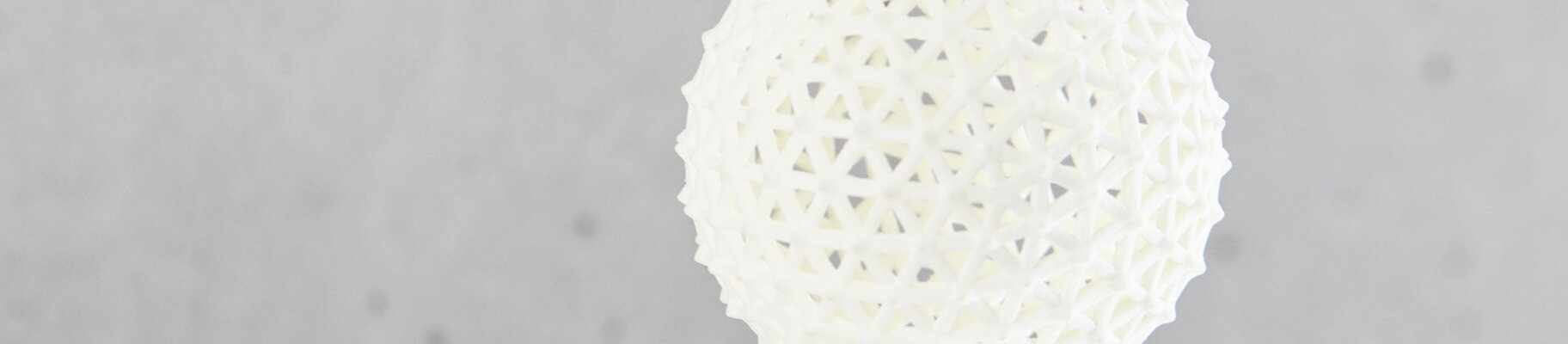
Nouveau sur FA: Guide du débutant sur la fabrication additive et ses principales technologies
8 MAI 2023 | Temps de lecture : 5 min
Vous ne connaissez pas encore le monde passionnant de la fabrication additive et les technologies clés qui la rendent possible ? Nous avons élaboré un guide complet mais simple dans ce blog.
La fabrication additive est une fabrication tournée vers l'avenir
Bien qu'il ne s'agisse pas d'une nouvelle technologie au sens strict, la fabrication additive (FA) - parfois appelée impression 3D - a suscité un vif intérêt ces dernières années. Et il y a de nombreuses raisons à cela :
-
Qu'une entreprise utilise les systèmes et matériaux du site FA pour façonner des mélanges de polymères de pointe ou des alliages d'aluminium polyvalents, il n'en reste pas moins qu'elle s'est équipée pour créer des pièces selon des paramètres géométriques qui étaient auparavant impossibles ou (au moins) extrêmement difficiles à réaliser.
-
Les pièces fabriquées par fabrication additive peuvent sembler plus "simples" que leurs homologues fabriquées traditionnellement - plus petites, plus légères, nécessitant moins de composants individuels, etc. Mais dans de nombreux cas, une pièce fabriquée par FA peut égaler ou dépasser les performances d'une pièce traditionnelle.
-
La fabrication additive fait ses preuves dans de nombreuses applications. Celles-ci vont des plus décontractées et amusantes (chaussures de course et casques de hockey) aux plus excitantes (moteurs de fusée) en passant par les plus importantes (implants médicaux et matériel chirurgical).
-
Les utilisateurs de la fabrication additive ont constaté des améliorations tangibles de la qualité et de l'efficacité de la production, ainsi qu'une réduction des délais de mise sur le marché et des dépenses globales.
EOS participe à la révolution de la fabrication additive depuis les premiers jours de la technologie, en développant des systèmes et des logiciels d'impression 3D ainsi que des services de formation et de conseil. Mais si vous ne connaissez pas encore FA, vous ne voulez peut-être pas encore être convaincu de la bonne foi de notre organisation - vous voulez en savoir plus sur l'historique, les processus, les applications et les réussites de cette technologie remarquable.
Et c'est exactement le voyage dans lequel nous avons l'intention de vous emmener.
