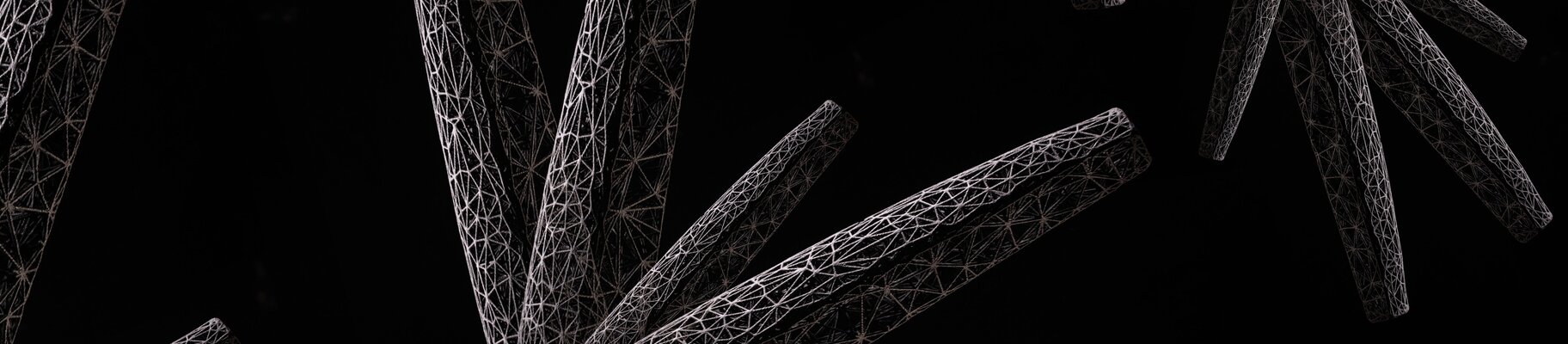
NextGen AM - La stampa 3D automatizzata si rivela un successo totale
Il progetto congiunto tra Premium AEROTEC, EOS e Daimler dimostra un enorme potenziale per la produzione di parti di ricambio e componenti di serie.
____ Augsburg/Varel, Krailling, Stoccarda, 30. aprile 2019
Ciò che è iniziato come una visione promettente nel maggio 2017 ha ora raggiunto una conclusione di successo: il progetto"NextGenAM" per lo sviluppo di una linea di produzione pilota per un processo di "Additive Manufacturing" automatizzato di nuova generazione da parte dei partner Premium AEROTEC, EOS e Daimler.
Il processo di stampa 3D, noto anche come "Additive Manufacturing" (AM), è diventato sempre più interessante come processo complementare o alternativo alle tecniche di produzione convenzionali. La tecnologia viene definita "additiva" per il modo in cui il processo prevede l'applicazione di uno strato dopo l'altro di materiale sottile, che viene poi indurito da una fonte di energia. Oltre alle materie plastiche e alle ceramiche, è possibile produrre anche componenti metallici con un processo di stampa 3D.
L'obiettivo del progetto pilota era quello di sviluppare una linea di produzione digitalizzata di nuova generazione in grado di produrre componenti in alluminio per i settori automobilistico e aerospaziale in modo significativamente più economico rispetto a quanto attualmente possibile. Il successo di NextGenAM: in termini di processo produttivo complessivo presso Premium AEROTEC, i costi di produzione potrebbero essere ridotti fino al 50% rispetto ai sistemi di stampa 3D esistenti.
"L'automazione è uno dei fattori chiave della nostra strategia, che rende possibile l'integrazione dei nostri sistemi in linee di produzione automatizzate come POLYLINE. E questo è importante per ridurre i costi per pezzo e garantire la giusta qualità lungo l'intera catena di produzione.
Consentire la produzione in serie è uno dei motivi principali per cui DyeMansion è stata fondata, ed è per questo che i nostri sistemi sono stati costruiti, per portare la post-elaborazione a questo livello. La Powershot DUAL Performance è stata costruita per la scala, in modo da poter servire dieci o anche più stampanti in produzione e quindi rendere possibile una fabbrica end-to-end. Il punto di partenza è che la stampa 3D permette di realizzare una fabbrica automatizzata end-to-end. Il successo del progetto POLYLINE dimostra cosa è possibile fare e questo è solo l'inizio".
