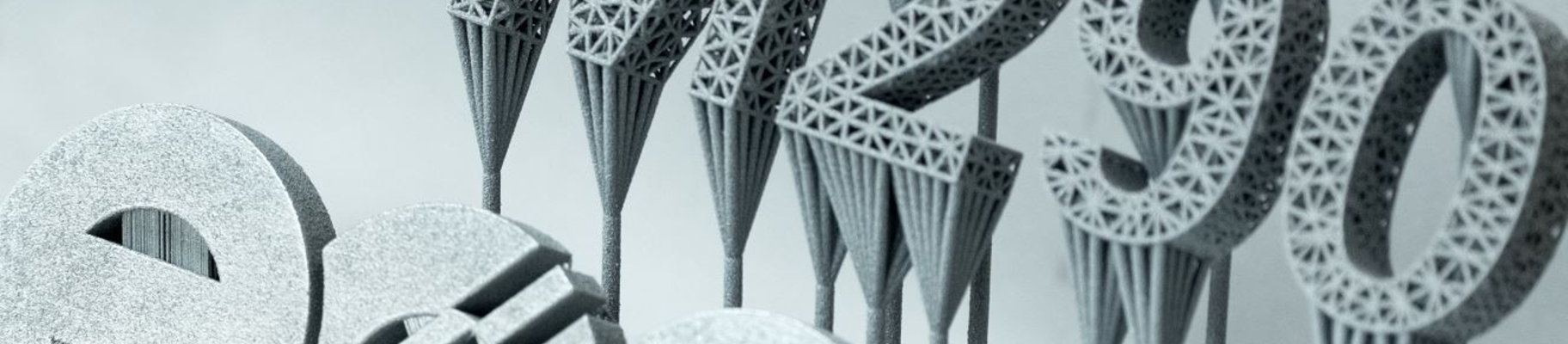
Casos prácticos de diferentes configuraciones de recobinador para Direct Metal Sinterizado láser (DMLS)
30 de septiembre de 2021 | Tiempo de lectura: 7 min
Cuando se trata de diferentes opciones de recubrimiento de álabes, siempre ha habido un debate en la comunidad de fabricación aditiva (FA) sobre si utilizar una solución de recubrimiento blando o duro. Aquí quiero ofrecer una visión general de los diferentes casos de uso y de las ventajas e inconvenientes del recubrimiento blando y duro.
Recobrador duro
La opción estándar para los sistemas EOS es el recubridor duro, debido a sus ventajas en términos de calidad de la pieza y repetibilidad. La cuchilla rígida garantiza un espesor de capa uniforme y puede eliminar las salpicaduras de la superficie de la pieza que se expulsaron del baño de fusión durante la exposición y que serían un factor de alto riesgo de falta de fusión en las capas posteriores. Debido a su forma y rigidez, la cuchilla dura compacta el polvo durante el recubrimiento, lo que proporciona un lecho de polvo de mayor densidad. Todos los parámetros de proceso estándar de EOS se desarrollan con cuchillas de recubrimiento duras, ya que son muy sensibles frente a parámetros de proceso inadecuados. De este modo, la ventana de proceso puede reducirse fácilmente a parámetros de proceso robustos, que proporcionan un proceso estable.
Un revestimiento duro presenta una resistencia al desgaste superior a la de los revestimientos blandos, lo que garantiza unas propiedades de revestimiento constantes incluso en trabajos de larga duración. De este modo, las propiedades son más uniformes en toda la pieza. Aunque los revestimientos duros suelen ser más caros que los revestimientos blandos, también hay que tener en cuenta la mayor vida útil y la menor necesidad de mantenimiento a la hora de analizar los costes.
Las industrias altamente reguladas han expresado sus reservas ante los recubridores blandos de polímero, porque el desgaste podría contaminar el polvo y provocar inclusiones. Por ejemplo, la industria aeroespacial quiere evitar especialmente las inclusiones de silicio en sus aplicaciones de motores. Sin embargo, no se trata de un criterio general de exclusión.
