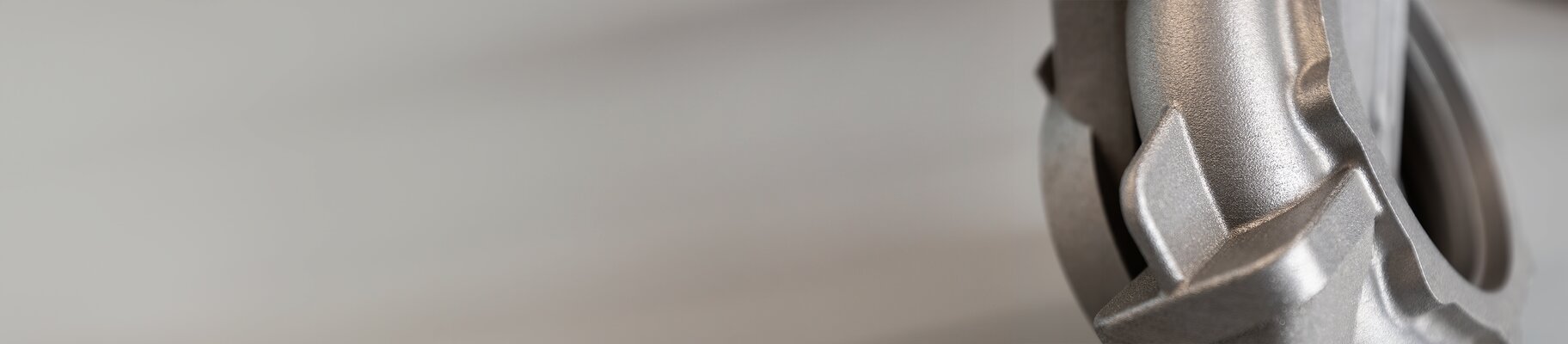
EOS NickelAlloy K500 pour la marine, la chimie et l'aérospatiale
14 NOVEMBRE 2024 | Temps de lecture : 5 min
L'alliage K500 est un membre remarquable de la famille des alliages de nickel, offrant une combinaison unique de propriétés mécaniques, de résistance à la corrosion et de conductivité thermique qui le rend idéal pour une variété d'applications exigeantes. Des environnements marins au traitement chimique et aux innovations aérospatiales, l'alliage K500 offre des performances fiables là où d'autres matériaux peuvent s'avérer insuffisants.
Chez EOS, nous sommes ravis d'apporter les avantages du K500 à la fabrication additive (FA) en utilisant la technologie LPBF (Laser Powder Bed Fusion). Ce développement révolutionne les industries en permettant la production de pièces complexes qui conservent les excellentes propriétés du K500 tout en bénéficiant de la flexibilité et de la précision de l'impression 3D.
Voici pourquoi le K500 est une solution idéale pour les applications marines, chimiques et aérospatiales, et comment EOS ouvre la voie en rendant ce matériau accessible à une production de pointe.
Qu'est-ce qui rend K500 unique ?
Le K500 est un alliage de nickel-cuivre (Ni-Cu) auquel s'ajoutent du titane et de l'aluminium. Il a été développé à l'origine en 1905, avant la plupart des superalliages modernes à base de nickel.
L'héritage du K500 a perduré, même lorsque de nouveaux alliages sont apparus au 20e siècle, ce qui souligne son attrait intemporel.
En fait, les spécialistes y ont de plus en plus souvent recours aujourd'hui, en particulier dans l'aérospatiale, où sa combinaison de solidité, de résistance à la corrosion et de conductivité thermique est difficile à égaler.
Propriétés principales :
- Bonne résistance mécanique : Le K500 conserve sa résistance même à des températures élevées, ce qui le rend idéal pour les applications qui exigent à la fois des performances élevées et une grande durabilité.
- Excellente résistance à la corrosion : Il présente des performances exceptionnelles dans les environnements difficiles, tels que les milieux marins et les usines de traitement chimique, en résistant à la corrosion par l'eau de mer, l'acide fluorhydrique et l'acide sulfurique.
- Conductivité thermique modérée : Le K500 offre une conductivité thermique de 17 à 20 W/mK dans une large gamme de températures de fonctionnement. Il offre ainsi un équilibre entre les superalliages à base de nickel, dont la conductivité est médiocre, et les alliages à base de cuivre, dont la conductivité est excellente mais la résistance plus faible.

Pourquoi K500 est parfait pour les applications FA
FA a ouvert de nouvelles portes pour des matériaux tels que le K500. Grâce à la technologie LPBF, des pièces complexes peuvent être produites avec une grande précision, en évitant les limites des méthodes de fabrication traditionnelles. Le K500 est particulièrement adapté à ce processus en raison de ses exigences simples en matière de post-traitement. L'alliage subit des traitements de vieillissement simples sans nécessiter d'étapes de durcissement complexes, ce qui en fait un choix rentable pour les fabricants.