Dr. Thomas Ehm, Presidente del Consiglio Direttivo di Premium AEROTEC
Produzione completamente automatizzata
Il segreto sta in una catena di produzione additiva ingegnosa e scalabile, che è completamente automatizzata fino al punto in cui i pezzi stampati vengono segati meccanicamente dalla piattaforma di costruzione. Ciò significa che non è necessario alcun lavoro manuale in nessuna fase del processo, dalla preparazione dei dati e dalla fornitura centrale di polvere fino al processo di costruzione AM vero e proprio, passando per il trattamento termico, il controllo qualità e la separazione dei componenti dalla piattaforma di costruzione. Il cuore tecnico del sistema è il sistema a quattro laser EOS M 400-4 per la stampa 3D industriale con materiali metallici. Un sistema di trasporto senza conducente e robot assicurano il movimento regolare dei pezzi in ogni fase della linea di produzione.
L'intero processo produttivo si svolge da solo, senza personale operativo, da un centro di controllo centrale e autonomo. Fondamentale per il sistema è il modo in cui tutte le macchine utilizzate sono collegate in rete. I dati relativi ai lavori di costruzione vengono trasmessi al centro di controllo, che stabilisce la priorità delle varie richieste di costruzione e le assegna a un sistema AM. Durante il processo di costruzione, lo stato di produzione può essere recuperato anche su un dispositivo mobile, indipendentemente dalla posizione. Una volta completata l'intera catena di produzione, i rapporti sulla qualità vengono inviati centralmente al centro di controllo. Qui è possibile accedere a tutti i dati necessari per la produzione di un "gemello" digitale, consentendo tra l'altro una tracciabilità completa.
La capacità può essere estesa
Una stringa continua di dati 3D con una gestione integrata della qualità fa di questo sistema di produzione uno dei primi esempi di riferimento per il futuro, l'Industria 4.0. Il processo di produzione è completamente scalabile: le linee di produzione possono essere semplicemente duplicate per ampliare la capacità dell'impianto. Ciò promette ulteriori risparmi sostanziali in futuro, man mano che i numeri aumenteranno. Oggi, l'impianto pilota è già in grado di produrre in modo automatizzato componenti secondo gli standard di qualità della produzione di serie.
I pezzi per Daimler vengono già prodotti sulla nuova linea tecnologica di Premium AEROTEC: l'unità autocarri, ad esempio, sta già utilizzando il primo pezzo di ricambio prodotto a Premium AEROTEC. Si tratta di una staffa per un motore diesel per autocarri.

Pezzi di ricambio per autocarri e autobus
Il processo di stampa 3D è particolarmente utile nel settore dei pezzi di ricambio poiché, in caso di problemi agli utensili, i pezzi richiesti di rado possono essere riprodotti in modo più economico rispetto ai processi tradizionali di fusione in sabbia o a pressione. Le prime richieste di parti di ricambio per autobus stampate in 3D in alluminio sono attualmente in fase di esame presso il Centro di competenza per la stampa 3D di Daimler Buses. Anche il team di analisi dell'area autovetture sta valutando le potenziali applicazioni più adatte.
Opportunità per le serie più piccole e per lo sviluppo avanzato
"L'Additive Manufacturing è adatto anche per la produzione di piccole serie di nuovi veicoli (edizioni limitate). Lo sviluppo sistematico di parti specifiche per la stampa 3D consente di ridurre ulteriormente i costi di produzione e di ottimizzare la qualità. La stampa 3D è particolarmente utile anche durante lo sviluppo anticipato dei veicoli. I bassi numeri richiesti possono spesso essere prodotti in modo più economico e veloce con l'Additive Manufacturing rispetto ai processi di produzione convenzionali".
Jasmin Eichler, responsabile delle tecnologie future di Daimler AG
E questo vale tanto per i veicoli con motore a combustione quanto per le auto elettriche. La stampa 3D è particolarmente adatta, ad esempio, per la produzione delle piastre di base integrate che trasportano le linee di raffreddamento delle batterie dei veicoli elettrici.
Alta qualità del prodotto come standard
L'alta qualità del prodotto è standard nell'impianto pilota: è previsto anche l'utilizzo di una lega di alluminio/magnesio/scandio ad alta resistenza (nota anche come Scalmalloy®) per i componenti utilizzati nei settori aeronautico e aerospaziale.