Las aplicaciones típicas que se benefician de las ventajas de los recubrimientos duros son las piezas con mayores exigencias de calidad repetible en términos de propiedades mecánicas o precisión dimensional, así como las piezas voluminosas, para las que un recubrimiento blando se desgastaría demasiado rápido en trabajos de larga duración.
Uno de los principales retos de las máquinas de recargue duro es su rigidez. Si la pieza entra en contacto con la máquina de recauchutado, el riesgo de interrupción del trabajo es alto, mientras que una máquina de recauchutado blanda se adaptaría a la deformación de la pieza. El contacto entre la pieza y la máquina de recauchutado se produce, por ejemplo, por el fallo del soporte debido a la tensión residual o por el sobrecalentamiento provocado por unos parámetros de proceso inadecuados.
Sin embargo, en el caso de piezas de alta calidad o de producción en serie, esta desventaja también puede considerarse una ventaja. Aunque el trabajo de fabricación finalizara con un repintado suave, el daño o la imperfección seguirían presentes al final y harían necesario el desguace de la pieza. Existe cierto riesgo de que el daño no se detecte hasta después del tratamiento térmico u otros pasos de postprocesado, lo que provocaría costes aún mayores. En el peor de los casos, si el defecto no se detecta en absoluto podría provocar un mal funcionamiento durante la operación. Aunque el trabajo se estrellara con un recargue duro, el ingeniero de FA recibe información directa de que algo en el diseño, los soportes o los parámetros del proceso va mal y de que la pieza tiene que pasar a la siguiente iteración.
Otra desventaja es que todas las fuerzas de fricción durante el recubrimiento se transmiten a la pieza, debido a la rigidez de la hoja. Este hecho limita la capacidad de fabricación cuando se trata de relaciones de aspecto elevadas. Durante el repintado, las fuerzas de fricción pueden doblar la pieza o provocar vibraciones que alteren el lecho de polvo. Este problema puede mitigarse parcialmente adaptando los parámetros del proceso, que tienen en cuenta la situación térmica de la pieza, pero sigue siendo un factor limitante para los diseños altos y delgados.
Sin embargo, los objetos finos, como las estructuras reticulares para aplicaciones médicas, demuestran que las piezas frágiles pueden fabricarse con bastante facilidad con un revestimiento duro si se adaptan los parámetros del proceso. Las copas de cadera son un buen ejemplo de piezas con estructuras finas pero con elevados requisitos de calidad, en las que el revestimiento duro puede demostrar sus ventajas.
Hay dos tipos diferentes de rectificadores duros disponibles para las máquinas EOS: HSS (acero rápido) y cerámica. Depende del material utilizado, la configuración del rectificador que debe seleccionarse. Para la mayoría de los materiales, se utiliza la cuchilla HSS, porque aunque esté templada, la cuchilla sigue mostrando cierta ductilidad. Por lo tanto, el riesgo de que se produzcan muescas tras el contacto con la pieza es menor que con el recargue cerámico. Sin embargo, en caso de muescas tras un trabajo brusco, por ejemplo debido a un fallo del soporte, no es necesario sustituir la cuchilla, sino que se puede rectificar con cuidado.
Si el material es magnetizable, debe elegirse una cuchilla de repintado de tipo cerámico. De lo contrario, el polvo se pegaría a la cuchilla y causaría rayas durante el repintado. Tales materiales en la cartera de EOS son aceros como CX, PH1, 17-4PH o MS1. A diferencia de la hoja HSS, las posibles muescas no se pueden rectificar debido a las características quebradizas de la cerámica. Sin embargo, el material es extremadamente resistente al desgaste.
Recubridores blandos
La principal ventaja de las opciones de recauchutado blando es la reducción de las fuerzas de recauchutado sobre la pieza durante el recauchutado. Al ser más flexible, la recauchutadora puede ceder si las fuerzas de fricción son demasiado elevadas o puede adaptarse en cierta medida al perfil de una pieza si ésta se deforma y se pega a través del lecho de polvo. Esto da lugar a dos casos de uso principales que presentan las ventajas de los recubridores blandos:
- mayor facilidad para fabricar piezas de gran relación de aspecto y elementos frágiles
- la menor probabilidad de que se interrumpa el trabajo debido a atascos en la rectificadora. Especialmente en la creación de prototipos, los resultados a corto plazo suelen ser más importantes que garantizar la calidad de las piezas. Por este motivo, muchos proveedores de servicios suelen utilizar máquinas de recargue blandas para cumplir plazos de entrega ajustados. Además, cada trabajo atascado aumentaría los costes de fabricación.
