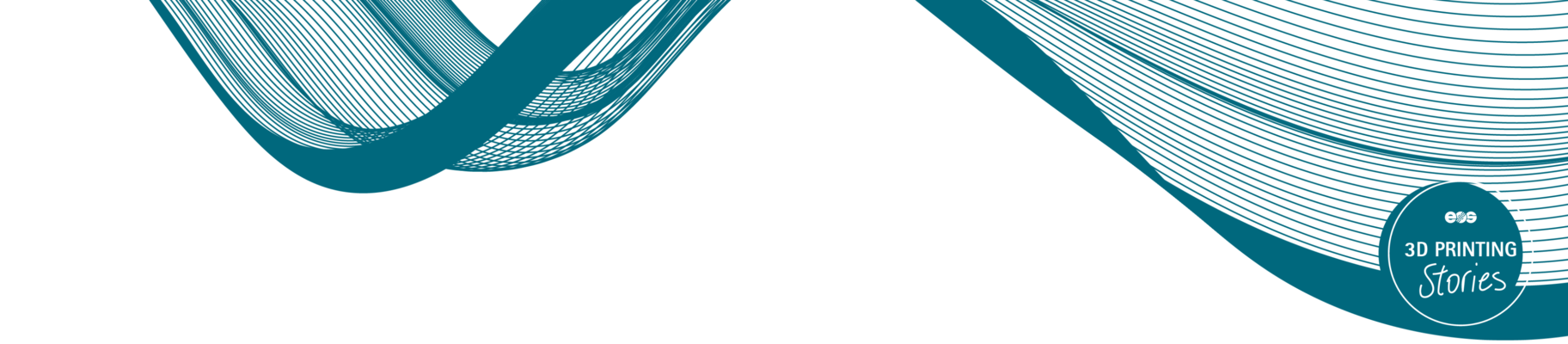
Un refroidisseur, qui refroidit l'air en utilisant de l'air
L'entreprise de technologies propres justairtech développe un système de refroidissement imprimé en 3D d'une efficacité nettement supérieure
26 février 2024 | Temps de lecture : 15 min
C'est impossible ? Oh si, c'est possible ! Cinq fois plus efficace et avec une consommation d'électricité réduite de 80 %.
Actuellement, tout le monde parle de l'utilisation des pompes à chaleur pour le chauffage des bâtiments. Un échangeur de chaleur fait non seulement partie intégrante d'une pompe à chaleur, mais il est également un composant essentiel d'un refroidisseur. Comment fonctionne-t-il ? Il fonctionne en transférant de l'énergie thermique entre deux milieux, mais selon un processus plutôt inefficace, que Holger Sedlak, directeur technique de justairtech, était déterminé à améliorer : "Je FA suis stimulé par l'idée de voir quelque chose qui n'était pas réalisable jusqu'à présent et qui est pourtant physiquement possible. Je commence alors à chercher des solutions. Dans le cas présent, nous ne nous occupons que de l'air". Au terme d'un parcours fascinant pour EOS et justairtech, il a été établi qu'une solution était effectivement possible. Le résultat est un échangeur de chaleur très efficace qui permet de concevoir un refroidisseur révolutionnaire ne nécessitant qu'un tiers de l'énergie électrique nécessaire auparavant.
Qu'y a-t-il de nouveau dans le concept justairtech ?
"Une seule voie rapide vaut mieux que plusieurs stations d'échange".
L'air d'une pièce est conditionné en l'aspirant dans un échangeur de chaleur, où il est refroidi. Il y a ensuite un circuit d'eau et un autre circuit avec un fluide tel que des hydrocarbures fluorés. Ces circuits doivent être entraînés par des pompes, et le système nécessite également des ventilateurs et des composants supplémentaires, qui consomment tous de l'électricité. M. Sedlak utilise un exemple descriptif pour expliquer son idée alternative de refroidir l'air avec de l'air : "Autrefois, pour aller de Munich à Berlin en train, il fallait changer de gare. Cela prenait non seulement du temps, mais c'était aussi assez ennuyeux. Mais si l'on peut éviter tous ces changements en empruntant une voie rapide, le voyage est à la fois beaucoup plus rapide et beaucoup plus agréable". Tel est le principe de base de son produit : Sedlak élimine tous les éléments intermédiaires inutiles, ce qui donne un échangeur de chaleur air-air fractal1 qui, comparé aux modèles conventionnels, permet de concevoir un nouveau refroidisseur et une nouvelle pompe à chaleur qui ne consomment qu'un cinquième de l'électricité. Jusqu'ici, tout va bien. L'une des raisons pour lesquelles cette solution n'existait pas jusqu'à présent est qu'elle ne pouvait tout simplement pas être produite.
1Fractale est un terme qui désigne certaines formes naturelles ou artificielles ou certains motifs géométriques (le libellé anglais correspond au texte original allemand). Source : Wikipedia, 24.07.2023
Défi relevé :
Surface maximale, épaisseur minimale des parois, etc.