Per il settore automobilistico viene utilizzata una lega di alluminio classica (AlSi10Mg), le cui proprietà sono state costantemente migliorate nel corso del progetto pilota. La resistenza del materiale e la qualità della finitura, tra gli altri fattori, sono state notevolmente migliorate rispetto a due anni fa, quando è iniziata la collaborazione.
Prospettive: La stampa 3D come metodo di produzione con buone prospettive
Ora che tutti i controlli di qualità effettuati finora sono stati superati con risultati così promettenti, sono in corso i preparativi per un audit in base ai requisiti della severa norma industriale VDA 6.3. Questo è uno dei prerequisiti di Daimler per la fornitura di componenti di serie da parte di fornitori di stampa a contratto. Questo è uno dei prerequisiti di Daimler per la fornitura di componenti di serie da parte di fornitori di stampa a contratto. L'automazione dell'intera catena di produzione AM consentirà in futuro di produrre in serie lotti più grandi, con la stessa affidabilità, funzionalità, durata ed efficienza economica dei componenti prodotti in modo tradizionale. I componenti dei nuovi veicoli possono essere ottimizzati per la stampa 3D durante la fase di progettazione, con la promessa di ulteriori vantaggi in termini di costi. La stampa 3D offre anche vantaggi in termini di peso, particolarmente interessanti per i veicoli elettrici. Per quanto riguarda i pezzi di ricambio, la stampa 3D offre il vantaggio di risparmiare sui costi di magazzino, perché i pezzi possono essere prodotti "su richiesta". Questa visione del futuro è nota in Daimler anche come "Digital Stock", ovvero la disponibilità centralizzata di dati di produzione digitali per consentire la produzione decentralizzata di parti di ricambio con la stampa 3D.
Come si vede, la stampa 3D è sulla buona strada per affermarsi ulteriormente nei settori automobilistico e aerospaziale come metodo di produzione aggiuntivo, molto versatile e relativamente giovane.

Partner del progetto
Premium AEROTEC
Premium AEROTEC è il primo produttore di componenti al mondo a fornire componenti stampati in 3D in leghe di titanio per la produzione in serie di aerei Airbus. L'azienda è un attore globale nel settore dell'aviazione. Il suo core business è lo sviluppo e la produzione di strutture aeronautiche in metallo e materiali compositi in fibra di carbonio. L'azienda opera in Germania nei siti di Augsburg, Brema, Amburgo, Nordenham e Varel. Premium AEROTEC si è assunta la responsabilità dell'intero processo produttivo del progetto comune.
______________
EOS
EOS è il fornitore leader mondiale di tecnologia nel campo della stampa 3D industriale di metalli e polimeri. Fondata nel 1989, l'azienda indipendente è pioniera e innovatrice di soluzioni complete per la produzione additiva. Il suo portafoglio prodotti di sistemi EOS, materiali e parametri di processo offre ai clienti vantaggi competitivi cruciali in termini di qualità del prodotto e di sostenibilità economica a lungo termine dei loro processi produttivi. Nell'ambito del progetto congiunto, EOS ha fornito la tecnologia di stampa 3D completa e le soluzioni software associate, nonché il centro di controllo per il collegamento e la gestione della catena di produzione.
______________
Daimler
Daimler ha contribuito al progetto con la sua esperienza nella produzione su larga scala. Le unità di ricerca e sviluppo avanzato hanno lavorato a stretto contatto. Tra gli aspetti trattati figurano i componenti campione, la robustezza computazionale e la digitalizzazione dei dati dei componenti per l'intero processo di produzione. Anche il collaudo dei componenti campione è stato coperto dalla casa automobilistica, così come la produzione di un libro di specifiche di produzione standardizzate per la stampa 3D. Daimler era inoltre responsabile del monitoraggio della convalida e della certificazione secondo lo standard VDA 6.3 per quanto riguarda la produzione in serie.
Scaricamento
-
Staffa per un motore diesel di camion, realizzata nell'ambito del progetto NextGenAM.
JPG 2,74 MB -
Il centro della catena di produzione pilota è il sistema a quattro laser EOS M 400-4 per la stampa 3D industriale con materiali metallici.
JPG 881,07 kB