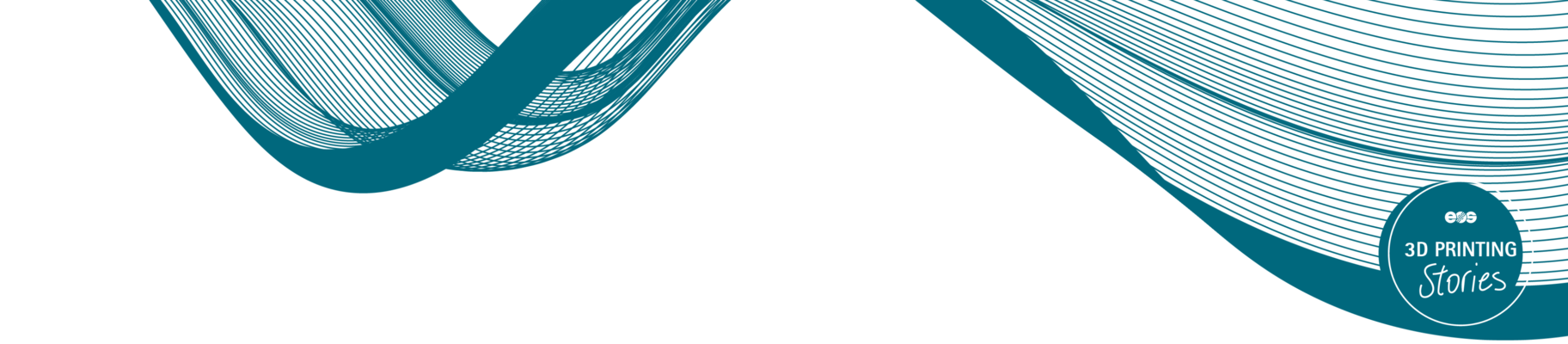
Un enfriador, que enfría el aire utilizando aire
Clean-Tech-Company justairtech desarrolla un sistema de refrigeración impreso en 3D con una eficiencia significativamente mayor
26 de febrero de 2024 | Tiempo de lectura: 15 min
¿No se puede hacer? ¡Oh, sí que se puede! Cinco veces más eficiente y con un consumo eléctrico un ochenta por ciento menor
En estos momentos, todo el mundo habla de utilizar bombas de calor para calentar edificios. Un intercambiador de calor no sólo es parte integrante de una bomba de calor, sino también un componente esencial de una enfriadora. ¿Cómo funciona? Funciona transfiriendo energía térmica entre dos medios, aunque en un proceso bastante ineficiente, que Holger Sedlak, Director Técnico de justairtech, estaba decidido a mejorar: "Me estimula la idea de ver que algo que hasta ahora era inalcanzable es físicamente posible. Entonces empiezo a buscar soluciones. En este caso, nos ocupamos únicamente del aire". Tras un viaje fascinante tanto para EOS como para justairtech, se ha demostrado que la solución es posible. El resultado es un intercambiador de calor muy eficiente que permite un diseño revolucionario del enfriador, que requiere sólo un tercio de la energía eléctrica que se necesitaba antes.
¿Qué tiene de nuevo el concepto justairtech?
"Una sola vía rápida es mejor que varias estaciones de intercambio"
El aire de una habitación se acondiciona introduciéndolo en un intercambiador de calor, donde se enfría. Luego hay un circuito de agua y otro circuito con un medio como los hidrocarburos fluorados. Estos circuitos deben ser accionados por bombas, y el sistema requiere también ventiladores y componentes adicionales, todo lo cual consume electricidad. Sedlak utiliza un ejemplo descriptivo para explicar su idea alternativa de refrigerar aire con aire: "Antiguamente, si querías ir de Múnich a Berlín en tren, tenías que hacer transbordo en varias estaciones. Esto no sólo llevaba mucho tiempo, sino que también era bastante molesto. Pero si puedes evitar todos estos cambios tomando una ruta rápida, el viaje será a la vez considerablemente más rápido y mucho más agradable". Este es el principio básico de su producto: Sedlak elimina todos los elementos intermedios innecesarios, dando como resultado un intercambiador de calor aire-aire fractal1 que, comparado con los modelos convencionales, permite un nuevo diseño de enfriadora y bomba de calor que consume sólo una quinta parte de electricidad. Hasta aquí, todo bien. Una de las razones por las que esta solución no existía hasta ahora es que, sencillamente, no se podía fabricar.