Brève histoire de la fabrication additive
Dans certaines sources, un brevet déposé par l'ingénieur et inventeur américain Bill Masters - plus précisément le brevet U.S. 4665492A, daté du 2 juillet 1984 - est considéré comme le premier brevet d'impression 3D. D'autres attribuent cette distinction à un brevet de Charles Hull déposé aux États-Unis la même année. Ces deux brevets sont essentiels à l'histoire de la technologie.
Mais une demande de brevet déposée auprès de l'Office japonais des brevets (JPO) par Hideo Kodama (JP S56-144478) précède Masters et Hull de près de trois ans : Comme la demande que Masters a finalement envoyée à l'Office américain des brevets et des marques (USPTO), elle décrit un processus automatisé de création de formes en 3D par l'utilisation de la chaleur - laser ou ultraviolet (UV) - pour durcir les plastiques souples.
Kodama n'a pas réussi à obtenir de financement pour son idée, bien qu'il l'ait publiée dans des revues spécialisées réputées, et il a donc abandonné sa demande de brevet. Masters est passé par son brevet, a reçu une subvention et a travaillé dans ce domaine pendant une dizaine d'années, mais n'a guère attiré l'attention.
Une année charnière méconnue
L'année 1984 a été marquée par l'invention de plusieurs procédés essentiels sur le site FA , même s'il a fallu du temps pour que ces premières innovations soient mises en œuvre à grande échelle. La conception de Masters (comme celle de Kodama) comportait des exemples précoces de commande numérique par ordinateur (CNC) et de conception assistée par ordinateur (CAO), qui font partie intégrante des futurs systèmes FA .
Cette année a également vu le dépôt de deux brevets essentiels pour l'un des premiers procédés de fabrication additive ayant une viabilité commerciale potentielle : la stéréolithographie (SLA).
La première, déposée par les inventeurs français Alain le Méhauté, Olivier de Witte et Jean Claude André, a été abandonnée par son promoteur peu de temps après son dépôt. Le second, qui appartenait à Charles Hull, a donné lieu à la production de l'imprimante 3D SLA-1. Le prix de la SLA-1 était prohibitif pour beaucoup, et Hull, comme d'autres partisans de la première heure de FA , a eu du mal à convaincre les fabricants traditionnels de son potentiel. Cependant, Hull a également inventé le STL pour les fichiers de conception de la SLA-1, et ce format reste courant aujourd'hui.
Raffinement et mise à l'échelle
Les ingénieurs, y compris ceux d'EOS, ont passé les années 1990 à améliorer régulièrement les premiers procédés de fabrication additive - SLA et FDM (fused deposition modeling) - et à en développer de nouveaux. La plupart d'entre eux (mais pas tous) étaient axés sur la mise en forme de polymères en composants 3D, y compris la projection de matériaux et de liants, le laminage de feuilles, la fusion sur lit de poudre laser (LPBF) et le frittage sélectif par laser (SLS). Certaines de ces techniques, comme le SLS et le LPBF, permettent un travail avancé des métaux, mais elles sont destinées à la fabrication traditionnelle (soustractive). Mais le développement de méthodes de dépôt de matériaux, notamment la microfusion et la pulvérisation thermique, a ouvert la voie à l'utilisation additive du métal.
Associé aux progrès des logiciels de CAO et à l'essor des poudres de polymères et de métaux, le perfectionnement des systèmes d'impression 3D industriels leur a permis de se faire connaître pour le prototypage rapide tout au long des années 2000. Dans les années 2010, la fabrication additive s'est suffisamment développée pour faciliter l'assemblage de pièces à des niveaux beaucoup plus élevés, dans certains cas suffisamment pour que l'on puisse parler de "production de masse". Même avec les quelques limitations qui affectent encore FA - la compatibilité des matériaux (principalement du côté du métal), le coût initial et les efforts nécessaires à la mise en œuvre, le manque de compétences (bien qu'il se réduise) et le scepticisme des fabricants traditionnels - la présence et l'importance de la technologie continuent de s'étendre.
Les principales technologies FA
L'étape suivante de tout projet sérieux de mise en œuvre de la fabrication additive dans vos installations de production consiste à se familiariser avec les principes fondamentaux des technologies clés du site FA .