En outre, la microstructure du K500 est plus simple que celle d'autres superalliages, ce qui signifie que ses propriétés restent constantes après le traitement FA . Cette facilité d'utilisation, combinée à la capacité de créer des designs complexes, explique pourquoi des industries telles que l'aérospatiale et le traitement chimique se tournent vers le K500 pour des composants critiques.
Applications marines : Résistance à la corrosion et durabilité
Dans les environnements marins, les matériaux sont constamment exposés à l'eau de mer corrosive et à des contraintes mécaniques élevées. Le K500 se distingue dans ce contexte par sa capacité à résister à la corrosion tout en conservant sa résistance mécanique, même dans des environnements à haute température.
Les applications marines typiques du K500 sont les suivantes :
- Attaches et ressorts
- Arbres et roues de pompes
La résistance de l'alliage à la corrosion de l'eau de mer en fait un matériau idéal pour les composants à longue durée de vie utilisés dans la marine. Qu'il s'agisse d'équipements d'ancrage, de fixations marines ou de systèmes de pompes sous-marines, le K500 garantit la fiabilité là où d'autres matériaux pourraient succomber à la rouille et à l'usure.
Industrie chimique : Solidité et inertie
L'industrie du traitement chimique exige des matériaux capables de résister à des environnements corrosifs sans se dégrader au fil du temps. L'inertie du K500 en présence d'acides fluorhydrique et sulfurique en fait un matériau de choix pour les composants critiques tels que les pompes et les vannes.
Il gagne également du terrain dans les initiatives d'énergie verte, en particulier dans le traitement de l'hydrogène. Alors que les industries s'orientent vers des sources d'énergie durables, le K500 offre la solidité, la résistance à la corrosion et la conductivité thermique nécessaires aux équipements utilisés pour la production et le stockage de l'hydrogène.
Les applications dans l'industrie chimique comprennent
- Pompes et composants de vannes
- Grattoirs et racloirs pour le traitement de la pâte à papier
- Chambres et filtres pour les procédés chimiques corrosifs
Aérospatiale : L'avenir des moteurs de fusée et des propulseurs
Dans le secteur aérospatial, la combinaison des propriétés du K500 - conductivité thermique, solidité et résistance à la corrosion - en fait un candidat idéal pour les moteurs de fusée, les tuyères et les propulseurs. Les moteurs-fusées, en particulier, sont confrontés à des conditions extrêmes dans lesquelles les matériaux doivent résister à des températures élevées, à des gaz d'échappement corrosifs et à des gradients de pression importants. Le K500 excelle dans ces scénarios en conservant son intégrité à des températures cryogéniques et élevées.
Actuellement, les alliages à base de cuivre tels que l'EOS CopperAlloy CuCrZr peuvent également être utilisés dans les chambres de combustion pour leur conductivité thermique, souvent recouverts d'alliages de nickel tels que l'EOS NickelAlloy IN718 pour une résistance accrue. Cependant, le K500 offre une alternative convaincante car il associe une résistance élevée à une conductivité thermique modérée, éliminant ainsi la nécessité d'un refroidissement supplémentaire dans certaines sections critiques.
Les applications aérospatiales du K500 comprennent
- Injecteurs de fusée
- Vannes à oxygène liquide
- Échangeurs de chaleur
- Collecteurs de turbines et pièces de moteurs
Comparaison du K500 avec d'autres alliages
Comparé aux superalliages à base de nickel, le K500 offre des performances plus complètes. Si les autres superalliages à base de nickel excellent dans les applications à haute résistance, leur faible conductivité thermique (5-10 W/mK) limite leur utilisation dans les environnements où la dissipation de la chaleur est cruciale. D'autre part, les alliages de cuivre comme le CuCrZr offrent une excellente conductivité thermique (260-340 W/mK), mais ils sont moins performants en termes de résistance.
Le K500 se situe entre ces deux extrêmes, offrant une conductivité thermique modérée (17-20 W/mK) ainsi que de bonnes propriétés mécaniques et une excellente résistance à la corrosion. Cet équilibre en fait un choix polyvalent pour les industries qui cherchent à optimiser les performances dans toute une série de conditions difficiles. C'est pourquoi EOS est fière de proposer le K500 sur le site FA.
Que vous construisiez des moteurs de fusée ou des équipements de traitement chimique, le K500 offre la durabilité et la fiabilité dont vous avez besoin pour rester en tête de la concurrence. En rendant cet alliage accessible grâce aux processus avancés FA , EOS continue de montrer la voie en apportant des solutions de pointe aux industries du monde entier. Pour en savoir plus sur les avantages du K500 et sur la façon dont EOS transforme les industries grâce à cet alliage polyvalent , cliquez ici.