1Fractal es un término que designa ciertas formas o patrones geométricos naturales o artificiales (redacción inglesa correspondiente al texto original alemán). Fuente: Wikipedia, 24.07.2023
Reto aceptado:
Máxima superficie, mínimo grosor de pared y más
Holger Sedlak llevó su idea a EOS en mayo de 2022, junto con la estructura clave de su intercambiador de calor. Philipp Komurka, del Equipo de Mentes Aditivas de EOS, discutió la idea con sus colegas, aunque inicialmente consideraron muy improbable el éxito de su puesta en práctica. El principal escollo que impedía su realización era el grosor extremadamente pequeño de la pared, de unos 150 micrómetros, junto con una superficie muy grande y en total unos 330.000 canales con un diámetro de sólo 0,5 milímetros. Aunque la impresión EOS DMLS-3D está concebida para estructuras muy intrincadas, el proceso láser requiere la transferencia de energía. Esto significa que el material tiene que fundirse para formar una capa, pero para cumplir las especificaciones de diseño extremadamente estrictas del componente y no obstruir los canales, está sujeto a limitaciones de altura. Otro requisito era el uso del material 316L, es decir, acero inoxidable. Aunque otros materiales habrían sido más fáciles de procesar, su conductividad habría sido demasiado alta, lo que habría perjudicado el funcionamiento del intercambiador de calor.
"En mi vida he conseguido hacer realidad muchas cosas imposibles, pero siempre he trabajado con socios. Lo que se necesita es un pensamiento sistémico y un viaje conjunto con otras personas para ver dónde pueden ser necesarios ajustes tanto en el diseño como en la tecnología de producción. Para mí estaba claro que mi producto sólo podía crearse mediante impresión 3D en metal, y EOS no sólo asumió parte del riesgo, sino que se comprometió enormemente a alcanzar conjuntamente el objetivo."
Holger Sedlak, Director Técnico de justairtech

El camino hacia la meta
Proceso y diseño, depowdering y construcción en frío
Dos miembros del equipo del proyecto se reunieron con Philipp Komurka para trabajar en hacer posible lo imposible. Empezaron modificando los parámetros y procesos y adaptando cada uno de ellos a los requisitos del intercambiador de calor justairtech. El equipo consiguió configurar variables como la potencia del láser, la velocidad y los rangos de temperatura de forma que, efectivamente, se pudiera construir una estructura de este tipo. En el verano de 2022, la primera prueba resultó un éxito, pero requirió un tiempo de construcción muy largo, de 110 horas. Proyectados sobre el componente en su conjunto, los costes unitarios habrían sido demasiado elevados para un funcionamiento económicamente viable.
Así que la siguiente tarea era reducir el tiempo de construcción a unas 20 horas, como había previsto inicialmente Holger Sedlak. Esto significaba reducir el tiempo de construcción hasta en un 80%. Un paso para lograrlo fue reducir el volumen de los datos de construcción, ya que los innumerables vectores originales daban lugar a un archivo de diseño muy grande, que a su vez provocaba un tiempo de procesamiento posterior excesivamente largo. El diseño se optimizó en estrecha colaboración entre EOS y justairtech y el volumen de datos se redujo considerablemente. El segundo paso consistió en el despolvoreado, ya que en el primer intento de construcción, la estructura acabada contenía unos 30 kilos de polvo suelto, que quedó atrapado en los diminutos canales. Komurka explica: "Para empezar, además de utilizar el sistema de despolvoreado, también tuvimos que golpear los canales a mano con un pequeño martillo, porque no habíamos esperado lo suficiente. Finalmente, nos dimos cuenta de que el componente simplemente necesitaba un tiempo de depowdering más largo". En otoño de 2022 y después de muchas fases de optimización, el tiempo de construcción había alcanzado las 60 horas, lo que corresponde ya a una reducción de casi el 50%. Para agilizar aún más el proceso, el componente se fabricó en frío en EOS M 400-4, ya que normalmente el espacio de fabricación se calienta, lo que facilita el trabajo con el material. Al final, el uso de la construcción en frío permitió reducir considerablemente el tiempo de enfriamiento.
Misión más que cumplida: ¿qué viene ahora?
"Por el momento, el tiempo de fabricación es de 10 a 12 horas, y el desmontaje, de unas 4 horas, lo que nos lleva a un tiempo de fabricación de unas 16 horas para completar el componente central del nuevo intercambiador de calor, por no mencionar el precio unitario significativamente más bajo", afirma Komurka con satisfacción. El primer enfriador completo se utilizará como prototipo en una aplicación industrial en la primavera de 2024; sin embargo, como el componente es escalable, también puede fabricarse más grande o más pequeño que los prototipos.
Hasta ahora, el proceso de construcción ha tenido lugar en EOS. Sin embargo, la idea es que justairtech funcione como un laboratorio de ideas, ya que no tiene previsto crear su propia planta de producción en el futuro nuestro socio de producción integral de EOS , MT Aerospace, se une a este proyecto para fabricar el componente en serie. Como señala Sedlak "Nuestro sistema es cinco veces más eficiente que los convencionales y ahorra energía,CO2 y costes de funcionamiento; además, gracias a su construcción compacta, puede instalarse en cualquier lugar. Aunque estamos empezando con aplicaciones industriales, tenemos previsto llegar a los consumidores finales, ya que el producto es apto para calentar y refrigerar cualquier tipo de edificio", afirma Sedlak, exponiendo su visión. Ya veremos a dónde nos lleva, y seguiremos acompañando a nuestro cliente en este proyecto en el futuro. Así que permanezcan atentos.
#3dprintingstories