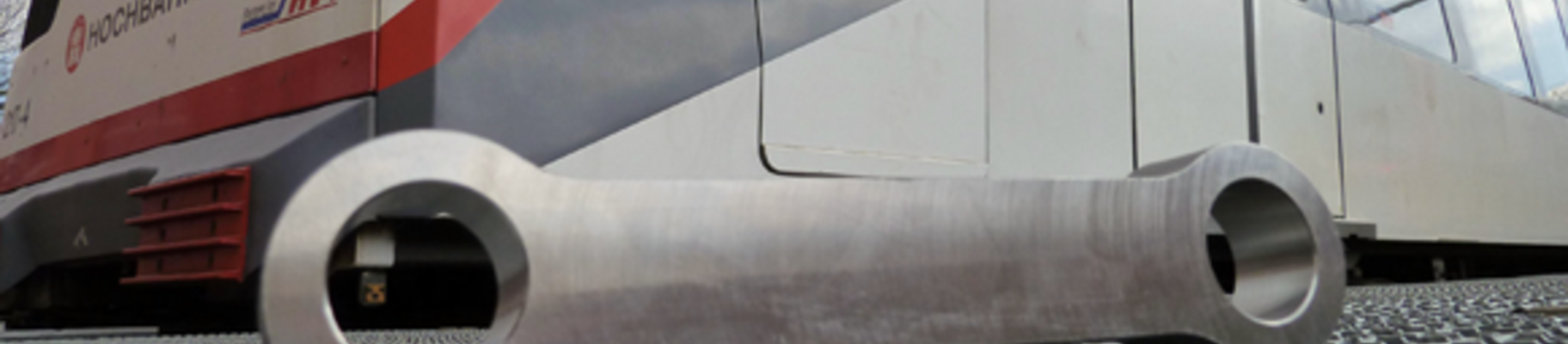
Repensar el ferrocarril: Stefanie Brickwede
El poder multimillonario de FA
17 DE ABRIL DE 2025 | Tiempo de lectura: 5 min
En un reciente episodio de Additive Snack Podcast, el presentador Fabian Alefeld volvió a dar la bienvenida a Stefanie Brickwede, una destacada figura que impulsa la adopción de FA no sólo en la compañía nacional de ferrocarriles de Alemania, Deutsche Bahn (DB), sino también en diversos sectores a través de la red que dirige.
El debate ofreció una visión fascinante de una década de implantación de FA en DB, la evolución estratégica desde aplicaciones especializadas a un pilar básico de la fabricación, y el papel fundamental de la colaboración para acelerar el progreso.
Un pionero vuelve al podcast
Fabian Alefeld volvió a presentar a Stefanie Brickwede, destacando su doble función como responsable de fabricación aditiva en Deutsche Bahn y directora general de la red Mobility Goes Additive (MGA). Tras haber hablado por última vez hace unos años, este episodio nos puso al día de los notables progresos realizados por DB y MGA.
Una década de aditivos en Deutsche Bahn: de la obsolescencia a la estrategia
Stefanie explicó que DB celebra este año su décimo aniversario de uso FA . El viaje empezó modestamente, afrontando el reto de la obsolescencia. Con trenes que a menudo funcionan durante 30, 40 o incluso 50 años, adquirir piezas de repuesto para modelos antiguos resulta cada vez más difícil y caro. FA presentó una solución perfecta para producir bajo demanda estas piezas no disponibles. Lo que empezó con sólo 10 piezas se ha disparado: DB ha impreso ahora más de 150.000 piezas en 700 casos de uso diferentes, utilizando 12 tecnologías FA distintas.
Curiosamente, el planteamiento inicial de DB era exclusivamente ascendente. Al ser principalmente una empresa de mantenimiento y no de construcción, DB carecía de bases de datos CAD completas para su vasto inventario. En lugar de la típica iniciativa corporativa de arriba abajo, el equipo de Stefanie se puso en contacto directamente con los compañeros de los talleres de mantenimiento, preguntando a personas entusiastas de toda la empresa de 200.000 empleados que estuvieran dispuestas a unirse al esfuerzo FA .
Así se creó un equipo apasionado e independiente de las jerarquías que identificaba las necesidades del mundo real directamente desde la base. No fue hasta más tarde cuando DB empezó a incorporar plantillas, utillajes y herramientas -a menudo consideradas fruta al alcance de la mano- y a desarrollar enfoques descendentes más estratégicos utilizando bases de datos mejoradas e incluso IA para identificar piezas imprimibles. Ahora, tanto el entusiasmo ascendente como la estrategia descendente trabajan en tándem.
Medir el éxito: De piezas impresas a millones ahorrados
Stefanie recuerda divertida una de las primeras conversaciones sobre indicadores clave de rendimiento en la que su jefe, que había trabajado en Airbus, sugirió inicialmente medir el éxito imprimiendo 20.000 piezas en el primer año, un objetivo que provocó risas, ya que entonces sólo habían impreso 10 piezas.