Il ne s'agit pas d'une liste de toutes les méthodes de fabrication additive, et toutes les techniques détaillées ci-dessous ne sont pas utilisées dans les systèmes EOS. Mais pour prendre la décision la plus éclairée possible à propos de FA , il faut avoir une compréhension du sujet qui va au-delà de notre catalogue de produits.
Photopolymérisation en cuve
Bien qu'il ne s'agisse pas du procédé SLA encore utilisé aujourd'hui, la photopolymérisation en cuve (ou parfois simplement la polymérisation) est sans doute le plus courant. Le nom de cette méthode vient de la source du matériau qui alimente la production : une cuve de résine photopolymère liquide. Une "plate-forme de construction" est descendue (puis remontée) à plusieurs reprises dans la cuve et, à chaque fois qu'elle en ressort, une source de lumière UV ou laser durcit la résine sur la plate-forme en couches qui forment un composant, conformément aux paramètres de conception du logiciel de CAO connecté au système. Une fois l'assemblage terminé, le système retire le produit de la cuve, qui a été vidée de l'excès de résine.
Les objets fabriqués additivement par polymérisation en cuve peuvent nécessiter davantage de post-traitement que les pièces fabriquées par d'autres méthodes ( FA ) : Une exposition supplémentaire aux UV ou au laser peut être nécessaire pour durcir efficacement le composant. En outre, au cours de la fabrication, des structures de soutien doivent parfois être mises en place sur la plate-forme pour que la résine durcisse et prenne la forme voulue par le concepteur ; si elles sont utilisées, elles doivent ensuite être soigneusement retirées de la pièce. Dans l'ensemble, la polymérisation en cuve est un procédé rapide et précis, mais comme les composants finis ne sont pas nécessairement résistants à la dégradation ou à la corrosion, il est peut-être préférable de l'utiliser pour le prototypage plutôt que pour la production de pièces prêtes à être commercialisées.
Jets de matériaux et de liants
La projection de matériau est peut-être plus proche par nature de l'"impression" que la plupart des autres méthodes de fabrication additive, même si l'impression 3D est parfois utilisée comme synonyme général de FA. Des buses placées au-dessus d'une plate-forme de fabrication émettent des matériaux liquéfiés (généralement des polymères ou de la cire, parfois du métal) sous forme de gouttes répétitives sur une plate-forme de fabrication. La lumière UV durcit les gouttes au fur et à mesure qu'elles forment des couches conformes aux paramètres de conception et prennent la forme de l'objet prévu. Le principal avantage de cette méthode est qu'elle ne génère que peu de déchets, ce qui est également utile pour le prototypage rapide.
Le jet de liant combine la poudre et le liquide, les déposant en couches alternées, et le liquide - typiquement un polycarbonate ou un polyamide - fonctionne comme un adhésif. Le principal avantage de cette méthode est que les alliages métalliques en poudre et les polymères ou céramiques peuvent être utilisés ensemble pour créer une pièce, mais cet avantage est quelque peu contrebalancé par le long temps de post-traitement nécessaire pour que les couches liquides se refroidissent et forment des liaisons appropriées.
Extrusion de matériaux
Il s'agit généralement de la modélisation par dépôt en fusion (FDM), l'une des premières méthodes de fabrication additive à avoir connu un succès industriel. C'est également la méthode la mieux connue des utilisateurs d'imprimantes 3D de bureau. Le polymère ou le plastique est aspiré dans l'imprimante, chauffé et finalement déposé en couches à travers une buse, qui s'ajuste automatiquement tout au long du processus pour répondre aux spécifications de la conception.
L'extrusion de matériaux par FDM ne permet d'imprimer que des polymères ou du plastique. Bien qu'une imprimante industrielle FDM soit compatible avec le plastique ABS, qui peut être à la base de pièces robustes, elle est lente et n'est que modérément précise par rapport à d'autres procédés de fabrication additive. C'est la principale raison pour laquelle les entreprises produisant des imprimantes FDM se sont fortement, voire totalement, tournées vers le marché grand public.
Plastification des feuilles
Méthode de fabrication additive exclusive à la tôle et au papier, le laminage de la tôle a des applications limitées, mais peut être utile pour la fabrication de prototypes à grande vitesse et à faible coût.
