA). La dernière fois que nous nous sommes parlés, c'était il y a quelques années. Cet épisode nous a permis de faire le point sur les progrès remarquables réalisés par DB et MGA.
Une décennie d'additifs à la Deutsche Bahn : de l'obsolescence à la stratégie
Stefanie a expliqué que la DB célébrait cette année le dixième anniversaire de l'utilisation de l'FA Le voyage a commencé modestement, en s'attaquant au défi de l'obsolescence. Les trains étant souvent en service depuis 30, 40, voire 50 ans, il devient de plus en plus difficile et coûteux d'acquérir des pièces de rechange pour les modèles plus anciens. FA a présenté une solution parfaite pour produire ces pièces indisponibles à la demande. Ce qui a commencé avec seulement 10 pièces a explosé : DB a maintenant imprimé plus de 150 000 pièces dans 700 cas d'utilisation différents, en utilisant 12 technologies FA différentes.
Il est intéressant de noter que l'approche initiale de la DB était uniquement ascendante. En tant qu'entreprise de maintenance plutôt que de construction, la DB ne disposait pas de bases de données CAO complètes pour son vaste inventaire. Au lieu d'une initiative d'entreprise descendante typique, l'équipe de Stefanie s'est adressée directement aux collègues des ateliers de maintenance, en demandant à des personnes enthousiastes de toute l'entreprise de 200 000 employés de se joindre à l'effort de l'FA
C'est ainsi qu'est née une équipe passionnée, indépendante de la hiérarchie, qui a identifié les besoins du monde réel directement à partir de la base. Ce n'est que plus tard que la DB a commencé à intégrer les gabarits, les montages et l'outillage - souvent considérés comme des fruits à portée de main - et à développer des approches descendantes plus stratégiques en utilisant des bases de données améliorées et même l'IA pour identifier les pièces imprimables. Aujourd'hui, l'enthousiasme de la base et la stratégie du sommet fonctionnent en tandem.
Mesurer le succès : Des pièces imprimées aux millions d'euros économisés
Stefanie se souvient avec amusement d'une discussion sur les indicateurs de performance clés au cours de laquelle son patron, qui travaillait auparavant pour Airbus, a suggéré de mesurer le succès en imprimant 20 000 pièces au cours de la première année - un objectif qui a suscité des rires étant donné qu'ils n'avaient imprimé que 10 pièces à l'époque.
Si le nombre de pièces (en particulier de vraies pièces de rechange, des prototypes ou de l'outillage, et non des cadeaux) a été un premier indicateur, l'accent a rapidement été mis sur l'impact financier quantifiable. Depuis 2019, la FA a généré des économies s'élevant à plus de 10 millions d'euros par an pour la DB.
Ces économies proviennent de plusieurs sources : dépassement des quantités minimales de commande, réduction significative des délais de livraison (comme dans le cas du carter d'engrenage évoqué ci-dessous) et prévention des arrêts de train coûteux.
Le potentiel futur le plus important réside toutefois dans l'entreposage numérique. L'entrepôt physique de la DB pour le matériel roulant contient à lui seul des pièces d'une valeur de 1,8 milliard d'euros, dont 10 % pourraient déjà être imprimées aujourd'hui.
La stratégie "Road to 100 Million" de la DB, qui vise à réaliser 100 millions d'euros d'économies grâce à la fabrication à la demande et à la réduction des stocks physiques, exploite ce potentiel. Pour y parvenir, la DB exige désormais que 10 % des pièces des trains nouvellement achetés soient conçues pour être imprimées, une tendance adoptée par les collègues néerlandais (NS).

Surmonter les obstacles : Acceptation, qualification et normes
Stefanie a souligné l'importance de rendre la technologie tangible - le fait de présenter des pièces métalliques imprimées aux parties prenantes a permis d'ouvrir les yeux. La communication, le marketing interne et même un concours organisé par les employés (qui a servi à la fois à trouver des applications et à sensibiliser le public) ont joué un rôle clé. La prévalence croissante des imprimantes FDM domestiques a également contribué à familiariser les employés avec les concepts de base de l'FA.