Holger Sedlak a présenté son idée à EOS en mai 2022, ainsi que la structure clé de son échangeur de chaleur. Philipp Komurka, de l'équipe Additive Minds d'EOS, a discuté de l'idée avec ses collègues, bien qu'ils aient d'abord considéré que le succès de sa mise en œuvre était très improbable. Le principal obstacle à sa réalisation était l'épaisseur extrêmement faible de la paroi, d'environ 150 mm micromètres, ainsi qu'une très grande surface et, au total, environ 330 000 canaux d'un diamètre de seulement 0,5 millimètre. Bien que l'impression EOS DMLS-3D soit conçue pour des structures très complexes, le processus laser nécessite un transfert d'énergie. Cela signifie que le matériau doit fondre pour former une couche, mais pour respecter les spécifications de conception extrêmement strictes du composant et ne pas obstruer les canaux, il est soumis à des contraintes de hauteur. Une autre exigence était l'utilisation du matériau 316L, c'est-à-dire de l'acier inoxydable. D'autres matériaux auraient été plus faciles à mettre en œuvre, mais leur conductivité aurait été trop élevée, ce qui aurait nui au fonctionnement de l'échangeur de chaleur.
"Dans ma vie, j'ai réussi à réaliser beaucoup de choses impossibles, mais j'ai toujours travaillé avec des partenaires. Ce qu'il faut, c'est une pensée systémique et un voyage commun avec d'autres personnes pour voir où des ajustements pourraient être nécessaires à la fois dans la conception et dans la technologie de production. Il était clair pour moi que mon produit ne pouvait être créé que par l'impression 3D sur métal, et EOS a non seulement assumé une partie du risque, mais elle s'est aussi engagée à fond pour atteindre l'objectif ensemble.
Holger Sedlak, directeur technique de justairtech

Le chemin vers l'objectif
Processus et conception, dépoussiérage et construction à froid
Deux membres de l'équipe du projet se sont réunis avec Philipp Komurka pour travailler à rendre l'impossible possible. Ils ont commencé par modifier les paramètres et les processus en les adaptant aux exigences de l'échangeur de chaleur justairtech. L'équipe a réussi à configurer des variables telles que la puissance du laser, la vitesse et les plages de température de manière à permettre la construction d'une telle structure. À l'été 2022, le premier essai s'est avéré concluant, mais il a nécessité un temps de construction très long de 110 heures. Projetés sur l'ensemble du composant, les coûts unitaires auraient été beaucoup trop élevés pour une exploitation économiquement viable.
La tâche suivante consistait donc à réduire le temps de construction à un niveau d'environ 20 heures, comme l'avait envisagé Holger Sedlak à l'origine. Cela signifiait une réduction de 80 % du temps de construction. Pour ce faire, il a fallu réduire le volume des données de construction, car les innombrables vecteurs à l'origine ont donné lieu à un fichier de conception très volumineux, ce qui a entraîné un temps de traitement ultérieur excessivement long. La conception a été optimisée dans le cadre d'une étroite collaboration entre EOS et justairtech et le volume de données a été considérablement réduit. La deuxième étape a consisté à dépoussiérer, car lors de la première tentative de construction, la structure finie contenait environ 30 kilogrammes de poudre en vrac, qui s'est retrouvée coincée dans les minuscules canaux. Komurka explique : "Au début, en plus d'utiliser le système de dépoudrage, nous avons dû tapoter les canaux à la main avec un petit marteau, parce que nous n'avions pas attendu assez longtemps. Finalement, nous nous sommes rendu compte que le composant avait simplement besoin d'un temps de dégazage plus long." À l'automne 2022 et après de nombreuses étapes d'optimisation, le temps de construction a atteint 60 heures, ce qui correspond à une réduction de près de 50 %. Pour accélérer encore le processus, le composant a été construit à froid sur le site EOS M 400 4 - normalement, l'espace de construction est chauffé, car cela facilite le travail avec le matériau. En fin de compte, l'utilisation de la construction à froid a permis de réduire considérablement le temps de refroidissement.
Mission plus que remplie - et maintenant ?
"Actuellement, nous avons un temps de construction de 10 à 12 heures, avec un dépouillement d'environ 4 heures - ce qui nous amène à un temps de construction d'environ 16 heures pour compléter le composant central du nouvel échangeur de chaleur, sans parler du prix unitaire nettement plus bas", se réjouit M. Komurka. Le premier refroidisseur complet devrait être utilisé comme prototype dans une application industrielle au printemps 2024 ; toutefois, comme le composant est évolutif, il peut également être fabriqué plus grand ou plus petit que les prototypes.
Jusqu'à présent, le processus de construction s'est déroulé chez EOS. Cependant, l'idée est que justairtech fonctionne comme un groupe de réflexion, car elle ne prévoit pas de mettre en place sa propre installation de production à l'avenir. Notre partenaire de production de bout en bout d'EOS, MT Aerospace, se joint à ce projet pour construire le composant en série. Comme le souligne M. Sedlak, "notre système est cinq fois plus efficace que les autres : "Notre système est cinq fois plus efficace que les systèmes conventionnels et permet d'économiser de l'énergie, duCO2 et des coûts d'exploitation ; en outre, grâce à sa construction compacte, il peut être installé n'importe où. Bien que nous commencions par des applications industrielles, nous prévoyons de nous tourner vers les consommateurs finaux, car le produit est adapté au chauffage et au refroidissement de tout type de bâtiment", explique M. Sedlak en présentant sa vision. Nous ne manquerons pas d'observer la suite des événements, et nous continuerons à accompagner notre client dans ce projet à l'avenir. Restez donc à l'écoute.
#3dprintingstories