La version métallique de ce processus est appelée fabrication additive par ultrasons (UAM) et implique le soudage par ultrasons de feuilles de métal (généralement de l'aluminium, du cuivre, de l'acier inoxydable ou du titane). En revanche, la fabrication d'objets laminés (LOM) consiste à superposer des feuilles de papier à l'aide d'un adhésif. Ces deux techniques ne conviennent que pour la création de modèles de pièces. Cela dit, la capacité de l'UAM à utiliser plusieurs métaux peut aider les concepteurs et les ingénieurs à simuler comment des pièces métalliques fabriquées additivement en cuivre, par exemple, pourraient être compatibles avec d'autres métaux dans des applications industrielles spécifiques.
Dépôt d'énergie dirigée
Comme son nom l'indique, le dépôt par énergie dirigée (DED) utilise généralement une buse montée sur un bras automatisé très flexible pour déposer des matériaux en couches sur une plate-forme de construction au moment précis où une source de chaleur est concentrée sur la substance. Le DED comporte un certain nombre de variantes et peut donc utiliser des polymères, des céramiques ou des métaux, mais sa sous-catégorie la plus courante, la fusion par faisceau d'électrons (EBM), ne concerne que le métal.
Bien que peu pratique pour la production de pièces, cette méthode peut être utile en tant que technique additive pour la réparation de composants, en raison de la flexibilité de sa buse. Cependant, la réparation à grande vitesse que permet le DED réduit la précision, et si la précision est une priorité, les ingénieurs doivent sacrifier la vitesse.
Fusion des lits de poudre
Certaines des techniques de fabrication additive les plus courantes relèvent de la fusion sur lit de poudre, notamment le SLS, le frittage thermique sélectif (SHS), la fusion sélective par laser (SLS) et l'EBM. L'élément commun à ces méthodes est l'utilisation de polymères ou de métaux en poudre : Les poudres sont prélevées en couches à l'aide d'un rouleau ou d'une lame dans un conteneur situé sous ou à côté de la plate-forme de construction (lit), puis chauffées pour se solidifier.
Les principales différences entre les méthodes de fusion sur lit de poudre sont les suivantes :
-
Le SLS fusionne (sinters) des polymères ou des plastiques en pièces finies.
-
La solidification directe des métaux par laser (DMLS) est la variante de la SLS utilisée pour les métaux en poudre.
-
Le SHS utilise une tête d'impression thermique pour fritter les couches du lit de poudre.
-
L'EBM ne fonctionne qu'avec des poudres métalliques sous vide, ce qui permet au faisceau d'électrons de fusionner les couches dans le lit de poudre.
La fusion sur lit de poudre est un peu plus lente que les autres méthodes de fabrication additive et nécessite une consommation d'énergie importante. Mais comme elle est principalement réservée aux applications industrielles, ces questions ne sont pas nécessairement problématiques. Les variantes de cette technique basées sur le laser sont également plus à même de produire de manière fiable des pièces fonctionnelles, prêtes à être commercialisées, plutôt que des modèles ou des prototypes.
Contributions d'EOS aux technologies FA
Les systèmes d'impression 3D industriels proposés par EOS utilisent les variantes SLS et DMLS de la fusion sur lit de poudre pour les poudres polymères et métalliques, respectivement. En fait, EOS a non seulement contribué à populariser la SLS pour les applications industrielles, mais a également inventé la DMLS pour l'impression 3D de métaux il y a près de 30 ans. À l'époque où peu de gens pensaient que la fabrication additive avec des métaux était même plausible, nos ingénieurs et nos experts affinaient nos outils et nos méthodes pour en faire une réalité.
L'innovation dans tous les domaines
La réputation d'EOS dans l'industrie additive ne repose pas uniquement sur les méthodes de fusion sur lit de poudre que nous avons affinées, les systèmes d'impression 3D que nous avons développés ou les matériaux de fabrication additive en polymère et en métal que nous avons créés en interne. Nous adoptons une approche holistique de la fabrication additive et proposons des services de confiance en complément de notre matériel et de nos logiciels, notamment des conseils en matière de projets dispensés par l'équipe primée Additive Minds et des cours d'impression 3D pour aider les novices en matière d'impression additive à devenir des concepteurs et à affiner les compétences des ingénieurs pour en faire des experts.
Contactez un expert d'Additive Minds pour en savoir plus, où que vous en soyez dans votre voyage dans le monde de la fabrication additive.