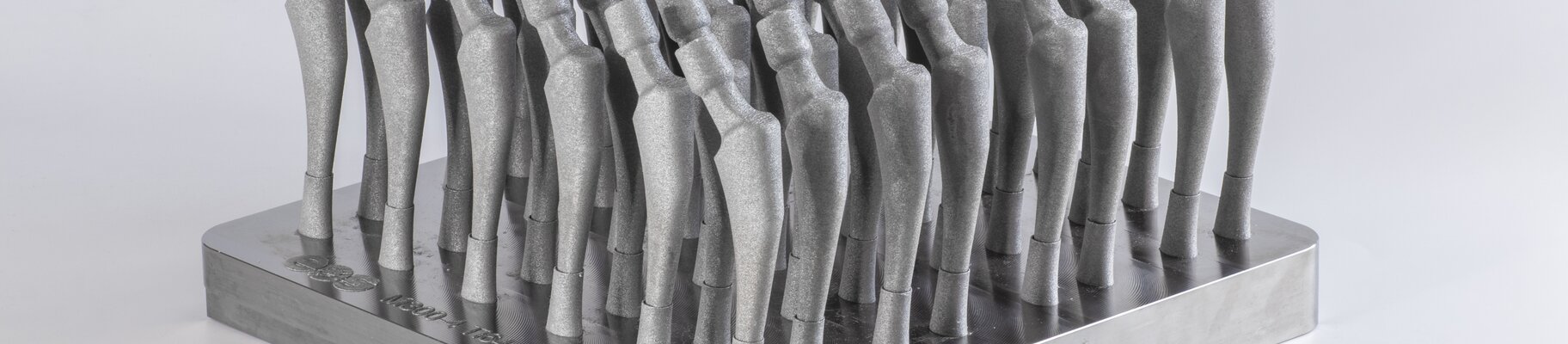
Implantes ortopédicos: Nuevas posibilidades con la impresión 3D de metales
30 de octubre de 2020 | Tiempo de lectura: 4 min
EOS ha desarrollado un proceso de Ti64 FA que, combinado con el proceso de tratamiento térmico de prensado isostático en caliente (HIP), crea unas propiedades de fatiga extraordinarias. El objetivo de este proyecto era poner de relieve y probar estas propiedades de fatiga en un diseño de implante real y comparar los resultados con los vástagos de cadera Ti64 forjados tradicionalmente.
Abriendo las posibilidades de la fabricación aditiva
Las secciones siguientes muestran cómo los conocimientos, la experiencia y los servicios que ofrece la red EOS se unieron para dar este salto adelante en la fabricación aditiva ortopédica:
Resultados de la fatiga
Las pruebas de fatiga fueron realizadas por el OIC, Orthopedic Innovation Center, Winnipeg, Canadá. Los vástagos de cadera se sometieron a pruebas de fatiga del cuello de acuerdo con la norma ISO 7206-6. Soportaron una carga de 5340 N durante 10 millones de ciclos. Soportaron una carga de 5340 N durante 10 millones de ciclos. En este estudio, se ensayaron 2 vástagos de cadera fabricados aditivamente y ambos superaron la prueba de 10 millones de ciclos. Esto demuestra que las propiedades de fatiga de estos implantes fabricados en FA eran al menos tan buenas como las del vástago de cadera Ti64 forjado tradicional. Es la primera vez que se miden unas propiedades de fatiga tan elevadas en un implante fabricado mediante fabricación aditiva.
Preparación de la construcción
Para evitar la necesidad de retirar el soporte y facilitar la extracción del implante de la plataforma, los vástagos de cadera se fabricaron en un "soporte". La principal función de este soporte es proporcionar protección frente a las fuerzas de recubrimiento. (Para obtener las mejores propiedades mecánicas, se utilizó una cuchilla HSS para garantizar un comportamiento óptimo y constante del recubrimiento). Sin embargo, no hay conexión entre el soporte y el vástago de la cadera, sino un espacio de entre 0,2 mm y 0,3 mm. El tamaño de la separación es un compromiso entre la facilidad de extracción y la firmeza para evitar que el vástago de la cadera vibre debido a las fuerzas del recubridor. El vástago de la cadera se mantiene en su sitio gracias a las fuerzas de fricción entre el soporte, el polvo y el vástago de la cadera.