Las principales desventajas de los recubridores blandos ya se han mencionado brevemente en la comparación con los recubridores duros. El mayor desgaste del recubridor puede afectar a las propiedades de la pieza durante trabajos de construcción largos, ya que no se puede garantizar un comportamiento de recubrimiento uniforme en toda la altura de construcción. Además, en caso de deformación de la pieza, por ejemplo debido a una fijación insuficiente a la placa de impresión, el trabajo continúa pero la pieza tiene una alta probabilidad de estar fuera de especificación en cuanto a precisión dimensional. Por lo tanto, la finalización satisfactoria de un trabajo no significa necesariamente que la pieza cumpla las especificaciones.
No obstante, la repintadora blanda es una herramienta útil y su necesidad depende de la aplicación. Puede convertirse en la solución más económica para determinadas aplicaciones que presentan características como las mencionadas anteriormente: Elevada relación de aspecto, características frágiles o necesidad de resultados a corto plazo.
EOS ofrece tres opciones diferentes de recubridores blandos. El recubridor de fibra de carbono con cepillo que ya está disponible desde hace muchos años y dos tipos de los recubridores de polímero mencionados anteriormente para el EOS M 290: Silicona y caucho de nitrilo butadieno (NBR).
El rectificador de cepillo está equipado con una colección de fibras de carbono cortas, que se montan en un soporte. Puede tener pequeñas ventajas en comparación con las escobillas de polímero, pero es más caro. En caso de contacto con la pieza, la probabilidad de que el recuperador sufra daños permanentes es ligeramente menor que en la opción de polímero, porque las fibras pueden doblarse hacia los lados hasta cierto punto. Además, el efecto de las fuerzas de fricción está más localizado porque la pieza sólo interactúa con una cierta cantidad de fibras, lo que la hace superior para construir piezas frágiles.
Los dos tipos de recubrimiento de polímero para la EOS M 290, también están disponibles para los sistemas de bastidor grande EOS M 400 y EOS M 400-4. La forma más fácil de distinguirlos es el color: la lámina de silicona es transparente y la de NBR es negra, pero también hay diferencias en cuanto a propiedades y casos de uso. El material de recubrimiento de NBR está especificado para un uso de hasta 80 °C y el de silicona es adecuado para trabajos de construcción a temperaturas más elevadas.
Con el fin de mostrar las capacidades de las nuevas opciones de recubrimiento blando de polímero, hemos construido algunas piezas de alta relación de aspecto con letras EOS M 290 encima para aumentar aún más el desafío. Materialise Magics se ha utilizado para crear los soportes de los árboles, que tienen una relación de aspecto máxima de 66 (2,5 mm de diámetro con una altura de 165 mm). La escritura EOS M 290 de la parte superior se ha diseñado con ayuda del software Materialise 3-matic y consiste en una celosía basada en mallas con gráficos de volumen en su interior. Además, el fino soporte del logotipo EOS se ha creado con Materialise e-Stage, que permite generar el soporte de forma totalmente automatizada y puede ayudar a ahorrar el material necesario para el soporte, así como a reducir considerablemente el tiempo de preparación de los datos. A continuación, todo se imprimió en una EOS M 290 con EOS Aluminum AlSi10Mg y el nuevo proceso AlSi10Mg 60 µm Core.
Conclusiones
Existe un caso de uso apropiado para cada tipo de recoater. EOS considera que el sistema de recargue duro es la opción estándar para las piezas más exigentes en cuanto a calidad repetible, mientras que el sistema de recargue blando permite fabricar piezas con relaciones de aspecto elevadas. Además, se prefiere el recocido blando cuando el plazo de entrega es más importante que el riesgo de imperfecciones. EOS ofrece tanto recargadoras duras como blandas para que pueda elegir fácilmente la que mejor se adapte a su aplicación.