Si bien el número de piezas (específicamente piezas de repuesto reales, prototipos o herramientas, no regalos) fue una métrica inicial, el enfoque cambió rápidamente al impacto financiero cuantificable. Desde 2019, FA ha generado ahorros que ascienden a dos dígitos de millones de euros anuales para DB.
Estos ahorros proceden de varias fuentes: superación de cantidades mínimas de pedido, reducción significativa de los plazos de entrega (como en el caso de la carcasa del engranaje que se comenta más adelante) y prevención de costosas paradas del tren.
Sin embargo, el mayor potencial de futuro reside en el almacenamiento digital. Solo el almacén físico de material rodante de DB contiene piezas por valor de 1.800 millones de euros, el 10% de las cuales podrían imprimirse ya hoy.
Aprovechar este potencial es la estrategia "Road to 100 Million" de DB, cuyo objetivo es ahorrar 100 millones de euros mediante la fabricación bajo demanda y la reducción del inventario físico. Para ello, DB exige que el 10 % de las piezas de los trenes de nueva adquisición sean imprimibles, una tendencia adoptada por sus colegas holandeses (NS).

Superar obstáculos: Aceptación, cualificación y normas
Stefanie destacó el poder de hacer tangible la tecnología: llevar piezas metálicas impresas físicas a las partes interesadas ayudó a abrir los ojos. La comunicación, el marketing interno e incluso un concurso para empleados (que sirvió tanto para encontrar aplicaciones como para difundir la concienciación) fueron fundamentales. La creciente prevalencia de las impresoras FDM domésticas también ayudó a familiarizar a los empleados con los conceptos básicos de FA.
Un obstáculo importante, sobre todo para los componentes críticos, es el largo proceso de certificación.
A menudo, la impresión en sí no es el cuello de botella, sino que la cualificación y las pruebas requieren más tiempo. Conscientes de ello, DB y MGA colaboraron activamente con organismos de normalización como el Instituto Alemán de Normalización (DIN) para crear las directrices necesarias. Un resultado clave es la norma DIN 52920, que ayuda a evaluar la capacidad de un centro de producción para imprimir piezas críticas de forma fiable.
Stefanie insistió en la necesidad de armonizar las normas europeas (EN) o internacionales (ISO, ASTM) para facilitar una adopción más amplia y simplificar la integración de los proveedores.
La movilidad se vuelve aditiva: El poder de la colaboración en red
Reconociendo la necesidad de aprender de los demás y escalar más rápido, DB inició la red MGA hace nueve años con sólo nueve miembros fundadores. Hoy en día, MGA es una red europea líder FA con cerca de 150 empresas miembros, entre las que se encuentran los principales operadores ferroviarios, proveedores, fabricantes de maquinaria, proveedores de materiales, empresas de software, institutos de I+D y universidades.
MGA fomenta la colaboración en toda la cadena de suministro y en múltiples sectores, como el ferroviario, la aviación, la automoción, el aeroespacial, la construcción, la defensa, el médico e incluso el estilo de vida (moda, joyería, diseño). Los grupos de trabajo abordan retos comunes como la certificación, el desarrollo de materiales, la sostenibilidad y la educación.
Stefanie compartió ejemplos como un taller rápido sobre impresión de cobre organizado en 14 días y el desarrollo de un polvo ignífugo necesario (que cumple normas ferroviarias estrictas, antes limitadas a materiales como Ultem 9085) gracias a la colaboración entre Siemens y el proveedor de materiales Lehmann&Voss. Esta red impulsada por los usuarios tiende un puente entre las necesidades de la industria y las capacidades de los proveedores.
Historia de éxito: Evitar una crisis con FA
Un buen ejemplo de la repercusión de FA fueron 50 locomotoras de carga paradas por falta de carcasas de engranajes. Los proveedores tradicionales ofrecían pedidos mínimos y un plazo de entrega de dos años.
Ante una posible crisis debatida en la junta directiva, el equipo de Stefanie aprovechó la red de MGA, rediseñó la pieza y utilizó FA para imprimir moldes de arena para fundir las carcasas en el material original.
Todo el proceso, desde la identificación del problema hasta la entrega de la primera carcasa de repuesto, duró sólo dos meses, una demostración espectacular de la capacidad de FA para garantizar la resistencia operativa.

El camino por recorrer: Crecimiento adaptativo y disruptivo
Stefanie subraya que FA ofrece tanto soluciones adaptativas (sustitución de piezas iguales, lo que facilita su adopción por industrias conservadoras) como potencial disruptivo (nuevos diseños, piezas optimizadas). Ambos son necesarios. Aboga por que la industria de FA se ponga en el lugar del usuario y se adapte a sus necesidades, en lugar de obligarle a adaptarse por completo a la tecnología.
Las ideas de Stefanie Brickwede subrayan el poder transformador de FA cuando se aplica de forma estratégica y colaborativa. El viaje de una década de Deutsche Bahn ofrece un modelo convincente para aprovechar la FA con el fin de mejorar la eficiencia, la resiliencia y la innovación, mientras que MGA demuestra el valor exponencial de las asociaciones entre industrias para superar los desafíos compartidos y acelerar la adopción de esta tecnología revolucionaria.