Me inspiré para esta estrategia de construcción en el post Construir sin soporte de mi colega Michael Wohlfart. Es muy gratificante dar vida a estas ideas innovadoras en una aplicación real.
Uso del programa Amphyon de Additive Works
El siguiente paso era asegurarse de que esta idea funcionaría en la práctica. Se utilizó Amphyon para confirmar que la estrategia de configuración no provocaba ningún problema, eliminando la necesidad de una estrategia de construcción de "prueba y error". Una queja habitual de los nuevos usuarios de FA , e incluso de los usuarios experimentados de FA que prueban nuevas aplicaciones, es la necesidad de utilizar una estrategia de "prueba y error" para las primeras construcciones.
Se realizaron simulaciones para comprobar la colisión del revestimiento, verificar que las deformaciones estaban dentro de los márgenes de tolerancia y comprobar las tensiones térmicas. Este análisis permite obtener una construcción de alta calidad antes de realizar un solo trabajo, lo que reduce costes y plazos.
Este software permite predeformar el vástago de la cadera para crear una pieza de gran precisión directamente de la impresora, a la primera. Según mi experiencia, esto funciona bien, especialmente para las deformaciones pequeñas y controladas que se esperan para el vástago de la cadera durante la impresión.
Excelentes propiedades a la fatiga
Proceso de vanguardia FA
Los vástagos de cadera se han fabricado utilizando el proceso EOS Titanium Ti64 Grade 23 en capas de 40 µm de grosor en una EOS M 290. Se eligió la EOS M 290 290 para este proyecto porque es el sistema industrial de fabricación aditiva más cualificado del mercado. Además, la fiabilidad y repetibilidad de la máquina es exactamente lo que se necesita para obtener unas propiedades de fatiga excelentes, ya que un solo defecto puede reducir significativamente las propiedades. En el futuro tendría sentido optimizar aún más el proceso para la fabricación en serie, mejorando potencialmente la velocidad de fabricación y la estabilidad dados los requisitos únicos de una aplicación de vástago de cadera.
Tratamiento térmico HIP optimizado
Las excelentes propiedades a la fatiga se obtienen gracias a la combinación de un proceso de vanguardia FA (mencionado anteriormente) combinado con un tratamiento térmico optimizado de Presión Isostática en Caliente (HIP). Los tratamientos térmicos HIP convencionales se optimizan para mejorar las propiedades mecánicas de la calidad y la microestructura de las piezas fundidas o similares a las fundidas. La calidad de un EOS M 290 es muy superior a ésta y, por ello, EOS ha desarrollado un tratamiento térmico HIP que tiene en cuenta la microestructura única de FA.
El tratamiento convencional de la cadera se realiza a 920 °C a 100 MPa durante 2 horas y está muy extendido entre diferentes industrias. El proceso desarrollado por EOS se realiza a 820 °C a 140 MPa durante 2 horas. Este ciclo HIP combinado con el proceso DMLS de EOS da como resultado una resistencia a la fatiga de 795 Mpa para 10^7 ciclos (N=9).
Postprocesado
El postprocesado es bastante sencillo y fue realizado por Precision ADM, Winnipeg, Canadá. El proceso FA se configuró de forma que se pudieran utilizar los mismos pasos de postratamiento que en un vástago de cadera fabricado de forma convencional. Por lo tanto, se optó por el enfoque sin soportes. Se mecanizó el cono y se pulió el cuello del vástago de la cadera para obtener unas propiedades de fatiga óptimas, similares a las de un dispositivo de referencia ya comercializado. Los resultados pueden verse a la derecha.
Conclusión
El hecho de que hoy sea posible conseguir propiedades mecánicas forjadas en una aplicación real supone un enorme salto en la fabricación aditiva para ortopedia. Este emocionante avance nos permite desbloquear el potencial de la fabricación aditiva para, una vez más, otro grupo de implantes. Ahora depende de los diseñadores de dispositivos de las empresas ortopédicas, y de otros, ampliar los límites de FA y hacer realidad ideas que se creían imposibles. Additive Minds está deseando trabajar con usted, desbloquear estas posibilidades y hacer posible la próxima generación de implantes.
Autor: Davy Orye