Le long processus de certification constitue un obstacle majeur, en particulier pour les composants critiques.
L'impression elle-même n'est souvent pas le goulot d'étranglement ; c'est la qualification et les essais qui prennent le plus de temps. Conscients de ce fait, DB et MGA ont travaillé activement avec des organismes de normalisation tels que l'Institut allemand de normalisation (DIN) afin d'élaborer les lignes directrices nécessaires. L'un des principaux résultats est la norme DIN 52920, qui permet d'évaluer la capacité d'un site de production à imprimer des pièces critiques de manière fiable.
Stefanie a souligné la nécessité d'harmoniser les normes européennes (EN) ou internationales (ISO, ASTM) pour faciliter une adoption plus large et simplifier l'intégration des fournisseurs, qualifiant le "piratage" des normes de véritablement "sexy" parce qu'il permet une mise à l'échelle.
La mobilité devient additive : La puissance de la collaboration en réseau
Consciente de la nécessité d'apprendre des autres et de se développer plus rapidement, la DB a lancé le réseau MGA il y a neuf ans avec seulement neuf membres fondateurs. Aujourd'hui, MGA est un réseau européen FA premier plan qui compte près de 150 entreprises membres, dont les principaux opérateurs ferroviaires, fournisseurs, fabricants de machines, fournisseurs de matériaux, sociétés de logiciels, instituts de R&D et universités.
MGA encourage la collaboration entre les différents acteurs de la chaîne d'approvisionnement et de multiples secteurs, notamment le rail, l'aviation, l'automobile, l'aérospatiale, la construction, la défense, la médecine et même le style de vie (mode, bijouterie, design). Des groupes de travail s'attaquent à des défis communs tels que la certification, le développement de matériaux, la durabilité et l'éducation.
Stefanie a cité des exemples tels qu'un atelier rapide sur l'impression sur cuivre organisé en 14 jours et le développement d'une poudre ignifuge nécessaire (répondant aux normes ferroviaires élevées, auparavant limitées à des matériaux tels que l'Ultem 9085) grâce à la collaboration entre Siemens et le fournisseur de matériaux Lehmann&Voss. Ce réseau axé sur l'utilisateur comble le fossé entre les besoins de l'industrie et les capacités des fournisseurs.
Histoire d'une réussite : Éviter une crise grâce à l'FA
Un exemple frappant de l'impact de FA concernait 50 locomotives de fret immobilisées en raison de l'impossibilité de se procurer des carters d'engrenage. L'approvisionnement traditionnel prévoyait des quantités de commande minimales et un délai de livraison de deux ans.
Face à une crise potentielle discutée au niveau du conseil d'administration, l'équipe de Stefanie s'est appuyée sur le réseau MGA, a réétudié la pièce et a utilisé FA pour imprimer des moules en sable afin de couler les boîtiers dans le matériau d'origine.
L'ensemble du processus, depuis l'identification du problème jusqu'à la livraison du premier logement de remplacement, n'a pris que deux mois - une démonstration spectaculaire de la capacité de la FA à assurer la résilience opérationnelle.

Le chemin à parcourir : Croissance adaptative et perturbatrice
Stefanie souligne que l FA offre à la fois des solutions adaptatives (remplacement des pièces à l'identique, facilitant l'adoption pour les industries conservatrices) et un potentiel de rupture (nouvelles conceptions, pièces optimisées). Les deux sont nécessaires. Elle plaide pour que l'industrie de FA se mette à la place de l'utilisateur, en s'adaptant à ses besoins plutôt qu'en l'obligeant à s'adapter entièrement à la technologie.
Les réflexions de Stefanie Brickwede soulignent le pouvoir de transformation de l'FA lorsqu'elle est mise en œuvre de manière stratégique et collaborative. Le parcours de la Deutsche Bahn, qui s'étend sur une décennie, fournit un modèle convaincant pour tirer parti de l'FA afin d'améliorer l'efficacité, la résilience et l'innovation, tandis que MGA démontre la valeur exponentielle des partenariats intersectoriels pour surmonter les défis communs et accélérer l'adoption de cette technologie qui modifie les règles du jeu.